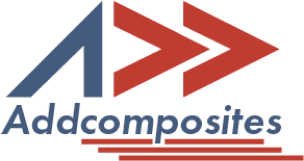
The aerospace industry is increasingly relying on CFRP for constructing modern aircraft, thanks to CFRP's advantageous properties. This trend is evident in the extensive use of CFRP in aircraft like the Boeing 787, Airbus A350, and Airbus Helicopters H145. However, the integration of CFRP poses significant challenges in design and process planning due to the complex nature of aerostructure manufacturing.
CFRP processing technologies vary widely, each with its unique limitations on part design and manufacturing. These technologies range from infusion and prepreg processes for thermoset composites, which are prevalent in aerospace, to emerging thermoplastic composite processes. The choice of technology affects automation levels, investment, and operational costs, making the selection critical to economic viability.
The development of aerostructures is further complicated by intricate interdependencies between design, material selection, and manufacturing technology. This complexity necessitates an upfront definition of materials and manufacturing processes before the final design can be determined. The traditional sequential product development approach, where manufacturing decisions are made post-design, is thus inadequate. Instead, a more integrated and iterative approach to design and manufacturing is essential, highlighting the need for automation and optimization in the planning stages.
This paper proposes a model-driven approach to address these challenges, utilizing a graph-based design language for integrated design and process planning. This approach aims to automate the generation of process models, optimize manufacturing sequences, and ultimately reduce production lead times for complex fiber composite structures, offering a significant step forward in the integrated product development and design optimization of fiber composite aerostructures.
The manufacturing of aerostructures, especially when involving CFRP, presents a plethora of challenges that significantly impact the design and planning processes. The core issues stem from the manual, labor-intensive efforts required to navigate these complexities, underscoring an urgent need for more streamlined operations.
The development and manufacturing of aerostructures, particularly when involving complex materials like CFRP, necessitate a paradigm shift towards more integrated and efficient processes. Addressing this need, a novel model-driven approach has been formulated, leveraging graph-based design languages and model transformations to seamlessly integrate design and process planning.
The approach is implemented using the Design Cockpit tool suite, which supports the creation and manipulation of graph-based models. This environment facilitates the application of the model-driven paradigm, from the definition of class models and object models to the execution of model transformations.
The model-driven approach to aerostructure manufacturing automation represents a leap forward in the design and production of complex structures, particularly those involving CFRP. Through the utilization of graph-based design languages and model transformations, this method offers significant advancements in efficiency, optimization, and error reduction. A case study involving the design and planning of an aerostructure showcases the tangible benefits of this approach.
The methodology was implemented using the Design Cockpit tool suite, supporting the creation and manipulation of graph-based models. This integrated development environment allowed for the application of model-driven paradigms, from class and object modeling to the execution of model transformations and optimizations.
The culmination of the research into a model-driven approach for the design and process planning of fiber composite aerostructures marks a significant step forward in aerospace manufacturing. By integrating design and process planning into a cohesive, graph-based design language workflow, the approach not only streamlines production but also paves the way for the incorporation of new manufacturing technologies and optimization techniques. This integration is instrumental in generating tasks, zones, and resources of the process plan, enhancing the efficiency and flexibility of manufacturing operations.
A big thank you to the authors Maximilian Holland, Nathalie Paul, Christian Linder, Hossam Elsafty, Gunar Ernis, and Steffen Geinitz for their significant contributions to the blog "MODEL-DRIVEN APPROACH FOR INTEGRATED DESIGN AND PROCESS PLANNING OF FIBER COMPOSITE AEROSTRUCTURES." Their work is paving the way for groundbreaking advancements in aerospace manufacturing, specifically in the efficient design and production of fiber composite aerostructures. Their affiliations with the prestigious Fraunhofer Institute and the University of Bonn highlight the depth of research and expertise involved in developing this innovative approach. Your dedication and effort in pushing the boundaries of aerospace engineering are truly appreciated. Thank you for your invaluable contributions to the field!
Discover the future of composite manufacturing with Addcomposites! Here's how you can get involved:
At Addcomposites, we are dedicated to revolutionizing composite manufacturing. Our AFP systems and comprehensive support services are waiting for you to harness. So, don't wait – get started on your journey to the future of manufacturing today!
The aerospace industry is increasingly relying on CFRP for constructing modern aircraft, thanks to CFRP's advantageous properties. This trend is evident in the extensive use of CFRP in aircraft like the Boeing 787, Airbus A350, and Airbus Helicopters H145. However, the integration of CFRP poses significant challenges in design and process planning due to the complex nature of aerostructure manufacturing.
CFRP processing technologies vary widely, each with its unique limitations on part design and manufacturing. These technologies range from infusion and prepreg processes for thermoset composites, which are prevalent in aerospace, to emerging thermoplastic composite processes. The choice of technology affects automation levels, investment, and operational costs, making the selection critical to economic viability.
The development of aerostructures is further complicated by intricate interdependencies between design, material selection, and manufacturing technology. This complexity necessitates an upfront definition of materials and manufacturing processes before the final design can be determined. The traditional sequential product development approach, where manufacturing decisions are made post-design, is thus inadequate. Instead, a more integrated and iterative approach to design and manufacturing is essential, highlighting the need for automation and optimization in the planning stages.
This paper proposes a model-driven approach to address these challenges, utilizing a graph-based design language for integrated design and process planning. This approach aims to automate the generation of process models, optimize manufacturing sequences, and ultimately reduce production lead times for complex fiber composite structures, offering a significant step forward in the integrated product development and design optimization of fiber composite aerostructures.
The manufacturing of aerostructures, especially when involving CFRP, presents a plethora of challenges that significantly impact the design and planning processes. The core issues stem from the manual, labor-intensive efforts required to navigate these complexities, underscoring an urgent need for more streamlined operations.
The development and manufacturing of aerostructures, particularly when involving complex materials like CFRP, necessitate a paradigm shift towards more integrated and efficient processes. Addressing this need, a novel model-driven approach has been formulated, leveraging graph-based design languages and model transformations to seamlessly integrate design and process planning.
The approach is implemented using the Design Cockpit tool suite, which supports the creation and manipulation of graph-based models. This environment facilitates the application of the model-driven paradigm, from the definition of class models and object models to the execution of model transformations.
The model-driven approach to aerostructure manufacturing automation represents a leap forward in the design and production of complex structures, particularly those involving CFRP. Through the utilization of graph-based design languages and model transformations, this method offers significant advancements in efficiency, optimization, and error reduction. A case study involving the design and planning of an aerostructure showcases the tangible benefits of this approach.
The methodology was implemented using the Design Cockpit tool suite, supporting the creation and manipulation of graph-based models. This integrated development environment allowed for the application of model-driven paradigms, from class and object modeling to the execution of model transformations and optimizations.
The culmination of the research into a model-driven approach for the design and process planning of fiber composite aerostructures marks a significant step forward in aerospace manufacturing. By integrating design and process planning into a cohesive, graph-based design language workflow, the approach not only streamlines production but also paves the way for the incorporation of new manufacturing technologies and optimization techniques. This integration is instrumental in generating tasks, zones, and resources of the process plan, enhancing the efficiency and flexibility of manufacturing operations.
A big thank you to the authors Maximilian Holland, Nathalie Paul, Christian Linder, Hossam Elsafty, Gunar Ernis, and Steffen Geinitz for their significant contributions to the blog "MODEL-DRIVEN APPROACH FOR INTEGRATED DESIGN AND PROCESS PLANNING OF FIBER COMPOSITE AEROSTRUCTURES." Their work is paving the way for groundbreaking advancements in aerospace manufacturing, specifically in the efficient design and production of fiber composite aerostructures. Their affiliations with the prestigious Fraunhofer Institute and the University of Bonn highlight the depth of research and expertise involved in developing this innovative approach. Your dedication and effort in pushing the boundaries of aerospace engineering are truly appreciated. Thank you for your invaluable contributions to the field!
Discover the future of composite manufacturing with Addcomposites! Here's how you can get involved:
At Addcomposites, we are dedicated to revolutionizing composite manufacturing. Our AFP systems and comprehensive support services are waiting for you to harness. So, don't wait – get started on your journey to the future of manufacturing today!