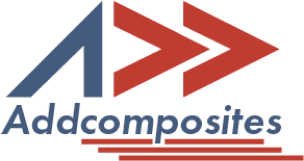
Process planning plays a crucial role in connecting product development and manufacturing of fiber composite structures. However, traditional methods often lack flexibility and adaptability, leading to inefficiencies and disconnects between design and production. Recent advancements in Large Language Models (LLMs) offer a promising solution to streamline process planning and enable more autonomous workflows.
LLMs, such as OpenAI's GPT-4, have demonstrated remarkable capabilities in reasoning, strategic thinking, and natural language understanding. These capabilities make them well-suited for complex and adaptive process planning tasks in the manufacturing of fiber composite structures. By leveraging LLMs, companies can:
The application of LLMs in process planning has the potential to significantly reduce lead times, improve efficiency, and enhance the overall quality of fiber composite products. As the technology continues to evolve, we can expect to see more advanced and integrated process planning solutions powered by LLMs, revolutionizing the way we design and manufacture fiber composite structures.
The interaction between product development and manufacturing poses significant challenges for many industrial organizations, particularly in the field of fiber composite structures. Disconnects between design and production can lead to:
Traditional process planning methods often struggle to bridge the gap between product development and manufacturing effectively. They may lack the flexibility and adaptability needed to handle the complex and dynamic nature of fiber composite manufacturing processes.
Integrating knowledge from various domain experts
Handling the complexity of fiber composite manufacturing processes
Adapting to changes in product design or manufacturing constraints
Optimizing resource allocation and task sequencing
Generating accurate and up-to-date manufacturing instructions
Overcoming these challenges requires innovative solutions that can streamline the process planning workflow, improve communication between design and production teams, and enable more autonomous and adaptive planning capabilities. By addressing these pain points, companies can unlock the full potential of fiber composite materials and achieve a more efficient, cost-effective, and high-quality manufacturing process.
The proposed approach to streamline process planning for fiber composite structures involves an autonomous agent powered by OpenAI's GPT-4 language model and the LangChain framework. The agent is designed to solve various process planning problems, including:
The autonomous process planning agent is implemented using the OpenAI Functions agent of the LangChain framework, which allows for the integration of custom process planning tools with the GPT-4 language model. These tools include:
By combining the reasoning capabilities of GPT-4 with domain-specific process planning tools, the agent can autonomously solve complex planning problems and adapt to various manufacturing scenarios. This approach eliminates the need for process planning expertise from the end user, as the agent's decision-making process is guided by structured tools and can be traced back for verification.
The integration of the LangChain framework and custom process planning tools with the GPT-4 language model enables a powerful and flexible solution for process planning in fiber composite manufacturing. This innovative approach has the potential to revolutionize the way companies handle process planning tasks, making it more efficient, adaptive, and accessible to a wider range of users.
The proposed approach of using Large Language Model (LLM) based agents offers flexible and adaptive process planning solutions for fiber composite structures. This innovative solution provides several key benefits:
By leveraging LLM-based agents, companies can unlock new levels of flexibility, adaptability, and efficiency in their process planning for fiber composite structures. This innovative approach has the potential to transform the way companies handle process planning tasks, ultimately leading to faster time-to-market, reduced costs, and improved product quality.
Thank you Maximilian Holland and Kunal Chaudhari for your research paper "Large language model based agent for process planning of fiber composite structures," which has provided valuable insights and information for this blog post. Your work, conducted at the Fraunhofer Institute for Casting, Composite and Processing Technology IGCV in Augsburg, Germany, has made a significant contribution to the field of process planning in fiber composite manufacturing.
We would like to express my gratitude to Maximilian Holland and Kunal Chaudhari for their dedication to developing an autonomous agent for process planning of fiber composite structures using Large Language Models, specifically OpenAI's GPT-4, and the LangChain framework. Your research has not only laid the foundation for the content presented in this blog but also sparked important conversations about the future of AI-driven process planning solutions.
Your work has shed light on the potential of LLMs to streamline and revolutionize process planning workflows in the fiber composite manufacturing industry. The detailed explanations and insights provided in your paper have been instrumental in creating this blog post and informing our understanding of the challenges and opportunities in connecting product development and manufacturing.
Discover the future of composite manufacturing with Addcomposites! Here's how you can get involved:
At Addcomposites, we are dedicated to revolutionizing composite manufacturing. Our AFP systems and comprehensive support services are waiting for you to harness. So, don't wait – get started on your journey to the future of manufacturing today!
Process planning plays a crucial role in connecting product development and manufacturing of fiber composite structures. However, traditional methods often lack flexibility and adaptability, leading to inefficiencies and disconnects between design and production. Recent advancements in Large Language Models (LLMs) offer a promising solution to streamline process planning and enable more autonomous workflows.
LLMs, such as OpenAI's GPT-4, have demonstrated remarkable capabilities in reasoning, strategic thinking, and natural language understanding. These capabilities make them well-suited for complex and adaptive process planning tasks in the manufacturing of fiber composite structures. By leveraging LLMs, companies can:
The application of LLMs in process planning has the potential to significantly reduce lead times, improve efficiency, and enhance the overall quality of fiber composite products. As the technology continues to evolve, we can expect to see more advanced and integrated process planning solutions powered by LLMs, revolutionizing the way we design and manufacture fiber composite structures.
The interaction between product development and manufacturing poses significant challenges for many industrial organizations, particularly in the field of fiber composite structures. Disconnects between design and production can lead to:
Traditional process planning methods often struggle to bridge the gap between product development and manufacturing effectively. They may lack the flexibility and adaptability needed to handle the complex and dynamic nature of fiber composite manufacturing processes.
Integrating knowledge from various domain experts
Handling the complexity of fiber composite manufacturing processes
Adapting to changes in product design or manufacturing constraints
Optimizing resource allocation and task sequencing
Generating accurate and up-to-date manufacturing instructions
Overcoming these challenges requires innovative solutions that can streamline the process planning workflow, improve communication between design and production teams, and enable more autonomous and adaptive planning capabilities. By addressing these pain points, companies can unlock the full potential of fiber composite materials and achieve a more efficient, cost-effective, and high-quality manufacturing process.
The proposed approach to streamline process planning for fiber composite structures involves an autonomous agent powered by OpenAI's GPT-4 language model and the LangChain framework. The agent is designed to solve various process planning problems, including:
The autonomous process planning agent is implemented using the OpenAI Functions agent of the LangChain framework, which allows for the integration of custom process planning tools with the GPT-4 language model. These tools include:
By combining the reasoning capabilities of GPT-4 with domain-specific process planning tools, the agent can autonomously solve complex planning problems and adapt to various manufacturing scenarios. This approach eliminates the need for process planning expertise from the end user, as the agent's decision-making process is guided by structured tools and can be traced back for verification.
The integration of the LangChain framework and custom process planning tools with the GPT-4 language model enables a powerful and flexible solution for process planning in fiber composite manufacturing. This innovative approach has the potential to revolutionize the way companies handle process planning tasks, making it more efficient, adaptive, and accessible to a wider range of users.
The proposed approach of using Large Language Model (LLM) based agents offers flexible and adaptive process planning solutions for fiber composite structures. This innovative solution provides several key benefits:
By leveraging LLM-based agents, companies can unlock new levels of flexibility, adaptability, and efficiency in their process planning for fiber composite structures. This innovative approach has the potential to transform the way companies handle process planning tasks, ultimately leading to faster time-to-market, reduced costs, and improved product quality.
Thank you Maximilian Holland and Kunal Chaudhari for your research paper "Large language model based agent for process planning of fiber composite structures," which has provided valuable insights and information for this blog post. Your work, conducted at the Fraunhofer Institute for Casting, Composite and Processing Technology IGCV in Augsburg, Germany, has made a significant contribution to the field of process planning in fiber composite manufacturing.
We would like to express my gratitude to Maximilian Holland and Kunal Chaudhari for their dedication to developing an autonomous agent for process planning of fiber composite structures using Large Language Models, specifically OpenAI's GPT-4, and the LangChain framework. Your research has not only laid the foundation for the content presented in this blog but also sparked important conversations about the future of AI-driven process planning solutions.
Your work has shed light on the potential of LLMs to streamline and revolutionize process planning workflows in the fiber composite manufacturing industry. The detailed explanations and insights provided in your paper have been instrumental in creating this blog post and informing our understanding of the challenges and opportunities in connecting product development and manufacturing.
Discover the future of composite manufacturing with Addcomposites! Here's how you can get involved:
At Addcomposites, we are dedicated to revolutionizing composite manufacturing. Our AFP systems and comprehensive support services are waiting for you to harness. So, don't wait – get started on your journey to the future of manufacturing today!