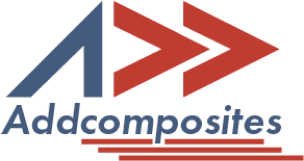
In the realm of composite materials, the intricacies of winding patterns and fiber stacking are not just minute details—they are pivotal elements that dictate the strength, durability, and overall performance of the final product. The blog delves into the heart of these techniques, unraveling the complexities and presenting them in a manner that both industry veterans and budding researchers can appreciate with the following key points
Filament winding is a fabrication process used to create composite materials with high strength-to-weight ratios. It involves winding filaments under tension over a rotating mandrel. The mandrel's shape dictates the final shape of the composite material, and the winding pattern determines the structural integrity and performance of the final product.
Winding patterns are crucial in filament winding as they affect the composite's mechanical properties and structural integrity. A suitable winding pattern ensures full and rotationally symmetric coverage, homogeneous thickness in the circumferential direction, and appropriate roving overlap according to the desired number of layers. The repetitive nature of the winding process means that each layer must be precisely placed adjacent to the previous one, with overlaps adjusted to achieve the desired laminate thickness and fiber volume fraction.
Fiber stacking, or the arrangement of fiber bundles in a composite, contributes significantly to the performance of the final product. The orientation and overlap of fibers affect the load distribution and the ability of the composite to withstand various stresses. For instance, a 50% overlap is preferred for two layers, while a 25% overlap is suitable for four layers, ensuring uniform thickness and strength across the composite.
The design process must consider the dimensions of the fiber bundle, as these will influence the winding pattern. The width and thickness of the fiber bundle, if not accounted for, can lead to inhomogeneities in the pattern and, consequently, in the structural performance of the composite.
The creation of winding patterns involves solving a first-order Diophantine equation, which is a relationship between integer numbers that governs the pattern. The equation takes into account the dimensions of the fiber bundle and the desired overlap, leading to an algorithm that can generate suitable patterns for a given set of parameters.
For example, the condition for full coverage at the equator of a wound body is given by the equation:
neq⋅beff=2π⋅R
where neq is the number of fiber bundles at the equator, beff is the effective width of the fiber bundle at the equator, and R is the radius of the body at the equator.
The basic theory of winding patterns and fiber stacking is a complex interplay of geometry, physics, and material science. The precise control of winding patterns and fiber stacking is essential in creating composites that meet specific performance criteria.
The filament winding process in composite material manufacturing relies heavily on the precision of winding patterns. These patterns are responsible for the distribution of fibers across the structure, directly influencing its mechanical properties and integrity. The algorithm for generating these patterns is a complex yet fascinating aspect of composite design, involving a blend of mathematics and material science.
The algorithm's primary goal is to create a winding pattern that ensures the optimal placement of fiber bundles, thereby achieving the desired structural integrity and performance. The process begins with the setting of input parameters, which are dictated by the scalar value of the winding angle, denoted as 'β'. This angle is independent and considered a control parameter, while the eccentricity value 'ε' and the fiber bundle thickness 't' are fixed.
To construct a suitable pattern, the algorithm considers 'β' as the main control parameter, with the dimensionless fiber bundle width 'B' associated with it. On the equatorial circumference, the fiber bundle occupies an arc corresponding to an angle 'Φβ', which is derived from the equation:
Φβ=B⋅cos(β)
This angle, in conjunction with 'ΦK(β)', determines the pattern parameters, which are initially real numbers. A perfect pattern is achieved when the Diophantine equations are satisfied for a particular 'β-value', meaning all involved products should be integers. However, this simultaneous satisfaction of conditions is generally not possible, necessitating a specialized strategy to identify potential solution intervals for 'β' and to select the best solutions to minimize undesired fiber bundle overlap.
The algorithm operates by localizing 'β-values' that provide integer numbers for 'p(β)', 'k(β)', and 'n(β)', which are points where the value of the stepped lines changes. These values, along with the bounds '[βmin, βmax]', define the intervals potentially containing a solution. The algorithm then identifies intervals containing a possible winding pattern by ensuring that the interval bounds satisfy a set of mathematical conditions.
Every interval that meets these conditions contains three integers that satisfy the Diophantine equation automatically for the assumed number of layers. The algorithm denotes the leading solution by '{p+, k+, dn+}' and the lagging one by '{p-, k-, dn-}'. The corresponding required 'ΦK-angles' can then be found by specific equations provided in the text.
Pattern pattern-generating algorithm is a critical component in the filament winding process, ensuring that the fiber bundles are placed accurately to achieve the desired structural properties. Its precision directly impacts the quality of the resulting product, particularly in terms of laminate coherence and thickness distribution.
In the realm of filament winding, the concept of laminate thickness is pivotal. It's not just a matter of layering fibers; it's about precision engineering that dictates the performance of the final composite structure. Here's a deep dive into the intricacies of laminate thickness variation and how it's managed in the filament winding process.
Laminate thickness in filament winding refers to the depth of the fiber layers that are applied to the mold. This thickness is not arbitrary; it is a calculated feature that directly influences the mechanical properties of the final product. The dimensionless radial coordinate of the fiber bundle centerline, denoted by β, and the dimensionless radius of the outer bundle edge, represented by ′β′, are crucial in determining the laminate thickness.
Several factors contribute to variations in laminate thickness during the winding process:
To manage and optimize laminate thickness, the following techniques are employed:
By understanding and controlling these factors, engineers can ensure that the laminate thickness is consistent, which is crucial for the structural integrity and performance of the final composite product. The decisions taken during the design stage have a significant impact on the quality of the resulting product, especially in terms of laminate coherence and thickness distribution.
Filament winding is a fabrication technique used extensively in the manufacturing of composite materials, particularly for creating items with a cylindrical shape such as pipes, tanks, and pressure vessels. The process involves winding filaments under tension over a rotating mandrel, which is then cured to form a rigid structure.
A pertinent example of filament winding can be found in the aerospace industry, where it is used to manufacture components such as rocket motor casings and fuselage sections for aircraft. In this context, the winding patterns are critical as they determine the directional strength characteristics of the final product. For instance, helical winding patterns are often employed to provide longitudinal strength, while hoop windings enhance the circumferential strength.
The example of aerospace components showcases the relevance of filament winding in industry practices. It highlights the importance of selecting appropriate winding patterns to meet specific strength requirements, which is crucial in applications where safety and performance are paramount. The technique's ability to produce lightweight yet strong structures is particularly valued in the aerospace sector, where reducing weight without compromising strength is a constant challenge.
For new researchers, this example underscores the importance of understanding the interplay between winding patterns and the mechanical properties of the final composite structure. It also emphasizes the need for precision in the winding process, as variations in tension or alignment can significantly affect the performance of the component. Additionally, researchers should note the following key points:
Filament winding is a prime example of how advanced manufacturing techniques are being applied to meet the stringent demands of modern industry. For researchers and practitioners alike, understanding the nuances of this process can lead to innovations that push the boundaries of material performance.
we recognize the pivotal role these elements play in the composites industry. Understanding the intricacies of winding patterns and the strategic placement of fibers is not just a matter of technical proficiency, but a cornerstone for innovation and advancement in the field.
Discover the future of composite manufacturing with Addcomposites! Here's how you can get involved:
At Addcomposites, we are dedicated to revolutionizing composite manufacturing. Our AFP systems and comprehensive support services are waiting for you to harness. So, don't wait – get started on your journey to the future of manufacturing today!
In the realm of composite materials, the intricacies of winding patterns and fiber stacking are not just minute details—they are pivotal elements that dictate the strength, durability, and overall performance of the final product. The blog delves into the heart of these techniques, unraveling the complexities and presenting them in a manner that both industry veterans and budding researchers can appreciate with the following key points
Filament winding is a fabrication process used to create composite materials with high strength-to-weight ratios. It involves winding filaments under tension over a rotating mandrel. The mandrel's shape dictates the final shape of the composite material, and the winding pattern determines the structural integrity and performance of the final product.
Winding patterns are crucial in filament winding as they affect the composite's mechanical properties and structural integrity. A suitable winding pattern ensures full and rotationally symmetric coverage, homogeneous thickness in the circumferential direction, and appropriate roving overlap according to the desired number of layers. The repetitive nature of the winding process means that each layer must be precisely placed adjacent to the previous one, with overlaps adjusted to achieve the desired laminate thickness and fiber volume fraction.
Fiber stacking, or the arrangement of fiber bundles in a composite, contributes significantly to the performance of the final product. The orientation and overlap of fibers affect the load distribution and the ability of the composite to withstand various stresses. For instance, a 50% overlap is preferred for two layers, while a 25% overlap is suitable for four layers, ensuring uniform thickness and strength across the composite.
The design process must consider the dimensions of the fiber bundle, as these will influence the winding pattern. The width and thickness of the fiber bundle, if not accounted for, can lead to inhomogeneities in the pattern and, consequently, in the structural performance of the composite.
The creation of winding patterns involves solving a first-order Diophantine equation, which is a relationship between integer numbers that governs the pattern. The equation takes into account the dimensions of the fiber bundle and the desired overlap, leading to an algorithm that can generate suitable patterns for a given set of parameters.
For example, the condition for full coverage at the equator of a wound body is given by the equation:
neq⋅beff=2π⋅R
where neq is the number of fiber bundles at the equator, beff is the effective width of the fiber bundle at the equator, and R is the radius of the body at the equator.
The basic theory of winding patterns and fiber stacking is a complex interplay of geometry, physics, and material science. The precise control of winding patterns and fiber stacking is essential in creating composites that meet specific performance criteria.
The filament winding process in composite material manufacturing relies heavily on the precision of winding patterns. These patterns are responsible for the distribution of fibers across the structure, directly influencing its mechanical properties and integrity. The algorithm for generating these patterns is a complex yet fascinating aspect of composite design, involving a blend of mathematics and material science.
The algorithm's primary goal is to create a winding pattern that ensures the optimal placement of fiber bundles, thereby achieving the desired structural integrity and performance. The process begins with the setting of input parameters, which are dictated by the scalar value of the winding angle, denoted as 'β'. This angle is independent and considered a control parameter, while the eccentricity value 'ε' and the fiber bundle thickness 't' are fixed.
To construct a suitable pattern, the algorithm considers 'β' as the main control parameter, with the dimensionless fiber bundle width 'B' associated with it. On the equatorial circumference, the fiber bundle occupies an arc corresponding to an angle 'Φβ', which is derived from the equation:
Φβ=B⋅cos(β)
This angle, in conjunction with 'ΦK(β)', determines the pattern parameters, which are initially real numbers. A perfect pattern is achieved when the Diophantine equations are satisfied for a particular 'β-value', meaning all involved products should be integers. However, this simultaneous satisfaction of conditions is generally not possible, necessitating a specialized strategy to identify potential solution intervals for 'β' and to select the best solutions to minimize undesired fiber bundle overlap.
The algorithm operates by localizing 'β-values' that provide integer numbers for 'p(β)', 'k(β)', and 'n(β)', which are points where the value of the stepped lines changes. These values, along with the bounds '[βmin, βmax]', define the intervals potentially containing a solution. The algorithm then identifies intervals containing a possible winding pattern by ensuring that the interval bounds satisfy a set of mathematical conditions.
Every interval that meets these conditions contains three integers that satisfy the Diophantine equation automatically for the assumed number of layers. The algorithm denotes the leading solution by '{p+, k+, dn+}' and the lagging one by '{p-, k-, dn-}'. The corresponding required 'ΦK-angles' can then be found by specific equations provided in the text.
Pattern pattern-generating algorithm is a critical component in the filament winding process, ensuring that the fiber bundles are placed accurately to achieve the desired structural properties. Its precision directly impacts the quality of the resulting product, particularly in terms of laminate coherence and thickness distribution.
In the realm of filament winding, the concept of laminate thickness is pivotal. It's not just a matter of layering fibers; it's about precision engineering that dictates the performance of the final composite structure. Here's a deep dive into the intricacies of laminate thickness variation and how it's managed in the filament winding process.
Laminate thickness in filament winding refers to the depth of the fiber layers that are applied to the mold. This thickness is not arbitrary; it is a calculated feature that directly influences the mechanical properties of the final product. The dimensionless radial coordinate of the fiber bundle centerline, denoted by β, and the dimensionless radius of the outer bundle edge, represented by ′β′, are crucial in determining the laminate thickness.
Several factors contribute to variations in laminate thickness during the winding process:
To manage and optimize laminate thickness, the following techniques are employed:
By understanding and controlling these factors, engineers can ensure that the laminate thickness is consistent, which is crucial for the structural integrity and performance of the final composite product. The decisions taken during the design stage have a significant impact on the quality of the resulting product, especially in terms of laminate coherence and thickness distribution.
Filament winding is a fabrication technique used extensively in the manufacturing of composite materials, particularly for creating items with a cylindrical shape such as pipes, tanks, and pressure vessels. The process involves winding filaments under tension over a rotating mandrel, which is then cured to form a rigid structure.
A pertinent example of filament winding can be found in the aerospace industry, where it is used to manufacture components such as rocket motor casings and fuselage sections for aircraft. In this context, the winding patterns are critical as they determine the directional strength characteristics of the final product. For instance, helical winding patterns are often employed to provide longitudinal strength, while hoop windings enhance the circumferential strength.
The example of aerospace components showcases the relevance of filament winding in industry practices. It highlights the importance of selecting appropriate winding patterns to meet specific strength requirements, which is crucial in applications where safety and performance are paramount. The technique's ability to produce lightweight yet strong structures is particularly valued in the aerospace sector, where reducing weight without compromising strength is a constant challenge.
For new researchers, this example underscores the importance of understanding the interplay between winding patterns and the mechanical properties of the final composite structure. It also emphasizes the need for precision in the winding process, as variations in tension or alignment can significantly affect the performance of the component. Additionally, researchers should note the following key points:
Filament winding is a prime example of how advanced manufacturing techniques are being applied to meet the stringent demands of modern industry. For researchers and practitioners alike, understanding the nuances of this process can lead to innovations that push the boundaries of material performance.
we recognize the pivotal role these elements play in the composites industry. Understanding the intricacies of winding patterns and the strategic placement of fibers is not just a matter of technical proficiency, but a cornerstone for innovation and advancement in the field.
Discover the future of composite manufacturing with Addcomposites! Here's how you can get involved:
At Addcomposites, we are dedicated to revolutionizing composite manufacturing. Our AFP systems and comprehensive support services are waiting for you to harness. So, don't wait – get started on your journey to the future of manufacturing today!