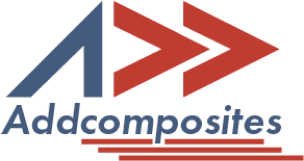
In the ever-evolving landscape of advanced materials, long fiber thermoplastic (LFT) composites have emerged as a cornerstone technology in the automotive and transportation sectors. Their appeal lies in a compelling combination of characteristics: ease of processing, recyclability, superior specific modulus, and excellent impact resistance. However, as industry demands grow more sophisticated, manufacturers face an increasing challenge: how to enhance the mechanical properties of LFT composites while maintaining their processing advantages?
Traditional manufacturing methods for LFT composites face several limitations:
These limitations have sparked a search for innovative manufacturing solutions that can overcome these constraints while maintaining the advantages of both processes.
Enter a groundbreaking solution: the integration of Automated Fiber Placement (AFP) with traditional LFT manufacturing. This hybrid approach combines:
This innovative combination represents a significant leap forward in composite manufacturing technology. The process leverages the strengths of both materials and manufacturing methods:
The significance of this development extends beyond mere technical innovation. In an era where lightweight, high-performance materials are crucial for advancing sustainable transportation and industrial applications, this hybrid manufacturing approach offers:
As industries push towards more efficient manufacturing processes, this hybrid approach represents a significant step forward in addressing the growing demand for high-performance composite materials while maintaining practical manufacturing considerations.
In the following sections, we'll delve deeper into the materials, manufacturing processes, and remarkable results achieved through this innovative approach to composite manufacturing.
The success of this hybrid manufacturing approach lies in the careful selection and integration of two distinct composite materials. Let's explore these materials and understand why they form such an effective combination.
Glass fiber reinforced composites have become a cornerstone in modern manufacturing, particularly in the form of Long Fiber Thermoplastic (LFT) composites. The specific material used in this innovation consists of:
PPS isn't just another polymer matrix - it's an engineering thermoplastic that brings several crucial advantages:
The second component of this hybrid system is the continuous carbon fiber reinforced tape, which brings its own set of distinctive characteristics:
The combination of these materials creates a synergistic effect that overcomes the limitations of each individual component:
When designing for automated fiber placement, the choice of these specific materials wasn't arbitrary. Key factors included:
This careful material selection forms the foundation for the remarkable property improvements achieved in the final hybrid composite. The next section will delve into how these materials are brought together through innovative manufacturing processes.
The success of this hybrid composite lies not just in the materials selected, but in the innovative manufacturing approach that combines traditional and cutting-edge processes. Let's explore how automated manufacturing techniques are revolutionizing composite production.
The manufacturing process is divided into two distinct steps, each crucial for achieving the desired properties in the final component:
The first step involves creating the G-LFT substrate through Extrusion Compression Molding (ECM). This process involves:
The second step utilizes Automated Fiber Placement (AFP) technology to apply the CF-Tape. This process represents a significant advancement in composite manufacturing:
Several factors are crucial for achieving optimal results in this hybrid manufacturing approach:
During the ATP process, two key phenomena occur:
To achieve optimal results, several factors require careful attention:
Several challenges were addressed during process development:
The success of this process opens doors for several manufacturing improvements:
This manufacturing approach demonstrates how traditional processes can be enhanced through the integration of advanced automation technologies, leading to superior composite properties while maintaining practical production considerations.
The effectiveness of combining AFP technology with traditional composites is best demonstrated through comprehensive performance analysis. Let's examine the remarkable improvements achieved through this hybrid manufacturing approach.
The addition of CF-Tape through ATP resulted in dramatic improvements in flexural properties:
Tensile testing revealed significant strengthening:
The critical interface between materials showed impressive performance:
Key thermal characteristics were maintained:
Thermal stability showed promising results:
Low-velocity impact testing revealed interesting characteristics:
Finite Element Analysis provided additional understanding:
The results demonstrate that this hybrid manufacturing approach successfully:
These results validate the effectiveness of combining ATP with traditional composite manufacturing, opening new possibilities for high-performance composite applications.
The successful integration of Automated Fiber Placement (AFP) with traditional composite manufacturing opens up exciting possibilities for the future of materials engineering. Let's explore the implications and potential developments of this innovative approach.
The automotive industry stands to benefit significantly from this technology:
The aerospace sector presents numerous opportunities:
Renewable energy applications show particular promise:
Future manufacturing developments will likely focus on:
The technology presents several opportunities for cost optimization:
Future research may focus on:
Next-generation manufacturing approaches might include:
The future of this technology must address environmental concerns:
Future research will likely explore:
The successful implementation will require:
The future of hybrid composite manufacturing looks promising, with several key areas of focus:
This innovative manufacturing approach represents a significant step forward in composite technology, with the potential to revolutionize multiple industries while addressing crucial sustainability and performance requirements.
The integration of Automated Fiber Placement (AFP) with traditional composite manufacturing represents more than just a technical advancement—it marks a significant milestone in the evolution of composite manufacturing. Let's summarize the key insights and implications of this innovative approach.
The hybrid manufacturing technique has delivered remarkable enhancements:
The process successfully combines:
This development represents a significant step forward in composite manufacturing technology:
The implications extend across multiple sectors:
The technology opens several avenues for advancement:
Environmental considerations remain central:
The successful development of this hybrid manufacturing approach demonstrates the potential for innovation in composite materials and processing. It shows that by combining traditional methods with advanced automation, we can achieve:
This advancement in composite manufacturing not only solves current challenges but also paves the way for future innovations. As we continue to push the boundaries of material science and manufacturing technology, such hybrid approaches will become increasingly important in meeting the demanding requirements of modern industrial applications.
The success of this technology serves as a reminder that significant advances often come not from completely new technologies, but from innovative combinations of existing ones. It demonstrates that the future of composite manufacturing lies not just in developing new materials or processes, but in finding smart ways to integrate and optimize what we already have.
As we move forward, this hybrid manufacturing approach stands as a testament to the power of innovative thinking in materials engineering and sets a new standard for what can be achieved in composite manufacturing.
This blog post is based on the research paper:
Chahine, G., Barakat, A., White, B., Schwartz, B., Marathe, U., Yeole, P., Hassen, A. A., & Vaidya, U. (2024). Advanced Hybrid Composites: Integrating Carbon Fiber Tape into Glass Fiber Thermoplastics Via Automated Tape Placement Overmolding. University of Tennessee and Oak Ridge National Laboratory.
For more information on composite manufacturing and AFP technology, explore these related articles:
Are you ready to revolutionize your composite manufacturing processes? Addcomposites offers cutting-edge solutions for automated fiber placement that can help you achieve:
Ready to transform your composite manufacturing capabilities? Contact our team of experts today:
Transform your manufacturing process with Addcomposites - Where Innovation Meets Excellence
This blog post was created based on research conducted at the University of Tennessee and Oak Ridge National Laboratory. We thank the authors for their groundbreaking work in advancing composite manufacturing technology.