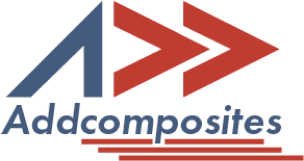
The demand for high-performance composite materials, prized for their exceptional strength-to-weight ratios, is soaring across industries like aerospace, automotive, and energy.1 These materials enable lighter, more fuel-efficient vehicles and aircraft, and larger, more efficient wind turbine blades. However, this progress comes with a significant challenge: the environmental impact of manufacturing and disposing of these advanced materials.2 Traditional thermoset composites, such as the widely used epoxy systems, form permanent, chemically cross-linked networks during curing.5 While this provides excellent mechanical properties and thermal stability, it renders them inherently difficult, if not impossible, to recycle, repair effectively, or reshape once cured.5 This leads to a growing stream of manufacturing scrap and end-of-life waste, often destined for landfills.3 Furthermore, the conventional manufacturing process for high-performance thermoset composites typically involves energy-intensive autoclave curing cycles, adding to their environmental footprint.11 The core tension between achieving high performance and meeting escalating sustainability demands, including circular economy principles, necessitates a paradigm shift in composite manufacturing.5
This is where Automated Fiber Placement (AFP) technology emerges not just as a method for improving manufacturing efficiency and precision, but as a pivotal enabler for a more sustainable future for composites. AFP, an advanced additive manufacturing process, offers a pathway to address the limitations of traditional methods.17 Its inherent precision minimizes material waste during production. Crucially, it is highly compatible with newer generations of composite materials, particularly thermoplastics and emerging vitrimers, which boast significantly enhanced recyclability and repairability.5 Furthermore, AFP facilitates out-of-autoclave (OoA) processing techniques like in-situ consolidation (ISC), drastically reducing the energy consumption associated with manufacturing.19 Finally, the design freedom offered by AFP allows engineers to create highly optimized, lightweight structures, reducing energy consumption throughout the product's operational life.20 The sustainability challenge is multifaceted, encompassing material end-of-life, process efficiency (waste and energy), and use-phase impact; AFP presents a unique opportunity to tackle these interconnected issues simultaneously.
At Addcomposites, we believe in democratizing access to advanced manufacturing technologies like AFP. Our mission is to empower innovators, researchers, and manufacturers of all sizes to harness the full potential of composites, driving progress towards both high performance and environmental responsibility.21 This article delves into how AFP technology fundamentally enables the production of recyclable and sustainable composite structures. We will explore the principles of AFP, examine the compatible recyclable materials it unlocks, quantify its benefits in waste reduction and energy efficiency, and discuss its role in creating lightweight designs for a greener lifecycle. We will also highlight how Addcomposites' tools, particularly our AddPath software, facilitate this transition towards a more sustainable composite manufacturing ecosystem.
Automated Fiber Placement (AFP) is an advanced additive manufacturing process where robotic systems precisely place continuous fiber-reinforced tapes or narrow strips, known as 'tows', onto a mold or mandrel surface to build up a composite part layer by layer (ply-by-ply).24 It operates on three fundamental inputs: the fiber/polymer tape material, a controlled heat source, and precisely applied pressure.24
The core operational principle involves several coordinated steps. Material, typically pre-impregnated fiber tows (e.g., carbon fiber with epoxy or thermoplastic resin), is fed from spools, often housed in a creel system.25 Depending on the material, the path to the deposition head might require specific handling – thermoset prepregs often benefit from cooled passages to maintain tack and prevent premature curing, while thermoplastic tapes necessitate significant heating capabilities at the deposition point.24 As the tow reaches the AFP head, a heat source – commonly infrared lamps or lasers – elevates the temperature of the incoming material and/or the underlying substrate.12 For thermosets, this heat activates the resin's tackiness, allowing the ply to adhere to the previous layer or tool surface.25 For thermoplastics, the temperature is raised above the polymer's melt or softening point to enable fusion bonding.30 Immediately following heating, a compaction roller integrated into the AFP head applies pressure, consolidating the material, ensuring intimate contact between layers, minimizing porosity (voids), and promoting strong interlaminar bonding.24
This entire deposition process is orchestrated by a robotic motion platform, which can be a large gantry system or a more flexible articulated robotic arm.25 The robot meticulously follows pre-programmed paths derived from a digital model of the part, controlling the placement, orientation, and speed of deposition.28 Key process parameters such as deposition speed, heating temperature, compaction force, and tow tension are tightly monitored and controlled by the system's automation controls, ensuring high levels of accuracy, repeatability, and quality control unattainable with manual methods.24 This precise control over material placement, heat, and pressure at the point of deposition forms the foundation of AFP's capabilities.
A typical AFP system comprises several key components 24:
Compared to traditional manual layup, AFP offers dramatic improvements in speed, consistency, and reduced labor intensity, although the initial investment is higher.17 It also differs from Automated Tape Laying (ATL), another automated technique. While ATL typically uses wider tapes (e.g., 75-300 mm) and excels at rapidly covering large, relatively flat or gently curved surfaces, AFP employs multiple narrow tows (often 3.2 mm to 12.7 mm wide).25 This use of narrow, individually controllable tows is a defining characteristic of AFP. It provides superior flexibility for laying material onto complex, highly curved geometries, allows for precise fiber steering along optimized paths, and enables much finer control over ply boundaries, leading to significantly less material scrap compared to cutting shapes from wider tapes or fabric sheets.17 This capability is fundamental to AFP's advantages in both design optimization and material efficiency. Furthermore, the tight integration of sophisticated planning and simulation software with the physical AFP system creates a powerful cyber-physical manufacturing environment. This allows for extensive virtual optimization, minimizing physical trial-and-error, reducing waste and energy consumption upfront, and paving the way for data-driven quality control and process improvement – key tenets of modern, sustainable manufacturing.24
A primary obstacle to sustainability in the composites industry has been the materials themselves. Traditional thermosetting polymers, like the epoxy resins prevalent in aerospace applications 41, undergo an irreversible chemical reaction during curing. This creates strong, permanent cross-links between polymer chains, resulting in excellent mechanical properties but rendering the material infusible and insoluble.5 Consequently, recycling or reprocessing thermoset composites is extremely challenging, often limited to energy recovery through incineration or downcycling the recovered fibers after matrix removal via harsh chemical (solvolysis) or thermal (pyrolysis) processes.4 This contributes significantly to the growing challenge of composite waste management.3 AFP technology, however, is adept at processing alternative materials that offer a path towards a more circular economy for composites.
Thermoplastic composites represent a major step towards recyclability. Unlike thermosets, thermoplastic polymers (such as PEEK, PEKK, PAEK, and others 4) consist of long, linear polymer chains with weaker intermolecular forces.5 This fundamental difference means they soften and melt when heated above their glass transition or melting temperature and solidify upon cooling – a process that can be repeated multiple times without degrading the polymer structure.5
This inherent melt-processability is the key to their recyclability. Manufacturing scrap and end-of-life thermoplastic composite parts can be collected, often shredded, and then re-melted and reformed into new components, potentially through processes like compression molding.5 This capability enables closed-loop material systems and aligns perfectly with circular economy principles, reducing reliance on virgin materials and minimizing landfill waste.14
Beyond end-of-life recycling, the ability to re-melt thermoplastics opens doors for efficient repair and assembly methods. Damage can potentially be repaired by locally heating and reforming the material.5 Furthermore, thermoplastic composite parts can be joined together using various welding techniques (e.g., induction, resistance, ultrasonic welding), eliminating the need for heavy, stress-concentrating fasteners or adhesives.4 This not only simplifies assembly and reduces part count but also contributes to further weight savings – a critical factor in transportation applications. These mid-life advantages in repairability and assembly efficiency significantly enhance the overall sustainability profile of thermoplastic composites.
AFP technology is particularly well-suited for processing thermoplastic tapes. While it requires modifications compared to thermoset AFP – notably, the integration of high-power heating systems (like lasers or enhanced infrared emitters) capable of rapidly reaching the high melt temperatures of engineering thermoplastics (often 300-400°C) 5 – the precise, localized application of heat and pressure by the AFP head is ideal. This capability enables the potential for in-situ consolidation (ISC), where each ply is fully melted, bonded, and consolidated as it is laid down, potentially eliminating the need for any subsequent oven or autoclave cycles.5 Addcomposites' AFP systems, for instance, can be equipped with accessories like water-cooled compaction rollers designed specifically for high-temperature thermoplastic operations.35 Other advantages of thermoplastics include their virtually unlimited shelf life at room temperature (eliminating the need for costly refrigerated storage and waste from expired materials) and often superior impact resistance and damage tolerance compared to thermosets.4
A newer, exciting class of polymers called vitrimers is emerging as a potential 'best-of-both-worlds' solution.6 Vitrimers are unique because they possess covalent adaptable networks (CANs). At typical operating temperatures, they behave much like traditional thermosets, exhibiting high strength, stiffness, and chemical resistance due to their cross-linked structure.6 However, these cross-links are dynamic and reversible. When subjected to a stimulus, usually heat above a specific 'vitrimer transition temperature' (Tv), the bonds can break and reform through associative exchange reactions (like transesterification) without reducing the overall cross-link density.6
This dynamic bond exchange mechanism endows vitrimers with remarkable properties typically associated with thermoplastics: they can be reprocessed, reshaped, welded, repaired, and even exhibit self-healing capabilities, where microcracks can autonomously mend under the right conditions.6 This opens up possibilities for recycling manufacturing scrap and end-of-life components, potentially through thermal reprocessing or solvent-based methods that can recover both the matrix and the reinforcement fibers.6 Many vitrimer systems are based on modified epoxy chemistries, potentially allowing manufacturers to leverage existing knowledge and infrastructure associated with thermosets.7
Vitrimers represent a potential disruption, aiming to decouple the traditional performance-vs-recyclability trade-off inherent in thermosets.6 However, the technology is still maturing. Key challenges include optimizing mechanical properties (particularly long-term creep resistance at elevated temperatures), ensuring stability, scaling up production cost-effectively, and demonstrating performance in demanding real-world applications.6 While AFP compatibility is not as extensively documented as for thermoplastics, the heat-activated nature of vitrimer reprocessing suggests potential synergy. Projects like the EU's AIRPOXY are actively exploring vitrimer composites for aerospace structures, highlighting the significant interest in their potential.10 Other potential applications span automotive (e.g., self-repairing panels 56), construction, and medical devices.57 For early adopters, vitrimers are a material class worth watching closely as they could offer a compelling pathway to sustainable, high-performance composites.
Note: Characteristics are generalized. Specific properties depend heavily on the exact polymer, fiber, and processing parameters.
Beyond enabling the use of recyclable materials, AFP technology inherently contributes to sustainability through significant reductions in manufacturing waste and energy consumption compared to traditional methods.
One of the most significant environmental and economic advantages of AFP is its ability to drastically reduce material waste. This stems directly from the process's precision in placing narrow, individual tows exactly where they are needed on the mold surface.25 The robotic system follows optimized paths, accurately conforming to complex contours and precisely defining the boundaries of each ply.25
This additive, near-net-shape approach contrasts sharply with conventional manufacturing paradigms. Subtractive manufacturing, common for metal components, often starts with a large billet of material, machining away the excess to achieve the final shape. This results in notoriously high "buy-to-fly" ratios – the ratio of raw material purchased to the weight of the final part. Ratios of 10:1 or even 20:1 are common in aerospace, meaning 90-95% of the initial material becomes scrap.58 Even traditional composite manufacturing methods like manual layup or ATL, which involve cutting ply shapes from large sheets of prepreg fabric or wide tapes, generate substantial offcut waste, particularly for complex geometries.27
AFP minimizes this waste dramatically. Because material is deposited only where required, offcuts are largely eliminated.39 Studies and practical applications have demonstrated remarkable improvements. For instance, specific case studies have shown material wastage rates plummeting from as high as 62% (using a combination of filament winding and hand layup) down to just 6% with AFP.27 Another comparison suggests typical waste percentages of 20% for manual prepreg layup versus only 4% for AFP tows.38 This translates to significantly improved buy-to-fly ratios 17 and substantial cost savings, given the high price of advanced composite materials.17 From an environmental perspective, reducing material waste means conserving the significant embodied energy associated with producing high-performance fibers and resins.2
The synergy between AFP's precision and advanced simulation software, like Addcomposites' AddPath, further enhances waste reduction. By simulating the entire layup process digitally, engineers can optimize toolpaths, predict material behavior during steering, identify potential defects, and refine ply boundaries before consuming any physical material.24 This virtual optimization minimizes errors, rework, and the generation of scrap during actual production, pushing material efficiency beyond what AFP alone could achieve through physical trial-and-error.
AFP also offers a pathway to significantly reduce the energy consumed during composite manufacturing, primarily by enabling processes that bypass the traditional, energy-intensive autoclave curing step required for most high-performance thermoset composites.
Autoclaves are essentially large, pressurized ovens used to consolidate and cure thermoset prepregs under controlled heat and pressure.11 While effective at producing high-quality parts, they are notoriously inefficient from an energy standpoint. They require heating not only the part itself but also the large thermal mass of the autoclave vessel and the internal atmosphere (typically nitrogen or air), often for extended periods (hours).16 This process consumes vast amounts of energy and often represents a significant bottleneck in production flow.11
AFP technology, particularly when used with thermoplastic composites, facilitates Out-of-Autoclave (OoA) manufacturing.4 The most promising OoA technique enabled by AFP is In-Situ Consolidation (ISC).11 During ISC-AFP, the heat source integrated into the AFP head (e.g., laser, high-intensity infrared) rapidly heats the incoming thermoplastic tape and the substrate to above the polymer's melting point. The compaction roller then applies pressure to fuse and consolidate the layers simultaneously with the placement process.11 If optimized correctly, this can produce a fully consolidated part directly off the machine, completely eliminating the need for a separate, energy-draining autoclave cycle.11
The energy savings achieved by eliminating the autoclave are substantial. Studies and industrial projects have reported energy reductions ranging from 75% 19 to over 90% 63, and even as high as 97% or "over two orders of magnitude" compared to conventional autoclave curing.64 While thermoplastic processing itself requires high localized temperatures 4, the energy is applied precisely where needed and for much shorter durations, avoiding the massive thermal inefficiency of heating an entire autoclave system.19 Specific energy consumption (SEC) figures vary widely depending on the process, material, and part size (e.g., autoclave thermoset might be around 5 kWh/kg 52 but can fluctuate significantly 65), but OoA processes consistently demonstrate lower overall energy demands.16
This shift from energy-intensive batch processing in an autoclave to potentially continuous or semi-continuous OoA processing with AFP-ISC represents a fundamental improvement in manufacturing efficiency. It not only saves energy but also dramatically shortens production cycle times 5, reduces work-in-progress inventory 5, potentially shrinks factory footprint requirements 11, and enables more agile, leaner production systems – all contributing factors to a more sustainable manufacturing model.
Note: Savings are indicative and depend on specific materials, part geometry, equipment efficiency, and cycle parameters. ISC requires significant localized energy input at the head but avoids heating the entire autoclave volume.
Beyond the manufacturing phase, AFP technology contributes significantly to sustainability by enabling the design and production of highly optimized, lightweight composite structures. This lightweighting has profound positive impacts on energy consumption throughout the product's operational life, especially in transportation sectors.
AFP's unique capability lies in its precision control over fiber orientation. Unlike traditional materials or manufacturing methods that result in isotropic properties or simple layer orientations, AFP allows engineers to "steer" continuous fibers along complex, curved paths.24 This means fibers can be precisely aligned with the principal stress directions and load paths within a component.27 By placing material only where it is structurally necessary and orienting it for maximum efficiency, engineers can design parts that achieve the required strength and stiffness with significantly less material, leading to substantial weight reductions compared to metal equivalents or conventionally manufactured composites.1
The benefits of this lightweighting are most pronounced during the product's use phase. In aerospace and automotive applications, reducing vehicle mass directly translates into lower energy consumption.1 A lighter aircraft requires less lift and thrust, burning less fuel.20 A lighter car requires less energy to accelerate and overcome rolling resistance.70 The impact is significant: studies suggest that every 1% reduction in aircraft weight can lead to approximately a 0.75% decrease in fuel consumption.72 A compelling example is the Boeing 787 Dreamliner, which extensively utilizes composites (many produced using automated methods like AFP/ATL); its reported 20% weight savings compared to previous generation aircraft contributed to a 10-12% improvement in fuel efficiency.20
Furthermore, lightweighting creates a positive feedback loop. A lighter airframe or chassis allows for the use of smaller, lighter engines or batteries to achieve the same performance targets, leading to further secondary weight savings and efficiency gains.2 Beyond fuel/energy savings, lightweighting improves vehicle performance (acceleration, handling), increases payload capacity, and directly reduces greenhouse gas emissions (CO2, etc.) associated with fuel combustion.1
AFP, therefore, acts as a critical design enabler. It empowers engineers to fully exploit the anisotropic nature of composite materials, moving beyond simple layered structures towards truly optimized designs. The design freedom offered by AFP – the ability to create complex shapes with tailored fiber paths 24 – when combined with powerful simulation tools like Finite Element Analysis (FEA), unlocks lightweighting potential that is simply unattainable with conventional manufacturing.35 This synergy allows for the creation of structures that are not only lighter but potentially stronger and stiffer where needed.
This use-phase energy reduction achieved through lightweighting often represents the most significant sustainability benefit over the entire product lifecycle, particularly for long-service-life assets like aircraft.3 While composite manufacturing can be energy-intensive, the substantial reduction in operational energy consumption and associated emissions frequently outweighs the initial manufacturing impact, resulting in a net positive environmental outcome.3 AFP's ability to maximize lightweighting potential is thus a cornerstone of its contribution to lifecycle sustainability.
Realizing the full potential of AFP for sustainable composite manufacturing requires not only capable hardware but also sophisticated software and accessible solutions. Addcomposites is dedicated to providing this complete ecosystem, empowering innovators to adopt and optimize AFP technology for demanding applications while prioritizing sustainability. Our versatile AFP systems, like the compact and adaptable AFP-XS, are designed to handle a range of materials including thermosets, thermoplastics, and dry fibers, offering the flexibility needed to explore sustainable material options.21 We aim to make advanced composite manufacturing accessible beyond large-scale industrial players, fostering innovation in research labs and smaller enterprises.21
Central to our offering is AddPath, a powerful yet intuitive software platform designed specifically for AFP programming, simulation, and process control.21 AddPath directly supports the implementation of sustainable AFP practices through several key features:
AddPath acts as the crucial link translating sustainable design intent into efficient manufacturing reality. It empowers designers to leverage AFP's unique capabilities for creating optimized, lightweight structures and ensures those complex designs can be manufactured reliably and efficiently, minimizing the waste and energy consumption that might otherwise occur. By offering accessible hardware solutions like the AFP-XS 21 and powerful, user-friendly software like AddPath 21, Addcomposites lowers the barrier to entry for adopting state-of-the-art AFP. This democratization is key to enabling a wider range of organizations – from research institutions to small and medium-sized enterprises – to innovate and implement sustainable composite manufacturing solutions.
Automated Fiber Placement technology stands at the forefront of a necessary evolution in composite manufacturing, offering a powerful toolkit to address the critical need for sustainability without compromising performance. As we've explored, AFP delivers multifaceted benefits:
AFP is therefore more than just an automation tool; it is a strategic technology enabling the design and production of the next generation of composite structures – components that are not only lighter, stronger, and produced more efficiently, but also fundamentally more sustainable from cradle to grave.
Addcomposites is committed to making these benefits accessible. Our integrated ecosystem of versatile AFP hardware and intelligent AddPath software provides the tools needed to implement and optimize sustainable composite manufacturing processes.
Are you ready to explore how AFP can revolutionize your composite applications and help you achieve your sustainability goals?
Together, we can leverage the power of AFP to build a more efficient, resource-conscious, and sustainable future for composite materials.