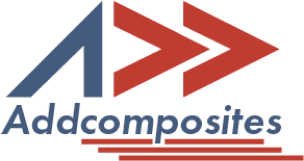
In the realm of additive manufacturing (AM), the quest for enhanced material properties has led to the development of continuous carbon fiber-reinforced composites. These materials offer exceptional mechanical properties, crucial for applications in aerospace, automotive, and military sectors. However, the integration of continuous carbon fibers into the fused filament fabrication (FFF) process introduces a set of complex challenges that significantly impact the quality and feasibility of the final products. the main challenges in additive manufacturing (fused filament fabrication) of continuous carbon fiber-reinforced composites include:
Achieving optimal performance in the print heads of fused filament fabrication (FFF) systems, particularly when dealing with continuous carbon fiber-reinforced composites, presents several significant technical challenges. The core difficulties stem primarily from the material characteristics of continuous carbon fibers combined with thermoplastic matrices, as well as the mechanical design constraints of print heads capable of precise and reliable extrusion.
The print head design needs to delicately balance the thermal, flow, and mechanical behaviors of the fibers and polymer melt to produce high-quality printed composites. This requires carefully optimizing each functional component and seamlessly integrating them. More modeling and simulation of the complex phenomena inside the print head is still needed to guide design improvements.
three main advanced extrusion methods for enhanced fabrication of continuous carbon fiber composites:
Among these, in-situ co-extrusion seems most promising for producing composites with high fiber content and good matrix-fiber interfacial bonding. However, it also poses the greatest challenges in print head design and processing control.
Dual extrusion could be suitable for large scale, high-speed printing but more research is needed on improving the consolidation quality.
In general, these advanced extrusion techniques aim to overcome the limitations of traditional single-extrusion while leveraging the benefits of using continuous fiber reinforcement. More innovations in print head design and processing science are still needed to fully realize their potential in composite additive manufacturing.
the future directions in print head technology for advancing additive manufacturing of continuous carbon fiber composites include:
Advancing the print head technology in these directions can help unlock the full potential of additive manufacturing for producing high-performance, multi-functional composite structures in a cost-effective and sustainable manner. However, realizing these will require close collaboration between the hardware, software, and material domains, as well as targeted research investments.
let’s take a moment to acknowledge the significant contributions of Heng Cai and Yuan Chen, the authors of the PDF titled "Fused Filament Fabrication of Continuous Carbon Fiber-Reinforced Composites." Their in-depth research and comprehensive analysis have provided a strong foundation for our discussions on advancements in print head technology for fused filament fabrication. We are immensely grateful for their meticulous work, which continues to inspire innovations and elevate standards in the field of additive manufacturing. Their dedication to exploring and addressing complex challenges in this domain is truly commendable.
Discover the future of composite manufacturing with Addcomposites! Here's how you can get involved:
At Addcomposites, we are dedicated to revolutionizing composite manufacturing. Our AFP systems and comprehensive support services are waiting for you to harness. So, don't wait – get started on your journey to the future of manufacturing today!
In the realm of additive manufacturing (AM), the quest for enhanced material properties has led to the development of continuous carbon fiber-reinforced composites. These materials offer exceptional mechanical properties, crucial for applications in aerospace, automotive, and military sectors. However, the integration of continuous carbon fibers into the fused filament fabrication (FFF) process introduces a set of complex challenges that significantly impact the quality and feasibility of the final products. the main challenges in additive manufacturing (fused filament fabrication) of continuous carbon fiber-reinforced composites include:
Achieving optimal performance in the print heads of fused filament fabrication (FFF) systems, particularly when dealing with continuous carbon fiber-reinforced composites, presents several significant technical challenges. The core difficulties stem primarily from the material characteristics of continuous carbon fibers combined with thermoplastic matrices, as well as the mechanical design constraints of print heads capable of precise and reliable extrusion.
The print head design needs to delicately balance the thermal, flow, and mechanical behaviors of the fibers and polymer melt to produce high-quality printed composites. This requires carefully optimizing each functional component and seamlessly integrating them. More modeling and simulation of the complex phenomena inside the print head is still needed to guide design improvements.
three main advanced extrusion methods for enhanced fabrication of continuous carbon fiber composites:
Among these, in-situ co-extrusion seems most promising for producing composites with high fiber content and good matrix-fiber interfacial bonding. However, it also poses the greatest challenges in print head design and processing control.
Dual extrusion could be suitable for large scale, high-speed printing but more research is needed on improving the consolidation quality.
In general, these advanced extrusion techniques aim to overcome the limitations of traditional single-extrusion while leveraging the benefits of using continuous fiber reinforcement. More innovations in print head design and processing science are still needed to fully realize their potential in composite additive manufacturing.
the future directions in print head technology for advancing additive manufacturing of continuous carbon fiber composites include:
Advancing the print head technology in these directions can help unlock the full potential of additive manufacturing for producing high-performance, multi-functional composite structures in a cost-effective and sustainable manner. However, realizing these will require close collaboration between the hardware, software, and material domains, as well as targeted research investments.
let’s take a moment to acknowledge the significant contributions of Heng Cai and Yuan Chen, the authors of the PDF titled "Fused Filament Fabrication of Continuous Carbon Fiber-Reinforced Composites." Their in-depth research and comprehensive analysis have provided a strong foundation for our discussions on advancements in print head technology for fused filament fabrication. We are immensely grateful for their meticulous work, which continues to inspire innovations and elevate standards in the field of additive manufacturing. Their dedication to exploring and addressing complex challenges in this domain is truly commendable.
Discover the future of composite manufacturing with Addcomposites! Here's how you can get involved:
At Addcomposites, we are dedicated to revolutionizing composite manufacturing. Our AFP systems and comprehensive support services are waiting for you to harness. So, don't wait – get started on your journey to the future of manufacturing today!