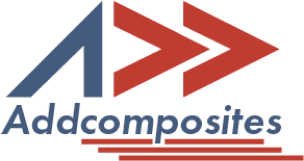
In the ever-evolving landscape of composite manufacturing, a groundbreaking fusion of technologies is set to redefine the boundaries of what's possible. Imagine a production system capable of weaving spacecraft components that are lighter than air yet stronger than steel. This isn't science fiction—it's the reality emerging from the integration of two game-changing technologies: Filament Winding and Automated Fiber Placement (AFP).
For years, these technologies have existed as separate entities, each with its own strengths and limitations. Filament winding has long been a cornerstone of composite manufacturing, particularly for axially symmetric hollow parts. Meanwhile, AFP systems brought new levels of precision and flexibility to the field. Now, with the advent of the AFP-XS system from Addcomposites, we're witnessing a technological convergence that promises to revolutionize composite manufacturing.
This blog post delves into the technical intricacies of this integration, exploring how it addresses the limitations of both technologies while opening up new possibilities for design and production. We'll examine the challenges overcome in merging these technologies, the resulting capabilities, and the implications for various industries, from aerospace to automotive.
As we pull back the curtain on this manufacturing revolution, prepare to challenge everything you thought you knew about composites manufacturing. Whether you're a seasoned industry professional or a curious enthusiast, this deep dive into the fusion of filament winding and AFP technologies promises to expand your understanding of what's possible in the world of advanced materials and manufacturing.
Let's embark on this technical journey, exploring the past, present, and future of composite manufacturing technology.
Filament winding has been a cornerstone of composite manufacturing for decades, particularly excelling in the production of axially symmetric hollow parts. This process involves winding continuous reinforcement fibers onto a rotating mandrel in a precise geometric pattern, creating strong, lightweight structures.
In filament winding, fibers are fed through a resin bath or are pre-impregnated with resin, then wound onto a rotating mandrel. The fiber delivery system moves along the length of the mandrel, precisely controlling the angle and position of the fibers. This process continues layer by layer until the desired thickness and strength are achieved.
Filament winding primarily consists of two methods:
Each method has its advantages in terms of cost-effectiveness, production volume, and part quality.
Filament winding offers several key strengths:
However, traditional filament winding also has limitations:
These limitations have historically restricted the application of filament winding to certain types of parts and industries, setting the stage for the development of more advanced technologies like AFP.
Automated Fiber Placement (AFP) represents a significant advancement in composite manufacturing technology, bringing new levels of precision and flexibility to the field. Developed to overcome some of the limitations of traditional filament winding, AFP has opened up new possibilities in composite part design and production.
AFP systems use a robotic arm or gantry to precisely place multiple pre-impregnated fiber tows or thermoset/thermoplastic tapes onto a mold or mandrel. The system can cut, restart, and precisely position these narrow strips of composite material, allowing for the creation of complex geometries and structures.
Key components of an AFP system typically include:
AFP technology offers several significant advantages:
Despite its advanced capabilities, AFP also has some limitations:
These strengths and limitations have positioned AFP as a powerful technology for producing complex, high-performance composite parts, particularly in industries like aerospace where precision and design flexibility are crucial.
The AFP-XS system from Addcomposites represents a significant leap forward in composite manufacturing technology, seamlessly integrating the capabilities of filament winding and Automated Fiber Placement (AFP). This fusion addresses the limitations of both technologies while combining their strengths, opening up new possibilities in composite part design and production.
The AFP-XS system is a ground-up redesign that considers both AFP and filament winding processes as part of a single, cohesive unit. This integration is achieved through:
This holistic approach allows for seamless transitions between AFP and filament winding processes, enabling the production of complex parts that were previously impossible or impractical to manufacture.
The integration of these technologies in the AFP-XS system offers several key advantages:
The AFP-XS system introduces several process improvements:
These features and improvements make the AFP-XS system a powerful tool for producing complex, high-performance composite parts across various industries, from aerospace and automotive to marine and energy.
The integration of filament winding and AFP technologies in the AFP-XS system opens up a wide range of new possibilities in composite manufacturing. This section explores some of the key applications and industry-specific use cases that showcase the potential of this revolutionary technology.
The AFP-XS system enables the production of previously unattainable or impractical structures:
The versatility of the AFP-XS system is also enabling new applications in emerging fields:
The AFP-XS system also contributes to more sustainable manufacturing practices:
The AFP-XS system's integration of filament winding and AFP technologies yields several significant technical advantages. These advancements not only enhance the manufacturing process but also expand the possibilities for composite part design and production.
One of the most notable features of the AFP-XS system is its ability to adapt in real-time between high-speed winding and precise placement:
The AFP-XS system offers unprecedented control over fiber placement and tension:
The AFP-XS system's versatility extends to its ability to work with a wide range of materials:
The AFP-XS system incorporates advanced quality control measures directly into the manufacturing process:
The AFP-XS system embraces the principles of Industry 4.0, offering complete digital integration throughout the manufacturing process:
Despite its advanced capabilities, the AFP-XS system is designed for accessibility and ease of integration:
As we look to the future, the integration of filament winding and AFP technologies in systems like the AFP-XS opens up exciting possibilities for further advancement in composite manufacturing. This section explores some of the emerging trends and potential developments that could shape the future of this technology.
The flexibility of the AFP-XS system sets the stage for the creation of highly optimized structures:
Future developments may see the AFP-XS system creating parts that go beyond structural functions:
The AFP-XS system is poised to become even more intelligent and adaptive:
Sustainability will likely play an increasingly important role in future developments:
As the technology advances, we can expect to see it applied in new and unexpected ways:
The future may see the AFP-XS system integrated with other cutting-edge technologies:
As we've explored throughout this blog, the integration of filament winding and Automated Fiber Placement (AFP) technologies, exemplified by systems like the AFP-XS, represents a significant leap forward in composite manufacturing. This fusion of technologies is not merely an incremental improvement, but a transformative approach that is reshaping the landscape of advanced materials production.
The integration of filament winding and AFP technologies represents more than just a new manufacturing method; it's a paradigm shift in how we approach the design and production of composite structures. As this technology matures and becomes more widely adopted, we can expect to see increasingly sophisticated, efficient, and sustainable composite products entering the market.
The journey of composite manufacturing, from traditional hand layup to today's integrated, AI-assisted systems, is a testament to human ingenuity and the relentless pursuit of technological advancement. As we look to the future, it's clear that the integration of filament winding and AFP is not the end point of this journey, but rather a springboard for even more exciting innovations to come.
The composite manufacturing revolution is here, and it's transforming our world, one fiber at a time.
Discover the future of composite manufacturing with Addcomposites! Here's how you can get involved:
At Addcomposites, we are dedicated to revolutionizing composite manufacturing. Our AFP systems and comprehensive support services are waiting for you to harness. So, don't wait – get started on your journey to the future of manufacturing today!