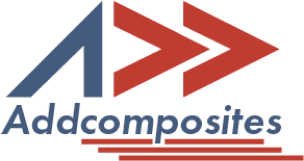
In the rapidly evolving world of electric vehicles and devices, the concept of structural batteries is emerging as a game-changer. These aren't your typical batteries; they're integral components of the device or vehicle's structure, contributing to its overall strength and stiffness. This introduction will provide a brief overview of structural batteries and the transformative role of Automated Fiber Placement (AFP) technology in their manufacturing.
Structural batteries are a novel concept that combines energy storage and structural function into a single unit. Unlike traditional batteries that simply add weight to a vehicle or device, structural batteries contribute to the overall strength and stiffness of the structure. This dual functionality can lead to significant weight reductions, making vehicles and devices more energy-efficient. [1]
The significance of structural batteries extends beyond just weight reduction. By integrating the battery into the structure of the vehicle or device, designers can free up space, allowing for more innovative and flexible designs. This has far-reaching implications for the future of electric vehicles and devices, potentially revolutionizing the way they're designed and manufactured.
AFP technology is a cutting-edge manufacturing technique used in the production of composite materials. It involves the precise placement of carbon, glass, or other types of fibers onto a mold using a computer-controlled system. This allows for the creation of complex shapes and structures that would be difficult, if not impossible, to achieve with traditional manufacturing methods.
In the context of structural battery manufacturing, AFP technology can play a crucial role. It can be used to precisely place the carbon fibers used in the negative electrode of the battery, ensuring optimal performance. Furthermore, AFP technology can automate the layering process involved in the manufacturing of structural batteries, enhancing accuracy and consistency.
In the realm of electric vehicles and devices, the concept of structural batteries is gaining significant traction. These batteries are not just energy storage systems; they are integral parts of the structure of the device or vehicle, contributing to its overall strength and stiffness. This section delves into the manufacturing process of structural batteries, based on the research paper "A Structural Battery and its Multifunctional Performance".
The manufacturing process of a structural battery is a fascinating blend of materials science and engineering. Here's a step-by-step breakdown:
The manufacturing process of structural batteries is unique in that it employs multifunctional constituents. Each component serves multiple functions, contributing to both the structural integrity and the electrical performance of the battery. Here's a closer look at these constituents: [3]
AFP technology is revolutionizing the way we manufacture composite materials, and its application in the production of structural batteries is no exception. This section explores how AFP technology can be integrated into the manufacturing process of structural batteries and the unique benefits it brings. [4]
AFP technology can be a game-changer in the manufacturing process of structural batteries. Here's how:
3.2 Unique Characteristics and Benefits of AFP Systems
AFP systems like AFP-XS, AFP-X, and SCF3D each bring unique characteristics and benefits to the table. Let's take a closer look:
Automation software plays a pivotal role in modern composites manufacturing, enhancing efficiency, precision, and flexibility. One such software is AddPath, an offline programming tool designed for path planning needs. This section explores how AddPath can enhance the manufacturing process of structural batteries.
AddPath is a user-friendly, open-access offline programming software designed to streamline and optimize the path planning process in composites manufacturing. Here are some of its key features:
AddPath can significantly enhance the manufacturing process of structural batteries in several ways:
As we reach the end of this exploration into the intersection of structural battery manufacturing and Automated Fiber Placement (AFP) technology, it's clear that we're standing on the precipice of a new era in composites manufacturing.
AFP technology has shown immense potential in revolutionizing the manufacturing process of structural batteries. With its precision, scalability, and versatility, AFP systems like AFP-XS, AFP-X, and SCF3D can significantly enhance the production of structural batteries. These systems allow for the precise placement of fibers, efficient layering of components, and rapid scaling of production, making them invaluable tools in the manufacturing process.
Moreover, the integration of automation software like AddPath further amplifies the capabilities of AFP technology. By offering precision planning, process simulation, and data analysis capabilities, AddPath can help manufacturers optimize their processes, improve product quality, and increase efficiency.
Looking ahead, the future of structural batteries and AFP technology is bright. As the demand for lightweight, energy-efficient electric vehicles and devices continues to grow, so too will the need for advanced manufacturing technologies like AFP.
In the coming years, we can expect to see further advancements in AFP technology and automation software, leading to even more efficient and cost-effective production of structural batteries. Moreover, as more manufacturers adopt these technologies, we can expect to see a rise in the quality and performance of structural batteries.
Discover the future of composite manufacturing with Addcomposites! Here's how you can get involved:
At Addcomposites, we are dedicated to revolutionizing composite manufacturing. Our AFP systems and comprehensive support services are waiting for you to harness. So, don't wait – get started on your journey to the future of manufacturing today!
In the rapidly evolving world of electric vehicles and devices, the concept of structural batteries is emerging as a game-changer. These aren't your typical batteries; they're integral components of the device or vehicle's structure, contributing to its overall strength and stiffness. This introduction will provide a brief overview of structural batteries and the transformative role of Automated Fiber Placement (AFP) technology in their manufacturing.
Structural batteries are a novel concept that combines energy storage and structural function into a single unit. Unlike traditional batteries that simply add weight to a vehicle or device, structural batteries contribute to the overall strength and stiffness of the structure. This dual functionality can lead to significant weight reductions, making vehicles and devices more energy-efficient. [1]
The significance of structural batteries extends beyond just weight reduction. By integrating the battery into the structure of the vehicle or device, designers can free up space, allowing for more innovative and flexible designs. This has far-reaching implications for the future of electric vehicles and devices, potentially revolutionizing the way they're designed and manufactured.
AFP technology is a cutting-edge manufacturing technique used in the production of composite materials. It involves the precise placement of carbon, glass, or other types of fibers onto a mold using a computer-controlled system. This allows for the creation of complex shapes and structures that would be difficult, if not impossible, to achieve with traditional manufacturing methods.
In the context of structural battery manufacturing, AFP technology can play a crucial role. It can be used to precisely place the carbon fibers used in the negative electrode of the battery, ensuring optimal performance. Furthermore, AFP technology can automate the layering process involved in the manufacturing of structural batteries, enhancing accuracy and consistency.
In the realm of electric vehicles and devices, the concept of structural batteries is gaining significant traction. These batteries are not just energy storage systems; they are integral parts of the structure of the device or vehicle, contributing to its overall strength and stiffness. This section delves into the manufacturing process of structural batteries, based on the research paper "A Structural Battery and its Multifunctional Performance".
The manufacturing process of a structural battery is a fascinating blend of materials science and engineering. Here's a step-by-step breakdown:
The manufacturing process of structural batteries is unique in that it employs multifunctional constituents. Each component serves multiple functions, contributing to both the structural integrity and the electrical performance of the battery. Here's a closer look at these constituents: [3]
AFP technology is revolutionizing the way we manufacture composite materials, and its application in the production of structural batteries is no exception. This section explores how AFP technology can be integrated into the manufacturing process of structural batteries and the unique benefits it brings. [4]
AFP technology can be a game-changer in the manufacturing process of structural batteries. Here's how:
3.2 Unique Characteristics and Benefits of AFP Systems
AFP systems like AFP-XS, AFP-X, and SCF3D each bring unique characteristics and benefits to the table. Let's take a closer look:
Automation software plays a pivotal role in modern composites manufacturing, enhancing efficiency, precision, and flexibility. One such software is AddPath, an offline programming tool designed for path planning needs. This section explores how AddPath can enhance the manufacturing process of structural batteries.
AddPath is a user-friendly, open-access offline programming software designed to streamline and optimize the path planning process in composites manufacturing. Here are some of its key features:
AddPath can significantly enhance the manufacturing process of structural batteries in several ways:
As we reach the end of this exploration into the intersection of structural battery manufacturing and Automated Fiber Placement (AFP) technology, it's clear that we're standing on the precipice of a new era in composites manufacturing.
AFP technology has shown immense potential in revolutionizing the manufacturing process of structural batteries. With its precision, scalability, and versatility, AFP systems like AFP-XS, AFP-X, and SCF3D can significantly enhance the production of structural batteries. These systems allow for the precise placement of fibers, efficient layering of components, and rapid scaling of production, making them invaluable tools in the manufacturing process.
Moreover, the integration of automation software like AddPath further amplifies the capabilities of AFP technology. By offering precision planning, process simulation, and data analysis capabilities, AddPath can help manufacturers optimize their processes, improve product quality, and increase efficiency.
Looking ahead, the future of structural batteries and AFP technology is bright. As the demand for lightweight, energy-efficient electric vehicles and devices continues to grow, so too will the need for advanced manufacturing technologies like AFP.
In the coming years, we can expect to see further advancements in AFP technology and automation software, leading to even more efficient and cost-effective production of structural batteries. Moreover, as more manufacturers adopt these technologies, we can expect to see a rise in the quality and performance of structural batteries.
Discover the future of composite manufacturing with Addcomposites! Here's how you can get involved:
At Addcomposites, we are dedicated to revolutionizing composite manufacturing. Our AFP systems and comprehensive support services are waiting for you to harness. So, don't wait – get started on your journey to the future of manufacturing today!