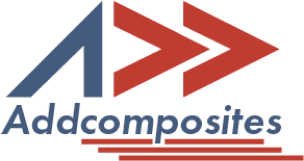
Composite pressure vessels have been widely used for decades in various industries such as aerospace, military, and marine applications due to their lightweight and high-strength properties. However, the automated fiber placement (AFP) process, which is a cutting-edge technology for fabricating composite pressure vessels, faces significant challenges in terms of wrinkle and overlap defects.
Key issues with AFP for composite pressure vessels:
Recent research has focused on addressing these problems through advanced placement path planning algorithms. Some notable approaches include:
However, there is still a need for a comprehensive solution that can generate wrinkle-free and defect-free placement paths for the entire pressure vessel structure, including the challenging dome sections. This is critical for improving the quality, performance, and efficiency of AFP-manufactured composite pressure vessels.
The presence of wrinkle and overlap defects in AFP-manufactured composite pressure vessels can have severe consequences on their structural integrity and performance.
Wrinkle defects, caused by out-of-plane buckling of prepreg tows during steering operations, can lead to:
Overlap defects, resulting from gaps between adjacent prepreg tows, can cause:
These defects not only compromise the mechanical properties and reliability of the composite pressure vessel but also hinder the efficiency and productivity of the AFP process. Key pain points include:
The impact of wrinkle and overlap defects extends beyond the manufacturing process. End-users of composite pressure vessels, such as aerospace and marine industries, face increased risks and costs associated with:
Addressing these defects is paramount for manufacturers to deliver high-quality, reliable, and cost-effective composite pressure vessels. This requires advanced placement path planning solutions that can minimize or eliminate wrinkle and overlap defects while optimizing production efficiency.
To address the challenges of wrinkle and overlap defects in AFP of composite pressure vessels, the authors propose a novel path planning approach that integrates a wrinkle-free criterion and defect-free algorithms specifically tailored for the ellipsoidal dome and cylinder sections.
Key features of the approach:
The approach leverages advanced computational methods and geometric analysis to generate optimized placement paths that minimize defects and maximize efficiency. Key advantages include:
The proposed path planning approach has been rigorously validated through simulations and experimental verification, demonstrating its effectiveness in generating
high-quality, defect-free placement paths for composite pressure vessels.
Simulation results:
Experimental verification:
Optimized motion control:
The simulation and experimental results confirm the effectiveness of the proposed approach in delivering wrinkle-free, defect-free, and full coverage placement paths for composite pressure vessels. The optimized motion control ensures the reliable and efficient execution of these paths on AFP machines.
Key benefits:
We would like to express my sincere gratitude to the authors Bo Wang, Lihua Wen, Jinyou Xiao, Shiyu Wang, Ping Ren, Liqiang Wang, Lei Zu, and Xiao Hou for their valuable contributions in writing this blog post. Their research paper, "Automated Fiber Placement Path Planning and Analysis of Pressure Vessels," served as the foundation for the content presented here.
Their innovative approach to optimizing automated fiber placement for composite pressure vessels, which integrates wrinkle-free criteria and defect-free algorithms, has the potential to revolutionize the manufacturing process. The comprehensive simulations and experimental validations conducted by the authors demonstrate the effectiveness of their method in reducing defects, improving quality, and increasing efficiency.
Discover the future of composite manufacturing with Addcomposites! Here's how you can get involved:
At Addcomposites, we are dedicated to revolutionizing composite manufacturing. Our AFP systems and comprehensive support services are waiting for you to harness. So, don't wait – get started on your journey to the future of manufacturing today!
Composite pressure vessels have been widely used for decades in various industries such as aerospace, military, and marine applications due to their lightweight and high-strength properties. However, the automated fiber placement (AFP) process, which is a cutting-edge technology for fabricating composite pressure vessels, faces significant challenges in terms of wrinkle and overlap defects.
Key issues with AFP for composite pressure vessels:
Recent research has focused on addressing these problems through advanced placement path planning algorithms. Some notable approaches include:
However, there is still a need for a comprehensive solution that can generate wrinkle-free and defect-free placement paths for the entire pressure vessel structure, including the challenging dome sections. This is critical for improving the quality, performance, and efficiency of AFP-manufactured composite pressure vessels.
The presence of wrinkle and overlap defects in AFP-manufactured composite pressure vessels can have severe consequences on their structural integrity and performance.
Wrinkle defects, caused by out-of-plane buckling of prepreg tows during steering operations, can lead to:
Overlap defects, resulting from gaps between adjacent prepreg tows, can cause:
These defects not only compromise the mechanical properties and reliability of the composite pressure vessel but also hinder the efficiency and productivity of the AFP process. Key pain points include:
The impact of wrinkle and overlap defects extends beyond the manufacturing process. End-users of composite pressure vessels, such as aerospace and marine industries, face increased risks and costs associated with:
Addressing these defects is paramount for manufacturers to deliver high-quality, reliable, and cost-effective composite pressure vessels. This requires advanced placement path planning solutions that can minimize or eliminate wrinkle and overlap defects while optimizing production efficiency.
To address the challenges of wrinkle and overlap defects in AFP of composite pressure vessels, the authors propose a novel path planning approach that integrates a wrinkle-free criterion and defect-free algorithms specifically tailored for the ellipsoidal dome and cylinder sections.
Key features of the approach:
The approach leverages advanced computational methods and geometric analysis to generate optimized placement paths that minimize defects and maximize efficiency. Key advantages include:
The proposed path planning approach has been rigorously validated through simulations and experimental verification, demonstrating its effectiveness in generating
high-quality, defect-free placement paths for composite pressure vessels.
Simulation results:
Experimental verification:
Optimized motion control:
The simulation and experimental results confirm the effectiveness of the proposed approach in delivering wrinkle-free, defect-free, and full coverage placement paths for composite pressure vessels. The optimized motion control ensures the reliable and efficient execution of these paths on AFP machines.
Key benefits:
We would like to express my sincere gratitude to the authors Bo Wang, Lihua Wen, Jinyou Xiao, Shiyu Wang, Ping Ren, Liqiang Wang, Lei Zu, and Xiao Hou for their valuable contributions in writing this blog post. Their research paper, "Automated Fiber Placement Path Planning and Analysis of Pressure Vessels," served as the foundation for the content presented here.
Their innovative approach to optimizing automated fiber placement for composite pressure vessels, which integrates wrinkle-free criteria and defect-free algorithms, has the potential to revolutionize the manufacturing process. The comprehensive simulations and experimental validations conducted by the authors demonstrate the effectiveness of their method in reducing defects, improving quality, and increasing efficiency.
Discover the future of composite manufacturing with Addcomposites! Here's how you can get involved:
At Addcomposites, we are dedicated to revolutionizing composite manufacturing. Our AFP systems and comprehensive support services are waiting for you to harness. So, don't wait – get started on your journey to the future of manufacturing today!