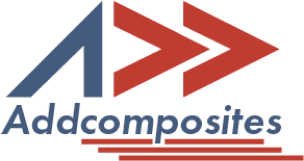
Simulating composite structures for cryogenic applications, such as those used in aerospace, introduces a unique set of challenges. These structures, critical in constructing cryogenic tanks, must endure extreme conditions that push the limits of current simulation technologies. The complexity arises from the need to accurately represent composite materials throughout the manufacturing process, which involves various thermomechanical processes critical to the final product's quality and performance.
During manufacturing, composite materials undergo processes that can induce defects such as porosities, misalignments of fibers, and incomplete curing. These defects significantly impact the materials' structural integrity and performance, making it crucial for simulations to predict these effects accurately. Moreover, simulating cryogenic conditions adds another layer of complexity. These conditions require the materials to withstand extremely low temperatures, which can drastically alter their physical properties and behavior.
Despite significant advancements in simulation technologies, there remains a notable gap in tools that can seamlessly predict the effects from the manufacturing phase through to the end-use conditions. Current simulations often fail to account fully for critical real-world operational stresses and conditions. This limitation highlights the need for more sophisticated modeling techniques that can integrate both micromechanical and macromechanical behaviors to enhance the accuracy of predictions and ensure that composite materials perform as expected under cryogenic conditions.
Current composite simulation practices face significant limitations when predicting the performance of materials under real-world conditions, particularly in the context of cryogenic applications such as those found in aerospace. These limitations arise from the complexities associated with the behavior of composite materials during manufacturing and their subsequent performance in operational environments. The key challenges include:
While current simulations provide a foundational understanding of composite behavior, they fall short in delivering the accuracy needed for high-stakes applications in cryogenic environments. This underscores the urgent need for more sophisticated modeling techniques that can bridge the gap between theoretical predictions and operational realities.
The integration of micromechanical and macromechanical models marks a significant advancement in the simulation of composite materials, particularly those used under cryogenic conditions. This approach addresses critical limitations of traditional simulations by providing a more nuanced understanding of material behavior from the microscale fiber-matrix interactions to the overall structural response at the macroscale. The key benefits of this integration include:
Despite the progress in integrating these models, challenges remain in fully realizing seamless multi-scale simulations. The complexity of accurately coupling the scales to reflect real-world manufacturing and operational conditions requires continuous refinement of simulation methodologies and tools.
A Multiscale Simulation Framework for Predicting Composite Performance in Cryogenic Tanks
-----------------------------------------------------------------------------------------
The development of a multiscale simulation framework for predicting the performance of composite materials in cryogenic tanks represents a groundbreaking advancement in the field of material science and engineering. This framework bridges the gap between the micromechanical scale, which focuses on fiber and matrix interactions, and the macromechanical scale, which considers the entire structural component under operational conditions. The key aspects of this framework include:
the multiscale simulation framework not only enhances the predictability and reliability of composite materials in cryogenic applications but also plays a vital role in reducing development costs and time. By providing a thorough understanding of material behavior across different scales, the framework ensures that the final products are both efficient and safe for their intended use, marking a significant step forward in the simulation-driven design of advanced composite materials.
We extend our heartfelt thanks to Paulo Reinier Teixeira Gonçalves, the primary author of the research detailed in "End-to-end simulation of composite structures: linking composites manufacturing and structural performance in cryogenic tanks". His pioneering work and dedication form the backbone of the simulation methodologies discussed in this blog. His doctoral dissertation under the guidance of Prof. PhD. Albertino Arteiro and co-supervision of PhD. Nuno Rocha at the Faculdade de Engenharia da Universidade do Porto has provided invaluable insights into the complexities of composite materials and their applications in cryogenic environments.
Special recognition is also due to the team at INEGI - Institute of Science and Innovation in Mechanical and Industrial Engineering, whose collaboration and support have been instrumental in advancing this research. Their commitment to pushing the boundaries of material science allows us to explore new horizons in aerospace and mechanical engineering.
We are also grateful to the financial backers from LAETA - Laboratório Associado de Energia, Transportes e Aeronáutica and the project UIDP/50022/2020 New Generation of Cryogenic Propulsion Systems for Future Launchers. Their support underscores the importance of this research in the development of future technologies and sustainable solutions.
Thank you to everyone involved for their hard work and persistence, which continue to inspire and drive progress in our industry.
Discover the future of composite manufacturing with Addcomposites! Here's how you can get involved:
At Addcomposites, we are dedicated to revolutionizing composite manufacturing. Our AFP systems and comprehensive support services are waiting for you to harness. So, don't wait – get started on your journey to the future of manufacturing today!
Simulating composite structures for cryogenic applications, such as those used in aerospace, introduces a unique set of challenges. These structures, critical in constructing cryogenic tanks, must endure extreme conditions that push the limits of current simulation technologies. The complexity arises from the need to accurately represent composite materials throughout the manufacturing process, which involves various thermomechanical processes critical to the final product's quality and performance.
During manufacturing, composite materials undergo processes that can induce defects such as porosities, misalignments of fibers, and incomplete curing. These defects significantly impact the materials' structural integrity and performance, making it crucial for simulations to predict these effects accurately. Moreover, simulating cryogenic conditions adds another layer of complexity. These conditions require the materials to withstand extremely low temperatures, which can drastically alter their physical properties and behavior.
Despite significant advancements in simulation technologies, there remains a notable gap in tools that can seamlessly predict the effects from the manufacturing phase through to the end-use conditions. Current simulations often fail to account fully for critical real-world operational stresses and conditions. This limitation highlights the need for more sophisticated modeling techniques that can integrate both micromechanical and macromechanical behaviors to enhance the accuracy of predictions and ensure that composite materials perform as expected under cryogenic conditions.
Current composite simulation practices face significant limitations when predicting the performance of materials under real-world conditions, particularly in the context of cryogenic applications such as those found in aerospace. These limitations arise from the complexities associated with the behavior of composite materials during manufacturing and their subsequent performance in operational environments. The key challenges include:
While current simulations provide a foundational understanding of composite behavior, they fall short in delivering the accuracy needed for high-stakes applications in cryogenic environments. This underscores the urgent need for more sophisticated modeling techniques that can bridge the gap between theoretical predictions and operational realities.
The integration of micromechanical and macromechanical models marks a significant advancement in the simulation of composite materials, particularly those used under cryogenic conditions. This approach addresses critical limitations of traditional simulations by providing a more nuanced understanding of material behavior from the microscale fiber-matrix interactions to the overall structural response at the macroscale. The key benefits of this integration include:
Despite the progress in integrating these models, challenges remain in fully realizing seamless multi-scale simulations. The complexity of accurately coupling the scales to reflect real-world manufacturing and operational conditions requires continuous refinement of simulation methodologies and tools.
A Multiscale Simulation Framework for Predicting Composite Performance in Cryogenic Tanks
-----------------------------------------------------------------------------------------
The development of a multiscale simulation framework for predicting the performance of composite materials in cryogenic tanks represents a groundbreaking advancement in the field of material science and engineering. This framework bridges the gap between the micromechanical scale, which focuses on fiber and matrix interactions, and the macromechanical scale, which considers the entire structural component under operational conditions. The key aspects of this framework include:
the multiscale simulation framework not only enhances the predictability and reliability of composite materials in cryogenic applications but also plays a vital role in reducing development costs and time. By providing a thorough understanding of material behavior across different scales, the framework ensures that the final products are both efficient and safe for their intended use, marking a significant step forward in the simulation-driven design of advanced composite materials.
We extend our heartfelt thanks to Paulo Reinier Teixeira Gonçalves, the primary author of the research detailed in "End-to-end simulation of composite structures: linking composites manufacturing and structural performance in cryogenic tanks". His pioneering work and dedication form the backbone of the simulation methodologies discussed in this blog. His doctoral dissertation under the guidance of Prof. PhD. Albertino Arteiro and co-supervision of PhD. Nuno Rocha at the Faculdade de Engenharia da Universidade do Porto has provided invaluable insights into the complexities of composite materials and their applications in cryogenic environments.
Special recognition is also due to the team at INEGI - Institute of Science and Innovation in Mechanical and Industrial Engineering, whose collaboration and support have been instrumental in advancing this research. Their commitment to pushing the boundaries of material science allows us to explore new horizons in aerospace and mechanical engineering.
We are also grateful to the financial backers from LAETA - Laboratório Associado de Energia, Transportes e Aeronáutica and the project UIDP/50022/2020 New Generation of Cryogenic Propulsion Systems for Future Launchers. Their support underscores the importance of this research in the development of future technologies and sustainable solutions.
Thank you to everyone involved for their hard work and persistence, which continue to inspire and drive progress in our industry.
Discover the future of composite manufacturing with Addcomposites! Here's how you can get involved:
At Addcomposites, we are dedicated to revolutionizing composite manufacturing. Our AFP systems and comprehensive support services are waiting for you to harness. So, don't wait – get started on your journey to the future of manufacturing today!