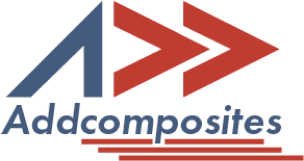
Processing carbon fiber (CF) composites is a tricky business, considering most engineers thinking of producing or designing come from a background of designing metallic parts. it’s been called black aluminum, and its design and fabrication have been described as black art. What is it, really?
The purpose of this design guide is to provide general information and specifications on carbon fiber composite materials and some guidelines for designing lightweight high-performance products with carbon fiber composites.
Carbon fiber composites have exceptional mechanical properties compared to homogenous metals and plastics. The material is strong, stiff, and lightweight. These composites are the material of choice for applications where lightweight & superior performance is paramount, such as components for spacecraft, fighter aircraft, and race cars.
Composite materials are made by combining reinforcement (fiber) with matrix (resin), and this combination of the fiber and matrix provides characteristics superior to either of the materials alone.
In a composite material, the fiber carries a majority of the load and is the major contributor to the material properties. The resin helps to transfer load between fibers, prevents the fibers from buckling, and binds the materials together.
Historically, carbon fiber composites have been very expensive, which has limited its use to only special applications. However, over the past fifteen years, as consumption has increased and automation in manufacturing processes has increased, the price of carbon fiber composites has declined. This fact is aided by the lowered cost of Carbon fiber material to a historic low of 15–20 USD/kg.
The combined effect has brought down the overall cost of high-end aluminum products. Today, carbon fiber composites are economically viable in many applications such as sporting goods, performance boats, performance vehicles, and high-performance industrial machinery.
Composite materials are extremely versatile. The engineer can choose from a wide variety of fibers and resins to obtain the desired material properties. Also, the material thickness and fiber orientations can be optimized for each application.
The advantages of carbon fiber composites are:
Looking at the table below, a comparison of costs and mechanical properties of carbon fiber composite, fiberglass composite, aluminum, and steel. Due to the wide variety of graphite fibers and resins available, and the numerous combinations of the materials, the properties are listed in ranges.
The unique positioning of the carbon fiber composites with high specific strength, stiffness, and low CTE provides them a unique place in many application areas as shown in the table below:
Carbon Fiber composites are considered "designer’s material" because the parts can be tailored to have strength and or stiffness in the directions and locations that are necessary. This is achieved by strategically placing materials and orienting fiber direction to best suit the requirements.
Also, the design and manufacturing flexibility that carbon fiber composites offer provides opportunities to optimize design, such as consolidating and incorporating many features in-situ, to further reduce the total part price. Some general design guidelines are listed below:
Molds are used to define the shape of the composite parts. The composite part will pick up all shapes and features of the molds; therefore the quality of the part is heavily influenced by the quality of the mold.
The molds can be either male or female. The female molds are the most common and they will produce a part with a smooth exterior surface while a male mold will produce a smooth interior surface. A matched mold (male and female) is required if the part is consolidated using a press.
The molds can be made with composite materials, metal-filled epoxy, or machined from aluminum or steel. The type of mold and materials used depends on the type of part and the production quantity.
Advanced carbon fiber production is usually carried out using pre-impregnated carbon fiber with thermoset resins. The two key methods used are:
The hand layup of pre-impregnated woven materials is still a large part of the composite manufacturing industry, requiring the skills and experience of a human workforce to form flat plies into complex shapes. It is capable of producing high-performance and complex parts but can be an expensive and highly variable process.
We have previously written a blog post about this, but the main things to consider are the width of the fiber you are using and the compaction roller radius. Read how these things, among others, affect the designing process here: “Things to consider when Designing for ATL/AFP Manufacturing”
If you are interested in learning more about affordable, yet advanced, composites production automation reach out to initiate a discussion! Let's make the power of composite production known to the world!
Addcomposites is the provider of the Automated Fiber Placement (AFP) system. The AFP system can be rented on a monthly basis to work with thermosets, thermoplastic, dry fiber placement, or in combination with 3d printers.
Processing carbon fiber (CF) composites is a tricky business, considering most engineers thinking of producing or designing come from a background of designing metallic parts. it’s been called black aluminum, and its design and fabrication have been described as black art. What is it, really?
The purpose of this design guide is to provide general information and specifications on carbon fiber composite materials and some guidelines for designing lightweight high-performance products with carbon fiber composites.
Carbon fiber composites have exceptional mechanical properties compared to homogenous metals and plastics. The material is strong, stiff, and lightweight. These composites are the material of choice for applications where lightweight & superior performance is paramount, such as components for spacecraft, fighter aircraft, and race cars.
Composite materials are made by combining reinforcement (fiber) with matrix (resin), and this combination of the fiber and matrix provides characteristics superior to either of the materials alone.
In a composite material, the fiber carries a majority of the load and is the major contributor to the material properties. The resin helps to transfer load between fibers, prevents the fibers from buckling, and binds the materials together.
Historically, carbon fiber composites have been very expensive, which has limited its use to only special applications. However, over the past fifteen years, as consumption has increased and automation in manufacturing processes has increased, the price of carbon fiber composites has declined. This fact is aided by the lowered cost of Carbon fiber material to a historic low of 15–20 USD/kg.
The combined effect has brought down the overall cost of high-end aluminum products. Today, carbon fiber composites are economically viable in many applications such as sporting goods, performance boats, performance vehicles, and high-performance industrial machinery.
Composite materials are extremely versatile. The engineer can choose from a wide variety of fibers and resins to obtain the desired material properties. Also, the material thickness and fiber orientations can be optimized for each application.
The advantages of carbon fiber composites are:
Looking at the table below, a comparison of costs and mechanical properties of carbon fiber composite, fiberglass composite, aluminum, and steel. Due to the wide variety of graphite fibers and resins available, and the numerous combinations of the materials, the properties are listed in ranges.
The unique positioning of the carbon fiber composites with high specific strength, stiffness, and low CTE provides them a unique place in many application areas as shown in the table below:
Carbon Fiber composites are considered "designer’s material" because the parts can be tailored to have strength and or stiffness in the directions and locations that are necessary. This is achieved by strategically placing materials and orienting fiber direction to best suit the requirements.
Also, the design and manufacturing flexibility that carbon fiber composites offer provides opportunities to optimize design, such as consolidating and incorporating many features in-situ, to further reduce the total part price. Some general design guidelines are listed below:
Molds are used to define the shape of the composite parts. The composite part will pick up all shapes and features of the molds; therefore the quality of the part is heavily influenced by the quality of the mold.
The molds can be either male or female. The female molds are the most common and they will produce a part with a smooth exterior surface while a male mold will produce a smooth interior surface. A matched mold (male and female) is required if the part is consolidated using a press.
The molds can be made with composite materials, metal-filled epoxy, or machined from aluminum or steel. The type of mold and materials used depends on the type of part and the production quantity.
Advanced carbon fiber production is usually carried out using pre-impregnated carbon fiber with thermoset resins. The two key methods used are:
The hand layup of pre-impregnated woven materials is still a large part of the composite manufacturing industry, requiring the skills and experience of a human workforce to form flat plies into complex shapes. It is capable of producing high-performance and complex parts but can be an expensive and highly variable process.
We have previously written a blog post about this, but the main things to consider are the width of the fiber you are using and the compaction roller radius. Read how these things, among others, affect the designing process here: “Things to consider when Designing for ATL/AFP Manufacturing”
If you are interested in learning more about affordable, yet advanced, composites production automation reach out to initiate a discussion! Let's make the power of composite production known to the world!
Addcomposites is the provider of the Automated Fiber Placement (AFP) system. The AFP system can be rented on a monthly basis to work with thermosets, thermoplastic, dry fiber placement, or in combination with 3d printers.