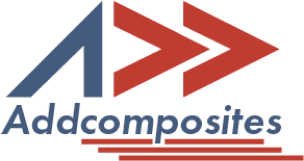
Automated fiber placement (AFP) machines are composite manufacturing technologies meant to increase rate and precision in the production of advanced composite parts. AFP combines industrial innovations, from new materials science, advanced manufacturing, and automation to advanced software platforms and robotics to redefine composites manufacturing for the future.
The complex nature of the process requires all of the above and more, creating a barrier for an average manufacturer to access advanced AFP systems.
The recent development in AFP systems enables the utilization of existing infrastructures and is supported by an innovative business model, that simplifies the above challenges. The new AFP system requires:
With the compact and adaptive new AFP solution you certainly save time and millions of euros, in addition, these AFP solutions are:
Start with a virtual planning software (AddPath) that can help you visualize your own production environment with AFP and simulate the production process, all in a couple easy steps:
Automated fiber placement (AFP) machines are composite manufacturing technologies meant to increase rate and precision in the production of advanced composite parts. AFP combines industrial innovations, from new materials science, advanced manufacturing, and automation to advanced software platforms and robotics to redefine composites manufacturing for the future.
The complex nature of the process requires all of the above and more, creating a barrier for an average manufacturer to access advanced AFP systems.
The recent development in AFP systems enables the utilization of existing infrastructures and is supported by an innovative business model, that simplifies the above challenges. The new AFP system requires:
With the compact and adaptive new AFP solution you certainly save time and millions of euros, in addition, these AFP solutions are:
Start with a virtual planning software (AddPath) that can help you visualize your own production environment with AFP and simulate the production process, all in a couple easy steps: