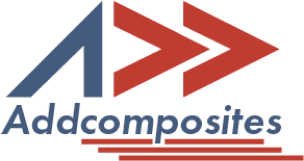
The electric vertical takeoff and landing (eVTOL) aircraft market is poised for remarkable growth in the coming years, transforming urban air mobility and revolutionizing transportation as we know it. This report delves into the current state of eVTOL manufacturing, exploring the key trends, challenges, and opportunities shaping this burgeoning industry. It examines the crucial role of advanced materials like composites and cutting-edge manufacturing techniques such as additive manufacturing in driving innovation and enabling the mass production of these revolutionary aircraft.
The eVTOL market is experiencing a surge in interest and investment, driven by the promise of efficient, sustainable, and convenient air travel. In 2020, the global eVTOL aircraft market size was valued at USD 1.11 billion 1. Furthermore, North America dominated the market with a 38.74% share 1, and the commercial segment is expected to lead the market in the forecast period 1. Market research indicates significant expansion in the coming years:
These figures highlight the immense potential of the eVTOL market and the increasing demand for these innovative aircraft. Advancements in battery technology are not merely incremental improvements; they are fundamental to the viability and future of the eVTOL market, directly impacting flight time, payload capacity, and ultimately, the commercial success of these aircraft 3.
The future of eVTOL manufacturing lies in the continued integration of advanced technologies and materials. Some key trends shaping the industry include:
These advancements will further enhance the performance, efficiency, and sustainability of eVTOLs, driving the growth of the market and accelerating the adoption of urban air mobility.
eVTOLs are not just a futuristic concept; they have the potential to become an integral part of public transportation systems. Their ability to take off and land vertically eliminates the need for long runways, allowing them to operate in urban environments with limited space 8. This opens up new possibilities for urban air mobility (UAM), offering a solution to traffic congestion and enhancing connectivity within cities and between urban and rural areas 9.
eVTOLs can be utilized for various public transportation applications:
Furthermore, beyond passenger transportation, eVTOLs hold the key to revolutionizing logistics, offering a faster, more flexible, and potentially more sustainable alternative to traditional ground-based delivery methods, particularly in congested urban environments and for time-sensitive goods 8.
By integrating eVTOLs into public transportation networks, cities can alleviate traffic congestion, reduce commute times, and improve overall transportation efficiency.
One of the key challenges in eVTOL manufacturing is achieving lightweight structures while maintaining structural integrity and safety. Composites, with their high strength-to-weight ratio and design flexibility, have emerged as the material of choice for eVTOL construction 13. The composites industry is experiencing a shift towards thermoplastics, necessitating a reevaluation of the supply chain to meet the demand for larger thermoplastic structures in eVTOL manufacturing 14.
Composites offer several advantages for eVTOL manufacturing:
Specific composite materials are being employed for different eVTOL components. For instance, toughened epoxy resins with intermediate modulus fibers are used for critical structural applications, while high-temperature thermoplastic resins with fibers are suitable for rotor blades and interiors 13. The use of composites is crucial for optimizing the performance and efficiency of eVTOLs, making them a viable and sustainable mode of transportation.
The pursuit of lightweighting in eVTOL design is intrinsically linked to the adoption of advanced manufacturing techniques. These technologies provide the necessary tools to fabricate complex composite structures with optimized material usage, achieving the weight reductions crucial for eVTOL performance and efficiency 13.
Additive manufacturing (AM), also known as 3D printing, is revolutionizing eVTOL manufacturing by enabling the creation of complex, lightweight components with increased efficiency and reduced waste 17. AM technologies like automated fiber placement (AFP), continuous fiber printing, and direct metal laser sintering (DMLS) are being employed to produce various eVTOL parts, including:
AM offers several benefits for eVTOL manufacturing:
Moreover, software advancements, such as Arevo's software, are simplifying composite design for non-experts, further facilitating the adoption of AM in eVTOL manufacturing 17. By leveraging AM technologies, eVTOL manufacturers can achieve significant improvements in production efficiency, cost-effectiveness, and design optimization.
This section provides a more in-depth look at specific advanced additive manufacturing techniques used in eVTOL production:
These advanced AM techniques offer a range of capabilities for producing high-performance, lightweight components, contributing to the overall efficiency and sustainability of eVTOL aircraft.
While the eVTOL market shows immense promise, manufacturers face several challenges in scaling up production to meet the anticipated demand:
Automation is not just a desirable feature in eVTOL manufacturing; it's a necessity for achieving the economies of scale required to meet the anticipated demand and make these aircraft commercially viable 7. Addressing these challenges through technological advancements, workforce development, and strategic investment will be crucial for the successful growth of the eVTOL industry.
eVTOL aircraft utilize various propulsion systems to achieve vertical takeoff and landing, as well as efficient forward flight. One common approach is the use of variable pitch propellers, which allow for adjustments in blade angle to optimize thrust and efficiency during different flight phases 22. This technology enables eVTOLs to transition smoothly from vertical takeoff to horizontal flight and achieve optimal performance in various operating conditions.
However, the use of multiple propellers in close proximity, particularly in configurations with side-by-side rotors, can create aerodynamic interactions that affect performance and stability. These interactions can lead to complex flow patterns, increased noise levels, and potential control challenges 23. Understanding and mitigating these aerodynamic effects through careful design and optimization of propeller placement and control systems are crucial for ensuring the safe and efficient operation of eVTOL aircraft.
Developing eVTOL aircraft involves a complex interplay of various engineering disciplines, including aerodynamics, structural design, propulsion systems, and control systems. To manage this complexity and ensure a successful design process, many eVTOL manufacturers are adopting model-based systems engineering (MBSE) approaches. MBSE tools, such as Zuken Vitech's GENESYS, provide a digital environment for modeling, simulating, and analyzing the entire aircraft system throughout its lifecycle 8. This approach facilitates collaboration among different engineering teams, enables early identification and resolution of design issues, and improves overall system integration and optimization.
Several eVTOL manufacturers are already implementing composites and additive manufacturing in their production processes:
These case studies demonstrate the successful application of composites and AM in eVTOL manufacturing, paving the way for wider adoption and further innovation in the industry. Notably, while some companies aim for commercial operation by 2025, challenges in the certification process may lead to delays 26.
Sustainability is a growing concern in the eVTOL industry, with manufacturers actively seeking ways to minimize the environmental impact of their production processes. One notable example is Boeing's partnership with ELG Carbon Fibre (now Gen 2 Carbon) to recycle carbon fiber from their factories 27. This initiative involves collecting scrap carbon fiber material and treating it in a furnace to remove the binding polymer, resulting in a clean material that can be reused. This recycling program is in action at 11 Boeing sites, contributing to their goal of reducing solid waste to landfill by 20% by 2025 27.
The eVTOL industry is poised for transformative growth, driven by advancements in electric propulsion, lightweight materials, and innovative manufacturing technologies. This report has explored the key trends shaping eVTOL manufacturing, highlighting the crucial role of composites and additive manufacturing in achieving lightweight, high-performance aircraft. The industry faces challenges in scaling up production and navigating complex certification processes, but the potential benefits of eVTOLs for urban air mobility, logistics, and sustainability are significant. Continued innovation in materials, manufacturing techniques, and systems engineering will be essential for the successful development and widespread adoption of these revolutionary aircraft.