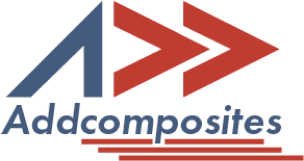
Laser-assisted automated fiber placement (LAFP) is a promising manufacturing technique for producing high-complexity and large-size thermoplastic composite structures, such as those made from carbon fiber-reinforced polyether ether ketone (CF/PEEK). However, LAFP-manufactured parts often suffer from several critical weaknesses:
These issues arise primarily due to the extremely short time (<1 second) available for achieving interlaminar bonding during the LAFP process. Incomplete interlaminar contact leads to void formation, while insufficient interdiffusion of polymer chains results in suboptimal mechanical properties.
Existing approaches to address these challenges include:
Method
Description
Drawbacks
Elevating tool temperature
Enables isothermal crystallization within processing window
Less feasible for large parts
Post-consolidation (autoclave, thermoforming)
Provides time for interdiffusion and consolidation
Additional processing time and energy
Repass treatment
Multiple localized heatings promote interlaminar bonding
Significantly reduces laydown efficiency
While these techniques can improve part quality, they either increase complexity or reduce the manufacturing efficiency that makes LAFP so attractive in the first place. Therefore, there remains a strong need for an LAFP manufacturing strategy that can simultaneously optimize both part quality and production efficiency for high-performance thermoplastic composites like CF/PEEK.
The extremely short time available for interlaminar bonding during laser-assisted automated fiber placement (LAFP) often leads to poor consolidation quality in the resulting CF/PEEK composite parts. Key problems include:
These poor interlaminar properties severely restrict the use of LAFP-manufactured thermoplastic composites in demanding aerospace applications. Current methods to improve part quality, such as elevating tool temperature, offline autoclave/ thermoforming post-consolidation, or laser repass treatments, all introduce additional cost and complexity while reducing the baseline speed and efficiency of the LAFP process.
The need to interrupt tape laying for multiple localized repass heating steps is especially detrimental to LAFP laydown rates. For example, applying a typical repass treatment to a 30-ply CF/PEEK laminate can double the required manufacturing time compared to single-pass LAFP. Therefore, the CF/PEEK composites industry requires an LAFP processing innovation that enhances interlaminar properties to aerospace-grade levels without compromising on laydown efficiency.
To address the challenges of poor interlaminar properties and reduced laydown efficiency in LAFP-manufactured CF/PEEK composites, the authors investigated an in-situ infrared annealing (IIA) approach. The key aspects of the IIA process are:
The researchers systematically compared the effects of IIA processing to untreated and laser repass treated LAFP samples:
Key findings demonstrate that IIA can provide heating power up to 700 W, sufficient to:
IIA Power
Effect
300-500 W
Exceed T_melt in first ply
500-600 W
Exceed T_melt in top 2 plies
700 W
Partially melt 3rd ply, fully melt and slowly cool top 2 plies
This localized remelting and slow cooling enables void reduction, polymer healing, and stress relief through IIA. The slow cooling rates (30-70% lower than repass) also promote high crystallinity.
Unlike repass treatments that require multiple heating steps, IIA achieves high crystallinity (up to 33.8%) within a single tape laying pass. This makes IIA a promising method to obtain aerospace-grade interlaminar properties in LAFP-manufactured CF/PEEK composites without sacrificing laydown efficiency.
The in-situ infrared annealing (IIA) method proved highly effective at enhancing the quality of LAFP-manufactured CF/PEEK composites while maintaining high laydown rates. Compared to untreated LAFP samples, laminates produced with 700 W IIA showed:
These mechanical properties are comparable to those achieved by laser repass treatment (ILSS = 72.3 MPa, GIC = 751.2 J/m2) while maintaining the full laydown speed of single-pass LAFP. The IIA method also provides more consistent crystallinities through the laminate thickness and reduces warpage by 78.6% compared to untreated LAFP.
Key advantages of in-situ infrared annealing over other LAFP enhancement techniques include:
Technique
Drawbacks
IIA Advantages
Repass
Multiple heating steps reduce laydown rate
Single-pass processing maintains efficiency
Autoclave
Extremely low efficiency, additional costs
In-situ integration, no extra equipment
Thermoforming
Long cycle times, only for simple geometries
Adaptable to complex shapes, fast layup
By achieving aerospace-grade mechanical properties in a single efficient laydown pass, in-situ infrared annealing provides an attractive new solution for high quality, cost-effective LAFP manufacturing of thermoplastic composites. This breakthrough could help expand the use of materials like CF/PEEK in demanding lightweight structures across the aerospace, automotive, and renewable energy industries.
I would like to express my gratitude to the authors of the research paper "In-situ infrared annealing for laser-assisted automated fiber placement to enhance interlaminar properties without sacrificing laydown efficiency" - Xukang Wang, Cheng Chen, Shirui Hu, Zhikun Chen, Wei Jiang, Guancheng Shen, Zhigao Huang, and Huamin Zhou from the State Key Laboratory of Materials Processing and Die & Mould Technology, School of Materials Science and Engineering, Huazhong University of Science and Technology.Xukang Wang, Cheng Chen, Shirui Hu, Zhikun Chen, Wei Jiang, Guancheng Shen, Zhigao Huang, and Huamin Zhou's innovative research on the in-situ infrared annealing (IIA) method for enhancing the interlaminar properties and manufacturing efficiency of laser-assisted automated fiber placement (LAFP) of CF/PEEK composites provided the foundation and inspiration for this article. The novel approach and thorough experimental work presented in their paper were instrumental in developing the content and key takeaways shared here.
I appreciate Xukang Wang, Cheng Chen, Shirui Hu, Zhikun Chen, Wei Jiang, Guancheng Shen, Zhigao Huang, and Huamin Zhou's dedication to advancing composite manufacturing techniques and their clear, detailed presentation of the challenges, methods, and results. Their work has made a significant contribution to the field and opens up exciting new possibilities for high-performance thermoplastic composite fabrication.
Robotics Power displayed through Tesla Optimus Robot
Discover the future of composite manufacturing with Addcomposites! Here's how you can get involved:
At Addcomposites, we are dedicated to revolutionizing composite manufacturing. Our AFP systems and comprehensive support services are waiting for you to harness. So, don't wait – get started on your journey to the future of manufacturing today!
Laser-assisted automated fiber placement (LAFP) is a promising manufacturing technique for producing high-complexity and large-size thermoplastic composite structures, such as those made from carbon fiber-reinforced polyether ether ketone (CF/PEEK). However, LAFP-manufactured parts often suffer from several critical weaknesses:
These issues arise primarily due to the extremely short time (<1 second) available for achieving interlaminar bonding during the LAFP process. Incomplete interlaminar contact leads to void formation, while insufficient interdiffusion of polymer chains results in suboptimal mechanical properties.
Existing approaches to address these challenges include:
Method
Description
Drawbacks
Elevating tool temperature
Enables isothermal crystallization within processing window
Less feasible for large parts
Post-consolidation (autoclave, thermoforming)
Provides time for interdiffusion and consolidation
Additional processing time and energy
Repass treatment
Multiple localized heatings promote interlaminar bonding
Significantly reduces laydown efficiency
While these techniques can improve part quality, they either increase complexity or reduce the manufacturing efficiency that makes LAFP so attractive in the first place. Therefore, there remains a strong need for an LAFP manufacturing strategy that can simultaneously optimize both part quality and production efficiency for high-performance thermoplastic composites like CF/PEEK.
The extremely short time available for interlaminar bonding during laser-assisted automated fiber placement (LAFP) often leads to poor consolidation quality in the resulting CF/PEEK composite parts. Key problems include:
These poor interlaminar properties severely restrict the use of LAFP-manufactured thermoplastic composites in demanding aerospace applications. Current methods to improve part quality, such as elevating tool temperature, offline autoclave/ thermoforming post-consolidation, or laser repass treatments, all introduce additional cost and complexity while reducing the baseline speed and efficiency of the LAFP process.
The need to interrupt tape laying for multiple localized repass heating steps is especially detrimental to LAFP laydown rates. For example, applying a typical repass treatment to a 30-ply CF/PEEK laminate can double the required manufacturing time compared to single-pass LAFP. Therefore, the CF/PEEK composites industry requires an LAFP processing innovation that enhances interlaminar properties to aerospace-grade levels without compromising on laydown efficiency.
To address the challenges of poor interlaminar properties and reduced laydown efficiency in LAFP-manufactured CF/PEEK composites, the authors investigated an in-situ infrared annealing (IIA) approach. The key aspects of the IIA process are:
The researchers systematically compared the effects of IIA processing to untreated and laser repass treated LAFP samples:
Key findings demonstrate that IIA can provide heating power up to 700 W, sufficient to:
IIA Power
Effect
300-500 W
Exceed T_melt in first ply
500-600 W
Exceed T_melt in top 2 plies
700 W
Partially melt 3rd ply, fully melt and slowly cool top 2 plies
This localized remelting and slow cooling enables void reduction, polymer healing, and stress relief through IIA. The slow cooling rates (30-70% lower than repass) also promote high crystallinity.
Unlike repass treatments that require multiple heating steps, IIA achieves high crystallinity (up to 33.8%) within a single tape laying pass. This makes IIA a promising method to obtain aerospace-grade interlaminar properties in LAFP-manufactured CF/PEEK composites without sacrificing laydown efficiency.
The in-situ infrared annealing (IIA) method proved highly effective at enhancing the quality of LAFP-manufactured CF/PEEK composites while maintaining high laydown rates. Compared to untreated LAFP samples, laminates produced with 700 W IIA showed:
These mechanical properties are comparable to those achieved by laser repass treatment (ILSS = 72.3 MPa, GIC = 751.2 J/m2) while maintaining the full laydown speed of single-pass LAFP. The IIA method also provides more consistent crystallinities through the laminate thickness and reduces warpage by 78.6% compared to untreated LAFP.
Key advantages of in-situ infrared annealing over other LAFP enhancement techniques include:
Technique
Drawbacks
IIA Advantages
Repass
Multiple heating steps reduce laydown rate
Single-pass processing maintains efficiency
Autoclave
Extremely low efficiency, additional costs
In-situ integration, no extra equipment
Thermoforming
Long cycle times, only for simple geometries
Adaptable to complex shapes, fast layup
By achieving aerospace-grade mechanical properties in a single efficient laydown pass, in-situ infrared annealing provides an attractive new solution for high quality, cost-effective LAFP manufacturing of thermoplastic composites. This breakthrough could help expand the use of materials like CF/PEEK in demanding lightweight structures across the aerospace, automotive, and renewable energy industries.
I would like to express my gratitude to the authors of the research paper "In-situ infrared annealing for laser-assisted automated fiber placement to enhance interlaminar properties without sacrificing laydown efficiency" - Xukang Wang, Cheng Chen, Shirui Hu, Zhikun Chen, Wei Jiang, Guancheng Shen, Zhigao Huang, and Huamin Zhou from the State Key Laboratory of Materials Processing and Die & Mould Technology, School of Materials Science and Engineering, Huazhong University of Science and Technology.Xukang Wang, Cheng Chen, Shirui Hu, Zhikun Chen, Wei Jiang, Guancheng Shen, Zhigao Huang, and Huamin Zhou's innovative research on the in-situ infrared annealing (IIA) method for enhancing the interlaminar properties and manufacturing efficiency of laser-assisted automated fiber placement (LAFP) of CF/PEEK composites provided the foundation and inspiration for this article. The novel approach and thorough experimental work presented in their paper were instrumental in developing the content and key takeaways shared here.
I appreciate Xukang Wang, Cheng Chen, Shirui Hu, Zhikun Chen, Wei Jiang, Guancheng Shen, Zhigao Huang, and Huamin Zhou's dedication to advancing composite manufacturing techniques and their clear, detailed presentation of the challenges, methods, and results. Their work has made a significant contribution to the field and opens up exciting new possibilities for high-performance thermoplastic composite fabrication.
Robotics Power displayed through Tesla Optimus Robot
Discover the future of composite manufacturing with Addcomposites! Here's how you can get involved:
At Addcomposites, we are dedicated to revolutionizing composite manufacturing. Our AFP systems and comprehensive support services are waiting for you to harness. So, don't wait – get started on your journey to the future of manufacturing today!