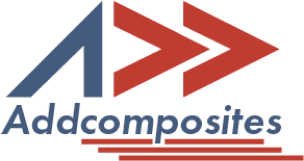
Welcome to our comprehensive guide on Automated Fiber Placement (AFP) machines, a transformative technology in the field of composite manufacturing. Whether you are new to AFP or looking to upgrade your existing system, this blog is designed to provide you with valuable insights and practical advice to help you make an informed decision. Here’s what you can expect:
Automated Fiber Placement (AFP) is a sophisticated process used in the manufacturing of composite materials, where continuous fibers are meticulously placed onto a substrate using a specialized machine. This technology has been around for decades, evolving significantly over time to enhance efficiency and quality. Today, AFP is a pivotal part of various industries, known for its ability to produce composite parts with superior mechanical properties, extended fatigue life, and enhanced fracture toughness.
The AFP machine operates by attaching an AFP head to an industrial robotic arm, programmed to place strips of composite material tapes, or tows, onto a tool surface. This process requires precision to ensure minimal defects and optimal adhesion between the tows and the substrate. The machine utilizes heating and compaction during the placement of the tows, and tow tension is meticulously managed to ensure accurate placement. The end result is a laminate, composed of multiple plies stacked together in a precise sequence.
The use of automation and robotics in AFP not only accelerates production but also ensures improved accuracy, quality, and a reduction in human error, making it an invaluable asset in composite manufacturing. Operators of AFP systems generally need a basic understanding of composites processing and CNC machine operation. The programming and operation of the machine involve several steps, including part production simulation, NC code generation, machine setup, and careful monitoring during the layup process.
AFP machines have found applications in various industries, such as aerospace for manufacturing aircraft components, automotive for composite parts, construction for materials like bridge decks and beams, and wind energy for composite wind turbine blades. The versatility and precision of AFP machines make them a valuable tool for manufacturing lightweight, complex-shaped structures optimized for load-carrying and efficiency.
By understanding these cost components, manufacturers can make more informed decisions when selecting an AFP machine, ensuring they choose a system that meets their specific needs and budget.
Automated Fiber Placement (AFP) machines, particularly those used in the aerospace industry for large, expensive parts, are typically custom-built. This customization is a significant factor in the pricing of these machines, making it a complex aspect to quantify. However, we can identify the main cost drivers and provide a general understanding of the pricing structure.
These examples illustrate the significant investment required for traditional large AFP machines, with prices ranging from $3 Million to $6 Million, depending on the size, capabilities, and additional features of the machine. It is crucial for manufacturers to carefully consider their specific needs and budget when selecting an AFP machine, as the cost implications are substantial.
The advent of modern modular Automated Fiber Placement (AFP) systems has revolutionized the composite manufacturing industry, offering a more cost-effective and flexible solution compared to traditional large AFP machines. These systems are designed to be user-friendly, versatile, and efficient, catering to the evolving needs of manufacturers.
The modular nature of these systems provides various pricing options, making them accessible for different needs and budgets.
AFP-XS stands out as a prime example of a modern modular AFP system, designed to bridge the gap between traditional AFP technology and the current needs of the industry. It is a product born out of a deep understanding of the user's pain points, aiming to make AFP technology more accessible and cost-effective.
AFP-XS is not just about affordability; it is about empowering users. With its user-centric design, it addresses safety concerns in composite manufacturing by providing multi-material capabilities. This aligns with the industry's shift towards more sustainable practices, ensuring safer material processing options.
The system's use of open-access software gives users the flexibility to build their own scripts and leverage digital twin capabilities, ensuring real-time quality control and superior system performance. Its compact and simplified design, focusing on single tow variable width options, reduces system complexity, ensuring ease of use and maintenance.
The application of heat is pivotal for proper adhesion of incoming tows to the substrate. Various heating systems are available, each with unique characteristics and applications.
The success of AFP operations hinges significantly on the software used, acting as the bridge connecting design, manufacturing, and quality control. Ensure to choose software that integrates well with the AFP system to avoid inefficiencies.
Making the right investment in an Automated Fiber Placement (AFP) system is crucial, and we understand the importance of having all the information you need to make an informed decision. To facilitate this, we offer an automated quoting system that provides you with a detailed and customized quote based on your specific requirements.
We are here to help you transition into the future of composite manufacturing with ease and confidence. Get your automated quote today and take the first step towards optimizing your production process with the right AFP system.
Get Your Automated AFP System Quote
If you have any questions or need further assistance, feel free to contact our support team. We are here to help you every step of the way.
Welcome to our comprehensive guide on Automated Fiber Placement (AFP) machines, a transformative technology in the field of composite manufacturing. Whether you are new to AFP or looking to upgrade your existing system, this blog is designed to provide you with valuable insights and practical advice to help you make an informed decision. Here’s what you can expect:
Automated Fiber Placement (AFP) is a sophisticated process used in the manufacturing of composite materials, where continuous fibers are meticulously placed onto a substrate using a specialized machine. This technology has been around for decades, evolving significantly over time to enhance efficiency and quality. Today, AFP is a pivotal part of various industries, known for its ability to produce composite parts with superior mechanical properties, extended fatigue life, and enhanced fracture toughness.
The AFP machine operates by attaching an AFP head to an industrial robotic arm, programmed to place strips of composite material tapes, or tows, onto a tool surface. This process requires precision to ensure minimal defects and optimal adhesion between the tows and the substrate. The machine utilizes heating and compaction during the placement of the tows, and tow tension is meticulously managed to ensure accurate placement. The end result is a laminate, composed of multiple plies stacked together in a precise sequence.
The use of automation and robotics in AFP not only accelerates production but also ensures improved accuracy, quality, and a reduction in human error, making it an invaluable asset in composite manufacturing. Operators of AFP systems generally need a basic understanding of composites processing and CNC machine operation. The programming and operation of the machine involve several steps, including part production simulation, NC code generation, machine setup, and careful monitoring during the layup process.
AFP machines have found applications in various industries, such as aerospace for manufacturing aircraft components, automotive for composite parts, construction for materials like bridge decks and beams, and wind energy for composite wind turbine blades. The versatility and precision of AFP machines make them a valuable tool for manufacturing lightweight, complex-shaped structures optimized for load-carrying and efficiency.
By understanding these cost components, manufacturers can make more informed decisions when selecting an AFP machine, ensuring they choose a system that meets their specific needs and budget.
Automated Fiber Placement (AFP) machines, particularly those used in the aerospace industry for large, expensive parts, are typically custom-built. This customization is a significant factor in the pricing of these machines, making it a complex aspect to quantify. However, we can identify the main cost drivers and provide a general understanding of the pricing structure.
These examples illustrate the significant investment required for traditional large AFP machines, with prices ranging from $3 Million to $6 Million, depending on the size, capabilities, and additional features of the machine. It is crucial for manufacturers to carefully consider their specific needs and budget when selecting an AFP machine, as the cost implications are substantial.
The advent of modern modular Automated Fiber Placement (AFP) systems has revolutionized the composite manufacturing industry, offering a more cost-effective and flexible solution compared to traditional large AFP machines. These systems are designed to be user-friendly, versatile, and efficient, catering to the evolving needs of manufacturers.
The modular nature of these systems provides various pricing options, making them accessible for different needs and budgets.
AFP-XS stands out as a prime example of a modern modular AFP system, designed to bridge the gap between traditional AFP technology and the current needs of the industry. It is a product born out of a deep understanding of the user's pain points, aiming to make AFP technology more accessible and cost-effective.
AFP-XS is not just about affordability; it is about empowering users. With its user-centric design, it addresses safety concerns in composite manufacturing by providing multi-material capabilities. This aligns with the industry's shift towards more sustainable practices, ensuring safer material processing options.
The system's use of open-access software gives users the flexibility to build their own scripts and leverage digital twin capabilities, ensuring real-time quality control and superior system performance. Its compact and simplified design, focusing on single tow variable width options, reduces system complexity, ensuring ease of use and maintenance.
The application of heat is pivotal for proper adhesion of incoming tows to the substrate. Various heating systems are available, each with unique characteristics and applications.
The success of AFP operations hinges significantly on the software used, acting as the bridge connecting design, manufacturing, and quality control. Ensure to choose software that integrates well with the AFP system to avoid inefficiencies.
Making the right investment in an Automated Fiber Placement (AFP) system is crucial, and we understand the importance of having all the information you need to make an informed decision. To facilitate this, we offer an automated quoting system that provides you with a detailed and customized quote based on your specific requirements.
We are here to help you transition into the future of composite manufacturing with ease and confidence. Get your automated quote today and take the first step towards optimizing your production process with the right AFP system.
Get Your Automated AFP System Quote
If you have any questions or need further assistance, feel free to contact our support team. We are here to help you every step of the way.