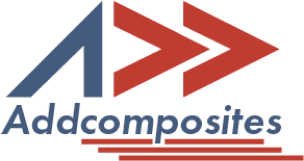
The manufacturing industry stands at the cusp of a revolutionary transformation, driven by the seamless integration of artificial intelligence (AI) and robotics. Nowhere is this evolution more apparent than in the field of continuous fiber composites manufacturing, where these technologies are fundamentally reshaping production processes and unlocking unprecedented possibilities. This comprehensive analysis explores how AI and robotics are revolutionizing the composites manufacturing landscape, with particular attention to processes like Automated Fiber Placement (AFP), continuous fiber 3D printing, winding, and braiding.
The implementation of AI in composites manufacturing has ushered in a new era of innovation and efficiency. In the realm of material discovery, AI algorithms and generative models are transforming how we develop new composite materials. These sophisticated systems enable virtual experimentation with various material compositions and microstructures, significantly reducing the need for costly physical testing while accelerating the development of materials with enhanced properties.
Manufacturing optimization through AI represents another significant advancement in the field. Advanced AI algorithms analyze data from sophisticated imaging techniques in real-time, allowing for immediate adjustments to manufacturing processes. This capability has proven particularly valuable in Automated Fiber Placement (AFP), where precision and consistency are paramount.
Quality assurance has seen remarkable improvements through the integration of AI-powered analysis tools with traditional inspection methods. These systems excel at identifying potential defects and assessing material microstructures, ensuring higher product quality and reliability. The ability to detect and address issues in real-time has significantly reduced waste and improved overall manufacturing efficiency.
The role of robotics in composites manufacturing has evolved from simple automation to sophisticated, intelligent systems capable of handling complex manufacturing tasks. Automated Fiber Placement represents one of the most significant applications of robotics in the field. Robotic systems precisely lay down continuous fiber tapes, creating complex laminated structures with unprecedented accuracy and consistency.
In the realm of additive manufacturing, robots have revolutionized 3D printing with composite materials. These systems can create intricate geometries and customized parts that would be impossible to produce through traditional manufacturing methods. The precision and flexibility of robotic systems have opened new possibilities in design and production.
The evolution of robotic winding processes has transformed how manufacturers approach fiber and resin placement. These advanced systems have not only improved efficiency but also enabled the production of more complex and precise components, particularly in the aerospace and automotive industries.
The combination of AI and robotics in composites manufacturing has created a synergistic effect that extends beyond the sum of their individual benefits. This integration has led to substantial reductions in material waste through optimized usage patterns and improved production processes. The enhanced precision and consistency achieved through these technologies have resulted in higher quality products with fewer defects.
Manufacturing efficiency has seen remarkable improvements, with AI-driven robotics systems operating continuously while maintaining consistent quality levels. These systems have also contributed to safer working environments by handling hazardous tasks and reducing human exposure to potentially dangerous materials and processes.
While the benefits of AI and robotics in composites manufacturing are clear, organizations face several important challenges in their implementation. The initial investment in robotic systems represents a significant financial commitment, requiring careful consideration of return on investment and long-term strategic planning. Additionally, these systems demand specialized programming skills and expertise, which may necessitate substantial training investments or new hiring initiatives.
The data requirements for effective AI implementation present another crucial consideration. Manufacturing organizations must develop robust data collection and management systems to support AI-driven decision-making and process optimization. Integration with existing manufacturing systems and workflows requires careful planning and execution to ensure smooth operations.
The future of AI and robotics in composites manufacturing appears increasingly promising. Industry experts anticipate greater adoption of collaborative robots (cobots) designed to work alongside human operators. The integration of AI with robotics will continue to deepen, leading to more intelligent and adaptive manufacturing systems.
We can expect to see these technologies expand into new applications and industries, with a particular focus on sustainability and efficiency. The rise of humanoid robots in manufacturing environments may offer new solutions to complex manufacturing challenges, especially in areas requiring human-like dexterity and adaptability.
Success in this evolving landscape requires a thoughtful and comprehensive approach to technology adoption. Organizations should prioritize comprehensive training programs that prepare their workforce for these new technologies. A clear implementation strategy, beginning with carefully selected pilot projects, can help organizations navigate the transition effectively.
Partnerships with technology providers and a commitment to fostering innovation within the organization will be crucial for long-term success. Manufacturers should also focus on developing the internal expertise needed to maintain and optimize these systems over time.
The integration of AI and robotics in continuous fiber composites manufacturing represents a fundamental shift in how we approach production processes. These technologies offer unprecedented opportunities for improvement in efficiency, quality, and innovation. While challenges exist, particularly in implementation and training, the potential benefits far outweigh the obstacles.
For manufacturers looking to maintain competitiveness in an increasingly advanced industry, embracing these technological advances while preparing their workforce for the future will be crucial. Through careful planning and implementation, organizations can leverage AI and robotics to create more efficient, sustainable, and innovative manufacturing processes.
For deeper insights into specific aspects of composite manufacturing, explore our detailed guides on Automated Fiber Placement, Continuous Fiber 3D Printing, and Advanced Composites Manufacturing.