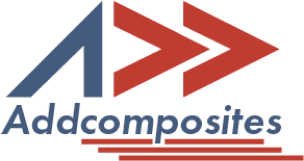
Composite materials, especially those reinforced with carbon or glass fibers, are widely used in aerospace and other high-performance applications due to their high strength-to-weight ratio and the ability to tailor their properties according to specific load requirements. However, optimizing the fiber placement in these materials is a complex problem. Traditional methods often fall short in balancing performance enhancement with manufacturability constraints.
The main challenge in optimizing fiber placement lies in the need to control the fiber curvature accurately. High curvature can lead to defects such as fiber wrinkling, tow overlaps, and gaps, which compromise the structural integrity of the composite. Therefore, a method that can optimize fiber paths while adhering to manufacturability constraints is essential.
To address this, a new numerical optimization method has been developed: the Iso-Contour Method. This method leverages an artificial surface defined by a small number of control points to manage fiber orientation smoothly across the composite structure. By doing so, it ensures that constraints like maximum fiber curvature (MFCC) and average fiber curvature (AFCC) are explicitly respected.
The Iso-Contour Method has been validated through several test cases, including simple plates under static loads and more complex structures like wingbox ribs. These validations have demonstrated that the method can produce optimal fiber orientations that significantly enhance structural performance while remaining within manufacturable limits.
One of the most pressing challenges in the optimization of fiber-steered composite materials is managing fiber curvature to ensure manufacturability. Composite materials, while highly customizable in terms of their mechanical properties, pose significant challenges during the manufacturing process, especially when automated fiber placement (AFP) techniques are used.
Key Challenges:
The Iso-Contour Method addresses these challenges by providing a novel approach to fiber path optimization that explicitly integrates curvature constraints into the optimization process. This method ensures that the resulting fiber paths are not only optimal in terms of performance but also manufacturable, thereby mitigating the common defects associated with high fiber curvature.
The Iso-Contour Method is a novel optimization technique designed to enhance the performance and manufacturability of fiber-steered composite materials. This method addresses the complex challenge of managing fiber curvature constraints while optimizing the fiber paths for improved structural performance.
Key Features of the Iso-Contour Method:
Advantages:
The Iso-Contour Method provides a robust solution for optimizing fiber-steered composite structures, significantly enhancing their structural performance while ensuring manufacturability. Here’s how this advanced optimization technique works and the solutions it offers:
1. Parametric Surface Control:
2. Integrated Curvature Constraints:
3. Two-Stage Optimization Approach:
4. Validation and Practical Applications:
5. Results and Performance Improvements:
We would like to extend our heartfelt thanks to the authors, Anna Arsenyeva, Fabian Duddeck, and Harvey M. Thompson, for their invaluable contributions to this blog. Their groundbreaking work, as detailed in the paper "An Iso-Contour Method for Automated Fiber Placement Optimization of Composite Structures," has provided a wealth of knowledge and insights. This blog post would not have been possible without their innovative research and dedication to advancing the field of composite materials. Thank you for your commitment to excellence and for sharing your expertise with the broader engineering and research community.
Discover the future of composite manufacturing with Addcomposites! Here's how you can get involved:
At Addcomposites, we are dedicated to revolutionizing composite manufacturing. Our AFP systems and comprehensive support services are waiting for you to harness. So, don't wait – get started on your journey to the future of manufacturing today!
Composite materials, especially those reinforced with carbon or glass fibers, are widely used in aerospace and other high-performance applications due to their high strength-to-weight ratio and the ability to tailor their properties according to specific load requirements. However, optimizing the fiber placement in these materials is a complex problem. Traditional methods often fall short in balancing performance enhancement with manufacturability constraints.
The main challenge in optimizing fiber placement lies in the need to control the fiber curvature accurately. High curvature can lead to defects such as fiber wrinkling, tow overlaps, and gaps, which compromise the structural integrity of the composite. Therefore, a method that can optimize fiber paths while adhering to manufacturability constraints is essential.
To address this, a new numerical optimization method has been developed: the Iso-Contour Method. This method leverages an artificial surface defined by a small number of control points to manage fiber orientation smoothly across the composite structure. By doing so, it ensures that constraints like maximum fiber curvature (MFCC) and average fiber curvature (AFCC) are explicitly respected.
The Iso-Contour Method has been validated through several test cases, including simple plates under static loads and more complex structures like wingbox ribs. These validations have demonstrated that the method can produce optimal fiber orientations that significantly enhance structural performance while remaining within manufacturable limits.
One of the most pressing challenges in the optimization of fiber-steered composite materials is managing fiber curvature to ensure manufacturability. Composite materials, while highly customizable in terms of their mechanical properties, pose significant challenges during the manufacturing process, especially when automated fiber placement (AFP) techniques are used.
Key Challenges:
The Iso-Contour Method addresses these challenges by providing a novel approach to fiber path optimization that explicitly integrates curvature constraints into the optimization process. This method ensures that the resulting fiber paths are not only optimal in terms of performance but also manufacturable, thereby mitigating the common defects associated with high fiber curvature.
The Iso-Contour Method is a novel optimization technique designed to enhance the performance and manufacturability of fiber-steered composite materials. This method addresses the complex challenge of managing fiber curvature constraints while optimizing the fiber paths for improved structural performance.
Key Features of the Iso-Contour Method:
Advantages:
The Iso-Contour Method provides a robust solution for optimizing fiber-steered composite structures, significantly enhancing their structural performance while ensuring manufacturability. Here’s how this advanced optimization technique works and the solutions it offers:
1. Parametric Surface Control:
2. Integrated Curvature Constraints:
3. Two-Stage Optimization Approach:
4. Validation and Practical Applications:
5. Results and Performance Improvements:
We would like to extend our heartfelt thanks to the authors, Anna Arsenyeva, Fabian Duddeck, and Harvey M. Thompson, for their invaluable contributions to this blog. Their groundbreaking work, as detailed in the paper "An Iso-Contour Method for Automated Fiber Placement Optimization of Composite Structures," has provided a wealth of knowledge and insights. This blog post would not have been possible without their innovative research and dedication to advancing the field of composite materials. Thank you for your commitment to excellence and for sharing your expertise with the broader engineering and research community.
Discover the future of composite manufacturing with Addcomposites! Here's how you can get involved:
At Addcomposites, we are dedicated to revolutionizing composite manufacturing. Our AFP systems and comprehensive support services are waiting for you to harness. So, don't wait – get started on your journey to the future of manufacturing today!