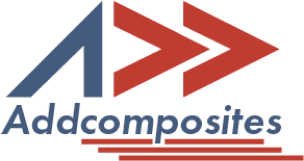
The manufacturing and recycling of Carbon Fiber Reinforced Thermoplastics (CFRTP) present multifaceted challenges that have become pivotal in the materials engineering and composites manufacturing sectors. These challenges stem from CFRTP's unique material properties, which, while advantageous in application, complicate their production and end-of-life processing. Herein, we explore the primary obstacles identified in the literature, focusing on technological, economic, and environmental aspects.
while CFRTP composites offer significant advantages for a range of applications, addressing their manufacturing and recycling challenges is crucial for their sustainable integration into future materials engineering and manufacturing strategies. The research and development efforts in this field are geared towards overcoming these barriers, aiming for a future where CFRTP can be widely used in a manner that is both economically and environmentally sustainable.
The production and recycling of CFRTP encompass a variety of complex challenges that significantly impact their overall cost-effectiveness and environmental sustainability. These complexities are primarily rooted in the inherent properties of CFRTP materials, the sophistication of their manufacturing processes, and the intricacies involved in their end-of-life recycling stages.
while CFRTP materials offer significant advantages in terms of performance and potential for sustainability, addressing the challenges associated with their production and recycling is crucial for their broader adoption and environmental impact mitigation. The research and development in this field continue to seek more efficient, cost-effective, and environmentally friendly methods for CFRTP manufacturing and end-of-life processing.
The manufacturing and recycling of Carbon Fiber Reinforced Thermoplastics (CFRTP) are undergoing revolutionary changes through the adoption of innovative techniques, addressing challenges that have historically limited their wider application. This evolution is characterized by advancements in both conventional and automated manufacturing methods, alongside novel approaches to recycling. These innovations promise to enhance the efficiency, cost-effectiveness, and environmental sustainability of CFRTP production and end-of-life management.
the advancements in the manufacturing and recycling of CFRTP reflect a growing trend towards more sustainable, efficient, and cost-effective methods. These innovations not only overcome previous limitations but also open new possibilities for the application of CFRTP in various industries, promising a future where these materials play a central role in the development of lightweight, high-performance, and environmentally friendly products.
The field of CFRTP has witnessed significant advancements and is poised for future growth across various industrial sectors. This section delves into the remarkable developments, the promising applications of CFRTP composites, and the strategic directions that could shape the future of this innovative material.
1. Technological Breakthroughs in CFRTP Composites:
2. Expansion in Industrial Applications:
3. Future Directions and Opportunities:
CFRTP technology stands at the brink of revolutionizing materials engineering and manufacturing across multiple industries. The continued exploration of its applications, coupled with advancements in manufacturing and recycling techniques, promises to unlock new potentials for CFRTP composites. This innovative material not only offers superior performance and environmental sustainability but also opens avenues for future research and development aimed at overcoming current limitations and exploiting its full range of benefits.
We sincerely thank Alaa M. Almushaikeh, Saleh O. Alaswad, Mohammed S. Alsuhybani, Bandar M. AlOtaibi, Ibrahim M. Alarifi, Naif B. Alqahtani, Salem M. Aldosari, Sami S. Alsaleh, Ahmed S. Haidyrah, Alanood A. Alolyan, and Basheer A. Alshammari for their significant contributions detailed in "Manufacturing of carbon fiber reinforced thermoplastics and its recovery of carbon fiber: A review." Their pioneering work in CFRTP technology has greatly enhanced our blog's depth, offering insights into the challenges, advancements, and sustainable practices within the field. Their research is instrumental in pushing the boundaries of material science, guiding us toward innovative solutions and sustainable futures.
Discover the future of composite manufacturing with Addcomposites! Here's how you can get involved:
At Addcomposites, we are dedicated to revolutionizing composite manufacturing. Our AFP systems and comprehensive support services are waiting for you to harness. So, don't wait – get started on your journey to the future of manufacturing today!
The manufacturing and recycling of Carbon Fiber Reinforced Thermoplastics (CFRTP) present multifaceted challenges that have become pivotal in the materials engineering and composites manufacturing sectors. These challenges stem from CFRTP's unique material properties, which, while advantageous in application, complicate their production and end-of-life processing. Herein, we explore the primary obstacles identified in the literature, focusing on technological, economic, and environmental aspects.
while CFRTP composites offer significant advantages for a range of applications, addressing their manufacturing and recycling challenges is crucial for their sustainable integration into future materials engineering and manufacturing strategies. The research and development efforts in this field are geared towards overcoming these barriers, aiming for a future where CFRTP can be widely used in a manner that is both economically and environmentally sustainable.
The production and recycling of CFRTP encompass a variety of complex challenges that significantly impact their overall cost-effectiveness and environmental sustainability. These complexities are primarily rooted in the inherent properties of CFRTP materials, the sophistication of their manufacturing processes, and the intricacies involved in their end-of-life recycling stages.
while CFRTP materials offer significant advantages in terms of performance and potential for sustainability, addressing the challenges associated with their production and recycling is crucial for their broader adoption and environmental impact mitigation. The research and development in this field continue to seek more efficient, cost-effective, and environmentally friendly methods for CFRTP manufacturing and end-of-life processing.
The manufacturing and recycling of Carbon Fiber Reinforced Thermoplastics (CFRTP) are undergoing revolutionary changes through the adoption of innovative techniques, addressing challenges that have historically limited their wider application. This evolution is characterized by advancements in both conventional and automated manufacturing methods, alongside novel approaches to recycling. These innovations promise to enhance the efficiency, cost-effectiveness, and environmental sustainability of CFRTP production and end-of-life management.
the advancements in the manufacturing and recycling of CFRTP reflect a growing trend towards more sustainable, efficient, and cost-effective methods. These innovations not only overcome previous limitations but also open new possibilities for the application of CFRTP in various industries, promising a future where these materials play a central role in the development of lightweight, high-performance, and environmentally friendly products.
The field of CFRTP has witnessed significant advancements and is poised for future growth across various industrial sectors. This section delves into the remarkable developments, the promising applications of CFRTP composites, and the strategic directions that could shape the future of this innovative material.
1. Technological Breakthroughs in CFRTP Composites:
2. Expansion in Industrial Applications:
3. Future Directions and Opportunities:
CFRTP technology stands at the brink of revolutionizing materials engineering and manufacturing across multiple industries. The continued exploration of its applications, coupled with advancements in manufacturing and recycling techniques, promises to unlock new potentials for CFRTP composites. This innovative material not only offers superior performance and environmental sustainability but also opens avenues for future research and development aimed at overcoming current limitations and exploiting its full range of benefits.
We sincerely thank Alaa M. Almushaikeh, Saleh O. Alaswad, Mohammed S. Alsuhybani, Bandar M. AlOtaibi, Ibrahim M. Alarifi, Naif B. Alqahtani, Salem M. Aldosari, Sami S. Alsaleh, Ahmed S. Haidyrah, Alanood A. Alolyan, and Basheer A. Alshammari for their significant contributions detailed in "Manufacturing of carbon fiber reinforced thermoplastics and its recovery of carbon fiber: A review." Their pioneering work in CFRTP technology has greatly enhanced our blog's depth, offering insights into the challenges, advancements, and sustainable practices within the field. Their research is instrumental in pushing the boundaries of material science, guiding us toward innovative solutions and sustainable futures.
Discover the future of composite manufacturing with Addcomposites! Here's how you can get involved:
At Addcomposites, we are dedicated to revolutionizing composite manufacturing. Our AFP systems and comprehensive support services are waiting for you to harness. So, don't wait – get started on your journey to the future of manufacturing today!