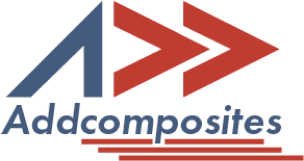
Composite materials have become a popular choice in the aerospace industry due to their lightweight, strong, and durable properties. They are made up of cloth or fibers and a matrix, which is an adhesive material that holds the fibers together. Composite materials have been used in the aerospace industry since the 1930s, and their usage has only increased with time. This blog will provide an overview of composite materials and their various applications in aerospace engineering.
Composite materials are made by combining two or more materials to create a material that has unique properties, such as strength, durability, and lightweight. The aerospace industry has been using composite materials since the 1930s, and their usage has only increased with time. Composite materials have become a popular choice in aerospace engineering due to their lightweight, strong, and durable properties.
Composite materials are found in nature, such as bones and bird nests, and can be man-made. Man-made composites include carbon fiber, glass fiber, and Kevlar.
Bones and bird nests are natural composites and are composed of a mesh framework of collagen, a leather-like material, and hydroxyapatite, a crystalline substance. This combination of a flexible mesh interwoven with a strong substrate material creates a strong, yet not overly brittle, structure.
Man-made composites, such as carbon fiber, glass fiber, and Kevlar, have been developed to create materials with similar properties. Glass fiber has a diameter of about 10 millimeters and is often used in boats, wind turbine blades, and some automobiles. Kevlar has a strength of more than three gigapascals and is often used in bulletproof vests, military helmets, and impact protection on aircraft. Carbon fiber has a diameter of about eight millimeters and is commonly used in high-performance race cars, fighter jets, and passenger aircraft.
Composite materials have a wide range of applications in aerospace engineering. Glass fiber is used in boats, wind turbine blades, and some automobiles. Kevlar is used in bulletproof vests, military helmets, and impact protection on aircraft. Carbon fiber is used in high-performance race cars, fighter jets, and passenger aircraft.
The aerospace industry started using composite materials as far back as the 1930s. Howard Hughes famously built his massive spruce goose flying boat using sheets of birch ply dura mold with phenolic resin laminated together at 138 centigrade. The first use of carbon fiber composites was in the 1960s on the compressor blades of the RB211 jet engine by Rolls-Royce.
Composite materials consist of two components, fibers, and a matrix. The matrix is an adhesive material that holds the fibers together. There are three main choices for matrix materials: phenolic, polyester, and epoxy.
Phenolic was the first modern resin and was used on wooden composite airplanes during World War II. It tends to be brittle and wets out the fibers badly but has good heat and fire resistance and does not produce toxic fumes in a fire. For this reason, it is often still used in aircraft and boat interiors. Polyester is the most used matrix for composite construction today, found in both holes and wind turbine blades. It does have poor chemical resistance and burns very easily. Epoxy is the most common matrix chosen for aerospace applications. It is very tough, lets out reinforcements very well, and has good chemical resistance. It is usually used in combination with carbon fiber for high-performance lightweight applications.
Composite materials have been chosen for several suborbital aerospace vehicles due to their lightweight and durability. Suborbital vehicles are in a completely different world than orbital vehicles.
The New Shepard rocket system is a suborbital tourist single-stage rocket and capsule configuration that goes straight up and comes back down. It does not turn to fire horizontally and does not even attempt to reach orbital velocity. It barely crosses the official von carmen line of 100 kilometers that denotes being in space.
The Virgin Galactic Spaceship 2 is a metal frame with composite materials used for the hull. This ship is also a space tourist suborbital transport vehicle and is carried to launch altitude by a composite-covered large carrier aircraft called White Knight. Once released, a hybrid rocket engine fires, carrying the ship above the Carmen line.
The Lynx was a unique space plane built for tourists that would have taken off from a runway like a regular airplane and come back the same way. Composite materials are perfect for these applications due to the relatively low velocity and atmospheres that they experience.
While composite materials are strong and durable, they do have limitations. The faster a ship travels through the atmosphere, the more heat-resistant it must be. Composite materials cannot survive temperatures above 200 degrees Celsius and become very brittle and weak with cryogenic temperature exposure.
Elon Musk discovered this when he tried to use composite materials for his innovative starship design. Once you get to larger volumes and colder cryogenic temperatures and must re-enter the atmosphere from orbital or translunar velocities, these materials are a poor choice.
The X-33 Venture Star was going to be a single-stage-to-orbit spaceship to replace the Space Shuttle. It was going to use an innovative linear aerospike engine that could have revolutionized rocket propulsion. However, composite materials had been chosen for the fuel tanks, and the engineers could not get the composite layers thick enough to prevent gas leakage and prevent fracturing from the very cold cryogenic fuels, especially liquid hydrogen. The engineers tried and tried to solve the problem, but they could not get it to work for hydrogen. The administrators told the engineers that they had to use composite tanks or the project would be canceled, and it was.
Composite materials are a vital part of aerospace engineering due to their lightweight, strong, and durable properties. Glass fiber, Kevlar, and carbon fiber are commonly used in the aerospace industry, along with matrix materials such as phenolic, polyester, and epoxy. Composite materials have been used in suborbital aerospace vehicles due to their lightweight and durability. However, these materials have limitations, and engineers must choose the right material for each application to ensure success.
Composite materials have become a popular choice in the aerospace industry due to their lightweight, strong, and durable properties. They are made up of cloth or fibers and a matrix, which is an adhesive material that holds the fibers together. Composite materials have been used in the aerospace industry since the 1930s, and their usage has only increased with time. This blog will provide an overview of composite materials and their various applications in aerospace engineering.
Composite materials are made by combining two or more materials to create a material that has unique properties, such as strength, durability, and lightweight. The aerospace industry has been using composite materials since the 1930s, and their usage has only increased with time. Composite materials have become a popular choice in aerospace engineering due to their lightweight, strong, and durable properties.
Composite materials are found in nature, such as bones and bird nests, and can be man-made. Man-made composites include carbon fiber, glass fiber, and Kevlar.
Bones and bird nests are natural composites and are composed of a mesh framework of collagen, a leather-like material, and hydroxyapatite, a crystalline substance. This combination of a flexible mesh interwoven with a strong substrate material creates a strong, yet not overly brittle, structure.
Man-made composites, such as carbon fiber, glass fiber, and Kevlar, have been developed to create materials with similar properties. Glass fiber has a diameter of about 10 millimeters and is often used in boats, wind turbine blades, and some automobiles. Kevlar has a strength of more than three gigapascals and is often used in bulletproof vests, military helmets, and impact protection on aircraft. Carbon fiber has a diameter of about eight millimeters and is commonly used in high-performance race cars, fighter jets, and passenger aircraft.
Composite materials have a wide range of applications in aerospace engineering. Glass fiber is used in boats, wind turbine blades, and some automobiles. Kevlar is used in bulletproof vests, military helmets, and impact protection on aircraft. Carbon fiber is used in high-performance race cars, fighter jets, and passenger aircraft.
The aerospace industry started using composite materials as far back as the 1930s. Howard Hughes famously built his massive spruce goose flying boat using sheets of birch ply dura mold with phenolic resin laminated together at 138 centigrade. The first use of carbon fiber composites was in the 1960s on the compressor blades of the RB211 jet engine by Rolls-Royce.
Composite materials consist of two components, fibers, and a matrix. The matrix is an adhesive material that holds the fibers together. There are three main choices for matrix materials: phenolic, polyester, and epoxy.
Phenolic was the first modern resin and was used on wooden composite airplanes during World War II. It tends to be brittle and wets out the fibers badly but has good heat and fire resistance and does not produce toxic fumes in a fire. For this reason, it is often still used in aircraft and boat interiors. Polyester is the most used matrix for composite construction today, found in both holes and wind turbine blades. It does have poor chemical resistance and burns very easily. Epoxy is the most common matrix chosen for aerospace applications. It is very tough, lets out reinforcements very well, and has good chemical resistance. It is usually used in combination with carbon fiber for high-performance lightweight applications.
Composite materials have been chosen for several suborbital aerospace vehicles due to their lightweight and durability. Suborbital vehicles are in a completely different world than orbital vehicles.
The New Shepard rocket system is a suborbital tourist single-stage rocket and capsule configuration that goes straight up and comes back down. It does not turn to fire horizontally and does not even attempt to reach orbital velocity. It barely crosses the official von carmen line of 100 kilometers that denotes being in space.
The Virgin Galactic Spaceship 2 is a metal frame with composite materials used for the hull. This ship is also a space tourist suborbital transport vehicle and is carried to launch altitude by a composite-covered large carrier aircraft called White Knight. Once released, a hybrid rocket engine fires, carrying the ship above the Carmen line.
The Lynx was a unique space plane built for tourists that would have taken off from a runway like a regular airplane and come back the same way. Composite materials are perfect for these applications due to the relatively low velocity and atmospheres that they experience.
While composite materials are strong and durable, they do have limitations. The faster a ship travels through the atmosphere, the more heat-resistant it must be. Composite materials cannot survive temperatures above 200 degrees Celsius and become very brittle and weak with cryogenic temperature exposure.
Elon Musk discovered this when he tried to use composite materials for his innovative starship design. Once you get to larger volumes and colder cryogenic temperatures and must re-enter the atmosphere from orbital or translunar velocities, these materials are a poor choice.
The X-33 Venture Star was going to be a single-stage-to-orbit spaceship to replace the Space Shuttle. It was going to use an innovative linear aerospike engine that could have revolutionized rocket propulsion. However, composite materials had been chosen for the fuel tanks, and the engineers could not get the composite layers thick enough to prevent gas leakage and prevent fracturing from the very cold cryogenic fuels, especially liquid hydrogen. The engineers tried and tried to solve the problem, but they could not get it to work for hydrogen. The administrators told the engineers that they had to use composite tanks or the project would be canceled, and it was.
Composite materials are a vital part of aerospace engineering due to their lightweight, strong, and durable properties. Glass fiber, Kevlar, and carbon fiber are commonly used in the aerospace industry, along with matrix materials such as phenolic, polyester, and epoxy. Composite materials have been used in suborbital aerospace vehicles due to their lightweight and durability. However, these materials have limitations, and engineers must choose the right material for each application to ensure success.