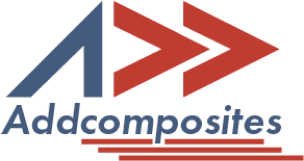
This article aims to provide
Specific details of how to improve thermoplastic placement quality
An overview of in-situ consolidation (ISC) is provided in this article. As the ISC manufacturing process evolves, it is additive in nature, limited by the orthotropic nature of composite materials, and thermoplastic matrix behavior. Key topics covered are as follows
The article is intended to help readers understand the key process parameters and enable them to achieve high product quality with a high deposition rate. This is achieved through an industrial process that is competitive with the current thermoset composite manufacturing process.
The development of thermoplastic polymeric matrix materials has not yet reached the same level as thermosets. This may be because of high process temperatures and lower productivity with thermoplastics. As opposed to thermoset composite materials, thermoplastic composite materials have no tackiness at room temperature and are solid at room temperature. Despite the fact that the matrix has already been polymerized, the viscosity values remain very high, making the process more complex and expensive than thermosets.
A thermoset AFP system with speeds of one meter per second is used to fabricate large structures. The material is partially cured, so it retains its tackiness, which makes it possible to join the different layers without any heating. During the second step, the completed layup needs to be placed in vacuum bags to be autoclave cured. The second step is highly manual and requires a huge autoclave i.e. pressurized oven, making the entire process extremely slow and expensive.
Thermoplastic AFP processes lack the tackiness between layers at room temperature, as opposed to Thermoset AFP, and require higher temperatures to melt the material (semi-crystalline) or to transition to glass (amorphous). As a result, it allows for the lay-up to be completed, while simultaneously ensuring high-quality bonding between layers, suppressing the need for subsequent curing stages in an oven or autoclave.
In situ consolidation refers to the placement of thermoplastic composite layers simultaneously while ensuring high-quality bonding between them. This process involves multiple physical parameters that take place simultaneously involving heating, cooling, pressure, placement speed, material FVF, tooling, and environmental temperature. If this process is to be applied in a profitable way, it must achieve high degrees of consolidation without having to repeat the re-consolidation process in an oven/autoclave twice.
When tool temperatures approach the melting temperature of the polymer used in the tape, the trend of decreasing void volume reverses. When the temperature is low, the tool usually acts as a heat sink, causing a high viscosity that prevents smooth movement of the chains. It is necessary to slow down the placement speed in this case due to the low degree of bonding. Alternatively, when the tool is heated to a high temperature (around 573 K for PEEK), effective bonding is achieved even close to 1.5 m/sec.
Bonding increases as contact forces rise, as is expected, and void content decreases as well. Its effect is more evident as the layup speed increases (the faster the layup, the greater the force). As a result of increasing force and increased speed, the porosity should decrease, whereas the degree of bonding decreases with speed despite increasing force.
When the number of layers of a laminate is high, a double effect occurs; the lower ones receive more consolidation stages (reconsolidation), but the upper ones are more isolated from the tooling surface. As a result, they experience increased heating, resulting in larger pores.
The level of porosity is increased by longer heating durations. In contrast, bonding is better, and the process can be carried out faster. Heating length and heating time are directly related since they depend on the speed of lamination.
Improvements in the taped material quality could improve the thermoplastic AFP layup
Effect of additive approach: As a result of the sequential increase in layers of material, the layup process also has a penalizing effect. This leaves the material in an unfavorable state from the standpoint of stress. When the laminate cools evenly, as it does in an autoclave, rather than being consolidated layer-by-layer, the residual stresses are different. Depending on the residual stress gradients, microcracks may develop in the resin when annealing over Tg.
In order to achieve a progressive drop in temperature when the tape and substrate come into contact, resulting in more progressive cooling and therefore reducing residual stresses.
A higher fiber placement speed increases residual stresses because there are more point zones experiencing higher thermal gradients.
Residual stress is also affected by the size of the heated surface. The smaller the heated surface, the sharper the heating-cooling profiles. Better results are observed when the heated surface of the substrate is larger than that of the contribution.
To achieve a higher surface finish, it is preferred to cool the roller with internal fluidic flow
It was first patented by DuPont in 1986 (layup method and equipment patent),
A patent issued by Northrop Corporation, an American aircraft manufacturer, on this topic was issued in 1991. It proposes to use a heated roller and a cooling system to accomplish this.
In 2002, Boeing also protected its work on the heating method and heating control system used in composite material layup, without specifying the type.
Using a technology called co-consolidation, Airbus filed a patent in 2003 to protect the development of a layup with integration
Following this, many machine manufacturers protected the following features
It is necessary to describe the adhesion mechanism between the layers of composite materials in a manner that takes into account two factors: On the one hand, it is necessary to eliminate surface roughness in the incoming material in order to allow the polymer chains to move, and, on the other hand, a mechanism that controls this movement of chains.
As a result of the inherent irregularities in the surfaces of thermoplastic pre-impregnated composite materials, gaps occur between two surfaces that are brought into contact without applying pressure or temperature. Since thermoplastic resins have high viscosities, they are limited in their ability to cover these areas by natural flow, so pressing both surfaces is necessary (application of pressure) to force their contact.
As two polymeric surfaces come into contact at temperatures above their glass transition, a diffusion of polymer chains occurs at the interface, often referred to as healing, diffusion, or self-adhesion. In order to develop a resistant joint, chains must diffuse correctly so that the interface becomes indistinguishable.
After obtaining the degree of intimate contact and diffusion, it is possible to combine their results to determine the degree to which the bonds are generally formed. Since the contact time is limited, diffusion has a small effect on bonding. Temperature is largely determined by speed, heat source, and material properties.
Crystallization is one of the key factors in the development of certain mechanical or structural properties. During crystallization amorphous material nucleates and grows spherulitic. Transcrystallization is a process of crystal growth affected by restricted space, which is representative of fiber-reinforced composite crystallization behaviors.
As a result of the high adhesion between resin and fiber, the highest value is achieved at lower cooling speeds. It is possible for the mechanical properties of a material to vary because of the correct or incorrect development of the transcrystalline layer during cooling
Thermal degradation is the irreversible loss of physical, mechanical, or electrical properties of a polymer due to the action of heat or high temperatures.
As polymeric materials decay, their long molecules break down into smaller segments that can be volatile. As soon as the fragments are generated, their evaporation ability increases; the rest of the molecules remain in the condensed phase (liquid or solid) and continue to decompose until the fragments are of the appropriate size.
The in-situ consolidation process for manufacturing thermoplastic composites is a delicate balance between a lot of parameters, as summarized below
This article aims to provide
Specific details of how to improve thermoplastic placement quality
An overview of in-situ consolidation (ISC) is provided in this article. As the ISC manufacturing process evolves, it is additive in nature, limited by the orthotropic nature of composite materials, and thermoplastic matrix behavior. Key topics covered are as follows
The article is intended to help readers understand the key process parameters and enable them to achieve high product quality with a high deposition rate. This is achieved through an industrial process that is competitive with the current thermoset composite manufacturing process.
The development of thermoplastic polymeric matrix materials has not yet reached the same level as thermosets. This may be because of high process temperatures and lower productivity with thermoplastics. As opposed to thermoset composite materials, thermoplastic composite materials have no tackiness at room temperature and are solid at room temperature. Despite the fact that the matrix has already been polymerized, the viscosity values remain very high, making the process more complex and expensive than thermosets.
A thermoset AFP system with speeds of one meter per second is used to fabricate large structures. The material is partially cured, so it retains its tackiness, which makes it possible to join the different layers without any heating. During the second step, the completed layup needs to be placed in vacuum bags to be autoclave cured. The second step is highly manual and requires a huge autoclave i.e. pressurized oven, making the entire process extremely slow and expensive.
Thermoplastic AFP processes lack the tackiness between layers at room temperature, as opposed to Thermoset AFP, and require higher temperatures to melt the material (semi-crystalline) or to transition to glass (amorphous). As a result, it allows for the lay-up to be completed, while simultaneously ensuring high-quality bonding between layers, suppressing the need for subsequent curing stages in an oven or autoclave.
In situ consolidation refers to the placement of thermoplastic composite layers simultaneously while ensuring high-quality bonding between them. This process involves multiple physical parameters that take place simultaneously involving heating, cooling, pressure, placement speed, material FVF, tooling, and environmental temperature. If this process is to be applied in a profitable way, it must achieve high degrees of consolidation without having to repeat the re-consolidation process in an oven/autoclave twice.
When tool temperatures approach the melting temperature of the polymer used in the tape, the trend of decreasing void volume reverses. When the temperature is low, the tool usually acts as a heat sink, causing a high viscosity that prevents smooth movement of the chains. It is necessary to slow down the placement speed in this case due to the low degree of bonding. Alternatively, when the tool is heated to a high temperature (around 573 K for PEEK), effective bonding is achieved even close to 1.5 m/sec.
Bonding increases as contact forces rise, as is expected, and void content decreases as well. Its effect is more evident as the layup speed increases (the faster the layup, the greater the force). As a result of increasing force and increased speed, the porosity should decrease, whereas the degree of bonding decreases with speed despite increasing force.
When the number of layers of a laminate is high, a double effect occurs; the lower ones receive more consolidation stages (reconsolidation), but the upper ones are more isolated from the tooling surface. As a result, they experience increased heating, resulting in larger pores.
The level of porosity is increased by longer heating durations. In contrast, bonding is better, and the process can be carried out faster. Heating length and heating time are directly related since they depend on the speed of lamination.
Improvements in the taped material quality could improve the thermoplastic AFP layup
Effect of additive approach: As a result of the sequential increase in layers of material, the layup process also has a penalizing effect. This leaves the material in an unfavorable state from the standpoint of stress. When the laminate cools evenly, as it does in an autoclave, rather than being consolidated layer-by-layer, the residual stresses are different. Depending on the residual stress gradients, microcracks may develop in the resin when annealing over Tg.
In order to achieve a progressive drop in temperature when the tape and substrate come into contact, resulting in more progressive cooling and therefore reducing residual stresses.
A higher fiber placement speed increases residual stresses because there are more point zones experiencing higher thermal gradients.
Residual stress is also affected by the size of the heated surface. The smaller the heated surface, the sharper the heating-cooling profiles. Better results are observed when the heated surface of the substrate is larger than that of the contribution.
To achieve a higher surface finish, it is preferred to cool the roller with internal fluidic flow
It was first patented by DuPont in 1986 (layup method and equipment patent),
A patent issued by Northrop Corporation, an American aircraft manufacturer, on this topic was issued in 1991. It proposes to use a heated roller and a cooling system to accomplish this.
In 2002, Boeing also protected its work on the heating method and heating control system used in composite material layup, without specifying the type.
Using a technology called co-consolidation, Airbus filed a patent in 2003 to protect the development of a layup with integration
Following this, many machine manufacturers protected the following features
It is necessary to describe the adhesion mechanism between the layers of composite materials in a manner that takes into account two factors: On the one hand, it is necessary to eliminate surface roughness in the incoming material in order to allow the polymer chains to move, and, on the other hand, a mechanism that controls this movement of chains.
As a result of the inherent irregularities in the surfaces of thermoplastic pre-impregnated composite materials, gaps occur between two surfaces that are brought into contact without applying pressure or temperature. Since thermoplastic resins have high viscosities, they are limited in their ability to cover these areas by natural flow, so pressing both surfaces is necessary (application of pressure) to force their contact.
As two polymeric surfaces come into contact at temperatures above their glass transition, a diffusion of polymer chains occurs at the interface, often referred to as healing, diffusion, or self-adhesion. In order to develop a resistant joint, chains must diffuse correctly so that the interface becomes indistinguishable.
After obtaining the degree of intimate contact and diffusion, it is possible to combine their results to determine the degree to which the bonds are generally formed. Since the contact time is limited, diffusion has a small effect on bonding. Temperature is largely determined by speed, heat source, and material properties.
Crystallization is one of the key factors in the development of certain mechanical or structural properties. During crystallization amorphous material nucleates and grows spherulitic. Transcrystallization is a process of crystal growth affected by restricted space, which is representative of fiber-reinforced composite crystallization behaviors.
As a result of the high adhesion between resin and fiber, the highest value is achieved at lower cooling speeds. It is possible for the mechanical properties of a material to vary because of the correct or incorrect development of the transcrystalline layer during cooling
Thermal degradation is the irreversible loss of physical, mechanical, or electrical properties of a polymer due to the action of heat or high temperatures.
As polymeric materials decay, their long molecules break down into smaller segments that can be volatile. As soon as the fragments are generated, their evaporation ability increases; the rest of the molecules remain in the condensed phase (liquid or solid) and continue to decompose until the fragments are of the appropriate size.
The in-situ consolidation process for manufacturing thermoplastic composites is a delicate balance between a lot of parameters, as summarized below