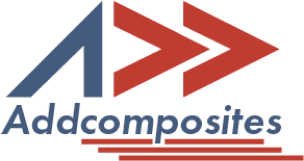
In today's rapidly evolving composite manufacturing landscape, versatility and cost-effectiveness are paramount. The AFP-XS system from Addcomposites has emerged as a revolutionary solution that uniquely combines Automated Fiber Placement (AFP) and filament winding capabilities in a single platform, creating unprecedented opportunities for manufacturers across aerospace, energy, defense, and marine sectors.
The AFP-XS represents a strategic fusion of AFP and filament winding technologies that creates synergistic capabilities far exceeding those of either method in isolation4. This integration enables unprecedented design freedom, material efficiency, and production flexibility that traditional single-process systems simply cannot match.
The system's innovative design features interchangeable compaction mechanisms that can alternate between AFP's localized pressure application and the continuous tension control required for filament winding4. Its adaptive tensioning system accommodates both AFP's low-tension placement (5-15 N) and winding's higher tension requirements (50-200 N), while the thermal management module offers dual-mode operation for both thermoplastic consolidation and thermoset resin control4.
Perhaps most impressively, the AFP-XS enables process switching through software with just an advanced planning module, compared to the 8+ hour changeover time typically required between traditional separate AFP and winding systems14. This hardware convergence reduces footprint requirements by 100% while maintaining the full capabilities of both technologies4.
The dual functionality of the AFP-XS delivers substantial return on investment through multiple avenues:
Hybrid AFP-filament winding systems demonstrate 80-85% cycle time reductions through strategic process allocation4. Filament winding handles 70-80% of symmetric, high-speed winding sections at 500-1000 mm/sec, while AFP concurrently places complex reinforcement features at 200-500 mm/sec with 0.5 mm placement accuracy4.
Lifecycle cost analyses show 50-60% savings over 5 years compared to maintaining separate AFP and winding systems4. The AFP-XS operates on a subscription model starting at €3,500 per month, with an option to purchase—a radical departure from traditional AFP systems requiring €1-5 million upfront investments6. Compared to legacy systems with €50,000-100,000 annual operational costs, the AFP-XS reduces total cost of ownership by 80-90% through its modular design and robotic compatibility6.
The system achieves material utilization improvements of up to 22% through waste reduction from AFP's precise ply tailoring at joint transitions and hybrid material streaming that enables simultaneous dry fiber winding and prepreg tape placement4. Through adaptive toolpath optimization in AddPath software, the AFP-XS achieves 85-92% material utilization rates across thermoset, thermoplastic, and dry fiber applications—a 35% improvement over manual layup processes6.
In a recent collaboration with defense manufacturer MBDA Systems and Compositadour, Addcomposites demonstrated the AFP-XS's capabilities in manufacturing rectangular tubes3. The layup program was generated using the winding feature of the company's AddPath software, ensuring wrinkle-free layup through sharp steering even on sharp radial corners3. The resulting rectangular tubes offered high strength-to-weight ratios, high load-bearing properties in both torsional and compression directions, and optimized environmental resistance—ideal for outdoor applications3.
A compelling use case for the AFP-XS's dual functionality is in next-generation hydrogen tanks, which demonstrated a 41% weight reduction through a combination of a 15-layer wound CFRP shell (0°/±85°), localized AFP reinforcement (T700SC/PEKK tapes) at port junctions, and an integrated thermoplastic liner via simultaneous SCF3D printing4. This hybrid approach would be impossible with single-process systems.
Compoxi, based in Girona, Spain, has installed the AFP-XS to characterize and qualify the technology for space applications, particularly targeting the growing New Space economy and constellation productions7. The company aims to leverage the system's higher placement accuracy with qualified materials for space applications to offer new services and broaden its portfolio for customers in the space sector7.
As the AFP-XS continues to gain traction with over 50 systems installed globally5, its dual AFP-filament winding functionality is reshaping the economic landscape of composite manufacturing. By enabling small and medium enterprises to compete on a global scale, this technology is democratizing access to advanced composite manufacturing techniques that were previously available only to large corporations with substantial budgets6.
The system's continued development focuses on AI-driven process optimization, circular economy integration, and microfactory networks, promising even greater efficiency and accessibility in the future6. As these innovations mature, the AFP-XS ecosystem will continue lowering barriers to advanced composite manufacturing, empowering manufacturers to lead the transition toward lightweight, sustainable industrial solutions.
In an industry where specialization has long been the norm, the AFP-XS proves that versatility and integration can deliver not just cost savings, but entirely new possibilities for composite design and manufacturing.