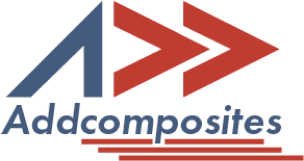
Addcomposites offers a range of Automated Fiber Placement (AFP) systems, each with unique characteristics and benefits designed to meet the varying needs of research centers, composite manufacturers, and technical centers. Here's a breakdown of their versatile AFP systems: AFP-XS, AFP-X, and SCF3D.
The AFP-XS is the introductory and most modular AFP system from Addcomposites. It's an ideal starting point for those venturing into advanced structural additive manufacturing:
The AFP-X is a production-class AFP multi-tow system designed for achieving a higher production rate for complex parts:
The SCF3D is Addcomposites' response to the increasing demand for continuous fiber additive manufacturing. It's designed to quickly create and print high-quality, structural components:
Addcomposites offers a versatile and robust Automated Fiber Placement (AFP) system, the AFP-XS. It is the most modular AFP system offered by Addcomposites, making it an ideal tool for anyone looking to venture into advanced structural additive manufacturing. It is a preferred system among technical centers and researchers due to its flexibility in working with different widths and types of material, and manufacturers appreciate its ability to cover larger surfaces without sacrificing the ability to layup on more complex shapes1.
The AFP-XS system extends its capabilities to tape winding and filament winding. This flexibility makes it possible to create a variety of components, from hydrogen tanks and booms to tubes and fittings.
One of the key advantages of the AFP-XS system is its ability to work with a wide range of materials. It can handle Dry fiber, Thermoset, and Thermoplastic materials, providing a significant degree of freedom for research and development, and for production strategies2.
The AFP-XS system's versatility, combined with its advanced capabilities, opens up a wide range of potential applications. It can be used in research centers and technical centers for the development of new materials and production strategies. It also serves as a powerful tool for composite manufacturers for the production of complex parts.
Discover the future of composite manufacturing with Addcomposites! Here's how you can get involved:
At Addcomposites, we are dedicated to revolutionizing composite manufacturing. Our AFP systems and comprehensive support services are waiting for you to harness. So, don't wait – get started on your journey to the future of manufacturing today!
Addcomposites offers a range of Automated Fiber Placement (AFP) systems, each with unique characteristics and benefits designed to meet the varying needs of research centers, composite manufacturers, and technical centers. Here's a breakdown of their versatile AFP systems: AFP-XS, AFP-X, and SCF3D.
The AFP-XS is the introductory and most modular AFP system from Addcomposites. It's an ideal starting point for those venturing into advanced structural additive manufacturing:
The AFP-X is a production-class AFP multi-tow system designed for achieving a higher production rate for complex parts:
The SCF3D is Addcomposites' response to the increasing demand for continuous fiber additive manufacturing. It's designed to quickly create and print high-quality, structural components:
Addcomposites offers a versatile and robust Automated Fiber Placement (AFP) system, the AFP-XS. It is the most modular AFP system offered by Addcomposites, making it an ideal tool for anyone looking to venture into advanced structural additive manufacturing. It is a preferred system among technical centers and researchers due to its flexibility in working with different widths and types of material, and manufacturers appreciate its ability to cover larger surfaces without sacrificing the ability to layup on more complex shapes1.
The AFP-XS system extends its capabilities to tape winding and filament winding. This flexibility makes it possible to create a variety of components, from hydrogen tanks and booms to tubes and fittings.
One of the key advantages of the AFP-XS system is its ability to work with a wide range of materials. It can handle Dry fiber, Thermoset, and Thermoplastic materials, providing a significant degree of freedom for research and development, and for production strategies2.
The AFP-XS system's versatility, combined with its advanced capabilities, opens up a wide range of potential applications. It can be used in research centers and technical centers for the development of new materials and production strategies. It also serves as a powerful tool for composite manufacturers for the production of complex parts.
Discover the future of composite manufacturing with Addcomposites! Here's how you can get involved:
At Addcomposites, we are dedicated to revolutionizing composite manufacturing. Our AFP systems and comprehensive support services are waiting for you to harness. So, don't wait – get started on your journey to the future of manufacturing today!