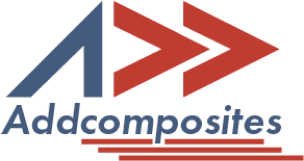
In the realm of high-performance materials, poly(aryletherketone)s (PAEKs), notably Poly(etherketoneketone) (PEKK), stand out for their superior mechanical properties, chemical resistance, and thermal stability. These materials have carved their niche in the aerospace industry, finding applications in structural parts like wing flaps, access panels, and floor panels. The allure of PEKK stems not only from its robust performance under demanding conditions but also from the diversity of grades available, each tailored for specific applications. This adaptability, however, comes with its own set of challenges, particularly when it comes to manufacturing processes like Automated Tape Placement (ATP).
ATP represents a leap forward in manufacturing efficiency, offering rapid production rates, automation, and high repeatability. Yet, the very speed that makes ATP attractive introduces complexities in achieving consistent crystallinity across composite parts. Crystallinity, or the degree of molecular order within the polymer, is a critical factor influencing a composite's mechanical, thermal, and chemical properties. Achieving uniform crystallinity is paramount, especially for semicrystalline thermoplastics like PEKK, where it dictates the final part's performance and reliability.
The challenge lies in the ATP process's inherent nature, where materials are subjected to high temperatures and pressures but for a limited duration. This constrained time frame can hinder the development of desired crystallinity levels, potentially compromising part quality and performance. The quest for uniform crystallinity across the thickness of CF/PEKK laminates manufactured via ATP is not just an academic pursuit but a pressing industrial need, highlighting the necessity for a deep dive into the crystallization kinetics and morphology of CF/PEKK composites.
This blog embarks on exploring these intricate details, aiming to shed light on the complexities of manufacturing high-performance thermoplastic composites through ATP. By delving into the crystallinity gradients and their implications on material properties, we aim to navigate through the challenges and uncover solutions that could revolutionize the manufacturing process, ensuring that the potential of PEKK composites is fully realized in high-stakes applications.
The pursuit of uniform crystallinity in high-performance thermoplastic composites like PEKK, particularly when manufactured through Automated Tape Placement (ATP), unveils a complex interplay between processing conditions and material properties. This section delves into the challenges of controlling crystallinity during manufacturing and its significant implications on composite strength, durability, and overall performance, shedding light on a critical issue for industry stakeholders.
In the journey to unravel the complexities of crystallinity in PEKK composites, this research employs state-of-the-art techniques such as Differential Scanning Calorimetry (DSC) and Scanning Electron Microscopy (SEM), enabling an in-depth analysis of the crystallization behavior and morphology of PEKK and its composites.
SEM analysis complements the DSC studies by offering a microscopic view of the material's morphology. This technique was particularly instrumental in examining the interfacial adhesion and matrix morphology post-cryofracture, highlighting the influence of crystallinity on the composite's mechanical integrity. By sputter coating the samples with gold to enhance conductivity, SEM images reveal intricate details about the crystalline structures and void content, providing a qualitative assessment of failure behaviors and the underlying crystallization morphology.
Through these innovative research methods, the study provides a comprehensive understanding of the crystallization kinetics and morphology of CF/PEKK composites. The findings underscore the significance of controlling processing conditions to achieve desired crystallinity levels, ultimately influencing the mechanical properties and performance of the composites. This research approach not only advances our knowledge of PEKK composites but also sets a foundation for optimizing manufacturing parameters in high-performance applications.
The comprehensive study of crystallinity gradients in CF/PEKK laminates manufactured via Automated Tape Placement (ATP) has unveiled significant findings that stand to revolutionize the manufacturing of thermoplastic composites. This section highlights the key discoveries, including crystallization kinetics and modeling, and explores how these insights pave the way for enhanced manufacturing techniques and material quality.
These findings equip manufacturers with the knowledge to fine-tune ATP processing parameters, thereby optimizing the crystallinity and, consequently, the mechanical properties of CF/PEKK composite parts.
This research provides a clearer understanding of the crystallization behavior of CF/PEKK composites, marking a milestone in the pursuit of manufacturing excellence in thermoplastic composites. By translating these scientific insights into practical applications, the path is set for the development of next-generation thermoplastic composites that meet the demanding requirements of high-performance applications.
We extend our deepest gratitude to Helena Pérez Martín for her pioneering research on crystallinity gradients in high-performance thermoplastic composites manufactured by automated tape placement. Her doctoral thesis "Studying Crystallinity Gradients in High
Performance Thermoplastic Composites Manufactured by Automated Tape Placement" provides invaluable insights into the complexities of material science and has greatly enriched the content of this blog. Helena's dedication to advancing our understanding of thermoplastic composites has not only paved the way for future innovations in aerospace manufacturing but also inspired countless professionals and enthusiasts in the field of materials science. Thank you, Helena Pérez Martín, for your significant contribution to the world of high-performance composites.
Discover the future of composite manufacturing with Addcomposites! Here's how you can get involved:
At Addcomposites, we are dedicated to revolutionizing composite manufacturing. Our AFP systems and comprehensive support services are waiting for you to harness. So, don't wait – get started on your journey to the future of manufacturing today!
In the realm of high-performance materials, poly(aryletherketone)s (PAEKs), notably Poly(etherketoneketone) (PEKK), stand out for their superior mechanical properties, chemical resistance, and thermal stability. These materials have carved their niche in the aerospace industry, finding applications in structural parts like wing flaps, access panels, and floor panels. The allure of PEKK stems not only from its robust performance under demanding conditions but also from the diversity of grades available, each tailored for specific applications. This adaptability, however, comes with its own set of challenges, particularly when it comes to manufacturing processes like Automated Tape Placement (ATP).
ATP represents a leap forward in manufacturing efficiency, offering rapid production rates, automation, and high repeatability. Yet, the very speed that makes ATP attractive introduces complexities in achieving consistent crystallinity across composite parts. Crystallinity, or the degree of molecular order within the polymer, is a critical factor influencing a composite's mechanical, thermal, and chemical properties. Achieving uniform crystallinity is paramount, especially for semicrystalline thermoplastics like PEKK, where it dictates the final part's performance and reliability.
The challenge lies in the ATP process's inherent nature, where materials are subjected to high temperatures and pressures but for a limited duration. This constrained time frame can hinder the development of desired crystallinity levels, potentially compromising part quality and performance. The quest for uniform crystallinity across the thickness of CF/PEKK laminates manufactured via ATP is not just an academic pursuit but a pressing industrial need, highlighting the necessity for a deep dive into the crystallization kinetics and morphology of CF/PEKK composites.
This blog embarks on exploring these intricate details, aiming to shed light on the complexities of manufacturing high-performance thermoplastic composites through ATP. By delving into the crystallinity gradients and their implications on material properties, we aim to navigate through the challenges and uncover solutions that could revolutionize the manufacturing process, ensuring that the potential of PEKK composites is fully realized in high-stakes applications.
The pursuit of uniform crystallinity in high-performance thermoplastic composites like PEKK, particularly when manufactured through Automated Tape Placement (ATP), unveils a complex interplay between processing conditions and material properties. This section delves into the challenges of controlling crystallinity during manufacturing and its significant implications on composite strength, durability, and overall performance, shedding light on a critical issue for industry stakeholders.
In the journey to unravel the complexities of crystallinity in PEKK composites, this research employs state-of-the-art techniques such as Differential Scanning Calorimetry (DSC) and Scanning Electron Microscopy (SEM), enabling an in-depth analysis of the crystallization behavior and morphology of PEKK and its composites.
SEM analysis complements the DSC studies by offering a microscopic view of the material's morphology. This technique was particularly instrumental in examining the interfacial adhesion and matrix morphology post-cryofracture, highlighting the influence of crystallinity on the composite's mechanical integrity. By sputter coating the samples with gold to enhance conductivity, SEM images reveal intricate details about the crystalline structures and void content, providing a qualitative assessment of failure behaviors and the underlying crystallization morphology.
Through these innovative research methods, the study provides a comprehensive understanding of the crystallization kinetics and morphology of CF/PEKK composites. The findings underscore the significance of controlling processing conditions to achieve desired crystallinity levels, ultimately influencing the mechanical properties and performance of the composites. This research approach not only advances our knowledge of PEKK composites but also sets a foundation for optimizing manufacturing parameters in high-performance applications.
The comprehensive study of crystallinity gradients in CF/PEKK laminates manufactured via Automated Tape Placement (ATP) has unveiled significant findings that stand to revolutionize the manufacturing of thermoplastic composites. This section highlights the key discoveries, including crystallization kinetics and modeling, and explores how these insights pave the way for enhanced manufacturing techniques and material quality.
These findings equip manufacturers with the knowledge to fine-tune ATP processing parameters, thereby optimizing the crystallinity and, consequently, the mechanical properties of CF/PEKK composite parts.
This research provides a clearer understanding of the crystallization behavior of CF/PEKK composites, marking a milestone in the pursuit of manufacturing excellence in thermoplastic composites. By translating these scientific insights into practical applications, the path is set for the development of next-generation thermoplastic composites that meet the demanding requirements of high-performance applications.
We extend our deepest gratitude to Helena Pérez Martín for her pioneering research on crystallinity gradients in high-performance thermoplastic composites manufactured by automated tape placement. Her doctoral thesis "Studying Crystallinity Gradients in High
Performance Thermoplastic Composites Manufactured by Automated Tape Placement" provides invaluable insights into the complexities of material science and has greatly enriched the content of this blog. Helena's dedication to advancing our understanding of thermoplastic composites has not only paved the way for future innovations in aerospace manufacturing but also inspired countless professionals and enthusiasts in the field of materials science. Thank you, Helena Pérez Martín, for your significant contribution to the world of high-performance composites.
Discover the future of composite manufacturing with Addcomposites! Here's how you can get involved:
At Addcomposites, we are dedicated to revolutionizing composite manufacturing. Our AFP systems and comprehensive support services are waiting for you to harness. So, don't wait – get started on your journey to the future of manufacturing today!