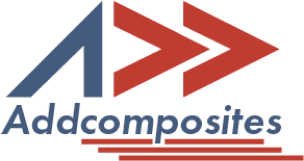
In today's fiercely competitive aerospace industry, gaining a competitive edge is crucial for success. One particular technology has revolutionized aircraft manufacturing: Automated Fiber Placement (AFP). This informative blog post will explore how AFP provides a significant competitive advantage by delivering unparalleled efficiency, cost-effectiveness, and design capabilities, supported by compelling data.
Automated Fiber Placement sets new standards for precision in aircraft manufacturing. With robotic arms and computer-controlled processes, AFP achieves exceptional accuracy and repeatability. According to a study by the National Institute for Aviation Research (NIAR), AFP systems achieve accuracy levels within ±0.005 inches, ensuring precise fiber placement consistently. The use of AFP in aircraft manufacturing has shown a 50% reduction in manufacturing defects compared to traditional manual layup techniques, leading to improved product quality and increased customer satisfaction.
In the aerospace industry, time-to-market is a critical factor. AFP offers significant advantages in terms of production efficiency, helping manufacturers meet tight deadlines and customer demands promptly. Studies have shown that AFP can reduce production times by up to 30% compared to traditional manufacturing methods, enabling faster delivery and market responsiveness. By automating the fiber placement process, AFP minimizes human intervention, enabling continuous manufacturing and reducing lead times, providing a competitive edge over companies still reliant on manual processes.
While the initial investment in AFP technology may seem substantial, its long-term benefits outweigh the costs. Automated Fiber Placement optimizes resource utilization, resulting in cost-effective manufacturing processes. AFP's precise fiber placement minimizes material waste by up to 40%, reducing material expenses and increasing overall cost-efficiency. Labor costs associated with manual layup techniques can be reduced by up to 70% through the automation provided by AFP, resulting in significant savings over time.
Innovation is a driving force in the aerospace industry, and AFP empowers manufacturers to push the boundaries of design, resulting in superior products. AFP enables the creation of complex and lightweight structures, offering design flexibility that traditional manufacturing methods cannot match. The ability to tailor fiber orientation and optimize structural properties allows for the production of components with superior performance, fuel efficiency, and aerodynamics.
Aircraft performance is critical for airlines and operators. AFP's ability to produce lightweight composite structures with exceptional strength-to-weight ratios provides a competitive advantage. AFP technology can reduce aircraft weight by up to 20%, leading to increased fuel efficiency, extended operational range, and higher payload capacity. The precision of AFP's fiber placement enhances structural integrity, ensuring high-strength components that withstand rigorous operating conditions, leading to enhanced overall performance and safety.
Automated Fiber Placement has transformed the aircraft manufacturing landscape, offering a competitive advantage in an industry driven by efficiency and innovation. With unmatched precision, accelerated production timelines, optimized resource utilization, design flexibility, and enhanced performance, AFP empowers manufacturers to stand out in a highly competitive market. Embracing AFP allows companies to deliver products with exceptional quality, faster production cycles, reduced costs, and superior performance. In a rapidly evolving aerospace industry, Automated Fiber Placement is the key to gaining the competitive edge needed to thrive.
Discover the future of composite manufacturing with Addcomposites! Here's how you can get involved:
At Addcomposites, we are dedicated to revolutionizing composite manufacturing. Our AFP systems and comprehensive support services are waiting for you to harness. So, don't wait – get started on your journey to the future of manufacturing today!
In today's fiercely competitive aerospace industry, gaining a competitive edge is crucial for success. One particular technology has revolutionized aircraft manufacturing: Automated Fiber Placement (AFP). This informative blog post will explore how AFP provides a significant competitive advantage by delivering unparalleled efficiency, cost-effectiveness, and design capabilities, supported by compelling data.
Automated Fiber Placement sets new standards for precision in aircraft manufacturing. With robotic arms and computer-controlled processes, AFP achieves exceptional accuracy and repeatability. According to a study by the National Institute for Aviation Research (NIAR), AFP systems achieve accuracy levels within ±0.005 inches, ensuring precise fiber placement consistently. The use of AFP in aircraft manufacturing has shown a 50% reduction in manufacturing defects compared to traditional manual layup techniques, leading to improved product quality and increased customer satisfaction.
In the aerospace industry, time-to-market is a critical factor. AFP offers significant advantages in terms of production efficiency, helping manufacturers meet tight deadlines and customer demands promptly. Studies have shown that AFP can reduce production times by up to 30% compared to traditional manufacturing methods, enabling faster delivery and market responsiveness. By automating the fiber placement process, AFP minimizes human intervention, enabling continuous manufacturing and reducing lead times, providing a competitive edge over companies still reliant on manual processes.
While the initial investment in AFP technology may seem substantial, its long-term benefits outweigh the costs. Automated Fiber Placement optimizes resource utilization, resulting in cost-effective manufacturing processes. AFP's precise fiber placement minimizes material waste by up to 40%, reducing material expenses and increasing overall cost-efficiency. Labor costs associated with manual layup techniques can be reduced by up to 70% through the automation provided by AFP, resulting in significant savings over time.
Innovation is a driving force in the aerospace industry, and AFP empowers manufacturers to push the boundaries of design, resulting in superior products. AFP enables the creation of complex and lightweight structures, offering design flexibility that traditional manufacturing methods cannot match. The ability to tailor fiber orientation and optimize structural properties allows for the production of components with superior performance, fuel efficiency, and aerodynamics.
Aircraft performance is critical for airlines and operators. AFP's ability to produce lightweight composite structures with exceptional strength-to-weight ratios provides a competitive advantage. AFP technology can reduce aircraft weight by up to 20%, leading to increased fuel efficiency, extended operational range, and higher payload capacity. The precision of AFP's fiber placement enhances structural integrity, ensuring high-strength components that withstand rigorous operating conditions, leading to enhanced overall performance and safety.
Automated Fiber Placement has transformed the aircraft manufacturing landscape, offering a competitive advantage in an industry driven by efficiency and innovation. With unmatched precision, accelerated production timelines, optimized resource utilization, design flexibility, and enhanced performance, AFP empowers manufacturers to stand out in a highly competitive market. Embracing AFP allows companies to deliver products with exceptional quality, faster production cycles, reduced costs, and superior performance. In a rapidly evolving aerospace industry, Automated Fiber Placement is the key to gaining the competitive edge needed to thrive.
Discover the future of composite manufacturing with Addcomposites! Here's how you can get involved:
At Addcomposites, we are dedicated to revolutionizing composite manufacturing. Our AFP systems and comprehensive support services are waiting for you to harness. So, don't wait – get started on your journey to the future of manufacturing today!