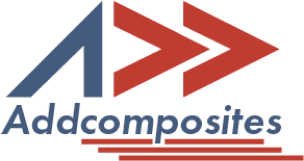
Automated Fiber Placement (AFP) represents a paradigm shift in aerospace manufacturing, merging the precision of automation with the strength of composite materials. This technology layers pre-impregnated fibers, typically carbon or glass, in a predetermined orientation, allowing for complex shapes and optimized structural properties. AFP is crucial in aerospace, where every gram and every inch must be accounted for, offering unparalleled efficiency and material performance. From the fuselages of commercial jets to the payload fairings of spacecraft, AFP is not just enhancing current capabilities — it's enabling the industry to reach new heights of innovation and design.
Fuselage Skins and Panels The fuselage — the aircraft's main body — is where AFP technology shines, enabling the fabrication of large, complex geometries with high precision. For instance, the Airbus A350 and Boeing 787 utilize AFP for their fuselage components, enhancing the structural integrity while reducing overall weight.
Wing Components (Spars, Ribs, Wing Boxes) Wings are critical for flight, and AFP is instrumental in their construction. The wing spars of the A350 are created using AFP on a rotating mandrel, illustrating how AFP simplifies the manufacturing of even the most substantial and vital aircraft parts. This method also applies to the ribs and wing boxes, which are pivotal for the aircraft's fuel storage and overall aerodynamics.
Fan Blades and Nacelles AFP's precision is paramount in engine components where performance and safety are non-negotiable. The fan blades, made using AFP systems, are integral to engine thrust. The nacelles, which house the engine, benefit from AFP's ability to create strong, heat-resistant structures necessary for modern jet engines.
Thrust Reversers While specific examples of thrust reversers made with AFP weren't found, the technology's application in related engine components like fan blades suggests its suitability for thrust reversers, which are critical for aircraft landing safety.
Control Surfaces (Flaps, Ailerons, Spoilers) AFP lends itself to the manufacturing of control surfaces such as ailerons and spoilers due to its ability to create lightweight yet strong composite structures. The Krueger flaps, part of the Hybrid Laminar Flow Control concept on wings, are manufactured using AFP for better aerodynamic efficiency and weight reduction.
Rotor blades are paramount in rotorcraft for providing lift and maneuverability. Automated Fiber Placement (AFP) allows for the precise alignment of fibers, essential for the rotor blades' strength and performance. The wind energy sector's trend toward AFP in blade manufacturing indicates its potential crossover to rotorcraft, where blade integrity is critical.
The CH-53K helicopter's composite flexbeams are a testament to the successful implementation of AFP. This flight-critical structure in the tail rotor has been automated, enhancing the strength-to-weight ratio and ensuring consistent quality — factors that are vital in rotorcraft operation.
While direct instances of AFP used in rotor cowls manufacturing were not found, the AFP's ability to create complex geometries and large, lightweight structures offers potential applications in rotor cowls. These components could benefit from AFP's precision and material efficiency, leading to improved performance and durability.
In the realm of space exploration, AFP is crucial for constructing launch vehicle components that demand high-strength and lightweight properties. Payload fairings, which protect satellites during launch, are being fabricated using AFP with materials such as TORAYCA™ prepreg. This method ensures efficient forming of complex shapes and large structures, vital for withstanding the rigors of space launch.
AFP's precision and strength advantages are equally beneficial for satellite structural components. Though specific examples were not detailed in our findings, the technology's use in payload fairings suggests a significant potential for its application in the construction of next-generation satellites, promising improvements in satellite longevity and performance.
The use of AFP in manufacturing access panels and doors optimizes structural weight without compromising strength. NORDAM's innovative use of AFP for these components demonstrates enhanced production efficiency and the ability to meet specific design requirements.
AFP's superior quality and cost benefits extend to the manufacturing of air ducts for environmental control systems. Its extensive use in the aerospace industry for parts like fuselage components suggests its potential for precision manufacturing of air ducts.
Radomes, crucial for protecting radar antennae, benefit from AFP's precision and material performance. NORDAM's use of AFP for SatCom radomes exemplifies how this technology can produce high-strength, precision-made components for critical communication systems.
The transformative impact of Automated Fiber Placement (AFP) in aerospace manufacturing is undeniably profound. From structural integrity to precision in complex components, AFP has proven to be more than just a technique; it's a cornerstone in the evolution of aerospace engineering. The future of AFP promises further innovation, with potential expansion into new materials and applications that could redefine the boundaries of aircraft and spacecraft design. As the industry continues to strive for greater efficiency and performance, AFP stands as a key enabler, poised to meet the challenges of tomorrow's aerospace ambitions.
Discover the future of composite manufacturing with Addcomposites! Here's how you can get involved:
At Addcomposites, we are dedicated to revolutionizing composite manufacturing. Our AFP systems and comprehensive support services are waiting for you to harness. So, don't wait – get started on your journey to the future of manufacturing today!
Automated Fiber Placement (AFP) represents a paradigm shift in aerospace manufacturing, merging the precision of automation with the strength of composite materials. This technology layers pre-impregnated fibers, typically carbon or glass, in a predetermined orientation, allowing for complex shapes and optimized structural properties. AFP is crucial in aerospace, where every gram and every inch must be accounted for, offering unparalleled efficiency and material performance. From the fuselages of commercial jets to the payload fairings of spacecraft, AFP is not just enhancing current capabilities — it's enabling the industry to reach new heights of innovation and design.
Fuselage Skins and Panels The fuselage — the aircraft's main body — is where AFP technology shines, enabling the fabrication of large, complex geometries with high precision. For instance, the Airbus A350 and Boeing 787 utilize AFP for their fuselage components, enhancing the structural integrity while reducing overall weight.
Wing Components (Spars, Ribs, Wing Boxes) Wings are critical for flight, and AFP is instrumental in their construction. The wing spars of the A350 are created using AFP on a rotating mandrel, illustrating how AFP simplifies the manufacturing of even the most substantial and vital aircraft parts. This method also applies to the ribs and wing boxes, which are pivotal for the aircraft's fuel storage and overall aerodynamics.
Fan Blades and Nacelles AFP's precision is paramount in engine components where performance and safety are non-negotiable. The fan blades, made using AFP systems, are integral to engine thrust. The nacelles, which house the engine, benefit from AFP's ability to create strong, heat-resistant structures necessary for modern jet engines.
Thrust Reversers While specific examples of thrust reversers made with AFP weren't found, the technology's application in related engine components like fan blades suggests its suitability for thrust reversers, which are critical for aircraft landing safety.
Control Surfaces (Flaps, Ailerons, Spoilers) AFP lends itself to the manufacturing of control surfaces such as ailerons and spoilers due to its ability to create lightweight yet strong composite structures. The Krueger flaps, part of the Hybrid Laminar Flow Control concept on wings, are manufactured using AFP for better aerodynamic efficiency and weight reduction.
Rotor blades are paramount in rotorcraft for providing lift and maneuverability. Automated Fiber Placement (AFP) allows for the precise alignment of fibers, essential for the rotor blades' strength and performance. The wind energy sector's trend toward AFP in blade manufacturing indicates its potential crossover to rotorcraft, where blade integrity is critical.
The CH-53K helicopter's composite flexbeams are a testament to the successful implementation of AFP. This flight-critical structure in the tail rotor has been automated, enhancing the strength-to-weight ratio and ensuring consistent quality — factors that are vital in rotorcraft operation.
While direct instances of AFP used in rotor cowls manufacturing were not found, the AFP's ability to create complex geometries and large, lightweight structures offers potential applications in rotor cowls. These components could benefit from AFP's precision and material efficiency, leading to improved performance and durability.
In the realm of space exploration, AFP is crucial for constructing launch vehicle components that demand high-strength and lightweight properties. Payload fairings, which protect satellites during launch, are being fabricated using AFP with materials such as TORAYCA™ prepreg. This method ensures efficient forming of complex shapes and large structures, vital for withstanding the rigors of space launch.
AFP's precision and strength advantages are equally beneficial for satellite structural components. Though specific examples were not detailed in our findings, the technology's use in payload fairings suggests a significant potential for its application in the construction of next-generation satellites, promising improvements in satellite longevity and performance.
The use of AFP in manufacturing access panels and doors optimizes structural weight without compromising strength. NORDAM's innovative use of AFP for these components demonstrates enhanced production efficiency and the ability to meet specific design requirements.
AFP's superior quality and cost benefits extend to the manufacturing of air ducts for environmental control systems. Its extensive use in the aerospace industry for parts like fuselage components suggests its potential for precision manufacturing of air ducts.
Radomes, crucial for protecting radar antennae, benefit from AFP's precision and material performance. NORDAM's use of AFP for SatCom radomes exemplifies how this technology can produce high-strength, precision-made components for critical communication systems.
The transformative impact of Automated Fiber Placement (AFP) in aerospace manufacturing is undeniably profound. From structural integrity to precision in complex components, AFP has proven to be more than just a technique; it's a cornerstone in the evolution of aerospace engineering. The future of AFP promises further innovation, with potential expansion into new materials and applications that could redefine the boundaries of aircraft and spacecraft design. As the industry continues to strive for greater efficiency and performance, AFP stands as a key enabler, poised to meet the challenges of tomorrow's aerospace ambitions.
Discover the future of composite manufacturing with Addcomposites! Here's how you can get involved:
At Addcomposites, we are dedicated to revolutionizing composite manufacturing. Our AFP systems and comprehensive support services are waiting for you to harness. So, don't wait – get started on your journey to the future of manufacturing today!