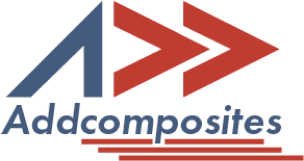
Advanced composite materials, primarily fiber-reinforced polymers (FRPs), consist of high-strength fibers embedded in a polymer matrix. These materials are characterized by their anisotropic properties, with fibers providing strength and stiffness in specific directions while the matrix transfers loads between fibers and protects them from environmental factors.
Common types of composites include:
For a more detailed exploration of composite materials, check out our Introduction to Composite Materials blog post.
These advantages make composites ideal for various applications across industries. To learn more about the real-world applications of composites, visit our Innovations in Composite Materials page.
For more information on composites in aerospace, read our article on Applications and Limitations of Composite Materials in Aerospace Engineering.
Discover more about composites in the automotive industry in our Driving Forward with Composite Materials blog post.
For a comprehensive look at composites in aerospace, visit our Composite Sky: Advanced Materials Defining Modern Aerospace article.
To learn more about composite manufacturing challenges, check out our Challenges of Switching to Composite Materials post.
The heterogeneous microstructure of composites introduces unique defect types:
These defects can significantly impact the performance and longevity of composite structures, necessitating advanced inspection techniques and tailored repair strategies. For a deeper dive into this topic, read our Understanding Defects and Damage in Composite Materials and Structures article.
By understanding the fundamentals of composite materials, their advantages, applications, and unique challenges, we lay the groundwork for identifying and addressing defects and damage in composite structures. This knowledge is crucial for ensuring the integrity and performance of composite components across various industries.
Understanding common defects and damage in composite materials is crucial for ensuring the structural integrity and performance of composite components. This chapter explores two main categories: manufacturing defects and in-service damage.
Manufacturing defects originate during the production process and can significantly impact the performance of composite structures. For a comprehensive overview of composite manufacturing processes, visit our Fundamentals of Composites Manufacturing page.
For more information on how these defects can be detected, check out our Non-Destructive Testing for Composites guide.
In-service damage occurs during the operational life of the composite structure.
For more details on how these types of damage affect composite structures, visit our Understanding Defects and Damage in Composite Materials and Structures page.
The impact of defects on structural integrity depends on several factors:
Criticality Ranking (general guideline):
Various Non-Destructive Inspection (NDI) techniques are employed to detect and characterize defects:
The selection of appropriate NDI methods depends on the defect type, material system, and structural configuration. Learn more about these techniques in our Non-Destructive Testing for Composites article.
Understanding common defects and damage in composites is essential for effective quality control, maintenance, and repair strategies. By recognizing these issues early and implementing appropriate mitigation measures, the performance and longevity of composite structures can be significantly enhanced.
Accurate characterization of defects and damage in composite materials is crucial for assessing their impact on structural integrity and determining appropriate repair strategies. This chapter explores the key aspects of defect characterization, including size, location, and frequency, as well as generalized defect types.
The size of a defect is a critical parameter in determining its impact on structural integrity. Defects are typically categorized as microscopic or macroscopic.
For more information on detection methods, visit our Non-Destructive Testing for Composites page.
The location of a defect within the composite structure significantly influences its effect on mechanical properties.
To learn more about how defect location affects composite structures, check our Understanding Defects and Damage in Composite Materials and Structures article.
The frequency or density of defects in a composite structure affects both local and global mechanical properties.
Example: Delamination interaction criterion
If (d < 2h), consider as single larger delamination
For more insights on how defect frequency impacts composite performance, visit our Defects and Damage in Composite Materials and Structures page.
Defects in composites can be generalized into four main categories based on their effect on the stress state of the material:
To understand how these defect types are addressed in the manufacturing process, check our Composites Manufacturing: Tracking and Reducing Waste article.
The generalized defect types can be related to their effect on the stress state:
For more details on how these stress states affect composite structures, visit our Structural Composites Design Concepts page.
By characterizing defects in terms of these generalized types, engineers can more effectively assess their impact on structural integrity and develop appropriate mitigation strategies. Understanding the size, location, frequency, and type of defects is crucial for maintaining the performance and safety of composite structures across various applications.
Non-Destructive Inspection (NDI) techniques are crucial for assessing the integrity of composite structures without causing damage. This chapter explores various NDI methods commonly used in the composite industry, their principles, capabilities, and limitations.
Visual inspection is the primary and most accessible NDI method for composite structures.
For more information on visual inspection techniques, visit our Defects and Damage in Composite Materials page.
Ultrasonic testing is widely used for detecting internal defects in composites.
To learn more about ultrasonic testing in composites, check our Non-Destructive Testing for Composites: Different Inspection Methods article.
Thermography utilizes infrared radiation to detect subsurface defects.
For more details on thermography in composite inspection, visit our Understanding Defects and Damage in Composite Materials and Structures page.
For a comprehensive overview of these techniques, check our Non-Destructive Testing for Composites: Different Inspection Methods article.
The choice of NDI method depends on various factors:
A multi-method approach is often employed for comprehensive inspection, combining the strengths of different techniques.
For more insights on the future of NDI in composites, visit our Advancing Composite Manufacturing with Machine Learning, Computer Vision, and Digital Twin page.
By understanding the capabilities and limitations of various NDI methods, engineers can develop effective inspection strategies for composite structures, ensuring their integrity throughout their service life. The integration of advanced technologies and AI-driven approaches is set to further enhance the accuracy and efficiency of composite inspection processes in the future.
Understanding the failure modes and mechanisms in composite materials is crucial for predicting and preventing structural failures. This chapter explores the basic failure modes, complex failure scenarios, and the underlying mechanisms that lead to composite failure.
Composite materials exhibit four primary failure modes at the microscopic level:
Fiber Tensile Strength:
σf_ult = Ef * εf_ult
Where:
Matrix Shear Strength (von Mises criterion):
τm_ult = σm_ult / √3
Where:
Critical Fiber Length for Load Transfer:
lc = (σf_ult * d) / (2 * τi)
Where:
Mode I Strain Energy Release Rate:
GI = (Kı^2) / E'
Where:
For more details on these basic failure modes, visit our Defects and Damage in Composite Materials and Structures page.
In real structures, failure modes often combine and interact, leading to complex failure scenarios:
CAI Strength Prediction (simplified):
σCAI = σ0 * (1 - (d/W)^2)
Where:
Bearing Strength:
σbr = Fbr / (d * t)
Where:
Interlaminar Normal Stress (simplified):
σz ≈ (Δα * ΔT * E2) / (1 - ν12 * ν21)
Where:
Stiffness Degradation Model:
E(n) = E0 * (1 - D(n))
Where:
To learn more about complex failure modes in composites, check our Understanding Defects and Damage in Composite Materials and Structures article.
Understanding the underlying mechanisms of failure is crucial for predicting and preventing composite failure:
Microbuckling Critical Stress:
σcr = (Gm * Vf) / (1 - Vf)
Where:
Puck's Action Plane Strength (APS) criterion for matrix failure:
(τnt / S21 - μnt * σn)^2 + (τn1 / S21)^2 = 1
Where:
Interfacial Shear Stress Distribution (shear-lag model):
τ(x) = (P * sinh(β * x)) / (2π * r * t * sinh(β * l))
Where:
Mixed-Mode Delamination Criterion (Power Law):
(GI / GIc)^α + (GII / GIIc)^β = 1
Where:
For more information on failure mechanisms in composites, visit our Mechanical Testing of Composites page.
Understanding these failure modes and mechanisms allows engineers to:
By considering the interplay between these various failure modes and mechanisms, engineers can better predict and mitigate potential failure scenarios in composite structures. This knowledge is crucial for ensuring the safety and reliability of composite components across various industries.
For further insights into composite design considering failure modes, check our Best Step-by-Step Guide for Composites Design article
Understanding how defects affect the structural integrity of composite materials is crucial for ensuring the safety and performance of composite structures. This chapter explores the impact of various defects on composite performance, focusing on matrix cracks, delaminations, and fiber cuts/holes.
Matrix cracks are one of the most common defects in composite materials, often occurring early in the loading history.
Stiffness reduction model (Continuum Damage Mechanics approach):
E2 = E20 * (1 - D2)
G12 = G120 * (1 - D6)
Where:
da/dN = C * (ΔK)^m
Where:
The concept of Critical Crack Density (CCD) is used to assess the significance of matrix cracking:
CCD = 1 / (2 * t * √(E2 / (G23 * (1 - ν23^2))))
Where:
For more information on matrix cracks and their effects, visit our Understanding Defects and Damage in Composite Materials and Structures page.
Delaminations are separations between adjacent plies and are among the most critical defects in laminated composites.
Compressive strength prediction (simplified):
σc = π^2 * E * (t_eff / L)^2
Where:
EI_eff = EI_total - EI_delaminated
da/dN = C * (ΔG)^m
Where:
Delamination Index (DI) concept:
DI = (a / W) * √(E11 / E22)
Where:
Critical DI values typically range from 0.5 to 2, depending on layup and loading.
To learn more about delaminations and their impact, check our Defects and Damage in Composite Materials and Structures article.
Fiber cuts and holes represent severe forms of damage in composites, directly affecting the load-bearing fibers.
Kt = 1 + √(2 * (√(E1/E2) - ν12) + E1/G12)
Where:
σN / σ0 = (1 - (R / (R + d0)))^-1/2
Where:
For more information on the impact of fiber cuts and holes, visit our Mechanical Testing of Composites page.
By understanding the impact of these defects on structural integrity, engineers can:
The interaction between different types of defects (e.g., matrix cracks leading to delaminations, which then interact with holes) often results in complex failure scenarios. Therefore, a holistic approach considering multiple defect types and their interactions is crucial for ensuring the structural integrity of composite components.
For further insights into designing composite structures with consideration for defects, check our Composites Structural Design article.
Effective repair of composite structures requires careful consideration of various criteria and design factors. This chapter explores the key aspects of repair design, including static strength and stability, durability and environmental factors, and aerodynamics and weight balance.
The primary goal of any repair is to restore the structural integrity of the component. This involves considerations of both strength and stability.
Tensile strength efficiency:
η = (σrepair / σoriginal) * 100%
Where:
Compressive strength prediction (simplified):
σc = k * (π^2 * E * t^2) / (12 * (1 - ν^2) * b^2)
Where:
Stiffness ratio:
SR = Erepair / Eoriginal
Where:
Aim for 0.8 ≤ SR ≤ 1.2 for most applications.
For more information on structural design considerations, visit our Structural Composites Design Concepts page.
Repairs must withstand long-term environmental exposure and cyclic loading.
Fatigue life prediction (S-N approach):
N = A * (Δσ)^-m
Where:
Moisture diffusion coefficient:
D = (π * h^2) / (16 * t0.5^2)
Where:
Coefficient of Thermal Expansion (CTE) mismatch:
Δε = (α1 - α2) * ΔT
Where:
To learn more about environmental considerations in composite repairs, check our Composite Repair article.
For aerospace applications, maintaining aerodynamic properties and weight balance is crucial.
Surface roughness effect on drag:
ΔCD = k * (R/c)^n
Where:
Moment change calculation:
ΔM = Δm * g * r
Where:
For more insights into aerodynamic considerations in composite design, visit our Applications and Limitations of Composite Materials in Aerospace Engineering page.
By carefully considering these repair criteria and design factors, engineers can ensure that composite repairs not only restore structural integrity but also maintain the overall performance characteristics of the component. The interplay between these various factors often requires a balanced approach and sometimes necessitates trade-offs between different performance aspects.
For further information on composite design and manufacturing considerations, check our Composites Design for Manufacturing course.
This chapter explores common repair designs used in composite structures, including filling/sealing repairs, doubler patch repairs, flush bonded repairs, and bolted repairs. Each repair type has its own advantages, limitations, and specific applications.
Filling/sealing repairs are typically used for minor damage that doesn't significantly affect structural integrity.
For more information on composite repair techniques, visit our Composite Repair page.
Doubler patch repairs involve bonding additional material over the damaged area to restore strength and stiffness.
Shear lag theory for load transfer:
τ(x) = P * (β/w) * (cosh(βx) / sinh(βL))
Where:
To learn more about non-destructive inspection methods for composite repairs, check our Non-Destructive Testing for Composites article.
Flush bonded repairs, including scarf and step-lap repairs, provide a smooth external surface and efficient load transfer.
σmax = 2 * τa * L / t
Where:
For more details on advanced composite manufacturing techniques, visit our Fundamentals of Composites Manufacturing page.
Bolted repairs use mechanical fasteners to join a repair patch to the parent structure.
P = σbr * d * t
Where:
To understand more about joining techniques in composites, check our Joining Composite Materials article.
In some cases, a combination of repair techniques may be used:
The choice of repair design depends on various factors including damage type and size, structural requirements, aerodynamic considerations, and available resources. Each repair type has its own advantages and limitations, and the selection should be based on a thorough engineering assessment.
For more information on composite design and manufacturing considerations, visit our Composites Design for Manufacturing course page.
Proper damage removal and surface preparation are crucial steps in ensuring the success and longevity of composite repairs. This chapter covers the key aspects of removing damaged material, moisture removal, and surface conditioning.
Proper removal of damaged material is crucial for effective composite repairs. The goal is to remove all compromised material while minimizing the removal of sound material.
For more information on damage assessment techniques, visit our Non-Destructive Testing for Composites page.
To learn more about composite repair techniques, check our Composite Repair article.
Moisture in composite materials can compromise repair integrity. Thorough drying is essential before repair application.
For more information on environmental effects on composites, visit our Challenges of Switching to Composite Materials page.
Proper surface conditioning ensures optimal adhesion for the repair patch or filler material.
For more insights into surface preparation techniques, check our Joining Composite Materials article.
Proper damage removal, moisture elimination, and surface conditioning are critical steps in ensuring the integrity and longevity of composite repairs. These processes set the foundation for successful adhesion and load transfer in the repaired structure. Careful attention to these preparatory steps can significantly enhance the overall quality and durability of the repair.
To learn more about composite manufacturing processes, visit our Fundamentals of Composites Manufacturing page.
Effective post-repair inspection and quality control are crucial for ensuring the integrity and longevity of composite repairs. This chapter explores various inspection techniques, non-destructive testing methods, and strategies for ensuring repair integrity.
Visual inspection is the first and most basic form of post-repair quality control. While limited to surface defects, it can provide valuable information about the repair quality.
For more information on visual inspection techniques, visit our Defects and Damage in Composite Materials and Structures page.
Non-Destructive Inspection (NDI) techniques are crucial for assessing the internal quality of composite repairs.
To learn more about NDI techniques for composites, check our Non-Destructive Testing for Composites: Different Inspection Methods article.
Ensuring the integrity of a composite repair involves a comprehensive approach combining inspection results with structural analysis and testing.
For more insights into composite repair and quality control, visit our Composite Repair page.
By implementing a thorough post-repair inspection and quality control process, the integrity and long-term performance of composite repairs can be ensured. This multi-faceted approach combines visual inspection, advanced NDI techniques, structural analysis, and ongoing monitoring to provide confidence in the repaired structure's ability to meet its design requirements throughout its service life.
To learn more about advanced manufacturing techniques and quality control in composites, check our Fundamentals of Composites Manufacturing article.