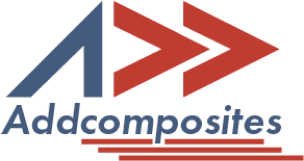
Designing dispersed continuous carbon fiber composite parts represents a cutting-edge area of research with significant implications for lightweight and high-performance structures. This complexity arises from the intricate interplay between material properties, manufacturing techniques, and the desired final mechanical behavior of the part.
The foundation of this challenge lies in the unique properties of carbon fiber reinforced polymers (CFRPs). These materials offer unparalleled strength-to-weight ratios, stiffness, toughness, and energy absorption capabilities. Their application spans critical sectors such as aerospace, automotive, and high-end sporting goods, where every gram of weight reduction can significantly enhance performance or fuel efficiency.
Despite these advantages, the manufacturing of composite laminates for structural applications has traditionally relied on quasi-isotropic lay-ups, which do not fully exploit the potential of composite materials. This limitation stems from the manufacturing complexities associated with achieving optimal ply orientation, especially for parts with complex geometries or those manufactured without additive manufacturing technologies.
The advent of Fused Filament Fabrication (FFF) for 3D printing has opened new possibilities in this domain. FFF allows for precise control over the orientation of continuous fiber reinforcements within the thermoplastic matrix, enabling the production of parts with customized mechanical properties tailored to specific applications. This includes the ability to design and manufacture parts with dispersed ply orientations, offering a broader range of fiber angles beyond the conventional 0°, 90°, and ±45°. Such versatility introduces the potential for lighter, more efficient structures with enhanced mechanical properties.
A key aspect of this design process involves overcoming the inherent challenges of FFF, such as void formation, layer adhesion, and the accurate prediction of mechanical behavior. Through a combination of experimental methods and numerical simulations, researchers have developed methodologies to optimize the fiber orientation and minimize defects, enhancing the mechanical performance of the printed parts.
One illustrative application of this methodology is the replacement of an aluminum motorcycle triple tree with an optimized 3D printed composite part. This example demonstrates not only the practical applicability of the research but also highlights the significant benefits in terms of weight reduction and cost savings.
The quest for achieving optimal mechanical properties in composite parts fabrication, especially using Fused Filament Fabrication (FFF) for carbon fiber reinforced polymers (CFRPs), poses significant challenges that span material selection, manufacturing process intricacies, and post-processing techniques. This section aims to dissect these challenges and explore the methodologies proposed to mitigate them, as illustrated in the comprehensive study of designing dispersed continuous carbon fiber composite parts.
One of the foremost challenges lies in the inherent limitations of the FFF process, particularly concerning void content and layer adhesion. These factors critically affect the mechanical properties of the manufactured parts. The study detailed an experimental approach to address this, revealing that post-processing at elevated temperatures and pressures significantly enhances interlaminar strength and reduces porosity, thereby improving mechanical properties. Specifically, a post-processing regimen of 150°C for 15 minutes under 1 MPa pressure was found to reduce porosity by approximately 90% and increase interlaminar strength by 150%, without altering the dimensions of the 3D model.
Achieving an optimal fiber orientation presents another substantial hurdle. The study outlined a methodology that begins with defining the problem and proceeds through optimizing fiber orientation based on load conditions, material characterization, and finally, virtual design and simulations. This process is vital for customizing the mechanical properties of parts to suit specific applications. By leveraging Classical Laminate Plate Theory (CLPT) and finite element analysis, the study showcased how to predict and enhance the mechanical performance of the printed parts.
We also touched on the optimization of laminate's thickness and the number of layers to match or exceed the mechanical performance of traditional quasi-isotropic layups. This optimization is crucial for parts intended to replace metal components, such as the motorcycle triple tree part explored in the study, which requires careful consideration of the structural integrity under operational loads.
Furthermore, the challenge extends to material characterization, which is necessary but not sufficient with standard unidirectional and cross-ply laminates. The dispersed laminates necessitate additional tests to complement the understanding of material behavior, highlighting the complexity of predicting the performance of these innovative materials accurately.
Fused Filament Fabrication (FFF), a form of 3D printing technology, has emerged as a pivotal technique in the advanced design and optimization of composite materials, particularly dispersed continuous carbon fiber composites. The methodology introduced through the study underpins a multifaceted approach involving customized mechanical properties, manufacturing via 3D printing, post-processing, and the characterization of material models for finite element simulations, culminating in virtual testing of structural parts.
The significant advantage of FFF lies in its capability to enhance the mechanical properties of laminates through pressurized post-processing. Experimental findings showcased that post-processing under controlled conditions (150°C for 15 minutes at 1 MPa) not only reduced porosity by approximately 90% but also amplified interlaminar strength by 150%, maintaining the 3D model's nominal dimensions. This result validates the material models utilized in virtual tests, offering a robust framework for predicting and improving the performance of printed parts.
The study further elaborates on a practical application: the replacement of an aluminum motorcycle triple tree with an optimized 3D printed composite part. This case underscores the methodology's efficacy in achieving enhanced mechanical properties suitable for demanding applications, such as braking and cornering forces in motorcycle components. The transition from traditional metal parts to optimized composite counterparts underscores a significant leap in material science, enabled by the precision and flexibility of FFF technology.
Furthermore, the integration of experimental and numerical methods facilitates a comprehensive understanding of the composite's behavior under various load conditions. This includes examining void content, characterizing material properties through standard tests, and validating these findings through finite element simulations that incorporate the specific geometry and load conditions of the structural part.
The transformation of composite part manufacturing through optimized fiber orientation presents a significant leap in engineering, primarily by enhancing mechanical properties to meet rigorous application demands. The article extensively discusses a novel methodology combining experimental tests with realistic simulations to tailor the mechanical behavior of 3D printed dispersed laminates, embodying a leap in material science and engineering.
The core of this revolution lies in optimizing the fiber orientation in the composite material. This strategy not only addresses the traditional constraints of composite manufacturing but also opens avenues for designing parts with unprecedented performance metrics. The dispersed laminate fabrication, enabled by Fused Filament Fabrication (FFF), offers a methodical approach to manipulate fiber orientation precisely, thereby optimizing the mechanical properties of the final product.
The experimental aspect of this methodology involves characterizing the mechanical behavior of the laminates post-fabrication and post-processing, which notably enhances the material's properties by reducing void content and improving interlaminar strength. These improvements are critical for achieving the desired mechanical properties and dimensional accuracy.
The optimization process extends beyond mere fabrication, incorporating a semi-automatic approach to determine the most effective fiber orientation based on stress distribution and mechanical demands of the intended application. This process, underpinned by Classical Laminate Plate Theory (CLPT) and finite element simulations, ensures that each layer within the laminate contributes optimally to the part's overall strength and durability.
An exemplary application of this methodology is illustrated through the replacement of a metallic motorcycle part with a 3D printed composite counterpart. This case study underscores not only the feasibility of substituting traditional materials with advanced composites but also the potential for significant weight reduction and cost savings without compromising safety or performance.
We extend our deepest gratitude to D. Garoz Gómez, C. Pascual-González, J. García-Moreno Caraballo, and J.P. Fernández-Blázquez for their significant contributions to the groundbreaking study on designing and optimizing dispersed continuous carbon fiber composite parts using fused filament fabrication (FFF). Their pioneering work has not only enhanced our understanding of composite material fabrication but has also provided invaluable insights into the potential of 3D printing technology in advancing the mechanical properties and design flexibility of structural parts.
Discover the future of composite manufacturing with Addcomposites! Here's how you can get involved:
At Addcomposites, we are dedicated to revolutionizing composite manufacturing. Our AFP systems and comprehensive support services are waiting for you to harness. So, don't wait – get started on your journey to the future of manufacturing today!
Designing dispersed continuous carbon fiber composite parts represents a cutting-edge area of research with significant implications for lightweight and high-performance structures. This complexity arises from the intricate interplay between material properties, manufacturing techniques, and the desired final mechanical behavior of the part.
The foundation of this challenge lies in the unique properties of carbon fiber reinforced polymers (CFRPs). These materials offer unparalleled strength-to-weight ratios, stiffness, toughness, and energy absorption capabilities. Their application spans critical sectors such as aerospace, automotive, and high-end sporting goods, where every gram of weight reduction can significantly enhance performance or fuel efficiency.
Despite these advantages, the manufacturing of composite laminates for structural applications has traditionally relied on quasi-isotropic lay-ups, which do not fully exploit the potential of composite materials. This limitation stems from the manufacturing complexities associated with achieving optimal ply orientation, especially for parts with complex geometries or those manufactured without additive manufacturing technologies.
The advent of Fused Filament Fabrication (FFF) for 3D printing has opened new possibilities in this domain. FFF allows for precise control over the orientation of continuous fiber reinforcements within the thermoplastic matrix, enabling the production of parts with customized mechanical properties tailored to specific applications. This includes the ability to design and manufacture parts with dispersed ply orientations, offering a broader range of fiber angles beyond the conventional 0°, 90°, and ±45°. Such versatility introduces the potential for lighter, more efficient structures with enhanced mechanical properties.
A key aspect of this design process involves overcoming the inherent challenges of FFF, such as void formation, layer adhesion, and the accurate prediction of mechanical behavior. Through a combination of experimental methods and numerical simulations, researchers have developed methodologies to optimize the fiber orientation and minimize defects, enhancing the mechanical performance of the printed parts.
One illustrative application of this methodology is the replacement of an aluminum motorcycle triple tree with an optimized 3D printed composite part. This example demonstrates not only the practical applicability of the research but also highlights the significant benefits in terms of weight reduction and cost savings.
The quest for achieving optimal mechanical properties in composite parts fabrication, especially using Fused Filament Fabrication (FFF) for carbon fiber reinforced polymers (CFRPs), poses significant challenges that span material selection, manufacturing process intricacies, and post-processing techniques. This section aims to dissect these challenges and explore the methodologies proposed to mitigate them, as illustrated in the comprehensive study of designing dispersed continuous carbon fiber composite parts.
One of the foremost challenges lies in the inherent limitations of the FFF process, particularly concerning void content and layer adhesion. These factors critically affect the mechanical properties of the manufactured parts. The study detailed an experimental approach to address this, revealing that post-processing at elevated temperatures and pressures significantly enhances interlaminar strength and reduces porosity, thereby improving mechanical properties. Specifically, a post-processing regimen of 150°C for 15 minutes under 1 MPa pressure was found to reduce porosity by approximately 90% and increase interlaminar strength by 150%, without altering the dimensions of the 3D model.
Achieving an optimal fiber orientation presents another substantial hurdle. The study outlined a methodology that begins with defining the problem and proceeds through optimizing fiber orientation based on load conditions, material characterization, and finally, virtual design and simulations. This process is vital for customizing the mechanical properties of parts to suit specific applications. By leveraging Classical Laminate Plate Theory (CLPT) and finite element analysis, the study showcased how to predict and enhance the mechanical performance of the printed parts.
We also touched on the optimization of laminate's thickness and the number of layers to match or exceed the mechanical performance of traditional quasi-isotropic layups. This optimization is crucial for parts intended to replace metal components, such as the motorcycle triple tree part explored in the study, which requires careful consideration of the structural integrity under operational loads.
Furthermore, the challenge extends to material characterization, which is necessary but not sufficient with standard unidirectional and cross-ply laminates. The dispersed laminates necessitate additional tests to complement the understanding of material behavior, highlighting the complexity of predicting the performance of these innovative materials accurately.
Fused Filament Fabrication (FFF), a form of 3D printing technology, has emerged as a pivotal technique in the advanced design and optimization of composite materials, particularly dispersed continuous carbon fiber composites. The methodology introduced through the study underpins a multifaceted approach involving customized mechanical properties, manufacturing via 3D printing, post-processing, and the characterization of material models for finite element simulations, culminating in virtual testing of structural parts.
The significant advantage of FFF lies in its capability to enhance the mechanical properties of laminates through pressurized post-processing. Experimental findings showcased that post-processing under controlled conditions (150°C for 15 minutes at 1 MPa) not only reduced porosity by approximately 90% but also amplified interlaminar strength by 150%, maintaining the 3D model's nominal dimensions. This result validates the material models utilized in virtual tests, offering a robust framework for predicting and improving the performance of printed parts.
The study further elaborates on a practical application: the replacement of an aluminum motorcycle triple tree with an optimized 3D printed composite part. This case underscores the methodology's efficacy in achieving enhanced mechanical properties suitable for demanding applications, such as braking and cornering forces in motorcycle components. The transition from traditional metal parts to optimized composite counterparts underscores a significant leap in material science, enabled by the precision and flexibility of FFF technology.
Furthermore, the integration of experimental and numerical methods facilitates a comprehensive understanding of the composite's behavior under various load conditions. This includes examining void content, characterizing material properties through standard tests, and validating these findings through finite element simulations that incorporate the specific geometry and load conditions of the structural part.
The transformation of composite part manufacturing through optimized fiber orientation presents a significant leap in engineering, primarily by enhancing mechanical properties to meet rigorous application demands. The article extensively discusses a novel methodology combining experimental tests with realistic simulations to tailor the mechanical behavior of 3D printed dispersed laminates, embodying a leap in material science and engineering.
The core of this revolution lies in optimizing the fiber orientation in the composite material. This strategy not only addresses the traditional constraints of composite manufacturing but also opens avenues for designing parts with unprecedented performance metrics. The dispersed laminate fabrication, enabled by Fused Filament Fabrication (FFF), offers a methodical approach to manipulate fiber orientation precisely, thereby optimizing the mechanical properties of the final product.
The experimental aspect of this methodology involves characterizing the mechanical behavior of the laminates post-fabrication and post-processing, which notably enhances the material's properties by reducing void content and improving interlaminar strength. These improvements are critical for achieving the desired mechanical properties and dimensional accuracy.
The optimization process extends beyond mere fabrication, incorporating a semi-automatic approach to determine the most effective fiber orientation based on stress distribution and mechanical demands of the intended application. This process, underpinned by Classical Laminate Plate Theory (CLPT) and finite element simulations, ensures that each layer within the laminate contributes optimally to the part's overall strength and durability.
An exemplary application of this methodology is illustrated through the replacement of a metallic motorcycle part with a 3D printed composite counterpart. This case study underscores not only the feasibility of substituting traditional materials with advanced composites but also the potential for significant weight reduction and cost savings without compromising safety or performance.
We extend our deepest gratitude to D. Garoz Gómez, C. Pascual-González, J. García-Moreno Caraballo, and J.P. Fernández-Blázquez for their significant contributions to the groundbreaking study on designing and optimizing dispersed continuous carbon fiber composite parts using fused filament fabrication (FFF). Their pioneering work has not only enhanced our understanding of composite material fabrication but has also provided invaluable insights into the potential of 3D printing technology in advancing the mechanical properties and design flexibility of structural parts.
Discover the future of composite manufacturing with Addcomposites! Here's how you can get involved:
At Addcomposites, we are dedicated to revolutionizing composite manufacturing. Our AFP systems and comprehensive support services are waiting for you to harness. So, don't wait – get started on your journey to the future of manufacturing today!