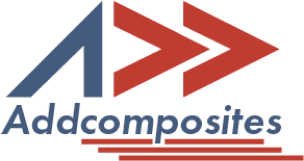
Plastic extrusion, once confined to large industrial settings, has now captured the imagination of hobbyists and small-scale manufacturers alike. This surge in interest is driven by several factors:
This guide aims to demystify the process of plasticizing screw extrusion for newcomers to the field. We'll cover:
While we'll touch on some advanced concepts, our focus is on providing a solid foundation for hobbyists and engineers new to the field. For those interested in a broader overview of additive manufacturing technologies, our article on What is Additive Manufacturing provides valuable context.
Before we dive in, let's clarify some key terms you'll encounter throughout this guide:
While plastic extrusion can be an exciting and rewarding process, it's crucial to prioritize safety. Key risks include:
Essential safety measures include:
Remember, safety should always be your top priority when working with extrusion equipment.
In the next section, we'll delve into the fascinating world of thermoplastics, exploring their properties and behavior during the extrusion process.
Before we dive into the extrusion process, it's crucial to understand the materials we're working with: thermoplastics. This knowledge will help you make informed decisions about which plastics to use and how to process them effectively.
Plastics fall into two main categories: thermosets and thermoplastics. Let's explore the differences:
For more information on how these materials are used in advanced manufacturing, check out our article on Continuous Fiber 3D Printing.
Thermoplastics have several properties that make them ideal for extrusion and 3D printing:
Understanding these properties is crucial for setting the right extrusion parameters. For instance, when creating filaments for 3D printing, you need to consider both the extrusion temperature and the printing temperature. Our article on Advancing 3D Printing: Continuous Carbon Fiber Reinforced Filaments provides more insights into how these properties affect advanced 3D printing techniques.
Here are some of the most frequently used thermoplastics in extrusion and 3D printing:
For more advanced applications, such as in the automotive or aerospace industries, specialized thermoplastics are often used. Learn more about these applications in our article on AFP ATL Thermoplastic Composite Production Tape Process and Heating.
While thermoplastics offer many advantages, they also present some challenges in processing:
Understanding these challenges is crucial for successful extrusion. In the next sections, we'll explore how the design of extrusion equipment addresses these issues.
By understanding the nature of thermoplastics, their properties, and the challenges they present, you're better equipped to handle the extrusion process. In the next chapter, we'll dive into the details of the screw extrusion process and the equipment used.
In this chapter, we'll explore the fascinating world of screw extrusion, breaking down the process and the equipment involved. This knowledge is crucial for anyone looking to understand or work with plastic extrusion, whether for 3D printing filament production or other applications.
Screw extrusion is a continuous process that melts, mixes, and shapes plastic materials. The core principle is simple: a rotating screw pushes plastic through a heated barrel, melting and homogenizing it before forcing it through a die to create a shaped product.
Key Steps in the Process:
For a more in-depth look at how this process is applied in advanced manufacturing, check out our article on Thermoplastic Tape Winding of Hydrogen Tank.
Let's break down the main parts of a typical screw extruder:
Understanding these components is crucial when working with or troubleshooting extrusion systems. For those interested in how these principles apply to large-scale production, our article on First Ever LFAM with High Volume Continuous Fiber Printing provides valuable insights.
The melting of plastic in a screw extruder is a complex process involving several heat sources:
Interestingly, in many extrusion setups, shear heating accounts for 60-80% of the total heat input.
The design of the extruder screw is critical to the extrusion process. Key features include:
For those interested in advanced screw designs used in high-performance applications, our article on The Rise of Continuous Fiber 3D Printing in Large-Scale Production offers valuable insights.
Understanding these components and their functions is crucial for anyone working with or troubleshooting extrusion systems. In the next chapter, we'll delve deeper into the different zones of the plasticizing screw and how they contribute to the extrusion process.
The plasticizing screw is the heart of the extrusion process. Understanding its different zones is crucial for anyone working with plastic extrusion, whether for creating 3D printer filaments or other applications. In this chapter, we'll break down the three main zones of a typical plasticizing screw and explain their functions.
A standard plasticizing screw is divided into three primary zones:
Each zone plays a specific role in transforming solid plastic pellets into a homogeneous melt ready for extrusion.
For those interested in how these zones apply to advanced manufacturing techniques, our article on AFP ATL Thermoplastic Composite Production Tape Process and Heating provides valuable context.
The feed zone is where the journey begins for the plastic pellets.
Key Characteristics:
Functions:
Challenges in the Feed Zone:
The compression zone is where most of the melting occurs.
Key Characteristics:
Functions:
The compression ratio, which we discussed in the previous chapter, is primarily determined by the design of this zone.
Understanding the melting process in this zone is crucial for optimizing extrusion parameters. For more on how this applies to advanced manufacturing, check out our article on Continuous Fiber 3D Printing.
The metering zone is the final section of the screw, where the plastic is prepared for extrusion.
Key Characteristics:
Functions:
The design of the metering zone is critical for maintaining consistent output quality.
For those interested in how precise control in this zone enables advanced applications, our article on SCF3D Unveiled: Transforming Industries with Continuous Fiber 3D Printing offers fascinating insights.
The design of each zone significantly impacts the extrusion process:
Optimizing these zones for specific materials and applications is a key aspect of screw design.
Understanding these zones and their functions is crucial for troubleshooting extrusion issues and optimizing the process for different materials. In the next chapter, we'll explore how barrel heating interacts with these zones to control the extrusion process.
Proper temperature control is crucial for successful plastic extrusion. In this chapter, we'll explore how barrel heating works, why it's important, and how to manage it effectively. This knowledge is essential for anyone working with extrusion, from creating 3D printer filaments to more advanced applications.
The extruder barrel is typically divided into several heating zones, each independently controlled. This zonal heating approach allows for precise temperature management throughout the extrusion process.
Key reasons for multiple temperature zones:
For insights into how precise temperature control enables advanced manufacturing techniques, check out our article on Thermoplastic Tape Winding of Hydrogen Tank.
Several methods are used to heat the extruder barrel:
Accurate temperature measurement is crucial for proper control. Common sensor types include:
These sensors are typically embedded in the barrel wall to provide real-time temperature data.
For more on how precise temperature sensing enables advanced processes, see our article on AFP ATL Thermoplastic Composite Production Tape Process and Heating.
Proper temperature settings are crucial for successful extrusion. Here's a general approach:
Remember, these are general guidelines. Specific applications, like those discussed in our
article on Continuous Fiber 3D Printing, may require unique temperature profiles.
Understanding common problems can help in troubleshooting:
While heating is crucial, cooling also plays a vital role, especially post-extrusion:
The cooling method can significantly affect the final product properties, especially in advanced applications like those discussed in our article on The Rise of Continuous Fiber 3D Printing in Large-Scale Production.
Understanding barrel heating and temperature control is crucial for producing high-quality extruded products. In the next chapter, we'll explore the final components of the extrusion system: the die, breaker plate, and filters.
As we reach the end of the extrusion system, we encounter three critical components: the die, breaker plate, and filters. These elements play crucial roles in shaping the final product and ensuring its quality. Understanding these components is essential for anyone involved in plastic extrusion, from creating 3D printer filaments to more complex applications.
The die is the final shaping tool in the extrusion process, determining the cross-sectional shape of the extruded product.
For more insights into how dies are used in advanced manufacturing processes, check out our article on First Ever LFAM with High Volume Continuous Fiber Printing.
The breaker plate is a critical component located between the end of the screw and the die.
For an example of how breaker plates are utilized in advanced applications, see our article on Thermoplastic Tape Winding of Hydrogen Tank.
Filters, also known as screens or screen packs, are essential for removing contaminants from the molten plastic.
For insights into how precise filtration enables advanced manufacturing techniques, check out our article on Advancing 3D Printing: Continuous Carbon Fiber Reinforced Filaments.
Proper maintenance of these components is crucial for consistent extrusion quality:
Common issues and solutions:
Understanding these components and their interplay is crucial for producing high-quality extruded products. For those interested in how these principles apply to advanced manufacturing, our article on The Rise of Continuous Fiber 3D Printing in Large-Scale Production offers valuable insights.
In the next chapter, we'll explore the various types of plastic materials used in extrusion and how to work with them effectively.
Understanding the properties and handling requirements of different plastic materials is crucial for successful extrusion. In this chapter, we'll explore various types of plastics, their characteristics, and best practices for working with them.
Virgin pellets are new, unprocessed plastic materials that haven't been used or recycled before.
For more information on how virgin materials are used in advanced applications, check out our article on Continuous Fiber 3D Printing.
Colorants and additives are used to modify the properties or appearance of the base plastic.
For insights into how additives enable advanced manufacturing techniques, see our article on AFP ATL Thermoplastic Composite Production Tape Process and Heating.
Using recycled plastics in extrusion can be both environmentally friendly and cost-effective, but it comes with challenges.
For more on working with recycled materials in advanced applications, check out Advancing 3D Printing: Continuous Carbon Fiber Reinforced Filaments.
Proper material preparation is crucial for successful extrusion.
Many plastics are hygroscopic (absorb moisture from the air) and require drying before processing.
Blending different materials or adding colorants/additives requires careful consideration.
For insights into material preparation for advanced processes, see our article on SCF3D Unveiled: Transforming Industries with Continuous Fiber 3D Printing.
Choosing the right material for your extrusion project involves several factors:
Understanding these materials and how to work with them is crucial for producing high-quality extruded products. For those interested in how material selection impacts advanced manufacturing, our article on The Rise of Continuous Fiber 3D Printing in Large-Scale Production offers valuable insights.
In the next chapter, we'll explore how extrusion technology is specifically applied in the context of 3D printing.
Extrusion technology plays a crucial role in the world of 3D printing. In this chapter, we'll explore how extrusion is applied in various 3D printing contexts, from creating filaments for desktop printers to large-scale additive manufacturing.
Fused Deposition Modeling (FDM), also known as Fused Filament Fabrication (FFF), is the most common type of 3D printing for hobbyists and small-scale production.
For more insights into advanced filament production, check out our article on Advancing 3D Printing: Continuous Carbon Fiber Reinforced Filaments.
Large-format 3D printers often use pellet extruders instead of filament, offering several advantages.
For a deep dive into large-format 3D printing, see our article on First Ever LFAM with High Volume Continuous Fiber Printing.
An advanced form of 3D printing that combines thermoplastic extrusion with continuous fiber reinforcement.
For more on this cutting-edge technology, check out our detailed article on Continuous Fiber 3D Printing.
Successful 3D printing requires careful control of extrusion parameters.
Different materials require different extrusion parameters. For example:
The field of extrusion-based 3D printing is rapidly evolving. Some exciting trends include:
For insights into the future of this technology, see our article on The Rise of Continuous Fiber 3D Printing in Large-Scale Production.
Understanding the application of extrusion technology in 3D printing opens up a world of possibilities for creating custom parts and products. Whether you're working with desktop FDM printers or exploring large-scale additive manufacturing, the principles of extrusion remain central to the process.
In the next chapter, we'll discuss common troubleshooting techniques for extrusion-related issues in both traditional extrusion and 3D printing applications.
Even with careful preparation and operation, extrusion processes can encounter various issues. In this chapter, we'll explore common problems in both traditional extrusion and 3D printing applications, along with strategies to diagnose and resolve them.
Inconsistent extrusion can manifest as variations in the diameter of extruded filament or inconsistent flow in 3D printing.
For more insights on maintaining consistent extrusion in advanced applications, see our article on AFP ATL Thermoplastic Composite Production Tape Process and Heating.
Degradation can occur when plastic is exposed to excessive heat or shear, leading to changes in color, smell, or material properties.
Surface defects can range from minor cosmetic issues to significant problems that affect part functionality.
For more on achieving high-quality surface finishes in advanced processes, check out our article on Continuous Fiber 3D Printing.
This issue is particularly common in 3D printing but can also occur in traditional extrusion processes.
Nozzle clogs can halt the 3D printing process and require immediate attention.
For insights on preventing clogs in advanced 3D printing processes, see our article on SCF3D Unveiled: Transforming Industries with Continuous Fiber 3D Printing.
When facing any extrusion issue, follow these general steps:
Regular maintenance can prevent many common extrusion issues:
For more on maintaining advanced extrusion systems, check out our article on The Rise of Continuous Fiber 3D Printing in Large-Scale Production.
Understanding these common issues and how to address them will help you maintain consistent, high-quality output in your extrusion projects, whether you're creating filaments, 3D printing parts, or working on other extrusion applications.
In our final chapter, we'll look at future trends and draw some conclusions about the exciting world of plasticizing screw extrusion.
As we conclude our exploration of plasticizing screw extrusion, let's look ahead to emerging trends and technologies that are shaping the future of this field. We'll also recap the key points we've covered throughout this guide.
The development of new and improved materials is driving innovation in extrusion technology.
For more on advanced materials in extrusion, check out our article on Advancing 3D Printing: Continuous Carbon Fiber Reinforced Filaments.
The integration of smart technologies is revolutionizing extrusion processes.
Environmental concerns are driving innovations in sustainable extrusion practices.
Learn more about sustainable extrusion in our article on The Rise of Continuous Fiber 3D Printing in Large-Scale Production.
Innovative screw designs are pushing the boundaries of what's possible in extrusion.
The integration of extrusion with other manufacturing techniques is opening new possibilities.
For insights into hybrid manufacturing processes, see our article on Continuous Fiber 3D Printing.
As we conclude this guide, let's recap some of the crucial points we've covered:
Plasticizing screw extrusion is a versatile and powerful technology with applications ranging from creating 3D printer filaments to producing complex industrial components. As we've seen throughout this guide, success in extrusion requires a blend of theoretical knowledge and practical skills.
Whether you're a hobbyist exploring 3D printing or an engineer working on advanced manufacturing processes, the principles we've discussed provide a solid foundation for your extrusion projects. Remember that mastery comes with practice and continuous learning.
We encourage you to explore the linked resources throughout this guide for more in-depth information on specific topics. Additionally, stay curious about new developments in the field – the world of extrusion is constantly evolving, offering exciting opportunities for innovation and improvement.
Thank you for joining us on this journey through the fundamentals of plasticizing screw extrusion. We hope this guide serves as a valuable resource in your extrusion endeavors.
For those looking to delve deeper into the world of plasticizing screw extrusion and related technologies, here are some valuable resources:
Additionally, we recommend exploring the following online resources:
For more specific topics related to advanced manufacturing techniques, don't forget to check out our other articles:
Figure Credits: The figures used in this blog post are adapted from the excellent resource provided by Dr. Flo:
We express our gratitude to Dr. Flo for the informative visuals that have enhanced the educational value of this guide.
We hope this guide has ignited your passion for plasticizing screw extrusion. Here are some ways you can continue to grow and innovate in this exciting field:
Remember, the realm of plasticizing screw extrusion is dynamic and full of opportunities. Your journey is just beginning, and the potential for innovation is limitless. Keep experimenting, learning, and pushing the boundaries of what's possible!