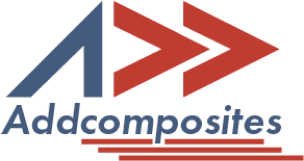
Welcome to our comprehensive course on the design and development of sustainable compressed hydrogen storage tanks. As the world moves towards cleaner energy solutions, hydrogen fuel cell technology is emerging as a key player in the future of advanced mobility and energy storage. This course aims to provide you with a thorough understanding of the challenges, technologies, and considerations involved in creating safe, lightweight, and competitive hydrogen storage solutions.
By the end of this course, you will:
1. Why do we need lighter hydrogen tanks?
2. What is a Hydrogen Tank & Tank-Types
3. Filament winding hydrogen tanks (Thermoset)
4. Thermoplastic Tape Winding of Hydrogen Tank
5. Traditional Filament winding vs. Robotic Winding
6. How to select the right Hydrogen tanks Liners, Matrix, and Fiber materials
7. Optimal design for composite high-pressure hydrogen storage tank
8. Hydrogen storage tanks: testing, certification, codes & standards
Key Takeaways
Who Should Take This Course
This course is ideal for:
As we progress through this course, you'll gain a comprehensive understanding of the intricate world of hydrogen storage tank development. From materials science to advanced manufacturing techniques, from complex design processes to stringent safety standards, this course will equip you with the knowledge needed to contribute to the exciting field of sustainable energy storage.
Are you ready to dive into the future of clean energy storage? Let's begin our journey into the design and development of sustainable compressed hydrogen storage tanks!
Start with Chapter 1: Why do we need lighter hydrogen tanks?
Welcome to the first chapter of our comprehensive course on the Design and Development of Sustainable Compressed Hydrogen Storage Tank. In this chapter, we'll explore the critical need for lighter hydrogen tanks and their impact on the future of sustainable energy.
The Weight Challenge in Hydrogen Storage
As we transition towards a hydrogen-based economy, one of the most significant challenges we face is the storage and transportation of hydrogen. Traditional storage methods often result in heavy tanks, which can limit the efficiency and practicality of hydrogen-powered systems, especially in mobile applications.
Developing lighter hydrogen tanks is crucial for several reasons:
Creating lighter hydrogen tanks isn't without its challenges. Engineers and researchers must navigate:
Researchers and manufacturers are exploring various strategies to reduce tank weight:
The development of lighter hydrogen tanks has implications beyond just transportation:
Looking Ahead: The Future of Hydrogen Storage
As we continue to innovate in the field of hydrogen storage, we can expect:
The need for lighter hydrogen tanks is driving innovation across multiple disciplines, from materials science to manufacturing techniques. As we progress in this field, we're not just solving a technical challenge – we're paving the way for a more sustainable, hydrogen-powered future.
In the next chapters of our Design and Development of Sustainable Compressed Hydrogen Storage Tank course, we'll delve deeper into the specific technologies and methodologies used to create these cutting-edge storage solutions.
Ready to dive deeper into the world of hydrogen storage? Continue to the next chapter where we'll explore the different types of hydrogen tanks and their applications.
Welcome to the second chapter of our comprehensive course on the Design and Development of Sustainable Compressed Hydrogen Storage Tank. In this chapter, we'll explore the fundamental concept of hydrogen tanks and delve into the various types of tanks used in different applications.
A hydrogen tank, also known as a hydrogen cylinder or hydrogen storage vessel, is a specialized container designed to store hydrogen gas under high pressure. These tanks play a crucial role in the hydrogen economy, enabling the storage and transportation of hydrogen for various applications, from fuel cell vehicles to industrial processes.
Key Features of Hydrogen Tanks:
The industry classifies hydrogen tanks into five main types, each with unique characteristics and applications:
Type I: All-Metal Tanks
Type II: Metal Liner with Composite Hoop Wrap
Type III: Metal Liner with Full Composite Wrap
Type IV: Polymer Liner with Full Composite Wrap
Type V: Linerless All-Composite
For a more detailed comparison of these tank types, refer to our article on Types of Hydrogen Tanks: Technological Differences and Advantages Explained.
The manufacturing process varies depending on the tank type:
Learn more about these manufacturing techniques in our chapter on composite manufacturing methods.
Selecting the appropriate tank type depends on several factors:
For guidance on material selection, refer to our guide on How to Select the Right Hydrogen Tanks Liners, Matrix, and Fiber Materials.
As we continue to innovate in the field of hydrogen storage, we're seeing exciting developments:
Understanding the different types of hydrogen tanks is crucial for designing and developing sustainable compressed hydrogen storage solutions. Each type offers unique advantages and challenges, and the choice depends on the specific application and requirements.
In the next chapters of our Design and Development of Sustainable Compressed Hydrogen Storage Tank course, we'll explore the manufacturing techniques, material selection, and design optimization for these advanced storage systems.
Ready to dive deeper into the world of hydrogen storage? Continue to the next chapter where we'll discuss the manufacturing techniques for composite hydrogen tanks.
Welcome to the third chapter of our comprehensive course on the Design and Development of Sustainable Compressed Hydrogen Storage Tank. In this chapter, we'll explore the filament winding process for manufacturing thermoset composite hydrogen tanks, a crucial technique in creating lightweight and strong storage solutions.
Filament winding is a manufacturing technique primarily used to create hollow, circular, or oval-shaped composite parts. It's particularly well-suited for producing high-pressure vessels like hydrogen tanks, where strength, weight, and durability are critical factors.
Key Advantages of Filament Winding:
Step 1: Mandrel Preparation
Step 2: Fiber Impregnation
Step 3: Winding
Step 4: Curing
Step 5: Mandrel Removal
The strength and performance of the tank heavily depend on the winding pattern:
Hoop Winding:
Helical Winding:
Combination Patterns:
Learn more about composite layup strategies in our chapter on composite design principles.
Thermoset resins, particularly epoxies, are commonly used in filament winding for hydrogen tanks due to their:
However, thermosets also have some limitations:
For a comparison with thermoplastic alternatives, see our chapter on thermoplastic composite tanks.
Modern filament winding for hydrogen tanks often incorporates advanced technologies:
Ensuring the quality of filament-wound tanks is crucial:
For more on testing procedures, see our chapter on hydrogen tank certification and testing.
While thermoset composites offer excellent performance, their environmental impact is a concern:
Efforts are ongoing to develop more sustainable thermoset resins and recycling methods.
Filament winding with thermoset composites is a cornerstone technology in the production of high-performance hydrogen tanks. Its ability to create lightweight, strong, and durable structures makes it ideal for the demanding requirements of hydrogen storage.
As we continue our Design and Development of Sustainable Compressed Hydrogen Storage Tank course, we'll explore alternative manufacturing methods and materials, each offering unique advantages in our quest for optimal hydrogen storage solutions.
Ready to learn about cutting-edge alternatives? Continue to the next chapter where we'll discuss thermoplastic tape winding for hydrogen tanks.
Welcome to the fourth chapter of our comprehensive course on the Design and Development of Sustainable Compressed Hydrogen Storage Tank. In this chapter, we'll explore the innovative technique of thermoplastic tape winding for manufacturing hydrogen tanks, a method that offers unique advantages in terms of sustainability and performance.
Thermoplastic Tape Winding (TTW) is an advanced manufacturing process that combines the principles of filament winding with the benefits of thermoplastic composites. This technique is gaining traction in the production of high-performance hydrogen tanks due to its potential for faster processing, improved recyclability, and enhanced mechanical properties.
Step 1: Material Preparation
Step 2: Mandrel Setup
Step 3: Winding
Step 4: In-Situ Consolidation
Step 5: Cooling
1. Temperature Control
2. Tape Placement Accuracy
3. Crystallinity Management
4. First Ply Adhesion
Materials for Thermoplastic Tape Winding
Common thermoplastic matrices used in hydrogen tank production include:
PEEK (Polyether Ether Ketone):
PEKK (Polyetherketoneketone):
PA12 (Polyamide 12):
For more on material selection, see our chapter on composite materials for hydrogen tanks.
In-Situ Crystallization Control
Hybrid Processes
Smart Manufacturing Integration
Environmental and Sustainability Aspects
Thermoplastic composites offer significant advantages in terms of sustainability:
However, challenges remain in establishing efficient recycling processes for composite structures. Learn more about sustainability in composites in our dedicated chapter.
While both materials can produce high-performance tanks, they have distinct characteristics:
For a detailed comparison, refer to our chapter on material selection for hydrogen tanks.
The field of thermoplastic tape winding for hydrogen tanks is rapidly evolving:
Thermoplastic tape winding represents a significant advancement in the manufacture of hydrogen tanks, offering a compelling combination of performance, processing speed, and sustainability. As we continue to innovate in this field, thermoplastic composites are likely to play an increasingly important role in the design and development of sustainable compressed hydrogen storage tanks.
Ready to explore more manufacturing techniques? Continue to the next chapter where we'll discuss the comparison between traditional and robotic winding methods.
Welcome to the fifth chapter of our comprehensive course on the Design and Development of Sustainable Compressed Hydrogen Storage Tank. In this chapter, we'll explore and compare two key manufacturing techniques: traditional filament winding and the more advanced robotic winding. Understanding these methods is crucial for optimizing the production of high-performance hydrogen tanks.
Winding techniques are fundamental in the production of composite pressure vessels, including hydrogen tanks. As we've discussed in our previous chapters on filament winding and thermoplastic tape winding, these methods allow for the creation of strong, lightweight structures ideal for hydrogen storage.
Overview
Traditional filament winding is a well-established manufacturing process that has been used for decades in the production of cylindrical and spherical pressure vessels.
Key Characteristics:
Process Description:
Advantages:
Limitations:
Overview
Robotic winding leverages advanced robotics and control systems to enhance the capabilities of the winding process.
Key Characteristics:
Process Description:
Advantages:
Limitations:
When choosing between traditional and robotic winding for sustainable hydrogen tank production, consider:
For more on sustainable manufacturing practices, see our chapter on sustainability in composite production.
Both traditional filament winding and robotic winding have their place in the manufacture of hydrogen storage tanks. The choice between them depends on factors such as production volume, geometric complexity, desired performance characteristics, and available investment.
As we continue to innovate in the Design and Development of Sustainable Compressed Hydrogen Storage Tank, the integration and optimization of these winding technologies will play a crucial role in producing efficient, safe, and sustainable hydrogen storage solutions.
Ready to dive deeper into the materials used in hydrogen tanks? Continue to the next chapter where we'll explore the selection of liners, matrices, and fiber materials for optimal tank performance.
Welcome to the sixth chapter of our comprehensive course on the Design and Development of Sustainable Compressed Hydrogen Storage Tank. In this crucial chapter, we'll explore the intricate process of selecting the optimal materials for hydrogen tanks, focusing on liners, matrix materials, and fiber reinforcements.
The performance, safety, and efficiency of a hydrogen tank heavily depend on the materials used in its construction. As we've discussed in our previous chapters on tank types and manufacturing methods, the choice of materials can significantly impact the tank's weight, strength, permeability, and overall sustainability.
The liner serves as a barrier between the stored hydrogen and the composite structure, playing a critical role in preventing hydrogen permeation.
Metal Liners
Advantages:
Disadvantages:
Common Materials:
Polymer Liners
Advantages:
Disadvantages:
Common Materials:
Linerless Designs
For certain applications, especially in aerospace, linerless tank designs are being explored:
The matrix material holds the reinforcing fibers together and transfers loads between them.
Thermoset Matrices
Advantages:
Disadvantages:
Common Materials:
Thermoplastic Matrices
Advantages:
Disadvantages:
Common Materials:
For more on the comparison between thermoset and thermoplastic composites, see our dedicated chapter.
Fibers provide the primary structural strength in composite hydrogen tanks.
Carbon Fiber
Advantages:
Disadvantages:
Glass Fiber
Advantages:
Disadvantages:
Some designs utilize a combination of fiber types:
Learn more about fiber reinforcements in our comprehensive guide.
When selecting materials for hydrogen tanks, consider the following factors:
Selecting the right combination of liner, matrix, and fiber materials is crucial for developing high-performance, safe, and sustainable hydrogen storage tanks. As we continue our journey through the Design and Development of Sustainable Compressed Hydrogen Storage Tank course, we'll explore how these material choices influence the overall tank design and performance.
Ready to learn how these materials come together in the tank design process? Continue to the next chapter where we'll delve into the optimal design strategies for composite high-pressure hydrogen storage tanks.
Welcome to the seventh chapter of our comprehensive course on the Design and Development of Sustainable Compressed Hydrogen Storage Tank. In this crucial chapter, we'll explore the intricate process of optimizing the design of composite high-pressure hydrogen storage tanks, bringing together the knowledge from our previous chapters on materials, manufacturing processes, and tank types.
Designing a high-pressure hydrogen storage tank involves balancing multiple factors including safety, performance, weight, cost, and sustainability. The goal is to create a tank that can safely store hydrogen at high pressures while being as light and efficient as possible.
Step 1: Define Requirements
Step 2: Material Selection
Refer to our previous chapter on material selection for detailed guidance. Key considerations include:
Step 3: Geometric Design
Step 4: Layup Design
Step 5: Finite Element Analysis (FEA)
Topology Optimization
Multi-Objective Optimization
Design for Manufacturing
Failure Modes to Consider
Progressive Failure Analysis
Burst Pressure Prediction
Material Efficiency
Design for Recyclability
Life Cycle Assessment (LCA)
Certification and Testing Considerations
Design with certification requirements in mind:
For more details on testing and certification, see our chapter on hydrogen tank safety and regulations.
Optimal design of composite high-pressure hydrogen storage tanks is a complex, multidisciplinary challenge. It requires a deep understanding of materials, manufacturing processes, and structural mechanics, as well as consideration of safety, performance, and sustainability factors.
As we continue our journey through the Design and Development of Sustainable Compressed Hydrogen Storage Tank course, we'll explore how these design principles are applied in real-world scenarios and how they interact with manufacturing processes and regulatory requirements.
Ready to see how these optimized designs are put to the test? Continue to the next chapter where we'll delve into the testing, certification, and regulatory landscape for hydrogen storage tanks.
Welcome to the eighth and final chapter of our comprehensive course on the Design and Development of Sustainable Compressed Hydrogen Storage Tank. In this crucial chapter, we'll explore the rigorous testing procedures, certification processes, and the complex landscape of codes and standards that govern the development and deployment of hydrogen storage tanks.
Introduction
The safety and reliability of hydrogen storage tanks are paramount, given the high pressures involved and the unique properties of hydrogen. As we've seen in our previous chapters on design and materials, creating a high-performance tank is only part of the journey. Ensuring that these tanks meet stringent safety standards is equally important.
Regulations
Codes
Standards
1. Design Qualification Tests
Burst Test
Cycle Test
Environmental Exposure Tests
Fire Resistance Test
2. Production Tests
Hydrostatic Proof Test
Leak Test
3. Batch Tests
Burst Test
Material Tests
Leak-Before-Burst Design
Pressure Relief Devices (PRDs)
Impact Resistance
Non-Destructive Evaluation (NDE) Techniques
Digital Twin Technology
Harmonization of Global Standards
Certification for New Materials and Processes
Sustainability Considerations in Standards
As discussed in our chapter on sustainable design, future standards are likely to incorporate:
The rigorous testing, certification processes, and adherence to codes and standards are crucial in ensuring the safety and reliability of hydrogen storage tanks. As we've explored throughout this Design and Development of Sustainable Compressed Hydrogen Storage Tank course, creating high-performance, safe, and sustainable hydrogen storage solutions requires a holistic approach that considers materials, design, manufacturing, and regulatory compliance.
By understanding and adhering to these standards, we can accelerate the adoption of hydrogen technologies while ensuring public safety and confidence in these critical components of a sustainable energy future.
Thank you for joining us on this comprehensive journey through the world of hydrogen storage tank development. We hope this course has provided you with valuable insights and knowledge to contribute to the advancement of sustainable energy solutions.