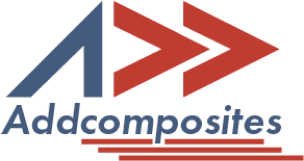
In today's aerospace industry, the pursuit of optimal performance drives a constant push toward lighter, stronger, and more efficient structures. This challenge has led to the widespread adoption of composite materials, particularly continuous fiber reinforced plastics and dry fiber systems with RTM infusion. However, manufacturing these advanced materials consistently and efficiently at scale presents its own set of challenges. This is where Automated Fiber Placement (AFP) technology has emerged as a game-changing solution.
AFP represents a significant leap forward from traditional hand layup processes, offering precision, repeatability, and efficiency that manual processes simply cannot match. For aerospace manufacturers, this technology opens new possibilities in part design and optimization while ensuring the high quality standards that the industry demands.
However, implementing AFP successfully requires careful planning, understanding of the technology's capabilities, and systematic approach to implementation. Whether you're a manufacturer currently relying on manual processes and considering automation, or an industry professional looking to optimize existing AFP operations, this guide will walk you through the essential steps and considerations for successful AFP implementation in aerospace applications.
We'll explore this topic through the lens of practical experience, focusing on real-world applications and challenges. From identifying suitable parts for AFP manufacturing to scaling up for production, each section provides actionable insights drawn from years of industry experience. The goal is to demystify AFP technology and provide a clear roadmap for its successful implementation in aerospace manufacturing.
The first and most crucial step in implementing AFP technology is identifying which parts are well-suited for automated manufacturing. Not all composite components are ideal candidates for AFP, and understanding these distinctions early can save significant time and resources in the development process.4
The most suitable candidates for AFP manufacturing typically share several important characteristics:5
When evaluating a part for AFP compatibility, consider not only its geometric characteristics but also its production volume, quality requirements, and potential for optimization. Parts that might seem suitable at first glance may present challenges in terms of tool access or process control, while others that appear complex might actually be ideal candidates when considered in terms of the overall manufacturing process.
Remember that AFP is particularly valuable for parts where:
By carefully evaluating these factors, you can identify the components that will benefit most from AFP technology and provide the best return on investment for your manufacturing operation.
Once you've identified potential parts for AFP manufacturing, the next critical step is validating their manufacturability through simulation. This phase is essential for preventing costly mistakes and optimizing the manufacturing process before any physical production begins.7
Modern simulation tools, such as ADD Path from Add Composites, provide powerful capabilities for validating AFP manufacturing processes.8 These tools allow you to:
Based on simulation results, different manufacturing strategies can be evaluated:
While running simulations, pay particular attention to:
The simulation phase should be iterative, with each round of analysis helping to refine and optimize the manufacturing approach. Don't hesitate to explore multiple scenarios and strategies – the time invested in simulation will pay dividends in reduced production issues and optimized processes.
Remember that simulation results should be validated against your specific machine capabilities and production requirements. While simulation tools are powerful, they should be used in conjunction with practical manufacturing experience and knowledge of your specific AFP system's capabilities.
After validating technical feasibility through simulation, the next critical step is evaluating the economic viability of using AFP for your specific application. This analysis helps build a comprehensive business case and provides crucial data for project planning and resource allocation.
When presenting the business case for AFP implementation, consider:
Remember that the evaluation should be comprehensive but focused on your specific situation. While AFP generally offers significant advantages for aerospace applications, the business case must be built on your particular circumstances, including:
This detailed analysis provides the foundation for making an informed decision about AFP implementation and helps set realistic expectations for the project timeline and resource requirements.
Once the business case is approved and you're ready to begin AFP implementation, attention to practical details becomes crucial. Success in AFP operations often hinges on careful control of environmental conditions, proper tooling preparation, and robust quality control measures.
Remember that successful AFP implementation requires:
The key to success is maintaining consistent conditions and catching any issues early before they affect part quality. Regular monitoring and documentation of all process parameters helps establish a reliable production process and provides data for continuous improvement efforts.
Once basic AFP operations are established and running consistently, the focus shifts to optimizing the process for maximum efficiency while maintaining quality standards. This phase is critical for achieving the full potential of your AFP investment.
Remember that optimization is an ongoing process:
The key to successful optimization is maintaining a balance between increasing efficiency and maintaining consistent quality. Each improvement should be thoroughly tested and validated before being incorporated into standard operating procedures.
Once process optimization is achieved, the final step is scaling up to full production volumes while maintaining consistent quality and efficiency. This phase requires careful attention to both technical and operational details to ensure successful aerospace production.
Remember that successful production requires:
The transition to full production is an ongoing process of refinement and improvement, always maintaining the balance between production efficiency and aerospace quality requirements.
Successfully implementing Automated Fiber Placement in aerospace manufacturing represents a significant but rewarding challenge. The journey from initial part selection to full-scale production requires careful planning, systematic execution, and continuous attention to detail. Each step builds upon the previous ones, creating a robust foundation for advanced composite manufacturing.
The key to success lies in maintaining a balanced approach:
As aerospace manufacturing continues to evolve, AFP technology will play an increasingly crucial role in meeting the industry's demands for lightweight, high-performance structures. The systematic approach outlined in this guide provides a framework for successful implementation, but remember that each organization's journey will be unique, shaped by specific requirements, capabilities, and objectives.
The future of AFP in aerospace looks promising, with ongoing developments in:
By following these guidelines and maintaining a commitment to excellence, manufacturers can successfully navigate the challenges of AFP implementation and realize the full potential of this transformative technology in aerospace manufacturing.
The figures used in this blog post are adapted from the following scientific paper:
Flynn, R. A., et al. (2021). "Automated fiber placement: A review of history, current technologies, and future paths forward." Journal of Manufacturing Science and Engineering, 143(11), 110801. DOI: https://doi.org/10.1115/1.4051663
Additional visual references and technical content are sourced from AddComposites technical documentation and resources.