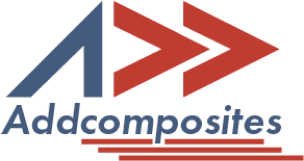
When selecting an Automated Fiber Placement (AFP) system, it's crucial to consider several factors to ensure it aligns with your specific requirements. Here's a structured guide to help you make an informed decision:
AFP-XS by Addcomposites: This system is versatile, capable of handling all the above materials. It features built-in cooling and IR heating for thermoset prepreg and can integrate external heaters for thermoplastic placement.
AFP-XS by Addcomposites provide a combination of all AFP, ATL and Filament winding into one. This is possible due to thestandard systems capability to support any width between 5 - 25 mm ( 50 mm possible on requests) thus allowing faster and finer opertions as needed for the shape. In addition the system has capability to work as thermoplastic and thermoset winder, in this mode the AFP does not in contact with mold/mandrel and able wind to very sharp concave shapes similar to winding
The application of heat is pivotal in ensuring the proper adhesion of incoming tows to the substrate. This heat is supplied by a device known as a "heater" that's mounted to the AFP head. Various heating systems are available, each with its unique characteristics and applications:
Heat is essential for achieving the right tackiness. AFP-XS by Addcomposites comes standard with IR heaters and is compatible with all of the above-mentioned external heaters. As mentioned each heating system does have their pro and cons thus its best to define the application very well before deciding on the right heating technology.
When it comes to Automated Fiber Placement (AFP) machines, the choice of motion platform is crucial. The type of machine selected largely depends on the size and shape of the part being manufactured. Here's a breakdown of the primary types of AFP machines and their applications:
Traditionally, AFP systems were either gantry or robotic style platforms, and they were shipped as a single unit with the AFP preattached to the CNC or robot. This made them expensive and challenging to install. However, the AFP-XS by Addcomposites revolutionizes this approach. It's designed as a plug-and-play unit, compatible with various industrial robots like Kuka, ABB, Fanuc, and Kawasaki. This not only reduces costs but also ensures there's no compromise in quality, thanks to Addcomposites' proprietary technology.
The success of Automated Fiber Placement (AFP) operations hinges significantly on the software used. It acts as the bridge connecting design, manufacturing, and quality control. Here's a detailed look into the process planning phase and the importance of integrated software:
Before the actual AFP layup, a process planning phase is essential. This phase involves:
Choosing software not provided by the AFP system's OEM can lead to integration issues, making the entire system inefficient. AFP-XS by Addcomposites addresses this concern by including its proprietary software, AddPath.
By integrating the right software and understanding the intricacies of process planning, manufacturers can ensure optimal outcomes in AFP operations.
Discover the future of composite manufacturing with Addcomposites! Here's how you can get involved:
At Addcomposites, we are dedicated to revolutionizing composite manufacturing. Our AFP systems and comprehensive support services are waiting for you to harness. So, don't wait – get started on your journey to the future of manufacturing today!
When selecting an Automated Fiber Placement (AFP) system, it's crucial to consider several factors to ensure it aligns with your specific requirements. Here's a structured guide to help you make an informed decision:
AFP-XS by Addcomposites: This system is versatile, capable of handling all the above materials. It features built-in cooling and IR heating for thermoset prepreg and can integrate external heaters for thermoplastic placement.
AFP-XS by Addcomposites provide a combination of all AFP, ATL and Filament winding into one. This is possible due to thestandard systems capability to support any width between 5 - 25 mm ( 50 mm possible on requests) thus allowing faster and finer opertions as needed for the shape. In addition the system has capability to work as thermoplastic and thermoset winder, in this mode the AFP does not in contact with mold/mandrel and able wind to very sharp concave shapes similar to winding
The application of heat is pivotal in ensuring the proper adhesion of incoming tows to the substrate. This heat is supplied by a device known as a "heater" that's mounted to the AFP head. Various heating systems are available, each with its unique characteristics and applications:
Heat is essential for achieving the right tackiness. AFP-XS by Addcomposites comes standard with IR heaters and is compatible with all of the above-mentioned external heaters. As mentioned each heating system does have their pro and cons thus its best to define the application very well before deciding on the right heating technology.
When it comes to Automated Fiber Placement (AFP) machines, the choice of motion platform is crucial. The type of machine selected largely depends on the size and shape of the part being manufactured. Here's a breakdown of the primary types of AFP machines and their applications:
Traditionally, AFP systems were either gantry or robotic style platforms, and they were shipped as a single unit with the AFP preattached to the CNC or robot. This made them expensive and challenging to install. However, the AFP-XS by Addcomposites revolutionizes this approach. It's designed as a plug-and-play unit, compatible with various industrial robots like Kuka, ABB, Fanuc, and Kawasaki. This not only reduces costs but also ensures there's no compromise in quality, thanks to Addcomposites' proprietary technology.
The success of Automated Fiber Placement (AFP) operations hinges significantly on the software used. It acts as the bridge connecting design, manufacturing, and quality control. Here's a detailed look into the process planning phase and the importance of integrated software:
Before the actual AFP layup, a process planning phase is essential. This phase involves:
Choosing software not provided by the AFP system's OEM can lead to integration issues, making the entire system inefficient. AFP-XS by Addcomposites addresses this concern by including its proprietary software, AddPath.
By integrating the right software and understanding the intricacies of process planning, manufacturers can ensure optimal outcomes in AFP operations.
Discover the future of composite manufacturing with Addcomposites! Here's how you can get involved:
At Addcomposites, we are dedicated to revolutionizing composite manufacturing. Our AFP systems and comprehensive support services are waiting for you to harness. So, don't wait – get started on your journey to the future of manufacturing today!