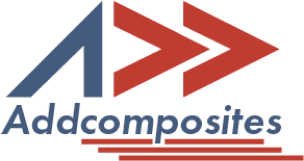
The Automated Fibre Placement (AFP) process, a cornerstone of contemporary composite manufacturing, has evolved significantly to cater to the growing demand for high-strength, lightweight materials, especially in aerospace and automotive industries. This evolution, however, is not without its complexities and challenges.
AFP technology, known for its ability to lay down composite materials accurately and efficiently, faces a myriad of challenges stemming from the inherent complexities of the process itself. One of the primary hurdles is the management of process variables that significantly impact the quality and integrity of the final composite component. These variables include the temperature at the nip-point of the roller, compaction pressure, and lay-up speed, each playing a crucial role in determining the quality of the manufactured component.
The temperature at the nip-point, for example, is critical for ensuring proper adhesion between layers and the removal of voids, which are crucial for the structural integrity of the component. Managing this temperature requires precision, as too much heat can degrade the composite material, while insufficient heat may lead to poor adhesion and delamination issues. Similarly, compaction pressure must be meticulously controlled to achieve the desired consolidation without damaging the fibres or causing defects like wrinkling or misalignment.
Furthermore, the lay-up speed needs to be optimized to balance manufacturing efficiency with quality. Higher speeds can reduce production times but may compromise the material's ability to properly bond and consolidate. Conversely, slower speeds enhance quality but may not be economically viable for large-scale production.
Another significant challenge is the automation of the AFP process. While automation offers numerous benefits, including increased precision and reduced labor costs, it also requires sophisticated software and hardware capable of handling the complexities of composite lay-up. This includes advanced path planning algorithms to navigate complex geometries and the integration of real-time monitoring systems to adjust process parameters on the fly.
Despite these challenges, advancements in machine learning and data-driven methodologies are beginning to offer promising solutions. By analyzing vast amounts of process data, these technologies can predict and mitigate potential quality issues before they occur, thus paving the way for more reliable and efficient AFP manufacturing processes.
Navigating the intricate landscape of Automated Fibre Placement (AFP) involves a detailed understanding of the process variables that significantly impact the quality of composite manufacturing. Among these, the temperature at the nip-point, compaction pressure, and lay-up speed stand out as pivotal factors, each carrying its weight in the balance of efficiency and excellence.
Addressing these intricacies necessitates a comprehensive understanding of the interplay between these variables and their collective impact on the AFP process. Innovations in real-time monitoring and control technologies have begun to offer solutions, enabling more precise adjustments to process parameters on the fly. Additionally, the advent of machine learning and data-driven approaches provides a promising avenue for predictive adjustments, potentially revolutionizing the way these process variables are managed.
Despite the focused exploration of these process variables, one area that remains less explored is the real-world application and validation of data-driven models in diverse manufacturing environments.
The automated lay-up of composites, particularly throughAFP, stands at the cusp of a significant evolution, driven by the integration of data-driven methodologies. These innovative approaches harness machine learning (ML) and artificial intelligence (AI) to tackle the inherent complexities and enhance the quality and efficiency of the AFP process.
The journey into leveraging data-driven methodologies begins with a deep dive into the process variables critical to AFP: temperature at the nip-point, compaction pressure, and lay-up speed. These variables, if not meticulously managed, can lead to defects that significantly undermine the structural integrity and performance of the final composite components. The conventional approach to managing these variables often relies on operator experience and trial-and-error adjustments, which, while effective to a degree, fall short of the precision required for optimal performance.
ML and big data analytics offer a paradigm shift in how these process variables are monitored and controlled. By collecting extensive datasets on the AFP process, including temperature profiles, pressure readings, and lay-up speeds across different materials and geometries, ML algorithms can identify patterns and correlations that may not be immediately apparent to human operators.
For instance, predictive models can forecast the optimal temperature settings for the nip-point based on the material being used, the specific geometry of the part, and the ambient conditions in the manufacturing environment. These models can adjust in real-time, ensuring the AFP process remains within the ideal parameters to maximize adhesion and minimize defects.
Similarly, ML algorithms can optimize compaction pressure and lay-up speed, balancing the need for rapid production with the imperative of maintaining high-quality outcomes. By analyzing historical data, these algorithms can predict the best settings for new parts, significantly reducing the time and material waste associated with trial-and-error methods.
A comprehensive analysis of implementing data-driven methodologies within the AFP process, detailing the development of predictive models and their potential impact on manufacturing outcomes. However, one aspect that emerges as a challenge is the integration of these methodologies into existing manufacturing workflows. Many companies may lack the infrastructure or expertise to implement and maintain sophisticated ML models, presenting a barrier to adoption.
Here we outlines the theoretical and initial practical applications of these models, further research could explore the scalability of such approaches. As companies vary in size, technical capability, and market focus, the adaptability of data-driven methodologies to a wide range of manufacturing environments remains an area ripe for exploration.
The culmination of integrating data-driven methodologies into AFP manufacturing represents a significant leap forward in the composite industry. The promise of these technologies is not just in enhancing existing processes but in fundamentally transforming the approach to composite manufacturing, enabling unprecedented levels of precision, efficiency, and quality.
The application of machine learning (ML) models to predict and optimize AFP process variables such as nip-point temperature, compaction pressure, and lay-up speed has demonstrated the potential to significantly reduce defects and improve material utilization. These advancements are crucial for industries where the performance-to-weight ratio of materials is paramount, such as aerospace, automotive, and renewable energy sectors.
One of the key findings is the successful development and deployment of predictive models that can accurately forecast optimal process parameters for different composite materials and component geometries.
By training on vast datasets encompassing various manufacturing scenarios, these models can anticipate potential issues before they manifest, allowing for preemptive adjustments to the manufacturing process. This capability not only minimizes waste but also accelerates the development cycle for new composite components, providing a competitive edge in fast-paced markets.
Furthermore, the research explores the integration of data-driven insights directly into the manufacturing workflow. This approach enables a more responsive and adaptable manufacturing process, where adjustments can be made in real-time based on continuous feedback from the AFP machine itself. The result is a dynamic, self-optimizing manufacturing system that can adapt to changes in material properties, environmental conditions, and design requirements with minimal human intervention.
Despite these advancements, challenges remain in the broader adoption of data-driven methodologies within the composite manufacturing industry. The research identifies the need for more robust and user-friendly tools that can lower the barrier to entry for companies looking to leverage ML and AI in their manufacturing processes. Additionally, there remains a gap in understanding how these technologies can be integrated into legacy systems and workflows, which are prevalent in the industry.
Looking ahead, the SOA suggests several areas for further research and development. These include the exploration of more sophisticated ML algorithms capable of handling the highly nonlinear and complex nature of composite manufacturing processes, as well as the development of standardized protocols for data collection and analysis to facilitate wider adoption of these technologies.
In crafting this blog, a significant acknowledgment is due to the foundational work laid down in Philip Druiff's dissertation, "Data-driven Manufacturing in the Automated Lay-up of Composites." This comprehensive study not only navigates through the complexities inherent in Automated Fibre Placement (AFP) but also paves the way for transformative methodologies that could redefine the future of composite manufacturing.
Druiff's in-depth exploration of AFP process variables, coupled with his innovative approach towards integrating machine learning and data analytics, offers a fresh perspective on optimizing manufacturing processes. His contributions provide both a technical foundation and a visionary outlook on harnessing data-driven insights to enhance precision, efficiency, and quality in composite manufacturing.
This blog owes much to the pioneering research and analytical rigor demonstrated in Druiff's work. His dedication to advancing the field of composite manufacturing, through both theoretical exploration and practical application, sets a benchmark for future research and development in this domain.
The Automated Fibre Placement (AFP) process, a cornerstone of contemporary composite manufacturing, has evolved significantly to cater to the growing demand for high-strength, lightweight materials, especially in aerospace and automotive industries. This evolution, however, is not without its complexities and challenges.
AFP technology, known for its ability to lay down composite materials accurately and efficiently, faces a myriad of challenges stemming from the inherent complexities of the process itself. One of the primary hurdles is the management of process variables that significantly impact the quality and integrity of the final composite component. These variables include the temperature at the nip-point of the roller, compaction pressure, and lay-up speed, each playing a crucial role in determining the quality of the manufactured component.
The temperature at the nip-point, for example, is critical for ensuring proper adhesion between layers and the removal of voids, which are crucial for the structural integrity of the component. Managing this temperature requires precision, as too much heat can degrade the composite material, while insufficient heat may lead to poor adhesion and delamination issues. Similarly, compaction pressure must be meticulously controlled to achieve the desired consolidation without damaging the fibres or causing defects like wrinkling or misalignment.
Furthermore, the lay-up speed needs to be optimized to balance manufacturing efficiency with quality. Higher speeds can reduce production times but may compromise the material's ability to properly bond and consolidate. Conversely, slower speeds enhance quality but may not be economically viable for large-scale production.
Another significant challenge is the automation of the AFP process. While automation offers numerous benefits, including increased precision and reduced labor costs, it also requires sophisticated software and hardware capable of handling the complexities of composite lay-up. This includes advanced path planning algorithms to navigate complex geometries and the integration of real-time monitoring systems to adjust process parameters on the fly.
Despite these challenges, advancements in machine learning and data-driven methodologies are beginning to offer promising solutions. By analyzing vast amounts of process data, these technologies can predict and mitigate potential quality issues before they occur, thus paving the way for more reliable and efficient AFP manufacturing processes.
Navigating the intricate landscape of Automated Fibre Placement (AFP) involves a detailed understanding of the process variables that significantly impact the quality of composite manufacturing. Among these, the temperature at the nip-point, compaction pressure, and lay-up speed stand out as pivotal factors, each carrying its weight in the balance of efficiency and excellence.
Addressing these intricacies necessitates a comprehensive understanding of the interplay between these variables and their collective impact on the AFP process. Innovations in real-time monitoring and control technologies have begun to offer solutions, enabling more precise adjustments to process parameters on the fly. Additionally, the advent of machine learning and data-driven approaches provides a promising avenue for predictive adjustments, potentially revolutionizing the way these process variables are managed.
Despite the focused exploration of these process variables, one area that remains less explored is the real-world application and validation of data-driven models in diverse manufacturing environments.
The automated lay-up of composites, particularly throughAFP, stands at the cusp of a significant evolution, driven by the integration of data-driven methodologies. These innovative approaches harness machine learning (ML) and artificial intelligence (AI) to tackle the inherent complexities and enhance the quality and efficiency of the AFP process.
The journey into leveraging data-driven methodologies begins with a deep dive into the process variables critical to AFP: temperature at the nip-point, compaction pressure, and lay-up speed. These variables, if not meticulously managed, can lead to defects that significantly undermine the structural integrity and performance of the final composite components. The conventional approach to managing these variables often relies on operator experience and trial-and-error adjustments, which, while effective to a degree, fall short of the precision required for optimal performance.
ML and big data analytics offer a paradigm shift in how these process variables are monitored and controlled. By collecting extensive datasets on the AFP process, including temperature profiles, pressure readings, and lay-up speeds across different materials and geometries, ML algorithms can identify patterns and correlations that may not be immediately apparent to human operators.
For instance, predictive models can forecast the optimal temperature settings for the nip-point based on the material being used, the specific geometry of the part, and the ambient conditions in the manufacturing environment. These models can adjust in real-time, ensuring the AFP process remains within the ideal parameters to maximize adhesion and minimize defects.
Similarly, ML algorithms can optimize compaction pressure and lay-up speed, balancing the need for rapid production with the imperative of maintaining high-quality outcomes. By analyzing historical data, these algorithms can predict the best settings for new parts, significantly reducing the time and material waste associated with trial-and-error methods.
A comprehensive analysis of implementing data-driven methodologies within the AFP process, detailing the development of predictive models and their potential impact on manufacturing outcomes. However, one aspect that emerges as a challenge is the integration of these methodologies into existing manufacturing workflows. Many companies may lack the infrastructure or expertise to implement and maintain sophisticated ML models, presenting a barrier to adoption.
Here we outlines the theoretical and initial practical applications of these models, further research could explore the scalability of such approaches. As companies vary in size, technical capability, and market focus, the adaptability of data-driven methodologies to a wide range of manufacturing environments remains an area ripe for exploration.
The culmination of integrating data-driven methodologies into AFP manufacturing represents a significant leap forward in the composite industry. The promise of these technologies is not just in enhancing existing processes but in fundamentally transforming the approach to composite manufacturing, enabling unprecedented levels of precision, efficiency, and quality.
The application of machine learning (ML) models to predict and optimize AFP process variables such as nip-point temperature, compaction pressure, and lay-up speed has demonstrated the potential to significantly reduce defects and improve material utilization. These advancements are crucial for industries where the performance-to-weight ratio of materials is paramount, such as aerospace, automotive, and renewable energy sectors.
One of the key findings is the successful development and deployment of predictive models that can accurately forecast optimal process parameters for different composite materials and component geometries.
By training on vast datasets encompassing various manufacturing scenarios, these models can anticipate potential issues before they manifest, allowing for preemptive adjustments to the manufacturing process. This capability not only minimizes waste but also accelerates the development cycle for new composite components, providing a competitive edge in fast-paced markets.
Furthermore, the research explores the integration of data-driven insights directly into the manufacturing workflow. This approach enables a more responsive and adaptable manufacturing process, where adjustments can be made in real-time based on continuous feedback from the AFP machine itself. The result is a dynamic, self-optimizing manufacturing system that can adapt to changes in material properties, environmental conditions, and design requirements with minimal human intervention.
Despite these advancements, challenges remain in the broader adoption of data-driven methodologies within the composite manufacturing industry. The research identifies the need for more robust and user-friendly tools that can lower the barrier to entry for companies looking to leverage ML and AI in their manufacturing processes. Additionally, there remains a gap in understanding how these technologies can be integrated into legacy systems and workflows, which are prevalent in the industry.
Looking ahead, the SOA suggests several areas for further research and development. These include the exploration of more sophisticated ML algorithms capable of handling the highly nonlinear and complex nature of composite manufacturing processes, as well as the development of standardized protocols for data collection and analysis to facilitate wider adoption of these technologies.
In crafting this blog, a significant acknowledgment is due to the foundational work laid down in Philip Druiff's dissertation, "Data-driven Manufacturing in the Automated Lay-up of Composites." This comprehensive study not only navigates through the complexities inherent in Automated Fibre Placement (AFP) but also paves the way for transformative methodologies that could redefine the future of composite manufacturing.
Druiff's in-depth exploration of AFP process variables, coupled with his innovative approach towards integrating machine learning and data analytics, offers a fresh perspective on optimizing manufacturing processes. His contributions provide both a technical foundation and a visionary outlook on harnessing data-driven insights to enhance precision, efficiency, and quality in composite manufacturing.
This blog owes much to the pioneering research and analytical rigor demonstrated in Druiff's work. His dedication to advancing the field of composite manufacturing, through both theoretical exploration and practical application, sets a benchmark for future research and development in this domain.