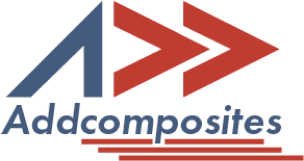
In the rapidly evolving landscape of electric vehicles, Tesla has consistently pushed the boundaries of innovation. Their latest breakthrough in motor technology – the "carbon-wrapped" motor – promises to redefine the standards of efficiency and performance in the automotive industry. This groundbreaking concept leverages advanced materials and cutting-edge manufacturing processes to create electric motors that are more powerful, compact, and efficient than ever before.
The carbon-wrapped motor concept involves encasing the rotor of a permanent magnet motor (PMM) with a precisely engineered carbon fiber sleeve. This seemingly simple addition has profound implications for motor performance. By providing superior containment of the rotor assembly, the carbon fiber wrapping allows the motor to operate at significantly higher rotational speeds. This translates directly into increased power density, meaning more power can be generated from a smaller, lighter motor – a critical advantage in the weight-sensitive world of electric vehicles.
But the true revolution lies not just in the concept, but in its execution. This is where Addcomposites enters the picture. Our state-of-the-art Automated Fiber Placement (AFP) technology, specifically our AFP-XS solution, is poised to play a crucial role in bringing Tesla's vision to life. By enabling the precise, repeatable, and cost-effective application of carbon fiber reinforcements, our technology bridges the gap between cutting-edge design and practical manufacturing.
In this blog post, we'll delve into the details of Tesla's carbon-wrapped motor concept, explore the transformative potential of AFP technology in motor manufacturing, and showcase how Addcomposites is at the forefront of this automotive revolution. Join us as we unpack the technology that could very well be the key to the next generation of electric vehicles.
At the heart of Tesla's innovative design is the carbon fiber sleeve that encases the rotor of their permanent magnet motors (PMMs). To understand its significance, let's first look at the basic structure of a PMM:
The carbon fiber sleeve is a thin, incredibly strong layer that wraps around the rotor. Its primary function is to contain the rotor assembly, particularly the permanent magnets, under the extreme centrifugal forces experienced during high-speed rotation.
The introduction of the carbon fiber sleeve brings several significant advantages:
To truly appreciate the innovation of Tesla's carbon-wrapped motor, let's compare it to traditional electric motor designs:
Tesla's carbon-wrapped motor represents a significant leap forward in electric motor design. By leveraging the unique properties of carbon fiber and advanced manufacturing techniques, Tesla has created a motor that pushes the boundaries of efficiency, power density, and performance. This innovation sets a new benchmark in the industry and opens up exciting possibilities for the future of electric vehicles.
Automated Fiber Placement (AFP) is a cutting-edge manufacturing process that has revolutionized the production of complex composite structures. This technology allows for the precise and automated laying of continuous fiber reinforcements, typically carbon fiber, onto a surface or mold.
The AFP process involves:
For a more comprehensive overview of AFP technology, check out our detailed guide: What is Automated Fibre Placement (AFP)?
When it comes to manufacturing the carbon fiber sleeves for Tesla's innovative motor design, AFP offers several significant advantages:
By leveraging AFP technology, manufacturers can produce carbon fiber sleeves that meet the exacting standards required for high-performance electric motors. The precision, consistency, and efficiency of AFP make it an ideal match for the demands of next-generation motor production.
As we continue to push the boundaries of electric motor performance, the role of advanced manufacturing technologies like AFP becomes increasingly crucial. At Addcomposites, we're proud to be at the forefront of this technological revolution, providing the tools and expertise needed to bring innovations like Tesla's carbon-wrapped motor to life.
At Addcomposites, we're proud to introduce our cutting-edge AFP-XS solution, a game-changing technology that's poised to revolutionize the manufacturing of carbon-wrapped motors. The AFP-XS is not just another Automated Fiber Placement system; it's a compact, versatile, and highly efficient solution designed to meet the exacting demands of next-generation motor production.
Our AFP-XS system stands out in the industry for its ability to deliver high-precision fiber placement in a package that's accessible to a wide range of manufacturers. Whether you're a major automotive OEM or an innovative start-up, the AFP-XS provides the capabilities you need to push the boundaries of electric motor design.
Let's dive into the features that make the AFP-XS the ideal solution for manufacturing carbon-wrapped motors:
With these advanced features, the AFP-XS is uniquely positioned to enable the production of revolutionary motor designs like Tesla's carbon-wrapped motor. Here's how:
By combining these features, the AFP-XS provides manufacturers with the tools they need to bring cutting-edge motor designs from concept to reality. It's not just about making better motors; it's about enabling a new generation of electric vehicles that are more efficient, more powerful, and more sustainable.
For more detailed information about the AFP-XS and its capabilities, visit our product page: AFP-XS
With Addcomposites' AFP-XS, the future of electric motor manufacturing is here. We're excited to be at the forefront of this technological revolution, providing the tools and expertise needed to drive the automotive industry forward.
The integration of carbon-wrapped motors manufactured using advanced AFP technology like our AFP-XS system is set to have a profound impact on the automotive industry, particularly in the realm of electrification. Let's explore the key areas where this technology is poised to make a significant difference.
While the initial investment in AFP technology may seem significant, the long-term cost benefits are substantial:
The AFP technology, particularly our AFP-XS solution, is well-suited for scaling up to mass production:
The impact of carbon-wrapped motors and AFP technology on automotive electrification cannot be overstated. This innovation has the potential to accelerate the transition to electric vehicles by addressing key challenges of performance, cost, and scalability. As this technology matures and becomes more widely adopted, we can expect to see electric vehicles that are more efficient, more powerful, and more affordable than ever before.
At Addcomposites, we're proud to be at the forefront of this technological revolution, providing the tools and expertise needed to turn these possibilities into reality. The future of automotive electrification is here, and it's being shaped by advanced manufacturing technologies like our AFP-XS system.
While the potential of carbon-wrapped motors manufactured with AFP technology is immense, the path to widespread implementation is not without its challenges. At Addcomposites, we've been working closely with our partners to address these hurdles head-on. Let's explore some of the key challenges and how they can be overcome.
While these challenges are significant, they are far from insurmountable. At Addcomposites, we're committed to working with our partners to overcome these hurdles and unlock the full potential of carbon-wrapped motors. By addressing these challenges head-on, we're paving the way for a new era of electric vehicle performance and efficiency.
The journey to revolutionizing automotive electrification may be complex, but with innovative solutions like our AFP-XS system and a collaborative approach to problem-solving, we're confident that the future of electric motors is carbon-wrapped and AFP-made.
As we stand on the cusp of a revolution in electric motor technology, it's exciting to consider the future prospects and potential for industry adoption of carbon-wrapped motors manufactured with AFP technology. At Addcomposites, we're not just observers of this transformation – we're active participants, shaping the future of motor manufacturing.
While our current focus is on the automotive sector, the potential applications of carbon-wrapped motors and AFP technology extend far beyond:
At Addcomposites, we're committed to driving the future of AFP in motor manufacturing. Our vision includes:
The future of motor manufacturing is carbon-wrapped and AFP-made. At Addcomposites, we're excited to be at the forefront of this revolution, providing the tools and expertise needed to turn these exciting possibilities into reality. As we continue to innovate and collaborate with partners across industries, we're confident that the impact of this technology will be transformative, not just for the automotive sector, but for the broader landscape of electric motor applications.
As we've explored throughout this blog post, carbon-wrapped motors manufactured using Automated Fiber Placement (AFP) technology stand poised to revolutionize the automotive industry and beyond. Let's recap the key points and consider the exciting road ahead.
Carbon-wrapped motors represent a significant leap forward in electric motor technology:
At Addcomposites, we're proud to be at the forefront of this technological revolution:
The potential of carbon-wrapped motors is clear, but realizing this potential requires collective effort and innovation. We call upon:
The future of electric motors is carbon-wrapped, and the time to act is now. At Addcomposites, we're ready to partner with you to turn this exciting potential into reality. Whether you're an established automotive manufacturer, a cutting-edge startup, or anywhere in between, we invite you to join us in shaping the future of electric mobility.
Let's work together to create motors that are not just more powerful and efficient, but that contribute to a more sustainable, electrified future. The revolution in motor technology is here – and with Addcomposites' AFP-XS system, you have the tools to be at its forefront.
Contact us today to learn more about how our AFP technology can transform your motor manufacturing processes and drive your innovations forward. The future is carbon-wrapped – let's build it together.
To further your understanding of carbon-wrapped motors, AFP technology, and their applications in the automotive and other industries, we've compiled a list of valuable resources. These include academic papers, industry reports, and additional content from Addcomposites.
These resources provide a wealth of information on carbon-wrapped motors, AFP technology, and their applications in various industries. We encourage you to explore these materials to deepen your understanding of this revolutionary technology and its potential impact on the automotive industry and beyond.
For more information or to discuss how Addcomposites can support your carbon-wrapped motor manufacturing needs, please contact us.