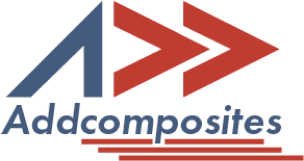
The transportation and aerospace industries are witnessing a revolutionary shift towards more efficient and lightweight storage solutions. At the forefront of this evolution are linerless composite pressure vessels, also known as Type V pressure vessels, which represent the next generation of storage technology. These advanced structures are gaining significant traction, particularly in low-pressure cryogenic storage applications, where their superior storage volume and reduced dry weight characteristics make them increasingly attractive.
The journey from concept to production of these sophisticated vessels presents a fascinating intersection of materials science, manufacturing technology, and advanced simulation. While traditional Automated Fiber Placement (AFP) has been a cornerstone in composite manufacturing, the unique challenges of linerless vessels demand an even more refined approach. The absence of an internal liner – a feature that distinguishes Type V vessels from their Type III and Type IV counterparts – introduces both opportunities and complexities in the manufacturing process.
Manufacturing these vessels requires navigating several critical challenges:
Beyond manufacturing, the operational requirements add another layer of complexity. These vessels must maintain their structural integrity under severe operating conditions, particularly at cryogenic temperatures. The interplay between manufacturing decisions and operational performance becomes crucial, as thermal stresses and material behavior at extreme temperatures significantly impact the vessel's long-term reliability.
The industry has reached a pivotal point where traditional manufacturing approaches are being enhanced by advanced simulation capabilities. Path planning and simulation platforms have become essential tools in predicting and optimizing manufacturing outcomes. This evolution has sparked an interesting debate in the industry regarding the optimal manufacturing method, particularly when comparing AFP versus filament winding for specific applications like hydrogen tanks.
Understanding the complete manufacturing process, from initial layup to final testing, requires a holistic view that encompasses both the theoretical foundations and practical considerations. The Overview of Automated Fiber Placement Process provides crucial insights into how modern manufacturing techniques are evolving to meet these challenges.
In this comprehensive exploration, we'll dive deep into the technical challenges, manufacturing considerations, and innovative solutions that are shaping the future of linerless composite pressure vessels. We'll examine how end-to-end simulation, combined with advanced manufacturing techniques, is revolutionizing the way these critical components are designed, produced, and validated for real-world applications.
The development of linerless composite pressure vessels introduces a complex web of technical challenges that span both manufacturing and operational considerations. Unlike their predecessors, Type V vessels eliminate the internal liner structure, creating a paradigm shift in how these critical components are manufactured and validated.
The absence of an internal liner fundamentally changes the manufacturing approach. Traditional composite pressure vessels rely on internal liner structures (metallic or polymeric) that serve dual purposes: as part of the vessel structure and as a molding surface for composite material deposition. In linerless vessels, this absence necessitates innovative solutions in composite design for automated production.
Material deposition presents its own set of challenges. While automated fiber placement has emerged as a leading solution, the process requires precise control over multiple parameters:
Recent studies have shown that residual stresses from manufacturing can reach up to 50% of the composite ply's transverse strength - a significant factor that directly impacts vessel performance. This finding underscores the critical importance of understanding tension and compaction in AFP.
The operational environment introduces another layer of complexity, particularly in cryogenic applications. The material behavior at extreme temperatures creates several critical considerations:
Temperature-induced stresses emerge from two primary sources:
These thermal effects can trigger micro-cracking at strain levels significantly below the fiber failure strain, potentially leading to premature leakage. The impact of crystallinity in automated fiber placement becomes particularly relevant here, as it affects both manufacturing quality and operational performance.
Perhaps one of the most significant challenges lies in ensuring consistent quality throughout the manufacturing process. The industry has evolved toward AI-driven defect detection systems, but several critical aspects require continuous monitoring:
Research has demonstrated that damage prediction requires understanding both manufacturing-induced stresses and operational loads. Thermal stresses developed during cooling to cryogenic conditions can reach the composite ply strength, potentially triggering matrix cracks before operational loading even begins.
The complexity of these vessels demands sophisticated simulation approaches. Traditional design methods often fall short in predicting:
Modern digital twin approaches for composite parts manufacturing are becoming essential tools in addressing these challenges, enabling manufacturers to predict and optimize outcomes before physical production begins.
The interplay between these various challenges necessitates an integrated approach to vessel design and manufacturing. Success requires not just addressing each challenge individually, but understanding their complex interactions and implementing solutions that optimize the entire manufacturing process while ensuring operational reliability.
Advanced simulation has evolved from a useful tool to an essential component in the design and manufacturing of linerless composite pressure vessels. The complexity of these structures, combined with the critical nature of their applications, demands a comprehensive understanding of their behavior throughout their entire lifecycle – from manufacturing to operational conditions.
Modern path planning and simulation platforms have revolutionized how we approach composite vessel design. Unlike traditional methods that often treated manufacturing and operational simulations separately, current best practices advocate for an end-to-end simulation strategy that encompasses:
This holistic approach has revealed critical insights. For instance, recent studies demonstrate that residual stresses from manufacturing can achieve values near 50% of the composite ply's transverse strength – a finding that significantly impacts design decisions and performance predictions.
The simulation of the manufacturing process has become increasingly sophisticated, particularly in automated fiber placement processes. Key aspects include:
Geometric Modeling:
Recent advancements in machine learning and computer vision have enhanced our ability to simulate and optimize these aspects in real-time, leading to improved manufacturing outcomes.
The simulation of thermal effects presents unique challenges, particularly for cryogenic applications. Advanced models now incorporate:
Temperature-dependent material properties across operating ranges:
These models have revealed that thermal stresses during cooling to cryogenic conditions can trigger transverse damage before pressure loading begins – a critical consideration for design optimization.
Modern simulation tools excel in predicting damage evolution through multiple mechanisms. The implementation of AI in automated fiber placement has enhanced our ability to:
The concept of digital twins for composite manufacturing has gained significant traction. These virtual representations provide:
Research indicates that integrating digital twin technology with advanced iso-contour path planning can enhance manufacturing precision while reducing defects.
Simulation results require careful validation against experimental data. Modern approaches combine:
The correlation between simulated predictions and experimental results has shown remarkable improvement through strategic data use in AFP manufacturing.
As simulation capabilities continue to evolve, we're seeing increased integration of:
The future points toward even more sophisticated autonomous systems streamlining automated fiber composite manufacturing, where simulation plays a central role in decision-making processes.
This comprehensive simulation approach not only improves design accuracy but also reduces development time and costs. By identifying potential issues before physical manufacturing begins, engineers can optimize designs and manufacturing parameters more effectively, leading to higher quality products with improved reliability.
The manufacturing of linerless composite pressure vessels represents a convergence of advanced materials science, precise process control, and sophisticated automation. Understanding and controlling these elements is crucial for producing reliable, high-performance vessels that meet stringent industry requirements.
Material selection forms the foundation of successful vessel manufacturing. The choice of materials must balance multiple factors:
Performance Requirements:
Recent developments in thermoplastic composites manufacturing have expanded material options, particularly for cryogenic applications. The understanding of crystallinity in these materials has become crucial for optimizing manufacturing parameters.
The evolution of automated fiber placement technology has revolutionized how we approach vessel manufacturing. Key considerations include:
Research has shown that tension and compaction control significantly influence final part quality. These parameters must be carefully balanced to achieve optimal results.
Modern manufacturing approaches incorporate real-time quality control measures. This includes:
In-Process Monitoring:
The integration of AI-driven defect detection systems has significantly enhanced our ability to identify and correct issues during manufacturing.
Temperature control during manufacturing proves critical for several reasons:
Recent studies in in-situ consolidation have demonstrated the importance of precise thermal management throughout the manufacturing process.
The manufacturing of linerless vessels often involves multiple stages of assembly and integration. Critical aspects include:
The design for automated production must consider these assembly requirements from the earliest stages of planning.
Manufacturing documentation and validation have become increasingly sophisticated, incorporating:
Modern manufacturing approaches must also address sustainability in composites manufacturing, including:
The industry trend toward waste tracking and reduction has led to more efficient manufacturing processes and improved resource utilization.
The design of the manufacturing cell itself requires careful consideration of:
Modern hybrid manufacturing cells integrate multiple processes while maintaining precise control over all manufacturing parameters.
These manufacturing considerations represent a complex interplay of factors that must be carefully balanced to produce high-quality linerless pressure vessels. Success requires not only understanding each element individually but also comprehending their interactions and impacts on the final product quality.
The complexities of linerless pressure vessel manufacturing demand comprehensive solutions that address both technical challenges and practical implementation needs. Addcomposites has developed an integrated ecosystem of hardware, software, and support services specifically designed to meet these demands.
At the core of Addcomposites' offering are two flagship automated fiber placement systems:
The AFP-XS System:
The AFP-X System:
Addcomposites' software suite addresses the entire manufacturing workflow:
AddPath Software:
AddPrint Software:
The AddCell integration package provides comprehensive manufacturing cell solutions:
Safety and Control:
Thermal management options include:
Addcomposites provides a complete range of manufacturing accessories:
Process Optimization Tools:
Quality Control Components:
Addcomposites' solutions are tailored for various sectors:
Comprehensive support services include:
What sets Addcomposites apart:
The integrated nature of Addcomposites' solutions ensures that manufacturers can address the full spectrum of challenges in linerless pressure vessel production, from initial design through final validation. This comprehensive approach, combined with ongoing support and training, enables organizations to achieve optimal results in their composite manufacturing operations.
Recent research into linerless composite pressure vessels has revealed crucial insights about the relationship between manufacturing parameters and vessel performance. Through comprehensive end-to-end simulation and experimental validation, we can now better understand how manufacturing decisions influence structural integrity and operational reliability.
The manufacturing process introduces significant residual stresses that profoundly affect vessel performance. Recent studies have demonstrated that these manufacturing-induced stresses can reach up to 50% of the composite ply's transverse strength - a finding that fundamentally changes how we approach vessel design and manufacturing. As discussed in Understanding Tension and Compaction in AFP, these residual stresses play a crucial role in determining the vessel's ultimate performance capabilities.
When examining the cylindrical region of pressure vessels, researchers found that residual stresses increase failure criteria values by approximately 30%, pushing them from 0.3 to 0.7 in standard testing conditions. This significant impact underscores the importance of process monitoring and control during manufacturing.
Temperature management during manufacturing and operation presents a particularly complex challenge. Through detailed analysis of cryogenic applications, researchers identified that cooling to operational temperatures can trigger transverse damage even before pressure loading begins. This phenomenon occurs due to the accumulation of thermal stresses on top of existing manufacturing residual stresses.
The study revealed three critical temperature-related phases that influence vessel integrity:
Initial Manufacturing Phase: During this stage, curing-induced stresses develop and become locked into the structure. These stresses are particularly significant in the transverse direction, where they can reach approximately 21 MPa in standard configurations.
Cooling Phase: As the vessel cools to cryogenic temperatures (-196°C), additional thermal stresses develop. The research showed that these stresses can push the material beyond its transverse strength limit, leading to potential micro-cracking before operational loads are even applied.
Operational Phase: During actual service, the combination of thermal and pressure-induced stresses creates a complex loading scenario. Advanced simulation techniques have shown that understanding this interaction is crucial for accurate performance prediction.
The study examined pressure loading effects under both room temperature and cryogenic conditions. At room temperature, transverse damage initiation typically occurs between 15 and 25 bar of pressure, with full propagation through the thickness achieved around 25 bar. This finding aligns with experimental results showing leakage failure at approximately 26 bar.
The introduction of advanced path planning strategies has shown potential for optimizing fiber placement to better handle these pressure loads. The research demonstrated that proper fiber orientation and layup sequence could significantly influence the vessel's pressure-bearing capacity.
One of the most significant findings relates to the accuracy of performance predictions when incorporating manufacturing effects. Traditional analysis approaches that neglected manufacturing residual stresses consistently overestimated vessel performance by approximately 40%. This highlights the critical importance of end-to-end simulation approaches that account for the complete manufacturing history.
The research validated these findings through extensive testing, demonstrating that data-driven optimization can significantly improve prediction accuracy. By incorporating manufacturing parameters into the analysis, engineers can now better predict:
These findings have profound implications for future vessel design and manufacturing approaches. The research clearly demonstrates that achieving optimal performance requires careful consideration of the entire manufacturing process, not just the final design parameters. This has led to the development of new concepts for consolidation and manufacturing techniques.
The integration of AI and machine learning into the manufacturing process has shown particular promise in addressing these challenges. By continuously monitoring and adjusting manufacturing parameters, these systems can help minimize residual stress development while optimizing structural performance.
This case study underscores the critical importance of understanding and controlling manufacturing parameters in linerless pressure vessel production. It demonstrates that achieving optimal performance requires a holistic approach that considers the entire manufacturing process as an integral part of the design specification.
The landscape of composite pressure vessel manufacturing stands at a fascinating crossroads where traditional manufacturing wisdom meets cutting-edge technology. As we look toward the future, several key developments are reshaping how we approach the design and production of these critical components.
The integration of artificial intelligence into composite manufacturing represents perhaps the most significant shift in recent years. Advanced machine learning approaches are transforming how we handle process optimization and quality control. These systems are moving beyond simple pattern recognition to become truly predictive tools that can anticipate and prevent manufacturing issues before they occur.
The evolution of autonomous manufacturing systems represents a particularly promising development. These systems combine real-time monitoring with adaptive control, creating manufacturing cells that can self-optimize based on continuous feedback. This capability is especially crucial for linerless pressure vessels, where maintaining consistent quality throughout the manufacturing process directly impacts vessel performance.
Advancements in material science are opening new possibilities for pressure vessel design and manufacturing. The development of next-generation thermoplastic composites, particularly for cryogenic applications, is reshaping our understanding of what's possible in terms of performance and manufacturing efficiency. Research into crystallinity control in thermoplastic composites is yielding promising results for improving both manufacturing processes and final product performance.
Sustainability considerations are also driving material innovation. The industry is witnessing increased focus on sustainable manufacturing approaches, including the development of recyclable composites and manufacturing processes that minimize waste. This shift toward sustainability isn't just environmentally responsible – it's becoming a crucial factor in maintaining competitiveness in the global market.
The concept of digital manufacturing is evolving beyond basic automation to encompass entire manufacturing ecosystems. Digital twin technology is becoming increasingly sophisticated, enabling real-time monitoring and optimization of manufacturing processes. These digital representations are proving invaluable for predicting and preventing potential issues before they impact production.
The integration of various manufacturing technologies is creating new possibilities for hybrid manufacturing approaches. We're seeing promising developments in combining traditional automated fiber placement with innovative techniques like continuous fiber 3D printing. These hybrid approaches offer unprecedented flexibility in design and manufacturing while maintaining the high performance standards required for pressure vessel applications.
Advanced process control systems are evolving to handle increasingly complex manufacturing scenarios. The development of sophisticated path planning algorithms is enabling more efficient material deposition while ensuring optimal fiber orientation for structural performance. These systems are becoming more adaptive, capable of real-time adjustments based on manufacturing conditions and quality requirements.
Quality control methodologies are also advancing significantly. In-situ monitoring systems are becoming more sophisticated, combining multiple sensor types with advanced analytics to provide comprehensive quality assessment during manufacturing. This evolution in process monitoring is particularly crucial for linerless vessels, where manufacturing defects can have severe consequences for vessel performance.
The application landscape for composite pressure vessels continues to expand, driven by emerging needs in various sectors. The hydrogen economy, in particular, is creating new demands for high-performance storage solutions. This is spurring innovation in manufacturing techniques for hydrogen tanks, pushing the boundaries of what's possible with composite materials.
The aerospace sector remains a key driver of innovation, with increasing demands for lightweight, high-performance pressure vessels for various applications. The development of new approaches to aerospace manufacturing is yielding insights that benefit the entire industry.
Looking ahead, several key areas are likely to dominate research and development efforts. The understanding of micro-scale damage mechanisms and their relationship to manufacturing parameters continues to evolve, supported by increasingly sophisticated simulation capabilities. Work on multiscale modeling approaches is providing new insights into how manufacturing decisions influence final product performance.
The development of predictive maintenance capabilities, powered by machine learning and extensive data analysis, represents another promising research direction. These systems aim to optimize not just the manufacturing process but the entire lifecycle of composite pressure vessels, from production through operational life.
As we look to the future, the integration of these various technological advances promises to make composite pressure vessel manufacturing more efficient, reliable, and sustainable. The key to success will lie in effectively combining these innovations while maintaining the high standards of quality and performance that the industry demands.
The manufacturing of linerless composite pressure vessels represents one of the most challenging and sophisticated applications in advanced composites manufacturing. Through our comprehensive examination of both theoretical foundations and practical implementations, several crucial insights have emerged that will shape the future of this technology.
The critical importance of end-to-end simulation and manufacturing integration cannot be overstated. Research has definitively shown that manufacturing-induced residual stresses can account for up to 50% of a vessel's transverse strength capacity, fundamentally challenging traditional design approaches that considered manufacturing and operational conditions separately. This finding emphasizes the need for comprehensive process monitoring and control throughout the manufacturing process.
The evolution of automated fiber placement technology has proven transformative in addressing these manufacturing challenges. Modern AFP systems, with their precise control over process parameters and advanced monitoring capabilities, provide the level of consistency and reliability required for producing high-performance linerless vessels. The integration of artificial intelligence and machine learning into these systems has further enhanced their capability to maintain optimal manufacturing conditions while predicting and preventing potential issues.
Temperature management emerges as a particularly critical factor, especially in cryogenic applications. The research clearly demonstrates that thermal stresses developed during manufacturing and cooling can trigger damage before operational loading begins. This understanding has led to the development of more sophisticated thermal management approaches that consider the entire thermal history of the vessel from manufacturing through operation.
The industry's shift toward digital manufacturing integration represents a significant step forward in addressing these complex challenges. Digital twin technology, combined with advanced simulation capabilities, now enables manufacturers to predict and optimize performance throughout the manufacturing process and operational life of the vessel.
Looking ahead, several key areas deserve continued focus and investment:
The development of more sophisticated material systems specifically designed for linerless pressure vessel applications continues to advance. These materials must balance processability with performance, particularly in extreme operating conditions. The growing emphasis on sustainable manufacturing approaches adds another dimension to this challenge, pushing the industry toward more environmentally conscious solutions.
Process automation and control systems will continue to evolve, becoming more intelligent and adaptive. The integration of advanced path planning with real-time quality monitoring systems promises to further improve manufacturing reliability and efficiency. These developments are particularly crucial for scaling up production while maintaining the high quality standards required for pressure vessel applications.
For organizations looking to advance their composite manufacturing capabilities, the path forward requires a holistic approach that considers both technical and practical aspects of implementation. Success in this field demands not just advanced equipment and materials, but also comprehensive training and support systems to ensure effective utilization of these technologies.
The future of linerless composite pressure vessel manufacturing lies in the effective integration of these various elements – advanced materials, sophisticated manufacturing systems, intelligent process control, and comprehensive training and support. Organizations that can successfully combine these elements while maintaining focus on quality and efficiency will be well-positioned to lead in this evolving industry.
As we continue to push the boundaries of what's possible in composite pressure vessel manufacturing, the importance of staying current with technological developments and best practices becomes ever more critical. The industry's ongoing evolution toward more automated, intelligent, and sustainable manufacturing approaches promises to create new opportunities for innovation and advancement in this crucial field.
The journey toward optimal linerless pressure vessel manufacturing continues, driven by technological innovation and deep understanding of manufacturing science. By embracing these advances while maintaining focus on practical implementation, manufacturers can achieve the high performance and reliability demands of modern applications while preparing for the challenges of tomorrow.
This blog post draws significantly from the following research paper:
Gonçalves, P.T.; Arteiro, A.; Rocha, N. End-to-End Simulation of Linerless Composite Pressure Vessels Using 3D Continuum Damage Models. J. Compos. Sci. 2024, 8, 504. https://doi.org/10.3390/jcs8120504
Special thanks to the authors of the primary research paper for their groundbreaking work in end-to-end simulation of linerless composite pressure vessels, which has significantly contributed to our understanding of manufacturing effects on vessel performance.