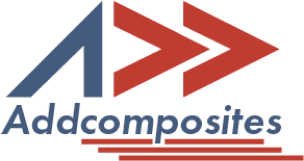
Welcome to the inaugural installment of our Composites Educational Hub series! Today, we embark on an exciting journey into the fascinating world of composite materials. This series is designed to cater to both industry professionals seeking to deepen their knowledge and curious academics eager to unravel the complexities of these revolutionary materials.
Before we delve into the intricacies of composites, we invite you to explore our comprehensive Composites Educational Hub. This resource provides a broader overview of the topics we'll be covering in this series, offering a roadmap for our educational journey together.
For a broader understanding of composite materials and their applications across various industries, check out our comprehensive guide on Where Are Composites Used.
At their core, composite materials, often simply referred to as composites, are a marvel of materials science. These engineered materials are born from the synergistic combination of two or more constituent materials, each possessing significantly different physical or chemical properties. The result of this union is nothing short of remarkable: a composite material that boasts characteristics distinctly different from its individual components, often superior in numerous aspects.
The science behind composites lies in the principle of combined action. By carefully selecting and combining materials, engineers can create a new material that leverages the strengths of its constituents while mitigating their individual weaknesses. This principle allows for the development of materials with previously unattainable combinations of properties, such as high strength coupled with low weight, or superior thermal resistance paired with excellent electrical conductivity.
To truly understand composites, we must first examine their fundamental components:
Understanding these building blocks and their interactions is key to grasping the fundamental principles of composite materials. As we progress through this series, we'll delve deeper into how these components are selected, combined, and processed to create composites with specific, desired properties for a wide range of applications.
For a more in-depth look at the various types of reinforcements used in composites, including their properties and applications, read our article on Reinforcement Fibers: Terminology, Types, and Formats.
In our next section, we'll take a fascinating journey through time, exploring the evolution of composites from ancient civilizations to modern industrial applications. This historical perspective will not only showcase human ingenuity but also set the stage for understanding the rapid advancements in composite technology we see today.
To delve deeper into the world of composite materials, explore our Introduction to Composite Materials post, which offers a more detailed explanation of their composition and properties.
The history of composite materials is a testament to human ingenuity, spanning millennia and crossing diverse civilizations. This journey not only illustrates the longstanding importance of composites but also provides valuable insights into the principles that guide modern composite design and manufacturing.
To learn more about how composite materials have evolved and their impact on modern industries, check out our History of Composites article.
Mongol Composite Bows (12th century A.D.): The Mongol warriors' composite bows represent a significant leap in composite technology. These bows were crafted from a sophisticated combination of materials including bamboo, silk, cattle tendons, horns, and pine resin. Each component played a crucial role:
This intricate design allowed the bow to store and release more energy than a simple wooden bow, resulting in increased range and power. The Mongol composite bow remained a feared weapon until the widespread adoption of firearms in the 14th century, demonstrating the potential of composites to create high-performance products.
Recent studies have shown that these 900-year-old bows are nearly as strong as modern composite bows, capable of hitting targets up to 450 meters away. This longevity and performance showcase the durability and effectiveness of well-designed composite materials.
The use of composites in warfare has continued to evolve. Today, advanced composites play a crucial role in defense applications. Learn more about modern military uses of composites in our Defense Applications overview.
The late 19th century marked a pivotal turning point in the history of composites with the development of synthetic resins. This period laid the groundwork for the modern era of engineered composite materials.
Synthetic Resins (1870-1890): The creation of the first synthetic resins that could be converted from a liquid to a solid state through polymerization was a revolutionary development. These resins provided a new type of matrix material with properties that could be more precisely controlled than natural alternatives. This development opened up new possibilities for creating composites with specific, tailored properties.
The evolution of composite materials has led to a wide range of resin systems. For a comparison of modern resin types, see our article on Thermoplastic vs. Thermoset Resins in FRP Composites.
The development of modern composites has paved the way for advanced manufacturing techniques. Learn about one of the most innovative methods in our Overview of Automated Fiber Placement Process article.
As we look to the future, the field of composite materials continues to evolve rapidly. Ongoing research focuses on developing more environmentally friendly and recyclable composites, as well as exploring new fibers and resins to expand the applications of these versatile materials. In our subsequent chapters, we'll delve deeper into these modern composites, their manufacturing processes, and their wide-ranging applications across industries.
Next, we'll explore the various types of composite materials, examining their unique properties and applications. Stay tuned as we continue our journey through the fascinating world of composites!
Addcomposites is at the forefront of this technology with our SCF3D (Structural Continuous Fiber 3D Printing) system, which combines the flexibility of 3D printing with the strength of continuous fiber reinforcement.
The world of composite materials is remarkably diverse, with each type of composite offering unique properties and advantages. Understanding these different types is crucial for engineers and materials scientists, as it allows for the selection of the most appropriate material for specific applications. Let's explore the main categories of composites, delving into their composition, properties, and real-world applications.
For a more detailed exploration of various composite types and their real-world applications, check out our article on Innovations in Composite Materials: Real-World Applications.
Polymer Matrix Composites, also known as Fiber Reinforced Polymers (FRPs), are the most commonly used type of composite material. They consist of a polymer resin as the matrix, with fibers as the reinforcement.
Composition:
Subcategories:
a) Thermoset Composites:
b) Thermoplastic Composites:
Key Characteristics:
Scientific Principle:
The performance of PMCs relies heavily on the interfacial bond between the fiber and matrix. This bond allows for effective load transfer from the matrix to the high-strength fibers. The orientation of fibers can be tailored to provide strength and stiffness in specific directions, leading to anisotropic properties.
Case Study:
The Boeing 787 Dreamliner extensively uses carbon fiber reinforced polymers (CFRPs) in its airframe, comprising about 50% of the aircraft by weight. This application of PMCs has resulted in a lighter, more fuel-efficient aircraft with improved passenger comfort due to higher cabin pressure and humidity levels.
Metal Matrix Composites use a metal as the matrix, reinforced with either particles or fibers.
Composition:
Key Characteristics:
Scientific Principle:
MMCs leverage the ductility and toughness of the metal matrix while benefiting from the high strength and stiffness of the ceramic reinforcement. The reinforcement impedes the movement of dislocations in the metal, leading to strengthening. In fiber-reinforced MMCs, load transfer from the matrix to the fibers is crucial for performance.
Applications:
Case Study:
The Toyota Altezza (sold as Lexus IS300 in some markets) uses an aluminum metal matrix composite cylinder block reinforced with alumina and short carbon fibers. This MMC engine block offers reduced weight and improved wear resistance compared to traditional cast iron blocks.
Ceramic Matrix Composites consist of ceramic fibers embedded in a ceramic matrix.
Composition:
Key Characteristics:
Scientific Principle:
CMCs address the inherent brittleness of ceramics by incorporating fibers that can deflect and bridge cracks. This crack deflection mechanism increases the energy required for crack propagation, resulting in a tougher material. The fiber-matrix interface is carefully engineered to allow for controlled debonding and sliding, further enhancing toughness.
Applications:
Case Study:
General Electric has developed silicon carbide CMCs for use in the hot section of jet engines. These CMCs can operate at higher temperatures than metal alloys, allowing for more efficient engine operation and reduced cooling requirements.
Carbon-Carbon Composites are a special class of composites where both the matrix and reinforcement are carbon.
Composition:
Key Characteristics:
Scientific Principle:
Carbon-carbon composites maintain their strength and stiffness at temperatures exceeding 2000°C, where most other materials would melt or degrade. This is due to the strong covalent bonds between carbon atoms in both the fibers and matrix.
Applications:
Case Study:
The nose cone and leading edges of the Space Shuttle used carbon-carbon composites due to their ability to withstand the extreme temperatures encountered during atmospheric reentry.
Hybrid Composites combine multiple types of reinforcements or matrices to achieve specific property combinations.
Composition:
Various combinations, such as:
Key Characteristics:
Scientific Principle:
Hybrid composites allow for the optimization of multiple properties simultaneously. For example, combining carbon and glass fibers can provide the high stiffness of carbon with the lower cost of glass, resulting in a material with intermediate properties and cost.
Applications:
Case Study:
The BMW i3 electric vehicle uses a hybrid composite structure in its passenger cell. The roof is made of recycled carbon fiber reinforced plastic (CFRP) for strength and low weight, while other parts use glass fiber reinforced plastic (GFRP) to balance cost and performance.
Understanding these different types of composites is crucial for materials selection in engineering design. Each type offers unique advantages and challenges, and the choice of composite depends on the specific requirements of the application, including mechanical properties, operating environment, manufacturing considerations, and cost constraints.
In our next section, we'll delve into the advantages and limitations of composite materials, providing a balanced view of their capabilities and challenges. This understanding will be crucial as we explore the applications of composites in various industries in future chapters of our series.
As with any class of materials, composite materials come with their own set of advantages and limitations. Understanding these is crucial for engineers, designers, and researchers when considering composites for specific applications. Let's explore these aspects in detail, providing a balanced view of the capabilities and challenges associated with composite materials.
Understanding the strengths and challenges of composites is crucial for effective application. For insights into overcoming some of these challenges, read our post on Challenges of Switching to Composite Materials.
Despite these limitations, the advantages of composites often outweigh the drawbacks in many applications. As research and development in composite materials continue, many of these limitations are being addressed through new materials, manufacturing processes, and design techniques.
In our next installment, we'll explore the future trends and innovations in the field of composite materials, examining how ongoing research is pushing the boundaries of what's possible with these versatile materials. Stay tuned as we continue our journey through the fascinating world of composites!
As we conclude this inaugural chapter of our Composites Educational Hub series, let's reflect on the key concepts we've explored and consider the exciting frontiers that lie ahead in the world of composite materials.
As we look to the future, the field of composite materials continues to evolve rapidly, driven by technological advancements and pressing global challenges. In our upcoming installments, we'll explore several exciting areas of development:
As we conclude this chapter, we invite you to reflect on the vast potential of composite materials. Whether you're a student, a professional engineer, or a curious learner, the world of composites offers endless opportunities for innovation and discovery.
In our next installment, we'll delve deeper into the science of fiber reinforcement, exploring how the type, orientation, and volume fraction of fibers influence the properties of composite materials. We'll examine the micromechanics of fiber-matrix interactions and discuss how this understanding informs the design of high-performance composites.
We encourage you to engage with the material, ask questions, and consider how the principles we've discussed might apply to your own field of interest or study. The journey into the world of composites is just beginning, and we look forward to exploring this fascinating field together in the chapters to come.
Thank you for joining us in this exploration of composite materials. Stay tuned for our next chapter, where we'll continue to unravel the complexities and possibilities of these remarkable materials!
To stay updated on the latest advancements in composite materials and manufacturing techniques, explore our Composites Educational Hub for regular insights and industry news.
Discover the future of composite manufacturing with Addcomposites! Here's how you can get involved:
At Addcomposites, we are dedicated to revolutionizing composite manufacturing. Our AFP systems and comprehensive support services are waiting for you to harness. So, don't wait – get started on your journey to the future of manufacturing today!