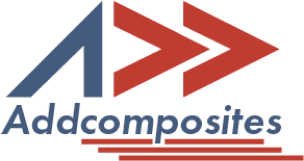
The use of carbon fiber-reinforced polyether ether ketone (CF/PEEK) composites has exponentially grown across various high-performance industries, including aerospace and marine sectors, primarily due to their exceptional strength-to-weight ratio and durability. This surge in utilization, however, has concurrently led to a significant increase in manufacturing waste, particularly in the form of offcuts from processes like laser-assisted tape placement (LATP). While CF/PEEK composites offer unparalleled benefits in application, the environmental and economic ramifications of their production waste have emerged as a pressing challenge.
The industry's current practices in handling CF/PEEK offcut waste—often involving disposal in landfills or incineration—pose severe environmental threats. Notably, the production of virgin CF and its composites is energy-intensive, contributing to a substantial carbon footprint. Moreover, the non-biodegradable nature of these materials exacerbates landfill issues, leading to a pressing need for sustainable waste management solutions.
The economic implications of discarding CF/PEEK offcuts cannot be understated.
Given the high costs associated with CF/PEEK production, the disposal of offcuts represents a significant loss of valuable materials and financial resources. In light of the growing emphasis on sustainability and circular economy principles, the industry faces increasing pressure to adopt more environmentally friendly and cost-effective methods for managing CF/PEEK waste.
The manufacturing of CF/PEEK composites, while critical for producing high-performance components in aerospace, marine, and automotive industries, generates substantial waste. Specifically, the offcuts from the laser-assisted tape placement (LATP) process represent a significant environmental and economic challenge. The conventional disposal methods of these offcuts, such as landfilling or incineration, have far-reaching consequences, emphasizing the need for sustainable waste management strategies.
Environmental Impact:
Economic Impact:
The environmental and economic impacts of discarding CF/PEEK manufacturing offcuts underscore the urgent need for sustainable waste management practices. By exploring innovative recycling methods, the industry can address these challenges, reduce its environmental footprint, and create economic value from materials that would otherwise contribute to waste. The next sections of the blog will delve into the innovative approaches being developed to recycle CF/PEEK offcuts, showcasing potential solutions to this multifaceted problem.
Addressing the pressing environmental and economic challenges posed by the disposal of CF/PEEK offcut waste requires innovative recycling solutions that circumvent traditional barriers. The process of recycling CF/PEEK composites, especially those resulting from high-precision manufacturing techniques like laser-assisted tape placement (LATP), demands methods that preserve the material's inherent high-performance properties while offering a sustainable pathway for waste reduction. An innovative approach that has shown promise involves the direct reuse of offcut waste without the need for shredding, grinding, or further cutting, thereby maintaining the structural integrity and performance characteristics of the original material.
The core of this innovative recycling approach is the utilization of offcut waste as it is, leveraging the existing dimensions and properties of the offcuts to create new laminates. By carefully arranging these offcuts into predefined patterns and configurations, it's possible to manufacture composite laminates that exhibit comparable mechanical properties to those made from virgin materials. This process involves:
The challenge of managing CF/PEEK offcut waste has prompted the development of an innovative recycling method that not only addresses environmental and economic concerns but also sets a new standard for sustainable manufacturing practices in the high-performance composite industry. This method, centered around the direct reuse of offcuts without additional processing, signifies a pivotal shift towards a more circular economy approach within the sector.
The introduction of this recycling method has demonstrated considerable success in transforming CF/PEEK offcut waste into valuable composite laminates. By maintaining the original properties of the offcuts and utilizing them in new manufacturing processes, this approach not only reduces waste but also maximizes the utilization of existing resources. The key achievements of this method include:
Despite its successes, the path to implementing this recycling method on a larger scale involves overcoming several challenges. These include ensuring the consistent quality of recycled laminates, developing more efficient sorting and assembly processes, and addressing logistical considerations for collecting and storing offcuts. Continuous innovation and research are crucial for refining the method and expanding its applicability across different composite manufacturing scenarios.
Looking forward, the success of recycling CF/PEEK offcuts could serve as a model for other materials and industries, highlighting the feasibility and benefits of sustainable manufacturing practices. Encouraging collaboration among industry stakeholders, researchers, and policymakers is essential to create an ecosystem that supports circular economy principles and sustainability goals.
The adoption of this recycling method signifies a promising step towards reducing the environmental impact of composite manufacturing and fostering a culture of sustainability within the industry. As we continue to explore and optimize this approach, the potential for significant advancements in sustainable manufacturing practices becomes increasingly evident, marking a positive trajectory towards a more responsible and efficient use of resources in the high-performance composite sector.
By embracing innovative recycling solutions like the direct reuse of CF/PEEK offcuts, the composite manufacturing industry can not only mitigate its environmental footprint but also demonstrate leadership in sustainability, setting a precedent for future developments in the field.
In drafting this blog, we extend our sincerest gratitude to Aswani Kumar Bandaru, Thomas Anderson, and Paul M. Weaver for their pioneering work detailed in the study, "Recycling CF/PEEK offcut waste from laser assisted tape placement: Influence of overlaps and gaps." Their research offers invaluable insights into innovative recycling methods for CF/PEEK offcuts, providing a sustainable solution to a significant environmental and economic challenge. Their contributions are not only pivotal in advancing sustainable manufacturing practices but also inspire continued innovation in the field of composite materials recycling. We thank them for their dedication and for laying the groundwork that could lead to more eco-efficient manufacturing processes in the aerospace, automotive, and marine industries.
Discover the future of composite manufacturing with Addcomposites! Here's how you can get involved:
At Addcomposites, we are dedicated to revolutionizing composite manufacturing. Our AFP systems and comprehensive support services are waiting for you to harness. So, don't wait – get started on your journey to the future of manufacturing today!
The use of carbon fiber-reinforced polyether ether ketone (CF/PEEK) composites has exponentially grown across various high-performance industries, including aerospace and marine sectors, primarily due to their exceptional strength-to-weight ratio and durability. This surge in utilization, however, has concurrently led to a significant increase in manufacturing waste, particularly in the form of offcuts from processes like laser-assisted tape placement (LATP). While CF/PEEK composites offer unparalleled benefits in application, the environmental and economic ramifications of their production waste have emerged as a pressing challenge.
The industry's current practices in handling CF/PEEK offcut waste—often involving disposal in landfills or incineration—pose severe environmental threats. Notably, the production of virgin CF and its composites is energy-intensive, contributing to a substantial carbon footprint. Moreover, the non-biodegradable nature of these materials exacerbates landfill issues, leading to a pressing need for sustainable waste management solutions.
The economic implications of discarding CF/PEEK offcuts cannot be understated.
Given the high costs associated with CF/PEEK production, the disposal of offcuts represents a significant loss of valuable materials and financial resources. In light of the growing emphasis on sustainability and circular economy principles, the industry faces increasing pressure to adopt more environmentally friendly and cost-effective methods for managing CF/PEEK waste.
The manufacturing of CF/PEEK composites, while critical for producing high-performance components in aerospace, marine, and automotive industries, generates substantial waste. Specifically, the offcuts from the laser-assisted tape placement (LATP) process represent a significant environmental and economic challenge. The conventional disposal methods of these offcuts, such as landfilling or incineration, have far-reaching consequences, emphasizing the need for sustainable waste management strategies.
Environmental Impact:
Economic Impact:
The environmental and economic impacts of discarding CF/PEEK manufacturing offcuts underscore the urgent need for sustainable waste management practices. By exploring innovative recycling methods, the industry can address these challenges, reduce its environmental footprint, and create economic value from materials that would otherwise contribute to waste. The next sections of the blog will delve into the innovative approaches being developed to recycle CF/PEEK offcuts, showcasing potential solutions to this multifaceted problem.
Addressing the pressing environmental and economic challenges posed by the disposal of CF/PEEK offcut waste requires innovative recycling solutions that circumvent traditional barriers. The process of recycling CF/PEEK composites, especially those resulting from high-precision manufacturing techniques like laser-assisted tape placement (LATP), demands methods that preserve the material's inherent high-performance properties while offering a sustainable pathway for waste reduction. An innovative approach that has shown promise involves the direct reuse of offcut waste without the need for shredding, grinding, or further cutting, thereby maintaining the structural integrity and performance characteristics of the original material.
The core of this innovative recycling approach is the utilization of offcut waste as it is, leveraging the existing dimensions and properties of the offcuts to create new laminates. By carefully arranging these offcuts into predefined patterns and configurations, it's possible to manufacture composite laminates that exhibit comparable mechanical properties to those made from virgin materials. This process involves:
The challenge of managing CF/PEEK offcut waste has prompted the development of an innovative recycling method that not only addresses environmental and economic concerns but also sets a new standard for sustainable manufacturing practices in the high-performance composite industry. This method, centered around the direct reuse of offcuts without additional processing, signifies a pivotal shift towards a more circular economy approach within the sector.
The introduction of this recycling method has demonstrated considerable success in transforming CF/PEEK offcut waste into valuable composite laminates. By maintaining the original properties of the offcuts and utilizing them in new manufacturing processes, this approach not only reduces waste but also maximizes the utilization of existing resources. The key achievements of this method include:
Despite its successes, the path to implementing this recycling method on a larger scale involves overcoming several challenges. These include ensuring the consistent quality of recycled laminates, developing more efficient sorting and assembly processes, and addressing logistical considerations for collecting and storing offcuts. Continuous innovation and research are crucial for refining the method and expanding its applicability across different composite manufacturing scenarios.
Looking forward, the success of recycling CF/PEEK offcuts could serve as a model for other materials and industries, highlighting the feasibility and benefits of sustainable manufacturing practices. Encouraging collaboration among industry stakeholders, researchers, and policymakers is essential to create an ecosystem that supports circular economy principles and sustainability goals.
The adoption of this recycling method signifies a promising step towards reducing the environmental impact of composite manufacturing and fostering a culture of sustainability within the industry. As we continue to explore and optimize this approach, the potential for significant advancements in sustainable manufacturing practices becomes increasingly evident, marking a positive trajectory towards a more responsible and efficient use of resources in the high-performance composite sector.
By embracing innovative recycling solutions like the direct reuse of CF/PEEK offcuts, the composite manufacturing industry can not only mitigate its environmental footprint but also demonstrate leadership in sustainability, setting a precedent for future developments in the field.
In drafting this blog, we extend our sincerest gratitude to Aswani Kumar Bandaru, Thomas Anderson, and Paul M. Weaver for their pioneering work detailed in the study, "Recycling CF/PEEK offcut waste from laser assisted tape placement: Influence of overlaps and gaps." Their research offers invaluable insights into innovative recycling methods for CF/PEEK offcuts, providing a sustainable solution to a significant environmental and economic challenge. Their contributions are not only pivotal in advancing sustainable manufacturing practices but also inspire continued innovation in the field of composite materials recycling. We thank them for their dedication and for laying the groundwork that could lead to more eco-efficient manufacturing processes in the aerospace, automotive, and marine industries.
Discover the future of composite manufacturing with Addcomposites! Here's how you can get involved:
At Addcomposites, we are dedicated to revolutionizing composite manufacturing. Our AFP systems and comprehensive support services are waiting for you to harness. So, don't wait – get started on your journey to the future of manufacturing today!