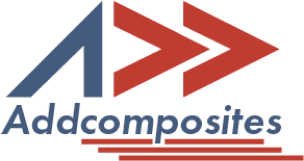
The blog highlights the source of challenges in being able to design composites suitable for automated manufacturing with DFM considerations.
DFM - Design For Manufacturing
As discussed in the previous blog, designers consider specific material, and fabrication limitations when creating designs. To know all about critical design parameters, material parameters, geometric constraints, etc. at an early stage is almost impossible. Thus, A lot of design decisions can not be made during the early stages as there are many unknowns, which leads to
There are numerous reasons why engineers pursue the black metal design approach. For one, the established guidelines make the design process straightforward. The challenge is that assessing the strength of a composite structure is more complex than assessing the strength of a metal structure. This is because the layered composites are made out of multiple plies, each with different spatial extents and angles.
The DFM process requires manufacturing constraints to be known at the time of design creation, which leads to two challenges for composites
Understanding the above-specified challenges provides a good grounding for the problem at hand. In the upcoming blogs, we will dig deeper into the state-of-the-art solution available to such challenges.
Addcomposites is the provider of the Automated Fiber Placement (AFP) ecosystem - including the Fiber Placement System (AFP-XS), 3D Simulation and Programming Software (AddPath), and Robotic Cells (AddCell). With the leasing program for the AFP system (AFPnext), composites manufacturers can work with thermosets, thermoplastics, dry fiber placement, or in combination with 3D Printers on a monthly basis.
Design for Automated Manufacture of Composite Structures
Design and Manufacturing Guideline for Aerospace Composites
Design tool for fiber-reinforced polymer structures
Carbon Fiber Composite Design Guide
The blog highlights the source of challenges in being able to design composites suitable for automated manufacturing with DFM considerations.
DFM - Design For Manufacturing
As discussed in the previous blog, designers consider specific material, and fabrication limitations when creating designs. To know all about critical design parameters, material parameters, geometric constraints, etc. at an early stage is almost impossible. Thus, A lot of design decisions can not be made during the early stages as there are many unknowns, which leads to
There are numerous reasons why engineers pursue the black metal design approach. For one, the established guidelines make the design process straightforward. The challenge is that assessing the strength of a composite structure is more complex than assessing the strength of a metal structure. This is because the layered composites are made out of multiple plies, each with different spatial extents and angles.
The DFM process requires manufacturing constraints to be known at the time of design creation, which leads to two challenges for composites
Understanding the above-specified challenges provides a good grounding for the problem at hand. In the upcoming blogs, we will dig deeper into the state-of-the-art solution available to such challenges.
Addcomposites is the provider of the Automated Fiber Placement (AFP) ecosystem - including the Fiber Placement System (AFP-XS), 3D Simulation and Programming Software (AddPath), and Robotic Cells (AddCell). With the leasing program for the AFP system (AFPnext), composites manufacturers can work with thermosets, thermoplastics, dry fiber placement, or in combination with 3D Printers on a monthly basis.
Design for Automated Manufacture of Composite Structures
Design and Manufacturing Guideline for Aerospace Composites
Design tool for fiber-reinforced polymer structures
Carbon Fiber Composite Design Guide