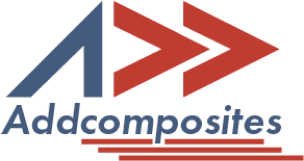
Welcome to a transformative journey in the world of composite manufacturing. For decades, the industry has been shackled by the misconception that automation is a distant, costly, and complex future. Today, we're here to shatter that myth and unveil the reality of modern composite manufacturing – a world where automation is not only accessible but also a catalyst for innovation, efficiency, and cost-effectiveness.
In the world of composite manufacturing, the traditional hand layup method has long been a cornerstone. It involves the manual application of layers of composite materials onto a mold to form various parts and components. The most prevalent technologies within this domain are the hand layup and wet layup methods.
These techniques are characterized by their labor-intensive nature, requiring skilled workers to meticulously place and shape composite materials like fiberglass or carbon fiber onto a mold. The process often involves the application of resin to bind these layers together, which is then left to cure, forming the final composite structure.
The challenges associated with these methods are significant, posing various limitations to the industry:
The transition from traditional hand layup methods to automated composite manufacturing began in earnest during the 1980s, initially driven by the aerospace industry's need for more efficient, precise, and scalable manufacturing processes. This shift was not only about overcoming the limitations of hand layup but also about expanding the market potential through automation.
AFP technology stands out for its ability to handle multiple sets of material tools, making it ideal for creating complex shapes while maintaining high throughput. This process involves the automated placement of fibers, allowing for a significant increase in efficiency and precision compared to manual methods.
ATL, while somewhat limited in the shapes it can create due to the wider tapes used, has seen advancements like continuous toe sharing, enhancing its capabilities. The tapes, often over 50mm wide, pose challenges in draping but are integral to certain manufacturing processes.
This technique is widely used for creating cylindrical shapes like pipes and tanks. It involves winding fibers around a form to create items with high strength and lightweight characteristics. The evolution of AFP to include tape winding for thermoplastics signifies the versatility and adaptability of these automated processes.
The adoption of these advanced technologies was driven by the increasing demand for higher manufacturing volumes and the need to address the inherent drawbacks of hand layup methods. Automated composite manufacturing technologies provide solutions that are not only efficient and precise but also expand the possibilities in terms of shapes, materials, and applications.
In the realm of composite manufacturing, automation has revolutionized the way components are produced, primarily by enhancing efficiency and enabling high volume production.
Unlike traditional hand layup methods, where the complexity and labor intensity remain constant from the first to the thousandth part, automated processes become more efficient over time. The initial setup for automated manufacturing might be complex, but as production continues, the process becomes faster and more streamlined. This is largely due to the high repeatability and accuracy that automation brings, ensuring consistent quality over a large number of parts.
As production volume increases, the efficiency of automated systems becomes more apparent. This shift towards automation is driven by the demand for higher volumes, which is a common trend across various industries including aerospace, automotive, energy, and sports. Automation not only meets this demand but does so with a higher level of precision and consistency than manual methods.
The evolution of computer technology and industrial robotics has played a significant role in this transition. As computing power increased, it enabled more sophisticated control over robotic systems, pushing industrial robots into the mainstream. These robots, essentially precise motion platforms with integrated computing capabilities, can be adapted for various composite manufacturing processes like AFP, ATL, filament winding, and continuous fiber 3D printing.
Companies like Addcomposites have leveraged this advancement, making automation more accessible in the composites industry. The versatility of these robotic systems means they are not limited to a specific brand or type, but rather represent an industry-wide movement towards more efficient, scalable, and precise manufacturing methods.
The evolution of composite manufacturing technologies has significantly expanded the possibilities in terms of shape complexity and material diversity. This evolution is particularly evident when contrasting automated manufacturing processes with traditional hand layup methods.
Automated processes like Automated Fiber Placement (AFP), Automated Tape Laying (ATL), and continuous fiber 3D printing have distinct capabilities in handling complex shapes. However, they do have limitations. For instance, AFP and ATL are generally confined to more 2D and 3D shapes without sharp internal radii, and they require a mold for production, similar to hand layup processes. Certain intricate structures, like a bike sprocket or a brake rocker arm, which require more intricate maneuvering, remain challenging for these automated technologies.
A significant advantage of automated processes is their ability to work with a wider range of materials, including both thermoset and thermoplastic composites. Hand layup methods are primarily limited to thermoset composites, as they cannot handle the high temperatures required for melting and processing thermoplastics. The push towards using thermoplastic composites is driven by their sustainability and recyclability, an area where automated manufacturing excels. Innovations are being made in recycling thermoset matrices, but these remain energy and chemically intensive.
Automated manufacturing processes are not limited by the size of the components they can produce. They are capable of fabricating large-scale structures like aircraft wings, something impractical with hand layup methods due to their labor and size constraints. Additionally, automated processes allow for selective fiber reinforcement at precise angles and locations, which is difficult to achieve consistently with hand layup.
One example of advanced automated manufacturing is the production of isogrid structures, commonly used in interstages of launch vehicles. These structures, characterized by their lightweight and high strength, are more suited to automated manufacturing due to their complexity and precision requirements.
The landscape of composite manufacturing has seen a paradigm shift in terms of cost-effectiveness and accessibility, especially in the context of automation. This shift has become particularly noticeable since 2015, thanks to innovations in automated technologies.
The introduction of compact automated systems like Fiber Placement (AFP) and Automated Tape Laying (ATL) machines, along with robotic filament winding and large-scale continuous fiber 3D printing, has changed the cost dynamics. These systems can now be leased at costs comparable to monthly labor expenses for manual processes. Such an approach significantly lowers the barrier to entry for adopting advanced manufacturing technologies.
The ROI on these automated systems can be remarkably quick – often within just a few months. This speed is due to their high productivity and the ability to start producing complex parts almost immediately after leasing. Companies like ADD Composites are at the forefront of making these systems accessible and justifiable in terms of cost, especially for medium to high volume production.
Automated systems have evolved to use materials previously limited to hand layup processes. This includes wet winding to compete with traditional wet processes and the use of pre-impregnated materials (prepregs). While there is an additional cost for AFP and ATL materials due to slitting, this is often offset by the high volume of production and the savings on labor.
An often overlooked aspect of automated manufacturing is its capability for quality control through data capture. Unlike hand layup processes, automated systems can record detailed data during production, significantly reducing the cost associated with quality control. This is particularly crucial for industries with stringent quality requirements, where the cost of manual quality assurance can be prohibitively high.
A practical approach to automation is starting with a pilot project, leasing equipment from suppliers to gradually scale up and familiarize workers with the new technology. This step-by-step approach de-risks the transition, allowing for a smoother adoption of AFP, ATL, filament winding, and continuous fiber 3D printing technologies.
Automated composite manufacturing brings an unparalleled level of precision, consistency, and design flexibility, revolutionizing the way composite materials are utilized and applied.
A key advantage of automation is the seamless integration of design, manufacturing, and quality control processes. Advanced software tools, like AdPath, allow for digital twin simulations, providing a platform for design validation and defect detection even before the actual manufacturing begins. This pre-emptive approach ensures that potential issues are addressed early, saving time and resources.
Automated processes, equipped with sophisticated sensors and control systems, consistently produce high-quality parts, maintaining uniformity across high volumes. This consistency is crucial for industries that demand precision and reliability, such as aerospace and automotive.
Automation unlocks new possibilities in design. Techniques like helical printing and the ability to quickly change tools on robotic arms allow for a combination of AFP, 3D printing, filament winding, and ATL processes. This flexibility paves the way for hybrid materials to be used more effectively, enabling manufacturers to explore and innovate without the constraints of manual handling.
Automated manufacturing also facilitates the incorporation of structural health monitoring sensors into the composite structures, leading to the creation of 'smart' or '4D' structures. Furthermore, the precise material placement capabilities of automated systems make them ideal for utilizing sustainable, naturally sourced materials like jute or bamboo fibers. This not only enhances the sustainability aspect but also maximizes the strength and functionality of these materials in high-quality applications, such as sports equipment.
The precision and efficiency of automated composite manufacturing have the potential to reduce raw material costs significantly. This cost reduction is vital for composites to compete effectively with traditional materials like metals, opening up broader applications and market opportunities.
As we reach the conclusion of our exploration into automated composite manufacturing, it's clear that this field represents not just an evolution in technology, but a pivotal shift in how industries approach production.
For businesses looking to embark on their journey towards automation, the following steps can help in de-risking the transition:
The future of composite manufacturing is inherently tied to automation. This technology not only meets the current demands of industries but also opens up new possibilities in design and material innovation. By embracing automated composite manufacturing, businesses can stay ahead in a competitive and ever-evolving landscape.
Discover the future of composite manufacturing with Addcomposites! Here's how you can get involved:
At Addcomposites, we are dedicated to revolutionizing composite manufacturing. Our AFP systems and comprehensive support services are waiting for you to harness. So, don't wait – get started on your journey to the future of manufacturing today!
Welcome to a transformative journey in the world of composite manufacturing. For decades, the industry has been shackled by the misconception that automation is a distant, costly, and complex future. Today, we're here to shatter that myth and unveil the reality of modern composite manufacturing – a world where automation is not only accessible but also a catalyst for innovation, efficiency, and cost-effectiveness.
In the world of composite manufacturing, the traditional hand layup method has long been a cornerstone. It involves the manual application of layers of composite materials onto a mold to form various parts and components. The most prevalent technologies within this domain are the hand layup and wet layup methods.
These techniques are characterized by their labor-intensive nature, requiring skilled workers to meticulously place and shape composite materials like fiberglass or carbon fiber onto a mold. The process often involves the application of resin to bind these layers together, which is then left to cure, forming the final composite structure.
The challenges associated with these methods are significant, posing various limitations to the industry:
The transition from traditional hand layup methods to automated composite manufacturing began in earnest during the 1980s, initially driven by the aerospace industry's need for more efficient, precise, and scalable manufacturing processes. This shift was not only about overcoming the limitations of hand layup but also about expanding the market potential through automation.
AFP technology stands out for its ability to handle multiple sets of material tools, making it ideal for creating complex shapes while maintaining high throughput. This process involves the automated placement of fibers, allowing for a significant increase in efficiency and precision compared to manual methods.
ATL, while somewhat limited in the shapes it can create due to the wider tapes used, has seen advancements like continuous toe sharing, enhancing its capabilities. The tapes, often over 50mm wide, pose challenges in draping but are integral to certain manufacturing processes.
This technique is widely used for creating cylindrical shapes like pipes and tanks. It involves winding fibers around a form to create items with high strength and lightweight characteristics. The evolution of AFP to include tape winding for thermoplastics signifies the versatility and adaptability of these automated processes.
The adoption of these advanced technologies was driven by the increasing demand for higher manufacturing volumes and the need to address the inherent drawbacks of hand layup methods. Automated composite manufacturing technologies provide solutions that are not only efficient and precise but also expand the possibilities in terms of shapes, materials, and applications.
In the realm of composite manufacturing, automation has revolutionized the way components are produced, primarily by enhancing efficiency and enabling high volume production.
Unlike traditional hand layup methods, where the complexity and labor intensity remain constant from the first to the thousandth part, automated processes become more efficient over time. The initial setup for automated manufacturing might be complex, but as production continues, the process becomes faster and more streamlined. This is largely due to the high repeatability and accuracy that automation brings, ensuring consistent quality over a large number of parts.
As production volume increases, the efficiency of automated systems becomes more apparent. This shift towards automation is driven by the demand for higher volumes, which is a common trend across various industries including aerospace, automotive, energy, and sports. Automation not only meets this demand but does so with a higher level of precision and consistency than manual methods.
The evolution of computer technology and industrial robotics has played a significant role in this transition. As computing power increased, it enabled more sophisticated control over robotic systems, pushing industrial robots into the mainstream. These robots, essentially precise motion platforms with integrated computing capabilities, can be adapted for various composite manufacturing processes like AFP, ATL, filament winding, and continuous fiber 3D printing.
Companies like Addcomposites have leveraged this advancement, making automation more accessible in the composites industry. The versatility of these robotic systems means they are not limited to a specific brand or type, but rather represent an industry-wide movement towards more efficient, scalable, and precise manufacturing methods.
The evolution of composite manufacturing technologies has significantly expanded the possibilities in terms of shape complexity and material diversity. This evolution is particularly evident when contrasting automated manufacturing processes with traditional hand layup methods.
Automated processes like Automated Fiber Placement (AFP), Automated Tape Laying (ATL), and continuous fiber 3D printing have distinct capabilities in handling complex shapes. However, they do have limitations. For instance, AFP and ATL are generally confined to more 2D and 3D shapes without sharp internal radii, and they require a mold for production, similar to hand layup processes. Certain intricate structures, like a bike sprocket or a brake rocker arm, which require more intricate maneuvering, remain challenging for these automated technologies.
A significant advantage of automated processes is their ability to work with a wider range of materials, including both thermoset and thermoplastic composites. Hand layup methods are primarily limited to thermoset composites, as they cannot handle the high temperatures required for melting and processing thermoplastics. The push towards using thermoplastic composites is driven by their sustainability and recyclability, an area where automated manufacturing excels. Innovations are being made in recycling thermoset matrices, but these remain energy and chemically intensive.
Automated manufacturing processes are not limited by the size of the components they can produce. They are capable of fabricating large-scale structures like aircraft wings, something impractical with hand layup methods due to their labor and size constraints. Additionally, automated processes allow for selective fiber reinforcement at precise angles and locations, which is difficult to achieve consistently with hand layup.
One example of advanced automated manufacturing is the production of isogrid structures, commonly used in interstages of launch vehicles. These structures, characterized by their lightweight and high strength, are more suited to automated manufacturing due to their complexity and precision requirements.
The landscape of composite manufacturing has seen a paradigm shift in terms of cost-effectiveness and accessibility, especially in the context of automation. This shift has become particularly noticeable since 2015, thanks to innovations in automated technologies.
The introduction of compact automated systems like Fiber Placement (AFP) and Automated Tape Laying (ATL) machines, along with robotic filament winding and large-scale continuous fiber 3D printing, has changed the cost dynamics. These systems can now be leased at costs comparable to monthly labor expenses for manual processes. Such an approach significantly lowers the barrier to entry for adopting advanced manufacturing technologies.
The ROI on these automated systems can be remarkably quick – often within just a few months. This speed is due to their high productivity and the ability to start producing complex parts almost immediately after leasing. Companies like ADD Composites are at the forefront of making these systems accessible and justifiable in terms of cost, especially for medium to high volume production.
Automated systems have evolved to use materials previously limited to hand layup processes. This includes wet winding to compete with traditional wet processes and the use of pre-impregnated materials (prepregs). While there is an additional cost for AFP and ATL materials due to slitting, this is often offset by the high volume of production and the savings on labor.
An often overlooked aspect of automated manufacturing is its capability for quality control through data capture. Unlike hand layup processes, automated systems can record detailed data during production, significantly reducing the cost associated with quality control. This is particularly crucial for industries with stringent quality requirements, where the cost of manual quality assurance can be prohibitively high.
A practical approach to automation is starting with a pilot project, leasing equipment from suppliers to gradually scale up and familiarize workers with the new technology. This step-by-step approach de-risks the transition, allowing for a smoother adoption of AFP, ATL, filament winding, and continuous fiber 3D printing technologies.
Automated composite manufacturing brings an unparalleled level of precision, consistency, and design flexibility, revolutionizing the way composite materials are utilized and applied.
A key advantage of automation is the seamless integration of design, manufacturing, and quality control processes. Advanced software tools, like AdPath, allow for digital twin simulations, providing a platform for design validation and defect detection even before the actual manufacturing begins. This pre-emptive approach ensures that potential issues are addressed early, saving time and resources.
Automated processes, equipped with sophisticated sensors and control systems, consistently produce high-quality parts, maintaining uniformity across high volumes. This consistency is crucial for industries that demand precision and reliability, such as aerospace and automotive.
Automation unlocks new possibilities in design. Techniques like helical printing and the ability to quickly change tools on robotic arms allow for a combination of AFP, 3D printing, filament winding, and ATL processes. This flexibility paves the way for hybrid materials to be used more effectively, enabling manufacturers to explore and innovate without the constraints of manual handling.
Automated manufacturing also facilitates the incorporation of structural health monitoring sensors into the composite structures, leading to the creation of 'smart' or '4D' structures. Furthermore, the precise material placement capabilities of automated systems make them ideal for utilizing sustainable, naturally sourced materials like jute or bamboo fibers. This not only enhances the sustainability aspect but also maximizes the strength and functionality of these materials in high-quality applications, such as sports equipment.
The precision and efficiency of automated composite manufacturing have the potential to reduce raw material costs significantly. This cost reduction is vital for composites to compete effectively with traditional materials like metals, opening up broader applications and market opportunities.
As we reach the conclusion of our exploration into automated composite manufacturing, it's clear that this field represents not just an evolution in technology, but a pivotal shift in how industries approach production.
For businesses looking to embark on their journey towards automation, the following steps can help in de-risking the transition:
The future of composite manufacturing is inherently tied to automation. This technology not only meets the current demands of industries but also opens up new possibilities in design and material innovation. By embracing automated composite manufacturing, businesses can stay ahead in a competitive and ever-evolving landscape.
Discover the future of composite manufacturing with Addcomposites! Here's how you can get involved:
At Addcomposites, we are dedicated to revolutionizing composite manufacturing. Our AFP systems and comprehensive support services are waiting for you to harness. So, don't wait – get started on your journey to the future of manufacturing today!