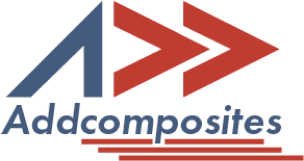
Imagine a world where 3D printed parts are not just prototypes, but fully functional, high-strength components used in aerospace and robotics. This isn't a distant dream – it's becoming a reality thanks to groundbreaking research in continuous carbon fiber reinforced printing filaments.
Traditional 3D printing materials often fall short when it comes to mechanical strength, limiting their use in demanding applications. But what if we could combine the flexibility of 3D printing with the strength of carbon fiber composites? This is exactly what researchers have been working on, and the results are promising.
In this post, we'll explore recent advancements in the preparation of continuous carbon fiber reinforced printing filaments. This technology has the potential to revolutionize manufacturing in industries where high-performance, lightweight materials are crucial. Whether you're an engineer, a tech enthusiast, or simply curious about the future of manufacturing, you'll want to know about this exciting development.
To understand the significance of this research, let's first look at the current landscape of 3D printing materials.
3D printing, particularly Fused Filament Fabrication (FFF), has gained popularity for its ability to create complex shapes quickly and affordably. FFF works by melting and extruding plastic filaments layer by layer to build up a three-dimensional object. However, the materials commonly used in this process - such as ABS or PLA plastics - have limitations.
These standard filaments often lack the mechanical strength, weather resistance, and heat tolerance required for high-performance applications. For instance, a 3D printed part made from typical plastic filaments might have a tensile strength under 100 MPa, which is far below what's needed for many aerospace or high-stress industrial uses.
Enter thermoplastic composites. These materials combine a plastic base (like nylon) with reinforcing fibers (like carbon fiber). The result is a material that's both printable and significantly stronger than pure plastics. However, most existing composite filaments use short, chopped fibers, which still don't match the performance of traditional fiber-reinforced composites.
This is where continuous carbon fiber reinforced filaments come in. By using long, unbroken carbon fibers throughout the filament, researchers aim to create 3D printable materials that can rival the strength and performance of traditional composites.
Despite the advancements in 3D printing technology, the materials used have remained a significant bottleneck. Current filaments, even those reinforced with short fibers or particles, face several challenges:
1. Low Mechanical Strength: Most filaments produce parts with tensile strengths under 100 MPa, which is insufficient for many high-performance applications.
2. Poor Weather and Heat Resistance: Many common 3D printing materials degrade when exposed to UV light or high temperatures, limiting their use in outdoor or high-heat environments.
3. Inadequate for Aerospace Structural Use: The aerospace industry demands materials with exceptional strength-to-weight ratios and reliability. Current 3D printing filaments fall short of these requirements.
To address these limitations, researchers have developed a process for creating continuous carbon fiber reinforced printing filaments. Here's how it works:
1. Preparation Process:
a. Material Selection and Pretreatment: The researchers used nylon (PA6) as the matrix material and T700 carbon fiber as reinforcement. Both materials are carefully dried to remove moisture before processing.
b. Preimpregnation and Extrusion: Unlike traditional methods, this process uses a crossing form in the prepreg process. The carbon fibers are infiltrated into the molten nylon using three sets of prepreg rolls under pressure. This ensures thorough impregnation of the fibers.
c. Sizing and Cooling: A special sizing equipment controls the final filament diameter. The filament is then air-cooled at room temperature.
2. Key Findings:
a. Fiber Distribution and Integration: Microscopic analysis revealed that the fibers and resin were well-integrated, without the core-shell structure seen in some other composite filaments. This suggests complete impregnation of the fibers, which is crucial for strength and performance.
b. High Mechanical Strength: The resulting filaments showed impressive mechanical properties. Tensile strength reached 820 MPa, with a tensile modulus of 42 GPa. This is comparable to the strength of the carbon fiber itself, indicating excellent fiber alignment and consolidation.
c. Advantages of Small Diameter Filaments: The researchers compared filaments with diameters of 1.75mm and 0.4mm. The smaller 0.4mm filaments showed significant advantages:
- Better storage and transportation: They could be wound into smaller coils without breaking.
- Improved printing quality: The smaller diameter allowed for more precise control during printing, resulting in smoother surfaces and the ability to print at sharper angles.
These advancements address the key limitations of current 3D printing filaments, opening up new possibilities for high-performance 3D printed parts.
The development of continuous carbon fiber reinforced printing filaments has significant implications for manufacturing and opens up exciting new possibilities:
1. Implications for Manufacturing:
a. Strength Meets Flexibility: This technology bridges the gap between the design freedom of 3D printing and the high performance of traditional composite materials. Manufacturers can now consider 3D printing for parts that previously required more complex and expensive production methods.
b. Reduced Waste: Unlike traditional composite manufacturing, which often involves cutting and discarding excess material, 3D printing is an additive process. This could lead to more efficient use of expensive carbon fiber materials.
c. Rapid Prototyping of High-Performance Parts: Engineers can now quickly produce and test prototypes that more accurately represent the strength and performance of final products.
2. Potential Applications:
a. Robotics: The high strength-to-weight ratio of these materials could enable the creation of lighter, stronger robot components. This could lead to more efficient and capable robots in various industries.
b. Aerospace: The aerospace industry stands to benefit significantly from this technology. Potential applications include:
- Custom brackets and mounting hardware
- Interior components for aircraft
- Satellite components
- Drone parts
c. Automotive: While not specifically mentioned in the research, the automotive industry could use this technology for creating strong, lightweight parts for high-performance or electric vehicles.
d. Sports Equipment: Custom-fit, high-performance sports gear could be another potential application, leveraging both the strength of the material and the customization possibilities of 3D printing.
3. Future Developments:
The research suggests that filaments with even smaller diameters (0.4mm or less) may offer further advantages in terms of printing precision and part quality. This points towards a future where we might see incredibly detailed, high-strength 3D printed parts.
The development of continuous carbon fiber reinforced printing filaments represents a significant leap forward in 3D printing technology. By addressing the key limitations of traditional 3D printing materials - namely, insufficient strength and poor environmental resistance - this innovation opens up a world of new possibilities for additive manufacturing.
Let's recap the key benefits of this technology:
1. Dramatically increased strength, with tensile strength reaching 820 MPa
2. Improved fiber orientation and integration with the polymer matrix
3. Better printability and part quality, especially with smaller diameter filaments
4. Potential for use in high-performance applications, including aerospace and robotics
As we look to the future, several exciting directions for further research and development emerge:
1. Exploration of even smaller filament diameters to push the boundaries of print precision
2. Investigation of different fiber and polymer combinations to tailor material properties for specific applications
3. Development of specialized 3D printers optimized for continuous fiber reinforced filaments
4. Creation of design guidelines and software tools to help engineers fully leverage this new material in their work
The journey from laboratory research to widespread industrial application is often a long one, but the potential benefits of this technology make it a path worth pursuing. For engineers, designers, and manufacturers, now is the time to start considering how continuous fiber reinforced 3D printing could transform your field.
We encourage readers to stay informed about this developing technology. Consider reaching out to research institutions or advanced manufacturing companies to learn more about pilot programs or collaborative research opportunities. By engaging with this technology early, you can help shape its development and be at the forefront of the next revolution in additive manufacturing.
Remember, today's cutting-edge research is tomorrow's industry standard. The future of 3D printing is strong, lightweight, and full of possibilities.
Robotics Power displayed through Tesla Optimus Robot
Discover the future of composite manufacturing with Addcomposites! Here's how you can get involved:
At Addcomposites, we are dedicated to revolutionizing composite manufacturing. Our AFP systems and comprehensive support services are waiting for you to harness. So, don't wait – get started on your journey to the future of manufacturing today!