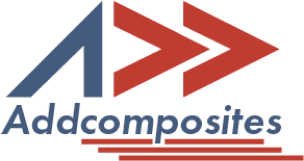
In the video 1/4'' thermoset tape is placed on a straight 0.9m long pass. All 20 layers are placed within the specified tolerances while cutting the tape on the fly.
One of the main sub-processes of AFP is cutting the fiber repeatably and consistently. This process involves fiber stabilization and shearing, repeated over thousands of times without error. In the all-new AFP-XS, the key mechanical innovation is the blades chemistry and their associated hardening processes. This enables very tough and wear-resistant cutting edges, improving cutter reliability by up to 500%, without deformation or reduction in cutting ability!
After continuous operation and thousands of cuts, the blades will become blunt and resin will become built up, resulting in a cut failure. The latest AFP-XS includes a clever sensor suite that detects whether or not a failure has occurred during operation, which then pauses the machine for operator attention. This has the potential to reduce scrap after many hours of layup work and material deposition, while simultaneously easing the operators' work during layup!
In previous models of the AFP-XS, the machine used to require a pause during the cutting process, resulting in considerably slower layup speeds. In order to increase operational speeds, the cutting action components have been packed tighter and streamlined, resulting in faster reaction time. This enables smoother and faster layups, while eliminating the hotspots and extra compaction caused during the pause required by the cutting process!
During the AFP process, the material must remain under constant tension all the way from the spool through deposition; all while collecting the backing tape, stabilizing and cutting the fiber, and restarting the individual passes - all at variable speeds. With the new model, the system eliminates unnecessary complexity while utilizing sensors and dynamic mechanisms to achieve the No-Lag Tension Control System. This enables the AFP-XS to run at speeds of over 1 m/s, while maintaining the aerospace-grade lateral fiber positioning accuracy of -0/ +2 mm.
At the early stage of adopting Automated Fiber Placement, there is a lot of uncertainty of configurations to work or choose. The AFP-XS offers the most modular system for the end-user, where the following option combinations are available to choose from:
a. Fiber tape widths
i. 1/4''ii. 1/2''iii. 1''iv. Custom widths ≤1''
b. Fiber tape matrix
i. Thermoset
ii. Thermoplastic
c. Heating options
i. IR heater
ii. humm3® from Heraeus
iii. Laser
iv. Hot Gas
v. Hot Air
d. Robots
i. KUKA
ii. FANUC
iii. ABB
A complete cell with all the bells and whistles might not make sense for some short-term projects, as the value of the project may not justify the process. In these instances, it is recommended to "Just Start" with AFP through the rental program offered for the AFP-XS. Read more about our take on the benefits of renting the system here. This drastically lowers the risk and qualifies you for a discount on the final purchase once the system is evaluated!
All these technological innovations have lead to the fastest, most reliable, and easy to use AFP-XS we've introduced. Reach out to info@addcomposites.com to learn how you can implement this system into your production!
In the video 1/4'' thermoset tape is placed on a straight 0.9m long pass. All 20 layers are placed within the specified tolerances while cutting the tape on the fly.
One of the main sub-processes of AFP is cutting the fiber repeatably and consistently. This process involves fiber stabilization and shearing, repeated over thousands of times without error. In the all-new AFP-XS, the key mechanical innovation is the blades chemistry and their associated hardening processes. This enables very tough and wear-resistant cutting edges, improving cutter reliability by up to 500%, without deformation or reduction in cutting ability!
After continuous operation and thousands of cuts, the blades will become blunt and resin will become built up, resulting in a cut failure. The latest AFP-XS includes a clever sensor suite that detects whether or not a failure has occurred during operation, which then pauses the machine for operator attention. This has the potential to reduce scrap after many hours of layup work and material deposition, while simultaneously easing the operators' work during layup!
In previous models of the AFP-XS, the machine used to require a pause during the cutting process, resulting in considerably slower layup speeds. In order to increase operational speeds, the cutting action components have been packed tighter and streamlined, resulting in faster reaction time. This enables smoother and faster layups, while eliminating the hotspots and extra compaction caused during the pause required by the cutting process!
During the AFP process, the material must remain under constant tension all the way from the spool through deposition; all while collecting the backing tape, stabilizing and cutting the fiber, and restarting the individual passes - all at variable speeds. With the new model, the system eliminates unnecessary complexity while utilizing sensors and dynamic mechanisms to achieve the No-Lag Tension Control System. This enables the AFP-XS to run at speeds of over 1 m/s, while maintaining the aerospace-grade lateral fiber positioning accuracy of -0/ +2 mm.
At the early stage of adopting Automated Fiber Placement, there is a lot of uncertainty of configurations to work or choose. The AFP-XS offers the most modular system for the end-user, where the following option combinations are available to choose from:
a. Fiber tape widths
i. 1/4''ii. 1/2''iii. 1''iv. Custom widths ≤1''
b. Fiber tape matrix
i. Thermoset
ii. Thermoplastic
c. Heating options
i. IR heater
ii. humm3® from Heraeus
iii. Laser
iv. Hot Gas
v. Hot Air
d. Robots
i. KUKA
ii. FANUC
iii. ABB
A complete cell with all the bells and whistles might not make sense for some short-term projects, as the value of the project may not justify the process. In these instances, it is recommended to "Just Start" with AFP through the rental program offered for the AFP-XS. Read more about our take on the benefits of renting the system here. This drastically lowers the risk and qualifies you for a discount on the final purchase once the system is evaluated!
All these technological innovations have lead to the fastest, most reliable, and easy to use AFP-XS we've introduced. Reach out to info@addcomposites.com to learn how you can implement this system into your production!