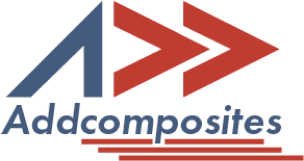
In the race towards a sustainable energy future, hydrogen has emerged as a promising clean energy carrier. As the demand for hydrogen-powered vehicles and applications grows, so does the need for efficient, safe, and cost-effective hydrogen storage solutions. At the heart of this challenge lies the hydrogen tank – a critical component that must withstand high pressures while remaining lightweight and durable.
Two manufacturing methods have risen to prominence in the production of these advanced composite pressure vessels: AFP and Filament Winding. Each of these techniques brings its own set of advantages and limitations to the table, shaping the landscape of hydrogen tank production.
In this blog post, we'll delve into the intricacies of AFP and Filament Winding, comparing their capabilities, efficiencies, and applications in the context of hydrogen tank manufacturing. We'll also explore an exciting development in the field – the AFP-XS system – which promises to combine the strengths of both methods, potentially revolutionizing the production process for industries with lower production volumes, such as aerospace, space, defense, and marine sectors.
Join us as we unravel the complexities of these manufacturing techniques and discover how the fusion of AFP and Filament Winding capabilities could pave the way for more versatile, efficient, and cost-effective hydrogen tank production.
To fully appreciate the comparison between AFP and Filament Winding, it's essential to understand the basics of each technology. Let's explore these two manufacturing methods in detail.
Automated Fiber Placement is an advanced manufacturing process that precisely lays down multiple narrow strips of composite material, called tows, onto a mold surface.
Filament Winding is a more traditional composite manufacturing process where continuous reinforcement fibers, often pre-impregnated with resin, are wound around a rotating mandrel.
Both AFP and Filament Winding have their strengths and are suited to different applications. Understanding these characteristics is crucial when deciding which method to use for hydrogen tank production.
When it comes to producing hydrogen tanks, both Automated Fiber Placement (AFP) and Filament Winding offer unique advantages and face distinct challenges. Understanding these differences is crucial for manufacturers in choosing the right technology for their specific needs.
Filament Winding has long been the go-to method for producing cylindrical and spherical pressure vessels. Its maturity brings reliability and a well-understood process, making it a safe choice for many manufacturers. However, this traditional approach comes with limitations in design flexibility.
In contrast, AFP represents a leap forward in manufacturing technology. Its ability to place fibers with high precision allows for complex geometries and optimized fiber orientations. This flexibility opens up new possibilities in tank design, potentially leading to lighter and more efficient structures. However, the relative newness of AFP technology means it's still gaining ground in terms of widespread adoption and long-term proven reliability.
When it comes to production speed, Filament Winding can be highly efficient for simple, symmetrical shapes. It's particularly well-suited for high-volume production of standard designs. However, this efficiency can decrease when dealing with more complex geometries.
AFP, while potentially slower for simple shapes, shines in the production of complex parts. Its precision can lead to significant material savings, as it allows for optimized fiber placement and reduced waste. This is particularly valuable when working with expensive composite materials.
Quality control in Filament Winding often relies heavily on operator skill and experience. While this can lead to high-quality products, it also introduces the potential for variability between production runs.
AFP, with its highly automated nature, offers superior consistency in production. Advanced control systems and real-time monitoring capabilities ensure that each layer is placed with high precision, leading to more uniform products. This consistency is crucial for applications where performance reliability is paramount, such as in the aerospace industry.
The cost equation for these technologies is not straightforward. Filament Winding generally has lower initial equipment costs, making it more accessible for smaller operations or those with limited capital. However, the long-term costs can be higher due to material waste and labor requirements.
AFP systems represent a significant upfront investment. However, they can offer long-term cost benefits through reduced material waste, lower labor costs, and the ability to produce more complex, high-value parts. For manufacturers looking at long-term production or those working with high-value materials, AFP can provide a strong return on investment.
As sustainability becomes an increasingly important factor in manufacturing decisions, the environmental impact of these technologies comes into focus. Filament Winding, while efficient, can produce more waste, especially when working with complex shapes.
AFP's precision placement can significantly reduce material waste. Moreover, some AFP systems are capable of working with thermoplastic composites, which are more easily recycled than traditional thermoset materials. This aligns well with the growing emphasis on sustainable manufacturing practices in the composites industry.
As we've seen, both AFP and Filament Winding have their unique advantages in composite manufacturing. But what if we could combine the best features of both technologies? Enter the AFP-XS System, a innovative solution that bridges the gap between these two methods.
The AFP-XS System is a cutting-edge manufacturing technology that integrates the precision and flexibility of Automated Fiber Placement with the simplicity and speed of Filament Winding. This hybrid approach offers a versatile solution for producing complex composite structures, including hydrogen tanks.
The AFP-XS System represents a significant advancement in composite manufacturing technology, offering a flexible and efficient solution for producing high-performance hydrogen tanks and other complex composite structures.
The advanced manufacturing techniques of Automated Fiber Placement (AFP), Filament Winding, and the hybrid AFP-XS system have found their way into various industries, each leveraging these technologies to meet their unique challenges and requirements.
In the aerospace industry, where every gram matters, AFP has become a game-changer. This technology allows for the creation of complex, lightweight structures that are crucial for fuel efficiency and performance. For instance, AFP is used in manufacturing fuselage sections and wing spars, where its precision in fiber placement results in optimized strength-to-weight ratios.
Filament Winding, while less common in modern aircraft manufacturing, still plays a role in producing cylindrical structures like rocket motor casings. Its efficiency in creating symmetrical, high-strength components makes it valuable in specific aerospace applications.
The AFP-XS system, with its ability to switch between AFP and Filament Winding modes, offers aerospace manufacturers unprecedented flexibility. This hybrid approach is particularly useful in producing components that require both complex geometries and cylindrical sections, such as next-generation aircraft designs or space vehicle structures.
As the automotive industry shifts towards alternative fuels, hydrogen fuel cell vehicles are gaining traction. Here, the manufacturing of high-pressure hydrogen storage tanks becomes critical. Filament Winding has traditionally been the go-to method for producing these cylindrical tanks, offering a cost-effective solution for high-volume production.
However, AFP is making inroads in this sector, particularly for more complex tank designs that aim to optimize storage capacity and vehicle integration. The precision of AFP allows for tanks with non-cylindrical sections, potentially improving the packaging efficiency within the vehicle.
The AFP-XS system presents an intriguing option for automotive manufacturers. It allows for the efficient production of traditional cylindrical tanks while also offering the flexibility to create more advanced designs as the technology and market evolve.
In the marine industry, the corrosion resistance and light weight of composite materials make them increasingly attractive. Filament Winding has long been used to produce cylindrical structures like submarine hulls and pipelines, where its ability to create strong, seamless tubes is advantageous.
AFP is finding applications in creating large, complex hull structures and masts. Its ability to precisely lay fibers over large, curved surfaces results in optimized structures that can withstand the harsh marine environment while minimizing weight.
The versatility of the AFP-XS system is particularly valuable in shipbuilding, where a wide range of components with varying geometries are required. From cylindrical sections to complex hull shapes, this hybrid system can adapt to diverse manufacturing needs within a single facility.
The energy sector, particularly in renewable energy storage, is another area where these manufacturing technologies are making an impact. Large-scale hydrogen storage tanks for energy applications often rely on Filament Winding for their construction, due to its efficiency in producing large cylindrical vessels.
However, as designs for hydrogen storage systems become more advanced, AFP is gaining relevance. Its precision can be crucial in creating storage solutions that integrate more seamlessly with other energy infrastructure or in producing tanks with optimized geometries for specific installation requirements.
The AFP-XS system offers energy infrastructure developers the flexibility to produce both traditional cylindrical tanks and more complex storage solutions. This adaptability could be key in creating the diverse range of hydrogen storage solutions needed for a comprehensive clean energy ecosystem.
In each of these industries, the choice between AFP, Filament Winding, or the hybrid AFP-XS system depends on factors such as production volume, part complexity, performance requirements, and cost considerations. The AFP-XS system, in particular, offers a versatile solution for industries with diverse manufacturing needs or those looking to optimize their production processes across different product lines.
As we've explored throughout this blog post, the production of hydrogen tanks represents a critical challenge in the ongoing transition to clean energy. The manufacturing methods we've discussed – Automated Fiber Placement (AFP), Filament Winding, and the innovative AFP-XS system – each play a vital role in addressing this challenge.
AFP excels in precision and flexibility, allowing for complex geometries and optimized fiber orientations. It's particularly valuable for high-performance applications where weight optimization is crucial.
Filament Winding offers simplicity and cost-effectiveness, especially for cylindrical or spherical shapes. Its established nature makes it a reliable choice for many traditional applications.
Both methods have their strengths, and the choice between them often depends on specific project requirements, production volumes, and cost considerations.
The emergence of hybrid systems like AFP-XS represents a significant leap forward in composite manufacturing technology. By combining the strengths of both AFP and Filament Winding, these systems offer:
As the demand for hydrogen storage solutions continues to grow across various industries – from aerospace and automotive to marine and energy – we can expect to see further innovations in manufacturing technologies. The trend towards more versatile, efficient, and sustainable production methods is likely to continue, with hybrid systems like AFP-XS potentially playing a central role.
For industries considering the production of hydrogen tanks or other composite structures, it's crucial to carefully evaluate the benefits of each manufacturing method. While traditional AFP and Filament Winding remain valuable options, the advantages offered by hybrid systems make them an increasingly attractive choice, especially for those seeking to balance performance, efficiency, and adaptability.
As we move forward, the continued development of these manufacturing technologies will be key to realizing the full potential of hydrogen as a clean energy carrier, contributing to a more sustainable future across multiple sectors.
Discover the future of composite manufacturing with Addcomposites! Here's how you can get involved:
At Addcomposites, we are dedicated to revolutionizing composite manufacturing. Our AFP systems and comprehensive support services are waiting for you to harness. So, don't wait – get started on your journey to the future of manufacturing today!
In the race towards a sustainable energy future, hydrogen has emerged as a promising clean energy carrier. As the demand for hydrogen-powered vehicles and applications grows, so does the need for efficient, safe, and cost-effective hydrogen storage solutions. At the heart of this challenge lies the hydrogen tank – a critical component that must withstand high pressures while remaining lightweight and durable.
Two manufacturing methods have risen to prominence in the production of these advanced composite pressure vessels: AFP and Filament Winding. Each of these techniques brings its own set of advantages and limitations to the table, shaping the landscape of hydrogen tank production.
In this blog post, we'll delve into the intricacies of AFP and Filament Winding, comparing their capabilities, efficiencies, and applications in the context of hydrogen tank manufacturing. We'll also explore an exciting development in the field – the AFP-XS system – which promises to combine the strengths of both methods, potentially revolutionizing the production process for industries with lower production volumes, such as aerospace, space, defense, and marine sectors.
Join us as we unravel the complexities of these manufacturing techniques and discover how the fusion of AFP and Filament Winding capabilities could pave the way for more versatile, efficient, and cost-effective hydrogen tank production.
To fully appreciate the comparison between AFP and Filament Winding, it's essential to understand the basics of each technology. Let's explore these two manufacturing methods in detail.
Automated Fiber Placement is an advanced manufacturing process that precisely lays down multiple narrow strips of composite material, called tows, onto a mold surface.
Filament Winding is a more traditional composite manufacturing process where continuous reinforcement fibers, often pre-impregnated with resin, are wound around a rotating mandrel.
Both AFP and Filament Winding have their strengths and are suited to different applications. Understanding these characteristics is crucial when deciding which method to use for hydrogen tank production.
When it comes to producing hydrogen tanks, both Automated Fiber Placement (AFP) and Filament Winding offer unique advantages and face distinct challenges. Understanding these differences is crucial for manufacturers in choosing the right technology for their specific needs.
Filament Winding has long been the go-to method for producing cylindrical and spherical pressure vessels. Its maturity brings reliability and a well-understood process, making it a safe choice for many manufacturers. However, this traditional approach comes with limitations in design flexibility.
In contrast, AFP represents a leap forward in manufacturing technology. Its ability to place fibers with high precision allows for complex geometries and optimized fiber orientations. This flexibility opens up new possibilities in tank design, potentially leading to lighter and more efficient structures. However, the relative newness of AFP technology means it's still gaining ground in terms of widespread adoption and long-term proven reliability.
When it comes to production speed, Filament Winding can be highly efficient for simple, symmetrical shapes. It's particularly well-suited for high-volume production of standard designs. However, this efficiency can decrease when dealing with more complex geometries.
AFP, while potentially slower for simple shapes, shines in the production of complex parts. Its precision can lead to significant material savings, as it allows for optimized fiber placement and reduced waste. This is particularly valuable when working with expensive composite materials.
Quality control in Filament Winding often relies heavily on operator skill and experience. While this can lead to high-quality products, it also introduces the potential for variability between production runs.
AFP, with its highly automated nature, offers superior consistency in production. Advanced control systems and real-time monitoring capabilities ensure that each layer is placed with high precision, leading to more uniform products. This consistency is crucial for applications where performance reliability is paramount, such as in the aerospace industry.
The cost equation for these technologies is not straightforward. Filament Winding generally has lower initial equipment costs, making it more accessible for smaller operations or those with limited capital. However, the long-term costs can be higher due to material waste and labor requirements.
AFP systems represent a significant upfront investment. However, they can offer long-term cost benefits through reduced material waste, lower labor costs, and the ability to produce more complex, high-value parts. For manufacturers looking at long-term production or those working with high-value materials, AFP can provide a strong return on investment.
As sustainability becomes an increasingly important factor in manufacturing decisions, the environmental impact of these technologies comes into focus. Filament Winding, while efficient, can produce more waste, especially when working with complex shapes.
AFP's precision placement can significantly reduce material waste. Moreover, some AFP systems are capable of working with thermoplastic composites, which are more easily recycled than traditional thermoset materials. This aligns well with the growing emphasis on sustainable manufacturing practices in the composites industry.
As we've seen, both AFP and Filament Winding have their unique advantages in composite manufacturing. But what if we could combine the best features of both technologies? Enter the AFP-XS System, a innovative solution that bridges the gap between these two methods.
The AFP-XS System is a cutting-edge manufacturing technology that integrates the precision and flexibility of Automated Fiber Placement with the simplicity and speed of Filament Winding. This hybrid approach offers a versatile solution for producing complex composite structures, including hydrogen tanks.
The AFP-XS System represents a significant advancement in composite manufacturing technology, offering a flexible and efficient solution for producing high-performance hydrogen tanks and other complex composite structures.
The advanced manufacturing techniques of Automated Fiber Placement (AFP), Filament Winding, and the hybrid AFP-XS system have found their way into various industries, each leveraging these technologies to meet their unique challenges and requirements.
In the aerospace industry, where every gram matters, AFP has become a game-changer. This technology allows for the creation of complex, lightweight structures that are crucial for fuel efficiency and performance. For instance, AFP is used in manufacturing fuselage sections and wing spars, where its precision in fiber placement results in optimized strength-to-weight ratios.
Filament Winding, while less common in modern aircraft manufacturing, still plays a role in producing cylindrical structures like rocket motor casings. Its efficiency in creating symmetrical, high-strength components makes it valuable in specific aerospace applications.
The AFP-XS system, with its ability to switch between AFP and Filament Winding modes, offers aerospace manufacturers unprecedented flexibility. This hybrid approach is particularly useful in producing components that require both complex geometries and cylindrical sections, such as next-generation aircraft designs or space vehicle structures.
As the automotive industry shifts towards alternative fuels, hydrogen fuel cell vehicles are gaining traction. Here, the manufacturing of high-pressure hydrogen storage tanks becomes critical. Filament Winding has traditionally been the go-to method for producing these cylindrical tanks, offering a cost-effective solution for high-volume production.
However, AFP is making inroads in this sector, particularly for more complex tank designs that aim to optimize storage capacity and vehicle integration. The precision of AFP allows for tanks with non-cylindrical sections, potentially improving the packaging efficiency within the vehicle.
The AFP-XS system presents an intriguing option for automotive manufacturers. It allows for the efficient production of traditional cylindrical tanks while also offering the flexibility to create more advanced designs as the technology and market evolve.
In the marine industry, the corrosion resistance and light weight of composite materials make them increasingly attractive. Filament Winding has long been used to produce cylindrical structures like submarine hulls and pipelines, where its ability to create strong, seamless tubes is advantageous.
AFP is finding applications in creating large, complex hull structures and masts. Its ability to precisely lay fibers over large, curved surfaces results in optimized structures that can withstand the harsh marine environment while minimizing weight.
The versatility of the AFP-XS system is particularly valuable in shipbuilding, where a wide range of components with varying geometries are required. From cylindrical sections to complex hull shapes, this hybrid system can adapt to diverse manufacturing needs within a single facility.
The energy sector, particularly in renewable energy storage, is another area where these manufacturing technologies are making an impact. Large-scale hydrogen storage tanks for energy applications often rely on Filament Winding for their construction, due to its efficiency in producing large cylindrical vessels.
However, as designs for hydrogen storage systems become more advanced, AFP is gaining relevance. Its precision can be crucial in creating storage solutions that integrate more seamlessly with other energy infrastructure or in producing tanks with optimized geometries for specific installation requirements.
The AFP-XS system offers energy infrastructure developers the flexibility to produce both traditional cylindrical tanks and more complex storage solutions. This adaptability could be key in creating the diverse range of hydrogen storage solutions needed for a comprehensive clean energy ecosystem.
In each of these industries, the choice between AFP, Filament Winding, or the hybrid AFP-XS system depends on factors such as production volume, part complexity, performance requirements, and cost considerations. The AFP-XS system, in particular, offers a versatile solution for industries with diverse manufacturing needs or those looking to optimize their production processes across different product lines.
As we've explored throughout this blog post, the production of hydrogen tanks represents a critical challenge in the ongoing transition to clean energy. The manufacturing methods we've discussed – Automated Fiber Placement (AFP), Filament Winding, and the innovative AFP-XS system – each play a vital role in addressing this challenge.
AFP excels in precision and flexibility, allowing for complex geometries and optimized fiber orientations. It's particularly valuable for high-performance applications where weight optimization is crucial.
Filament Winding offers simplicity and cost-effectiveness, especially for cylindrical or spherical shapes. Its established nature makes it a reliable choice for many traditional applications.
Both methods have their strengths, and the choice between them often depends on specific project requirements, production volumes, and cost considerations.
The emergence of hybrid systems like AFP-XS represents a significant leap forward in composite manufacturing technology. By combining the strengths of both AFP and Filament Winding, these systems offer:
As the demand for hydrogen storage solutions continues to grow across various industries – from aerospace and automotive to marine and energy – we can expect to see further innovations in manufacturing technologies. The trend towards more versatile, efficient, and sustainable production methods is likely to continue, with hybrid systems like AFP-XS potentially playing a central role.
For industries considering the production of hydrogen tanks or other composite structures, it's crucial to carefully evaluate the benefits of each manufacturing method. While traditional AFP and Filament Winding remain valuable options, the advantages offered by hybrid systems make them an increasingly attractive choice, especially for those seeking to balance performance, efficiency, and adaptability.
As we move forward, the continued development of these manufacturing technologies will be key to realizing the full potential of hydrogen as a clean energy carrier, contributing to a more sustainable future across multiple sectors.
Discover the future of composite manufacturing with Addcomposites! Here's how you can get involved:
At Addcomposites, we are dedicated to revolutionizing composite manufacturing. Our AFP systems and comprehensive support services are waiting for you to harness. So, don't wait – get started on your journey to the future of manufacturing today!