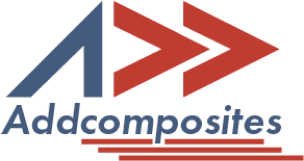
The landscape of advanced manufacturing is witnessing a revolutionary leap forward with the introduction of a groundbreaking Large Format Additive Manufacturing (LFAM) system called Structural Continuous Fiber 3D Printing (SCF3D) system. This innovative technology seamlessly integrates high volume continuous fiber printing, marking a significant milestone in the evolution of 3D printing for industrial applications.
Unlike traditional LFAM systems that prioritize polymer output volume, this new technology redefines the paradigm by focusing on achieving unprecedented strength-to-weight ratios. By incorporating the capability to print with continuous fiber reinforcement, this system bridges the gap between conventional additive manufacturing and high-performance composite production.
The significance of this development cannot be overstated. It represents a fusion of additive manufacturing's design freedom with the superior mechanical properties of continuous fiber composites. This convergence opens up new possibilities for industries ranging from aerospace and automotive to marine and sports equipment manufacturing, where lightweight, high-strength parts are crucial.
As we delve deeper into the features and capabilities of this new LFAM system, we'll explore how it's poised to revolutionize composite manufacturing, offering enhanced design flexibility, improved cost-effectiveness, and the potential to accelerate innovation across various industrial sectors.
To fully appreciate the impact of this new LFAM system, it's essential to understand the broader context of composite materials and manufacturing. For an in-depth introduction to composites, check out our comprehensive guide on composite materials. Additionally, to see how this technology fits into the larger picture of additive manufacturing, read our article on the evolution of additive manufacturing in composites.
The new Large Format Additive Manufacturing (LFAM) system with high volume continuous fiber printing capabilities stands out due to its innovative features:
These features collectively represent a significant advancement in LFAM technology, offering unprecedented control over material properties and part performance.
For a deeper dive into the AddPrint software and its capabilities, visit our AddPrint product page. To understand how digital twin technology is revolutionizing composite manufacturing, read our article on digital twins in composite parts manufacturing.
The new LFAM system with high volume continuous fiber printing capabilities represents a paradigm shift in large format additive manufacturing. To fully appreciate its innovations, let's compare it with traditional LFAM methods:
By focusing on strategic fiber placement and advanced process control, this new LFAM technology achieves a level of part performance and material efficiency that was previously unattainable with traditional large format additive manufacturing methods.
To further explore the advantages of this new LFAM system over traditional methods, check out our comprehensive comparison of automated fiber placement vs. filament winding for hydrogen tank production. For those interested in the evolution of LFAM technologies, our article on the shift from traditional to intelligent composite manufacturing provides valuable insights.
The new LFAM i.e. SCF3D system with high volume continuous fiber printing capabilities offers exceptional versatility in terms of material compatibility and achieves impressive performance metrics:
The combination of material flexibility and high performance makes this LFAM system suitable for a wide range of industrial applications, from lightweight aerospace components to high-strength automotive parts and durable marine structures.
For a more in-depth look at the materials used in advanced composite manufacturing, including those compatible with our new LFAM system, visit our guide on fiber reinforcements. To understand the performance characteristics of continuous fiber composites, read our article on understanding continuous fiber composites.
The new LFAM i.e. SCF3D system with high volume continuous fiber printing offers several significant advantages over traditional manufacturing methods:
These advantages position the new LFAM i.e. SCF3D system as a game-changer in composite manufacturing, offering a unique combination of performance, efficiency, and flexibility that addresses many of the challenges faced by traditional manufacturing methods.
To further explore the advantages of this new LFAM technology, particularly in terms of sustainability, read our article on embracing circular economy in composite materials. For those interested in the cost-effectiveness of this technology, our guide on how much an automated fiber placement machine costs provides valuable insights.
The new LFAM system with high volume continuous fiber printing capabilities opens up a wide range of applications across various industries. Its ability to produce lightweight, high-strength parts with complex geometries makes it particularly suitable for:
The versatility of this LFAM system makes it particularly suited for industries requiring 1,000 to 10,000 highly customized parts per year. It bridges the gap between prototyping and mass production, offering a cost-effective solution for medium-volume, high-performance part manufacturing.
For more detailed information on how this LFAM technology can be applied in specific industries, visit our application pages for aerospace, automotive, and marine sectors. To see how continuous fiber 3D printing is being used in large-scale production, read our article on the rise of continuous fiber 3D printing in large-scale production.
While the new LFAM system with high volume continuous fiber printing represents a significant advancement in composite manufacturing, it's important to acknowledge its current limitations and the ongoing research efforts to overcome these challenges.
By addressing these limitations and pursuing these research directions, the technology is poised to further revolutionize composite manufacturing, opening up new possibilities across various industries.
To stay updated on the latest developments in composite manufacturing research, including efforts to overcome current limitations, subscribe to our monthly research updates. For those interested in contributing to the advancement of this technology, explore our educational rental options for university projects and research programs.
Discover the future of composite manufacturing with Addcomposites! Here's how you can get involved:
At Addcomposites, we are dedicated to revolutionizing composite manufacturing. Our AFP systems and comprehensive support services are waiting for you to harness. So, don't wait – get started on your journey to the future of manufacturing today!
As you consider the next steps in exploring this groundbreaking LFAM technology, we invite you to learn more about our specific products. Visit our product pages for the AFP-XS, AFP-X, and SCF3D systems to find the solution that best fits your needs. For those ready to take the plunge into advanced composite manufacturing, contact us to discuss how we can help revolutionize your production processes.