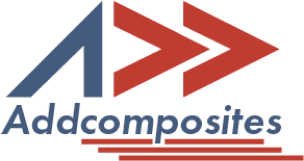
Production of hydrogen tanks has been done using wet/dry filament winding for many decades now. This article focuses on describing the filament winding with the Wet and Towpreg approach. Highlighting the benefits of each process. Towards the conclusion, the article directs toward the complete course for Design and Development of Compressed Hydrogen Storage Tanks.
Filament winding is a technique primarily used to manufacture hollow, circular, or prismatic parts such as pipes and tanks. It is performed by winding continuous fiber tows onto a rotating mandrel using a specialized winding machine. Filament wound parts are commonly used in the aerospace, energy, and consumer product industries.
Figure 1. Filament Wound Parts (Source: Lentus Composites)
Continuous fiber tows are fed through a fiber delivery system to the filament winding machine, where they are wound onto a mandrel in a predetermined, repeating geometric pattern. The tow location is guided by a fiber delivery head, which is attached to a movable carriage on the filament winding machine. The relative angle of the tow to the mandrel axis, called the winding angle, can be tailored to provide strength and stiffness in the desired directions. When sufficient layers of tow have been applied, the resulting laminate is cured on the mandrel. The overall size and shape of the finished part are determined by the mandrel shape and thickness of the laminate.
Video 1. SM+ Filament Winder Commissioning Video (Source: Engineering Technology Corporation)
The winding angles will determine the mechanical properties of the composite part, such as strength, stiffness, and weight. The density of the laminate is the result of the tension of the tows during winding. The composite parts made through these methods generally have good strength-to-weight properties.
The towpreg winding uses a fiber tow that is pre-impregnated with resin (prepreg). It is ideal for making cylindrical and/or hemispheric components. Towpreg material generally has a high filament count, making it a good choice for automotive parts, which require robust mechanical performance at a low cost.
Due to its fast speed, it is suitable for large-scale production with applications in several industries, providing products with high fiber content (usually over 60%) and excellent mechanical properties. Winding is particularly suitable for producing axially asymmetrical shapes, as in the case of tanks.
Resin impregnation in the filament can be performed at different stages of the manufacturing process using different techniques. In the wet wrapping method, perhaps the most common, the dry bundle is coated with a molten resin before it comes into contact with the mandrel by resin immersion.
Addcomposites now offers the tape and filament winding capability for the AFP system that can work across the material line from Dry Fiber, Thermoset, and Thermoplastic. (Learn more >)
The above article is part of the course Design and Development of Compressed Hydrogen Storage Tanks. The course covers a lot more, starting with discussing challenges in material selection and manufacturing practices, as well as cutting-edge trends being explored. Key problems in the design and analysis of the hydrogen reservoir are also addressed. Finally, testing and certification requirements are discussed as they play an important role in industry acceptance.
Production of hydrogen tanks has been done using wet/dry filament winding for many decades now. This article focuses on describing the filament winding with the Wet and Towpreg approach. Highlighting the benefits of each process. Towards the conclusion, the article directs toward the complete course for Design and Development of Compressed Hydrogen Storage Tanks.
Filament winding is a technique primarily used to manufacture hollow, circular, or prismatic parts such as pipes and tanks. It is performed by winding continuous fiber tows onto a rotating mandrel using a specialized winding machine. Filament wound parts are commonly used in the aerospace, energy, and consumer product industries.
Figure 1. Filament Wound Parts (Source: Lentus Composites)
Continuous fiber tows are fed through a fiber delivery system to the filament winding machine, where they are wound onto a mandrel in a predetermined, repeating geometric pattern. The tow location is guided by a fiber delivery head, which is attached to a movable carriage on the filament winding machine. The relative angle of the tow to the mandrel axis, called the winding angle, can be tailored to provide strength and stiffness in the desired directions. When sufficient layers of tow have been applied, the resulting laminate is cured on the mandrel. The overall size and shape of the finished part are determined by the mandrel shape and thickness of the laminate.
Video 1. SM+ Filament Winder Commissioning Video (Source: Engineering Technology Corporation)
The winding angles will determine the mechanical properties of the composite part, such as strength, stiffness, and weight. The density of the laminate is the result of the tension of the tows during winding. The composite parts made through these methods generally have good strength-to-weight properties.
The towpreg winding uses a fiber tow that is pre-impregnated with resin (prepreg). It is ideal for making cylindrical and/or hemispheric components. Towpreg material generally has a high filament count, making it a good choice for automotive parts, which require robust mechanical performance at a low cost.
Due to its fast speed, it is suitable for large-scale production with applications in several industries, providing products with high fiber content (usually over 60%) and excellent mechanical properties. Winding is particularly suitable for producing axially asymmetrical shapes, as in the case of tanks.
Resin impregnation in the filament can be performed at different stages of the manufacturing process using different techniques. In the wet wrapping method, perhaps the most common, the dry bundle is coated with a molten resin before it comes into contact with the mandrel by resin immersion.
Addcomposites now offers the tape and filament winding capability for the AFP system that can work across the material line from Dry Fiber, Thermoset, and Thermoplastic. (Learn more >)
The above article is part of the course Design and Development of Compressed Hydrogen Storage Tanks. The course covers a lot more, starting with discussing challenges in material selection and manufacturing practices, as well as cutting-edge trends being explored. Key problems in the design and analysis of the hydrogen reservoir are also addressed. Finally, testing and certification requirements are discussed as they play an important role in industry acceptance.