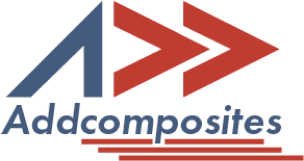
TLDR
Additive manufacturing (AM) of continuous carbon fiber composites faces unique challenges, primarily due to the nature of carbon fiber-reinforced polymers (CFRP). These challenges stem from CFRP's inherent material properties and the limitations of current AM technologies. One of the main hurdles is achieving optimal fiber orientation and distribution within the printed parts, which is crucial for harnessing the full strength and stiffness potential of carbon fibers. Traditional AM methods, like Fused Deposition Modeling (FDM), struggle with this because they typically lay down material in planar layers, which can lead to suboptimal mechanical properties in the final parts due to weak interlayer adhesion and the inability to align fibers along the principal stress directions of the part.
Moreover, most AM technologies are not designed to handle the continuous fibers effectively, which can result in additional challenges, such as the interruption of fiber continuity or the difficulty in achieving complex geometries with optimal fiber paths. This not only limits the design freedom but also the applicability of AM for producing high-performance components that can meet the rigorous demands of industries such as aerospace, automotive, and sports equipment, where the strength-to-weight ratio is of paramount importance.
To address these challenges, the document discusses an innovative approach that involves a nonplanar slicing technique, designed to optimize the orientation of carbon fibers throughout the part by following the load paths and principal stress directions. This method aims to overcome the limitations of traditional layer-by-layer printing, offering a potential solution to the complex problem of fabricating high-strength, lightweight CFRP parts using additive manufacturing. However, implementing such advanced techniques requires sophisticated software and hardware capabilities, indicating a gap between the current state of AM technologies and the ideal scenario where complex carbon fiber composites can be manufactured with ease, efficiency, and superior performance characteristics.
A significant pain point in the additive manufacturing (AM) of continuous carbon fiber-reinforced polymers (CFRP) is the weak interlayer adhesion in fused deposition modeling (FDM). This problem arises because the FDM process builds parts layer by layer, with each layer typically being deposited in a planar fashion. While FDM offers the advantage of creating complex geometries with relative ease, the method inherently introduces weaknesses between these layers. Such weaknesses are particularly pronounced when manufacturing parts intended to bear loads, as the interlayer adhesion does not fully capitalize on the strength properties of continuous carbon fibers.
Interlayer adhesion's weakness is a multifaceted problem, impacting not only the mechanical strength and durability of the parts but also their reliability and performance in critical applications. In industries where safety and performance are paramount, such as aerospace, automotive, and sporting goods, the demand for high-strength and lightweight components means that any compromise in material integrity can be a significant setback. This issue is further exacerbated by the limitations in controlling fiber orientation precisely within each layer, which is crucial for maximizing the mechanical properties of CFRP.
The document details how traditional FDM approaches struggle to overcome this challenge, highlighting the need for innovative solutions that can enhance interlayer bonding without compromising the inherent benefits of carbon fiber materials. Addressing this issue is not just about improving the mechanical properties of the printed parts but also about expanding the potential applications of CFRP in AM, thereby unlocking new possibilities for design and manufacturing in various high-performance sectors.
The document introduces a groundbreaking approach to overcome the weak interlayer adhesion problem in fused deposition modeling (FDM) of continuous carbon fiber-reinforced polymers (CFRP). This innovative method, known as the load-oriented nonplanar slicing approach, aims to significantly enhance the mechanical strength of CFRP parts by optimizing the orientation of carbon fibers according to the principal stress directions.
This technique departs from traditional planar layering, proposing a method where layers are deposited in a nonplanar fashion. By aligning the carbon fibers along the load paths, this approach seeks to ensure that the fibers bear the majority of the applied stress, thereby maximizing the part's overall strength and durability. The process involves a series of steps, including the identification of critical regions within the part, optimization of the vector and scalar fields to determine the ideal orientation of fibers, and the generation of nonplanar slicing paths that guide the deposition of the carbon fiber material.
Moreover, the document highlights the compatibility of this approach with multi-axis robotic 3D printing technologies, which are instrumental in realizing the nonplanar layers and complex geometries that traditional FDM printers cannot achieve. This advanced path planning technique not only addresses the challenge of weak interlayer adhesion but also paves the way for the creation of CFRP parts with significantly improved structural integrity and performance capabilities.
The adoption of the load-oriented nonplanar slicing approach represents a significant leap forward in the additive manufacturing of CFRP, offering a solution that could revolutionize the production of high-strength, lightweight components across various industries.
The culmination of this study introduces a solution that leverages advanced path planning and multi-axis printing techniques to optimize the manufacturing of continuous carbon fiber-reinforced polymers (CFRP) parts. This solution addresses the challenges previously identified, such as weak interlayer adhesion, by employing a sophisticated approach that aligns carbon fibers along the principal stress directions. The methodology entails a complex but effective process of critical region identification, vector and scalar field optimization, nonplanar slicing, support generation, and meticulous path planning.
The implementation of these techniques enables the production of CFRP parts that are not only structurally superior but also more efficient in terms of material use and weight. The document showcases experimental validation of this approach, illustrating its potential to significantly enhance the mechanical properties of 3D printed CFRP parts. By exploiting multi-axis robotic 3D printing, this solution opens up new possibilities for creating parts with complex geometries and optimized fiber orientation, pushing the boundaries of what's possible in additive manufacturing of composite materials.
We extend our sincere appreciation to Johann Kipping and Thorsten Schüppstuhl for their pivotal contributions to the study that served as the foundation for our blog post, "Revolutionizing Additive Manufacturing with Continuous Carbon Fiber Composites." Their dedication to advancing the field through innovative research has provided invaluable insights into optimizing the additive manufacturing process for continuous carbon fiber-reinforced polymers. Thank you, Johann and Thorsten, for your significant contributions and for enabling us to share your groundbreaking work with our audience.
Discover the future of composite manufacturing with Addcomposites! Here's how you can get involved:
At Addcomposites, we are dedicated to revolutionizing composite manufacturing. Our AFP systems and comprehensive support services are waiting for you to harness. So, don't wait – get started on your journey to the future of manufacturing today!
TLDR
Additive manufacturing (AM) of continuous carbon fiber composites faces unique challenges, primarily due to the nature of carbon fiber-reinforced polymers (CFRP). These challenges stem from CFRP's inherent material properties and the limitations of current AM technologies. One of the main hurdles is achieving optimal fiber orientation and distribution within the printed parts, which is crucial for harnessing the full strength and stiffness potential of carbon fibers. Traditional AM methods, like Fused Deposition Modeling (FDM), struggle with this because they typically lay down material in planar layers, which can lead to suboptimal mechanical properties in the final parts due to weak interlayer adhesion and the inability to align fibers along the principal stress directions of the part.
Moreover, most AM technologies are not designed to handle the continuous fibers effectively, which can result in additional challenges, such as the interruption of fiber continuity or the difficulty in achieving complex geometries with optimal fiber paths. This not only limits the design freedom but also the applicability of AM for producing high-performance components that can meet the rigorous demands of industries such as aerospace, automotive, and sports equipment, where the strength-to-weight ratio is of paramount importance.
To address these challenges, the document discusses an innovative approach that involves a nonplanar slicing technique, designed to optimize the orientation of carbon fibers throughout the part by following the load paths and principal stress directions. This method aims to overcome the limitations of traditional layer-by-layer printing, offering a potential solution to the complex problem of fabricating high-strength, lightweight CFRP parts using additive manufacturing. However, implementing such advanced techniques requires sophisticated software and hardware capabilities, indicating a gap between the current state of AM technologies and the ideal scenario where complex carbon fiber composites can be manufactured with ease, efficiency, and superior performance characteristics.
A significant pain point in the additive manufacturing (AM) of continuous carbon fiber-reinforced polymers (CFRP) is the weak interlayer adhesion in fused deposition modeling (FDM). This problem arises because the FDM process builds parts layer by layer, with each layer typically being deposited in a planar fashion. While FDM offers the advantage of creating complex geometries with relative ease, the method inherently introduces weaknesses between these layers. Such weaknesses are particularly pronounced when manufacturing parts intended to bear loads, as the interlayer adhesion does not fully capitalize on the strength properties of continuous carbon fibers.
Interlayer adhesion's weakness is a multifaceted problem, impacting not only the mechanical strength and durability of the parts but also their reliability and performance in critical applications. In industries where safety and performance are paramount, such as aerospace, automotive, and sporting goods, the demand for high-strength and lightweight components means that any compromise in material integrity can be a significant setback. This issue is further exacerbated by the limitations in controlling fiber orientation precisely within each layer, which is crucial for maximizing the mechanical properties of CFRP.
The document details how traditional FDM approaches struggle to overcome this challenge, highlighting the need for innovative solutions that can enhance interlayer bonding without compromising the inherent benefits of carbon fiber materials. Addressing this issue is not just about improving the mechanical properties of the printed parts but also about expanding the potential applications of CFRP in AM, thereby unlocking new possibilities for design and manufacturing in various high-performance sectors.
The document introduces a groundbreaking approach to overcome the weak interlayer adhesion problem in fused deposition modeling (FDM) of continuous carbon fiber-reinforced polymers (CFRP). This innovative method, known as the load-oriented nonplanar slicing approach, aims to significantly enhance the mechanical strength of CFRP parts by optimizing the orientation of carbon fibers according to the principal stress directions.
This technique departs from traditional planar layering, proposing a method where layers are deposited in a nonplanar fashion. By aligning the carbon fibers along the load paths, this approach seeks to ensure that the fibers bear the majority of the applied stress, thereby maximizing the part's overall strength and durability. The process involves a series of steps, including the identification of critical regions within the part, optimization of the vector and scalar fields to determine the ideal orientation of fibers, and the generation of nonplanar slicing paths that guide the deposition of the carbon fiber material.
Moreover, the document highlights the compatibility of this approach with multi-axis robotic 3D printing technologies, which are instrumental in realizing the nonplanar layers and complex geometries that traditional FDM printers cannot achieve. This advanced path planning technique not only addresses the challenge of weak interlayer adhesion but also paves the way for the creation of CFRP parts with significantly improved structural integrity and performance capabilities.
The adoption of the load-oriented nonplanar slicing approach represents a significant leap forward in the additive manufacturing of CFRP, offering a solution that could revolutionize the production of high-strength, lightweight components across various industries.
The culmination of this study introduces a solution that leverages advanced path planning and multi-axis printing techniques to optimize the manufacturing of continuous carbon fiber-reinforced polymers (CFRP) parts. This solution addresses the challenges previously identified, such as weak interlayer adhesion, by employing a sophisticated approach that aligns carbon fibers along the principal stress directions. The methodology entails a complex but effective process of critical region identification, vector and scalar field optimization, nonplanar slicing, support generation, and meticulous path planning.
The implementation of these techniques enables the production of CFRP parts that are not only structurally superior but also more efficient in terms of material use and weight. The document showcases experimental validation of this approach, illustrating its potential to significantly enhance the mechanical properties of 3D printed CFRP parts. By exploiting multi-axis robotic 3D printing, this solution opens up new possibilities for creating parts with complex geometries and optimized fiber orientation, pushing the boundaries of what's possible in additive manufacturing of composite materials.
We extend our sincere appreciation to Johann Kipping and Thorsten Schüppstuhl for their pivotal contributions to the study that served as the foundation for our blog post, "Revolutionizing Additive Manufacturing with Continuous Carbon Fiber Composites." Their dedication to advancing the field through innovative research has provided invaluable insights into optimizing the additive manufacturing process for continuous carbon fiber-reinforced polymers. Thank you, Johann and Thorsten, for your significant contributions and for enabling us to share your groundbreaking work with our audience.
Discover the future of composite manufacturing with Addcomposites! Here's how you can get involved:
At Addcomposites, we are dedicated to revolutionizing composite manufacturing. Our AFP systems and comprehensive support services are waiting for you to harness. So, don't wait – get started on your journey to the future of manufacturing today!