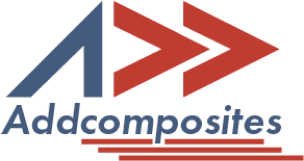
Recent advancements in composite manufacturing have demonstrated that the strategic integration of Automated Fiber Placement (AFP) and filament winding technologies creates synergistic capabilities far exceeding those of either method in isolation. This fusion enables unprecedented design freedom, material efficiency, and production flexibility across aerospace, energy storage, and transportation sectors [1][5][6].
Modern hybrid systems like Addcomposites' AFP-XS exemplify the physical integration of AFP and filament winding through multi-process toolheads that operate on shared robotic platforms [1][6]. These systems feature:
The AFP-XS configuration enables process switching within software through just advanced planning module, compared to traditional 8+ hour changeovers between separate AFP and winding systems [6][11]. This hardware convergence reduces footprint requirements by 100% while maintaining full functionality of both technologies [5][11].
AddPath's integrated programming environment represents a breakthrough in hybrid process control, combining:
This software integration enables first-pass success rates exceeding 92% for complex hybrid layups, compared to 65–75% for separately programmed processes [5][6].
Hybrid systems demonstrate 80–85% cycle time reductions through strategic process allocation:
Material utilization improvements reach 22% through:
Lifecycle cost analyses show 50-60% savings over 5 years compared to maintaining separate AFP and winding systems [5][6]:
Data aggregated from [5][6][11]
The hybrid process enables novel configurations unachievable with individual technologies:
Use Case: Next-gen hydrogen tanks demonstrate 41% weight reduction through:
Process compatibility with diverse material forms enables:
Hybrid systems overcome traditional thermoplastic processing limits through:
The integration supports circular economy objectives through:
End-of-life disassembly via targeted thermal debonding of hybrid joints [13][16]
ArianeGroup's prototype cryogenic tank demonstrates hybrid manufacturing advantages:
BMW's Neue Klasse platform utilizes:
Emerging innovations focus on:
Industry adoption metrics project:
This technological convergence redefines composite manufacturing capabilities, enabling lighter, stronger, and more sustainable structures across industries. Manufacturers adopting hybrid systems position themselves at the forefront of advanced materials innovation while realizing significant operational efficiencies.