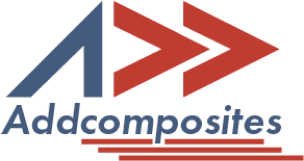
Composite material is a material made up of various recognizable individual components. They can either be naturally occurring or man-made, which ultimately creates a part that is much stronger than each individual component on its own, usually a reinforcement and a matrix.
3D printing enables the manufacturing process to be automated since the entire process is driven by software and requires manual input only at the post-processing stage.
In 3D printing, it’s possible to print with two reinforcement types of fiber, chopped and continuous. In the case of chopped fiber, small strands, less than a millimeter in length, are integrated into the polymer material. The percentage of fiber used, and the base thermoplastic determines how strong the final part is. In the case of continuous fiber, long strands of fiber are mixed with a thermoplastic, like PLA, ABS, Nylon, PETG, and PEEK during the printing process. Parts 3D-printed with continuous fiber are extremely lightweight, yet as strong as metal. In terms of types of fibers used, carbon fiber is one of the most popular, followed by fiberglass and Kevlar.
In 2020, the market for composite 3D printing remains young, with only a handful of companies offering composite 3D printing solutions. Most 3D printers capable of processing composite materials are based on the polymer-extrusion process, known as Fused Filament Fabrication (FFF). In FFF, a nozzle is moving above the build platform, extruding a melted thread of plastic, called a filament, and creating an object layer-by-layer. 3D printing of filaments containing chopped fibers is straightforward, only requiring a hardened steel nozzle to resist abrasive fiber strands. However, when it comes to continuous fiber printing, the FFF process will require a second nozzle to separately deposit a single, uninterrupted strand of fiber.
Although the additive manufacturing of polymer matrix composites has gone through a significant improvement in recent years, it is still not widely adopted by various industrial sectors for functional applications. Several limitations that need to be overcome are demonstrated in Figure 1 below. These problems are very similar to other AM techniques, such as direct metal laser sintering, which are more mature and overcome these restrictions for a wider infusion into the industry. There is a wide application of AM, and the amount of interest in industry and academia for producing polymer matrix composites has been growing significantly, and this is expected to continue exponentially in the coming years.
Figure 1: Limitations of the AM of polymer matrix composites similar to other materials in their development phases
Despite being a young technology, composite 3D printing is gaining a stronger foothold within the manufacturing industry. It offers a faster and more automated approach to producing composite parts, which for a long time have been handmade. Composite 3D printing helps in rethinking the material choice for certain applications, allowing manufacturers to replace metal with durable, cheaper plastic. Finally, it helps to make the process of manufacturing composite parts less expensive. Combined, these benefits suggest that composite 3D printing will only be growing and maturing to become a standard method in the composite manufacturer’s toolbox.
Composite 3D Printing: An Emerging Technology with a Bright Future
Addcomposites is the provider of the Automated Fiber Placement (AFP) system. The AFP system provided by Addcomposites can be rented on a monthly basis to work with thermosets, thermoplastic, dry fiber placement, or in combination with 3d printers.
Composite material is a material made up of various recognizable individual components. They can either be naturally occurring or man-made, which ultimately creates a part that is much stronger than each individual component on its own, usually a reinforcement and a matrix.
3D printing enables the manufacturing process to be automated since the entire process is driven by software and requires manual input only at the post-processing stage.
In 3D printing, it’s possible to print with two reinforcement types of fiber, chopped and continuous. In the case of chopped fiber, small strands, less than a millimeter in length, are integrated into the polymer material. The percentage of fiber used, and the base thermoplastic determines how strong the final part is. In the case of continuous fiber, long strands of fiber are mixed with a thermoplastic, like PLA, ABS, Nylon, PETG, and PEEK during the printing process. Parts 3D-printed with continuous fiber are extremely lightweight, yet as strong as metal. In terms of types of fibers used, carbon fiber is one of the most popular, followed by fiberglass and Kevlar.
In 2020, the market for composite 3D printing remains young, with only a handful of companies offering composite 3D printing solutions. Most 3D printers capable of processing composite materials are based on the polymer-extrusion process, known as Fused Filament Fabrication (FFF). In FFF, a nozzle is moving above the build platform, extruding a melted thread of plastic, called a filament, and creating an object layer-by-layer. 3D printing of filaments containing chopped fibers is straightforward, only requiring a hardened steel nozzle to resist abrasive fiber strands. However, when it comes to continuous fiber printing, the FFF process will require a second nozzle to separately deposit a single, uninterrupted strand of fiber.
Although the additive manufacturing of polymer matrix composites has gone through a significant improvement in recent years, it is still not widely adopted by various industrial sectors for functional applications. Several limitations that need to be overcome are demonstrated in Figure 1 below. These problems are very similar to other AM techniques, such as direct metal laser sintering, which are more mature and overcome these restrictions for a wider infusion into the industry. There is a wide application of AM, and the amount of interest in industry and academia for producing polymer matrix composites has been growing significantly, and this is expected to continue exponentially in the coming years.
Figure 1: Limitations of the AM of polymer matrix composites similar to other materials in their development phases
Despite being a young technology, composite 3D printing is gaining a stronger foothold within the manufacturing industry. It offers a faster and more automated approach to producing composite parts, which for a long time have been handmade. Composite 3D printing helps in rethinking the material choice for certain applications, allowing manufacturers to replace metal with durable, cheaper plastic. Finally, it helps to make the process of manufacturing composite parts less expensive. Combined, these benefits suggest that composite 3D printing will only be growing and maturing to become a standard method in the composite manufacturer’s toolbox.
Composite 3D Printing: An Emerging Technology with a Bright Future
Addcomposites is the provider of the Automated Fiber Placement (AFP) system. The AFP system provided by Addcomposites can be rented on a monthly basis to work with thermosets, thermoplastic, dry fiber placement, or in combination with 3d printers.