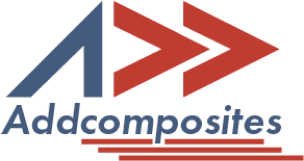
The necessity of high-performance materials has become latent in high technology sectors such as aerospace, automotive, renewable energy, and sports. The expanding impact on future manufacturing of waste management legislation and increasing the price of current waste management methods stress the importance of an efficient and sustainable way of recycling waste generated in the composites industry.
Aerospace companies estimated that 30–50% of materials in aircraft production are scrapped due to the way it is manufactured. Companies need to pay for landfilling the composite materials that otherwise can be a valuable resource. In a view that looking at individual production waste outputs could maximize the material reuse or recycling capability, gaining information about the type of scrap materials could inform the development of a composite reuse/recycling supply chain.
This blog focuses on understanding the scale of scrap created in individual composites manufacturing processes to assess its potential value in terms of reuse/recycle capabilities.
The waste hierarchy presented in the EU Waste Framework Directive released in 2008, introduces a scale to classify the different types of waste into five levels according to their management procedures:
Figure 1. EU waste framework
Tools for resource flow mapping are widely used for manufacturing optimization. Process mapping allows us to realize the current scenario and act as a benchmark for improvement activities. Process mapping tools have been used to identify waste that is ‘most suitable for transformation'. This suggests that process mapping is concentrating on waste where the potential of maximization of value from transforming waste is possible.
Figure 2. Process Mapping for Tracking Waste
Four open-ended questions are answered regarding the key manufacturing process that helps establish the view on improvement potential. It also serves to act as a trigger for different points of innovation in recyclability from the manufacturing process:
We answer the questions above from the viewpoint of implementing an AFP system to address these concerns.
What would you change in this process?
AFP offers the distinct benefit of using the least amount of material possible to achieve near net-shaped layups. This is possible because the fiber width being placed in AFP is only 1/4" - 2" wide, and so less material extends past the EOP during layup.
What scrap has reuse potential? In which industry?
Cured material can be ground and reused in the construction industry. If fibers could be extracted, they could be reused to produce non-primary structures, such as materials with thermoplastic matrices.
What scrap/waste do you think could be easily reduced? How?
As the scrap from AFP is clean, non-cured prepreg, it could be used as reinforcement as virgin fiber in bulk molding compound or SMC.
What innovation do you think should happen?
Two innovation areas were identified: autoclave multifunction and parallel production capabilities and automation of simple parts making.
These questions are now answered from the viewpoint of performing the hand layup process.
What would you change in this process?
Automating the process could help in reducing the material usage in the process. specifically for highly complex geometry that performs production to near net shape using an automated process
What scrap has reuse potential? In which industry?
Since the material used in hand layup is the generally dry fiber that gets infused later, there is a lot of potential reuse in the scrap produced. One example explored could be DMC/SMC modeling for low aesthetic products – i.e. pipes, underground tanks, etc.
What scrap/waste do you think could be easily reduced? How?
Using the optimal amount of resin for production, as well as performing defect elimination exercises to minimize rejects.
What innovation do you think should happen?
Complete automation of the process innovation that is able to produce highly complex customized parts.
Through research, it has been clear that although the exercise allows capturing the percentage of material used in the production vs scrap, it only suggests the efficiency of the production line itself. However, the data collected does not indicate the actual amount of material that is wasted and does not provide an idea of volume.
Figure 3. Waste comparison between AFP and Hand Layup
Reincorporating carbon fiber reinforced plastics (CFRP) and glass fiber reinforced plastics (GFRP) into a different range of products in a form of fiber or powder (where resin and powder mix is used) has been demonstrated in construction, products for automotive, electronics and SMC manufacturing.
Figure 4. Lists of Recycling Methods
Monitoring and management for both minimizations of waste and selection of appropriate downstream processing of composite waste can be achieved through the application of the methodology using the presented framework. Wider adoption of the methodology could help in reducing the manufacturing waste generated by the industry, and of course, bring environmental and economic benefits.
Following all the regulations about tracking and reducing waste above, the manufacturers in many industries want to decrease the unsustainable process with a much larger carbon footprint. Understanding the rising demand, Addcomposites announced the open access to AFP Programming and Simulation software - AddPath for anyone to create programs and perform simulations for AFP on their personal or work computers, enabling digital composites additive manufacturing from home or the office.
Figure 5. AddPath Interface
The solution offers the designers and manufacturers to go through the rigor of designing a part for manufacturability which includes mentioned points below to reduce the wastes in composites manufacturing.
You can download the AddPath now by following the instructions here.
The blog is a summary of a recently published research article "Capturing composites manufacturing waste flows through process mapping"
Addcomposites is the provider of the Automated Fiber Placement (AFP) ecosystem - including the Fiber Placement System (AFP-XS), 3D Simulation and Programming Software (AddPath), and Robotic Cells (AddCell). With the leasing program for the AFP system (AFPnext), composites manufacturers can work with thermosets, thermoplastics, dry fiber placement, or in combination with 3D Printers on a monthly basis.
The necessity of high-performance materials has become latent in high technology sectors such as aerospace, automotive, renewable energy, and sports. The expanding impact on future manufacturing of waste management legislation and increasing the price of current waste management methods stress the importance of an efficient and sustainable way of recycling waste generated in the composites industry.
Aerospace companies estimated that 30–50% of materials in aircraft production are scrapped due to the way it is manufactured. Companies need to pay for landfilling the composite materials that otherwise can be a valuable resource. In a view that looking at individual production waste outputs could maximize the material reuse or recycling capability, gaining information about the type of scrap materials could inform the development of a composite reuse/recycling supply chain.
This blog focuses on understanding the scale of scrap created in individual composites manufacturing processes to assess its potential value in terms of reuse/recycle capabilities.
The waste hierarchy presented in the EU Waste Framework Directive released in 2008, introduces a scale to classify the different types of waste into five levels according to their management procedures:
Figure 1. EU waste framework
Tools for resource flow mapping are widely used for manufacturing optimization. Process mapping allows us to realize the current scenario and act as a benchmark for improvement activities. Process mapping tools have been used to identify waste that is ‘most suitable for transformation'. This suggests that process mapping is concentrating on waste where the potential of maximization of value from transforming waste is possible.
Figure 2. Process Mapping for Tracking Waste
Four open-ended questions are answered regarding the key manufacturing process that helps establish the view on improvement potential. It also serves to act as a trigger for different points of innovation in recyclability from the manufacturing process:
We answer the questions above from the viewpoint of implementing an AFP system to address these concerns.
What would you change in this process?
AFP offers the distinct benefit of using the least amount of material possible to achieve near net-shaped layups. This is possible because the fiber width being placed in AFP is only 1/4" - 2" wide, and so less material extends past the EOP during layup.
What scrap has reuse potential? In which industry?
Cured material can be ground and reused in the construction industry. If fibers could be extracted, they could be reused to produce non-primary structures, such as materials with thermoplastic matrices.
What scrap/waste do you think could be easily reduced? How?
As the scrap from AFP is clean, non-cured prepreg, it could be used as reinforcement as virgin fiber in bulk molding compound or SMC.
What innovation do you think should happen?
Two innovation areas were identified: autoclave multifunction and parallel production capabilities and automation of simple parts making.
These questions are now answered from the viewpoint of performing the hand layup process.
What would you change in this process?
Automating the process could help in reducing the material usage in the process. specifically for highly complex geometry that performs production to near net shape using an automated process
What scrap has reuse potential? In which industry?
Since the material used in hand layup is the generally dry fiber that gets infused later, there is a lot of potential reuse in the scrap produced. One example explored could be DMC/SMC modeling for low aesthetic products – i.e. pipes, underground tanks, etc.
What scrap/waste do you think could be easily reduced? How?
Using the optimal amount of resin for production, as well as performing defect elimination exercises to minimize rejects.
What innovation do you think should happen?
Complete automation of the process innovation that is able to produce highly complex customized parts.
Through research, it has been clear that although the exercise allows capturing the percentage of material used in the production vs scrap, it only suggests the efficiency of the production line itself. However, the data collected does not indicate the actual amount of material that is wasted and does not provide an idea of volume.
Figure 3. Waste comparison between AFP and Hand Layup
Reincorporating carbon fiber reinforced plastics (CFRP) and glass fiber reinforced plastics (GFRP) into a different range of products in a form of fiber or powder (where resin and powder mix is used) has been demonstrated in construction, products for automotive, electronics and SMC manufacturing.
Figure 4. Lists of Recycling Methods
Monitoring and management for both minimizations of waste and selection of appropriate downstream processing of composite waste can be achieved through the application of the methodology using the presented framework. Wider adoption of the methodology could help in reducing the manufacturing waste generated by the industry, and of course, bring environmental and economic benefits.
Following all the regulations about tracking and reducing waste above, the manufacturers in many industries want to decrease the unsustainable process with a much larger carbon footprint. Understanding the rising demand, Addcomposites announced the open access to AFP Programming and Simulation software - AddPath for anyone to create programs and perform simulations for AFP on their personal or work computers, enabling digital composites additive manufacturing from home or the office.
Figure 5. AddPath Interface
The solution offers the designers and manufacturers to go through the rigor of designing a part for manufacturability which includes mentioned points below to reduce the wastes in composites manufacturing.
You can download the AddPath now by following the instructions here.
The blog is a summary of a recently published research article "Capturing composites manufacturing waste flows through process mapping"
Addcomposites is the provider of the Automated Fiber Placement (AFP) ecosystem - including the Fiber Placement System (AFP-XS), 3D Simulation and Programming Software (AddPath), and Robotic Cells (AddCell). With the leasing program for the AFP system (AFPnext), composites manufacturers can work with thermosets, thermoplastics, dry fiber placement, or in combination with 3D Printers on a monthly basis.