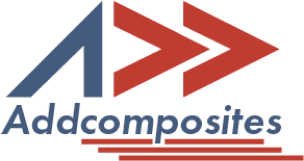
In this article, we will combine the theories discussed in Beam Bending and Fiber Strength, and how to combine them in the world of composites to create strong, lightweight structural parts. When combined, beam bending and fiber strength can be used to create what is called a Sandwich Panel. Similar to an I-Beam, a sandwich panel places reinforcing material on the top and bottom planes of the beam.
However, unlike an I-Beam composed of a single metal, a sandwich panel is comprised of three separate components: fiber, matrix, and core material. This is what makes it a composite part: a part made up of two or more individual components with different properties that, when combined, give the final part exceptional properties different than its constituents.
Figure 1. Composite sandwich panels are very similar to I-Beams, in that the strongest sections are at the extremes
A traditional sandwich panel consists of a stack of three sheets - two "skins", of the same composition of fiber and matrix, on either side of the "core"; thus creating the sandwich. Given what we learned from the beam bending theory, the skins will experience most of the force when bent. So the skins of a sandwich panel are usually a strong, stiff material, while the core of the sandwich panel is often a weak but durable material designed to space the two skins apart.
In structural composites, the material with the strongest properties determines the behavior of the panel where that property takes effect. So if your core was stronger than your skin, the skin material wouldn't have very much impact and would fracture or tear almost immediately under an applied load.
This is why you never see a sandwich panel that places carbon fiber in the interior, as it will not be an efficient use of the carbon fiber. Because the largest forces are applied to the extremes of a beam when bending, we want the skin of a sandwich panel to take the majority of the force, while the core experiences only minimal load. This means the skin needs to be stronger than the core, or else the part will fail.
Figure 2. Fiber (in blue) is most effective when added to the top- and bottom-most faces of a beam because that is where most of the load is experienced
This makes a sandwich panel an effective, lightweight structure. Higher-strength materials are more expensive, but when using the strongest material as only the skin, where it makes the most impact, you save overall cost, material, and weight; adding your skins at the extremes of a beam maximizes impact.
As you thicken the skins, decreasing core thickness, you get diminishing returns on its effectiveness. A strong material closer to the core doesn't contribute much to the strength of the part, because the material will experience much lower forces than the outermost fibers.
Figure 3. A carbon fiber sheet like this one can be used as the "skin" of a sandwich panel to make the part stiff and strong (Source: Markforged)
As we learned previously, a bending force on a beam reduces to tensile and compressive forces on these panels. So the skin of a sandwich panel should be made of a material that performs well under tension - which is often easier to optimize for than compression. This makes continuous fibers a good fit for sandwich panel skins because they are built and optimized for their strength in tension.
Whether woven in sheets, formed into tubes or made with ATL/AFP, a structure is created such that these fiber materials can act like the skin of a sandwich panel so that they can provide the most impact. Now that we have discussed the basics of sandwich panels, beam bending, and fiber strength, and how they all relate, it's time for you to design your part in the most efficient manner.
Addcomposites is the provider of the Automated Fiber Placement (AFP) system. The AFP system can be rented on a monthly basis to work with thermosets, thermoplastic, dry fiber placement, or in combination with 3d printers.
In this article, we will combine the theories discussed in Beam Bending and Fiber Strength, and how to combine them in the world of composites to create strong, lightweight structural parts. When combined, beam bending and fiber strength can be used to create what is called a Sandwich Panel. Similar to an I-Beam, a sandwich panel places reinforcing material on the top and bottom planes of the beam.
However, unlike an I-Beam composed of a single metal, a sandwich panel is comprised of three separate components: fiber, matrix, and core material. This is what makes it a composite part: a part made up of two or more individual components with different properties that, when combined, give the final part exceptional properties different than its constituents.
Figure 1. Composite sandwich panels are very similar to I-Beams, in that the strongest sections are at the extremes
A traditional sandwich panel consists of a stack of three sheets - two "skins", of the same composition of fiber and matrix, on either side of the "core"; thus creating the sandwich. Given what we learned from the beam bending theory, the skins will experience most of the force when bent. So the skins of a sandwich panel are usually a strong, stiff material, while the core of the sandwich panel is often a weak but durable material designed to space the two skins apart.
In structural composites, the material with the strongest properties determines the behavior of the panel where that property takes effect. So if your core was stronger than your skin, the skin material wouldn't have very much impact and would fracture or tear almost immediately under an applied load.
This is why you never see a sandwich panel that places carbon fiber in the interior, as it will not be an efficient use of the carbon fiber. Because the largest forces are applied to the extremes of a beam when bending, we want the skin of a sandwich panel to take the majority of the force, while the core experiences only minimal load. This means the skin needs to be stronger than the core, or else the part will fail.
Figure 2. Fiber (in blue) is most effective when added to the top- and bottom-most faces of a beam because that is where most of the load is experienced
This makes a sandwich panel an effective, lightweight structure. Higher-strength materials are more expensive, but when using the strongest material as only the skin, where it makes the most impact, you save overall cost, material, and weight; adding your skins at the extremes of a beam maximizes impact.
As you thicken the skins, decreasing core thickness, you get diminishing returns on its effectiveness. A strong material closer to the core doesn't contribute much to the strength of the part, because the material will experience much lower forces than the outermost fibers.
Figure 3. A carbon fiber sheet like this one can be used as the "skin" of a sandwich panel to make the part stiff and strong (Source: Markforged)
As we learned previously, a bending force on a beam reduces to tensile and compressive forces on these panels. So the skin of a sandwich panel should be made of a material that performs well under tension - which is often easier to optimize for than compression. This makes continuous fibers a good fit for sandwich panel skins because they are built and optimized for their strength in tension.
Whether woven in sheets, formed into tubes or made with ATL/AFP, a structure is created such that these fiber materials can act like the skin of a sandwich panel so that they can provide the most impact. Now that we have discussed the basics of sandwich panels, beam bending, and fiber strength, and how they all relate, it's time for you to design your part in the most efficient manner.
Addcomposites is the provider of the Automated Fiber Placement (AFP) system. The AFP system can be rented on a monthly basis to work with thermosets, thermoplastic, dry fiber placement, or in combination with 3d printers.