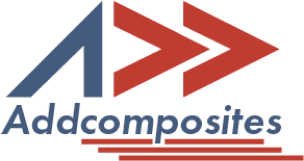
Composite isogrid structures have emerged as a transformative solution in aerospace, automotive, and advanced engineering applications due to their exceptional strength-to-weight ratios, damage tolerance, and structural efficiency. These lattice-like configurations, characterized by triangular rib patterns, outperform traditional sandwich structures and aluminum isogrids by combining lightweight design with isotropic mechanical behavior 1 6 13. Recent advancements in automated fiber placement (AFP), filament winding, and continuous fiber 3D printing have further enhanced their manufacturability, enabling cost-effective production of complex geometries. This report examines the rationale behind the preference for isogrid structures and explores the technical nuances of their fabrication using modern manufacturing technologies.
The triangular isogrid pattern mimics isotropic material behavior by evenly distributing mechanical loads across its lattice 1 3. Unlike conventional honeycomb cores, which rely on shear transfer through adhesive bonds, composite isogrid ribs integrally connect to the skin, eliminating delamination risks while maintaining stiffness. Studies demonstrate that isogrid panels achieve 20–30% weight reduction compared to aluminum counterparts while matching or exceeding their buckling resistance 6 8. The repetitive rib-skin architecture also provides redundancy, allowing localized damage (e.g., impact-induced rib fractures) to remain contained within individual cells without catastrophic failure 9 13.
Composite isogrids exhibit superior performance in hostile environments. Open lattice structures prevent moisture retention—a critical flaw in honeycomb sandwiches where water ingress accelerates corrosion 9. Thermal stability is enhanced through tailored coefficient of thermal expansion (CTE) matching between ribs and skins. For instance, hybrid molds combining aluminum and Teflon optimize compaction during curing by exploiting differing CTEs, ensuring dimensional precision under thermal cycling 1.
Isogrids adapt to diverse geometries, from parabolic antenna reflectors to cylindrical rocket fuselages 4 12. Automated processes like AFP and filament winding enable rapid production of curved and flat panels with minimal manual intervention, reducing labor costs by up to 40% compared to hand-laid composites 6 12.
AFP employs robotic systems to lay continuous prepreg tows (typically 3.2–12.7 mm wide) into predefined helical or axial grooves. A multi-axis gantry guides the placement head, ensuring precise fiber orientation aligned with principal stress directions 6 12. Post-deposition, circumferential skin layers are wound over the ribs, and the assembly is vacuum-bagged and cured in autoclaves 8.
EADS CASA Espacio demonstrated AFP’s scalability by fabricating 4-meter-diameter isogrid cylinders for satellite launch vehicles. Using Toray T800H/3900-2 carbon-epoxy prepreg, the process achieved a fiber volume fraction of 58% with ±1° angular accuracy. Post-cure ultrasonic testing revealed <0.5% void content, meeting aerospace-grade standards 8 12.
Filament winding constructs isogrids by depositing continuous fibers (wet or pre-impregnated) into machined mandrel grooves. After filling the grooves, a secondary skin layer is wound over the structure, and the entire assembly is co-cured 3 11.
Wet filament-wound isogrids exhibit 10–15% higher interlaminar shear strength than AFP-manufactured counterparts due to optimized resin infusion. A study by CETMA and COMEC produced epoxy-based isogrid panels with 320 MPa compressive strength—comparable to aluminum 6061-T6—at 40% lower weight 1 11.
Additive manufacturing systems like the Anisoprint Composer A3 co-extrude thermoplastics (e.g., PA6) and continuous carbon fiber tows pre-impregnated with thermoset binders. Layer-by-layer deposition builds isogrid lattices with programmable infill densities (10–80%) 2 10 15.
Roboze’s FFF-based Carbon PA (20% short carbon fiber-reinforced polyamide) produced isogrid panels with specific buckling loads of 0.31 kN/g. Optimized parameters (240°C extrusion, 70°C bed temperature) minimized warping, achieving ±0.1 mm dimensional accuracy 5 15.
Composite isogrid structures represent a paradigm shift in lightweight design, offering unmatched strength-to-weight ratios and environmental resilience. AFP and filament winding provide industry-proven solutions for large-scale production, whereas continuous fiber 3D printing democratizes access to isogrid fabrication for SMEs and research institutions. Future advancements in hybrid manufacturing—combining AFP’s precision with additive manufacturing’s flexibility—promise to further reduce costs and expand applications into renewable energy and automotive sectors. As demonstrated by CETMA, COMEC, and Anisoprint, ongoing innovation in tooling and material systems will solidify isogrids as a cornerstone of next-generation composite engineering 1 2 15.