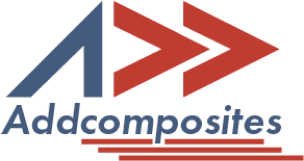
The aviation industry has always been at the forefront of adopting innovative materials and technologies to enhance the performance, safety, and efficiency of aircraft. One such revolutionary material that has gained significant traction in recent years is thermoplastic composites. These materials, characterized by their ability to be melted and reshaped multiple times without significant degradation, offer numerous advantages over traditional materials. This section delves into the importance of thermoplastic materials in aviation, the challenges associated with achieving perfect in situ consolidation, and the transformative role of robotic automated fiber/tape laying processes.
Thermoplastic matrix composites are increasingly finding applications across various industrial sectors, primarily due to their environmental compatibility and processability. In the aviation domain, the tape placement process stands out as a promising technique with the potential to process thermoplastic composites for large-scale industrial applications. The intrinsic benefits of thermoplastic composites, such as their ability to undergo high heating and cooling rates during the tape placement process, make them an attractive choice for aerospace applications. Moreover, the application of laser heating in the tape placement process necessitates a comprehensive understanding of the involved factors to ensure optimal results
Achieving full in situ consolidation is a complex endeavor, primarily due to the inherent challenges associated with thermoplastic materials. The primary constraint of full in situ consolidation lies in the speed and productivity of the LATP/LAFP process, which is often limited by the physics or chemistry of thermoplastic materials. This method places significant demands on the AFP process to ensure the final part quality, including low porosity, appropriate crystallinity, and autohesion
Robotic automated fiber/tape laying processes have emerged as a game-changer in the production of high-performance composite components from unidirectional precast materials. Typically, a robot is employed to lay the lanes along predefined paths, offering immense design freedom for the final product. The automated laying process involves stacking layers atop each other on a tool, known as a mandrel, coupled with the application of heat and pressure. It's crucial during this procedure to enable the strips to consolidate directly during installation, eliminating the need for additional post-consolidation efforts. The research in this domain aims to leverage robotic processes for the automatic laying of fibers/tapes, anticipating the enhanced quality of composite structures through on-site consolidation.
The selection of the right raw material is paramount in the ATP/AFP processes. The raw material, specifically the Unidirectional (UD) thermoplastic prepreg, plays a significant role in determining the final attributes of the product. Before commencing the manufacturing process, it's crucial to identify the type of fiber required and the appropriate matrix, depending on the desired characteristics of the final product. Once these are determined, the next step involves procuring materials from various manufacturers. This phase is followed by a rigorous quality control process for the raw material.
The material used in ATP/AFP processes is a vital process parameter. The production process for obtaining composites from thermoplastic materials is largely dependent on the resin's viscosity. This makes impregnation a critical aspect. The quality of the raw material can vary significantly across suppliers, and for each material matrix. Defects, especially porosity, can often occur in the production of thermoplastic tape. These defects necessitate adjustments in temperature, consolidation, and melting time during the ATP/AFP process.
The steps for producing a high-quality final product using the ATP/AFP technology are outlined in a detailed process. Each step is elaborated upon in individual subchapters. Some of the key parameters that influence the quality of the final product in the process include:
These parameters have varying impacts on the final product's attributes, such as voids and the degree of crystallinity.
The process of creating composites from thermoplastic composite tapes is intricate and involves several critical steps. Among these, impregnation, consolidation, and crystallinity stand out as the three main pillars that ensure the composite's strength and durability.
The development of intimate contact between the layers is a prerequisite for achieving a strong bond or connection. This involves equalizing the unevenness of the tape and the laminate. The presence of voids in the starting material requires a longer heating time and greater pressure during the process of laying a thermoplastic strip with a laser. It is essential to understand the percentage of voids on the tape that will be used in the process. The resin content in the thermoplastic band not only influences the mechanical properties of the finish but also affects the percentage of crystallinity and the heat balance for the ATP/AFP process.
The application of heat is a fundamental aspect of the AFP/ATL process, ensuring proper adhesion between the substrate and incoming tows. The device responsible for this is typically referred to as a "heater," mounted to the AFP head. Various heating systems have been developed and utilized over the years, each with its unique advantages and challenges. Here, we delve into the specifics of three primary heating systems:
HGTs have been in use for over two decades, initially in Automated Tape Laying (ATL) machines and later in AFP machines. This mechanism utilizes a hot gas, typically nitrogen, with the temperature controlled by the gas flow rate. While HGTs are cost-effective, temperature control can be challenging. They are suitable for thermoplastic layups due to the high temperatures they can achieve. However, when compared to laser heaters, HGTs offer more distributed heating and heat both the polymers and fibers, with fewer safety concerns.
Laser heaters are preferred for thermoplastic layups, offering advantages like high energy density, focused heating, faster processing rates, and a better surface finish. They have become more affordable and robust over time. However, they require safety precautions, including laser shielding around the AFP cell and personal protection equipment (PPE) for personnel.
Pulsed light heaters are a newer development, offering an alternative to traditional hot gas and lasers. These systems provide rapid heating, with heating time and temperature comparable to laser systems. One of their significant advantages is safety; they do not require the stringent protection measures associated with lasers, making them a safer choice in many manufacturing environments.
Robotic tape laying processes have emerged as a pivotal technique in the realm of composite manufacturing, especially in sectors demanding high precision and efficiency, such as aerospace. The integration of robotics ensures a consistent and high-quality output, making it an ideal choice for producing carbon fiber-reinforced parts.
The process intricacies involve a myriad of parameters, each playing a crucial role in determining the final product's quality. These parameters range from temperature aspects like laser temperature, laser angle, and mandrel’s temperature to pressure dynamics involving the compaction force of the roller. The time factor, represented by the layup speed, also significantly influences the outcome.
Achieving complete consolidation through robotic processes necessitates comprehensive research. This is to optimize the multitude of parameters required to produce composite parts of varying sizes and shapes. The interrelationship between the process parameters, material properties, and the bond strength between the interlaminar layers has been a focal point of investigation.
In the tape-laying process, the choice of heat source plays a pivotal role in determining the quality and efficiency of the final product. Among the prominent heat sources, HGT (Hot Gas Torches), Laser, and Flash lamps each cater to specific applications and have their unique advantages.
The Flash lamp, a relatively newer entrant in the field, stands out for its safety features. It offers rapid and focused heating, making it a promising choice for certain applications. On the other hand, Laser heating, with its precision and consistency, has established itself as the most widely used and proven heat source in the industry.
HGT, despite being one of the earliest heat sources employed, has faced challenges in maintaining consistent quality during the process. While it has served the industry for a long time, advancements in technology and the emergence of more efficient heat sources have overshadowed its utility.
In essence, while each heat source has its place in the tape-laying process, factors such as safety, precision, and consistency play a crucial role in determining their suitability for specific applications.
Discover the future of composite manufacturing with Addcomposites! Here's how you can get involved:
At Addcomposites, we are dedicated to revolutionizing composite manufacturing. Our AFP systems and comprehensive support services are waiting for you to harness. So, don't wait – get started on your journey to the future of manufacturing today!
The aviation industry has always been at the forefront of adopting innovative materials and technologies to enhance the performance, safety, and efficiency of aircraft. One such revolutionary material that has gained significant traction in recent years is thermoplastic composites. These materials, characterized by their ability to be melted and reshaped multiple times without significant degradation, offer numerous advantages over traditional materials. This section delves into the importance of thermoplastic materials in aviation, the challenges associated with achieving perfect in situ consolidation, and the transformative role of robotic automated fiber/tape laying processes.
Thermoplastic matrix composites are increasingly finding applications across various industrial sectors, primarily due to their environmental compatibility and processability. In the aviation domain, the tape placement process stands out as a promising technique with the potential to process thermoplastic composites for large-scale industrial applications. The intrinsic benefits of thermoplastic composites, such as their ability to undergo high heating and cooling rates during the tape placement process, make them an attractive choice for aerospace applications. Moreover, the application of laser heating in the tape placement process necessitates a comprehensive understanding of the involved factors to ensure optimal results
Achieving full in situ consolidation is a complex endeavor, primarily due to the inherent challenges associated with thermoplastic materials. The primary constraint of full in situ consolidation lies in the speed and productivity of the LATP/LAFP process, which is often limited by the physics or chemistry of thermoplastic materials. This method places significant demands on the AFP process to ensure the final part quality, including low porosity, appropriate crystallinity, and autohesion
Robotic automated fiber/tape laying processes have emerged as a game-changer in the production of high-performance composite components from unidirectional precast materials. Typically, a robot is employed to lay the lanes along predefined paths, offering immense design freedom for the final product. The automated laying process involves stacking layers atop each other on a tool, known as a mandrel, coupled with the application of heat and pressure. It's crucial during this procedure to enable the strips to consolidate directly during installation, eliminating the need for additional post-consolidation efforts. The research in this domain aims to leverage robotic processes for the automatic laying of fibers/tapes, anticipating the enhanced quality of composite structures through on-site consolidation.
The selection of the right raw material is paramount in the ATP/AFP processes. The raw material, specifically the Unidirectional (UD) thermoplastic prepreg, plays a significant role in determining the final attributes of the product. Before commencing the manufacturing process, it's crucial to identify the type of fiber required and the appropriate matrix, depending on the desired characteristics of the final product. Once these are determined, the next step involves procuring materials from various manufacturers. This phase is followed by a rigorous quality control process for the raw material.
The material used in ATP/AFP processes is a vital process parameter. The production process for obtaining composites from thermoplastic materials is largely dependent on the resin's viscosity. This makes impregnation a critical aspect. The quality of the raw material can vary significantly across suppliers, and for each material matrix. Defects, especially porosity, can often occur in the production of thermoplastic tape. These defects necessitate adjustments in temperature, consolidation, and melting time during the ATP/AFP process.
The steps for producing a high-quality final product using the ATP/AFP technology are outlined in a detailed process. Each step is elaborated upon in individual subchapters. Some of the key parameters that influence the quality of the final product in the process include:
These parameters have varying impacts on the final product's attributes, such as voids and the degree of crystallinity.
The process of creating composites from thermoplastic composite tapes is intricate and involves several critical steps. Among these, impregnation, consolidation, and crystallinity stand out as the three main pillars that ensure the composite's strength and durability.
The development of intimate contact between the layers is a prerequisite for achieving a strong bond or connection. This involves equalizing the unevenness of the tape and the laminate. The presence of voids in the starting material requires a longer heating time and greater pressure during the process of laying a thermoplastic strip with a laser. It is essential to understand the percentage of voids on the tape that will be used in the process. The resin content in the thermoplastic band not only influences the mechanical properties of the finish but also affects the percentage of crystallinity and the heat balance for the ATP/AFP process.
The application of heat is a fundamental aspect of the AFP/ATL process, ensuring proper adhesion between the substrate and incoming tows. The device responsible for this is typically referred to as a "heater," mounted to the AFP head. Various heating systems have been developed and utilized over the years, each with its unique advantages and challenges. Here, we delve into the specifics of three primary heating systems:
HGTs have been in use for over two decades, initially in Automated Tape Laying (ATL) machines and later in AFP machines. This mechanism utilizes a hot gas, typically nitrogen, with the temperature controlled by the gas flow rate. While HGTs are cost-effective, temperature control can be challenging. They are suitable for thermoplastic layups due to the high temperatures they can achieve. However, when compared to laser heaters, HGTs offer more distributed heating and heat both the polymers and fibers, with fewer safety concerns.
Laser heaters are preferred for thermoplastic layups, offering advantages like high energy density, focused heating, faster processing rates, and a better surface finish. They have become more affordable and robust over time. However, they require safety precautions, including laser shielding around the AFP cell and personal protection equipment (PPE) for personnel.
Pulsed light heaters are a newer development, offering an alternative to traditional hot gas and lasers. These systems provide rapid heating, with heating time and temperature comparable to laser systems. One of their significant advantages is safety; they do not require the stringent protection measures associated with lasers, making them a safer choice in many manufacturing environments.
Robotic tape laying processes have emerged as a pivotal technique in the realm of composite manufacturing, especially in sectors demanding high precision and efficiency, such as aerospace. The integration of robotics ensures a consistent and high-quality output, making it an ideal choice for producing carbon fiber-reinforced parts.
The process intricacies involve a myriad of parameters, each playing a crucial role in determining the final product's quality. These parameters range from temperature aspects like laser temperature, laser angle, and mandrel’s temperature to pressure dynamics involving the compaction force of the roller. The time factor, represented by the layup speed, also significantly influences the outcome.
Achieving complete consolidation through robotic processes necessitates comprehensive research. This is to optimize the multitude of parameters required to produce composite parts of varying sizes and shapes. The interrelationship between the process parameters, material properties, and the bond strength between the interlaminar layers has been a focal point of investigation.
In the tape-laying process, the choice of heat source plays a pivotal role in determining the quality and efficiency of the final product. Among the prominent heat sources, HGT (Hot Gas Torches), Laser, and Flash lamps each cater to specific applications and have their unique advantages.
The Flash lamp, a relatively newer entrant in the field, stands out for its safety features. It offers rapid and focused heating, making it a promising choice for certain applications. On the other hand, Laser heating, with its precision and consistency, has established itself as the most widely used and proven heat source in the industry.
HGT, despite being one of the earliest heat sources employed, has faced challenges in maintaining consistent quality during the process. While it has served the industry for a long time, advancements in technology and the emergence of more efficient heat sources have overshadowed its utility.
In essence, while each heat source has its place in the tape-laying process, factors such as safety, precision, and consistency play a crucial role in determining their suitability for specific applications.
Discover the future of composite manufacturing with Addcomposites! Here's how you can get involved:
At Addcomposites, we are dedicated to revolutionizing composite manufacturing. Our AFP systems and comprehensive support services are waiting for you to harness. So, don't wait – get started on your journey to the future of manufacturing today!